制桶工艺学
第七章 冲压
第二节 冲压模具
7.2.2 拉伸模
三、拉伸的计算
(1)拉伸的系数。拉伸次数与拉伸时材料的变形程度有密切的关系,拉伸时材料允许的变形量通常用拉伸系数m表示。对于封闭器的拉伸件,着次拉伸时,此系数为筒部外径在d1与毛坯直径D之比,即m1=d1/D。在以后的拉伸时,拉伸后筒部外径与拉伸前筒部外径之比,即mn=dn/dn-1。如图7-22所示。
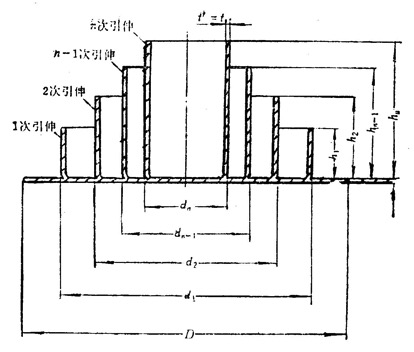
图7-22 多次拉伸的方法
拉伸系数m与拉伸时材料断面收缩率ψ的关系如下:

式中 F1、F2——拉伸前后圆筒形壁部的横断面积(mm2);
d1、d2——拉伸前后筒部外径(mm)。
由此可见,拉伸系数总是小于1,而且其值越小,材料变形越大。
(2)影响拉伸系数的因素如下:
① 拉伸材料的机械性能和表面状态的影响。由图7-23中可知,要使金属发生塑性变形,必须使金属受到超过屈服点s,但小于抗拉强度极限b,这样拉伸工作就应在金属的允许变形区(s点与b点)曲线下的阴影部分内进行。由于各种材料的机械性能不同,拉伸曲线也不一样,因此拉伸系数也不同。
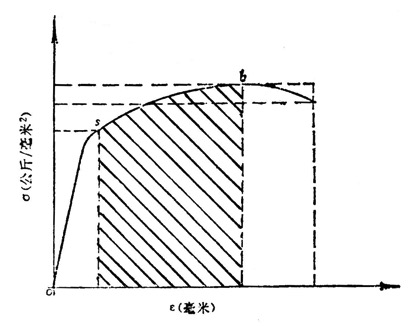
图7-23 材料拉伸性能图
由实验可知:
a. 材料的抗拉强度愈高,拉伸系数愈大。
b. 对于屈版点应力数值低、抗拉强度高,延伸率大的材料,其拉伸系数可取小些。
c. 塑性变形会使材料的强度和硬度增加,延伸率降低,而其允许变形则相应减小。所以多次拉伸的拉伸系数应逐次增大。
d. 表面愈光洁、平整、允许的拉伸系数愈小,材料表面有锈斑,其拉伸系数应增大20~30%。
② 材料厚度的影响。对于厚材料拉伸因不易起皱,拉伸系数值可以减小。
③ 材料内部结构的影响。晶粒粗大和过细对拉伸变形不利,晶粒内部的片状化合物(碳素钢中的碳化物)也会降低材料的塑性,这些都使拉伸系数增大。
④ 凸、凹模的圆角半径、模具间隙及模具表面质量等影响。一般地说,采用较大的圆角半径时,拉伸系数可小些,反之拉伸系数要大些。因为圆角半径小,材料进入凹模的摩擦阻力大,拉伸时会使制件内部应力增大,容易发生断裂。模具间隙大,模具硬度高,表面光洁度高,拉伸系数也可减小。但圆角半径或间隙太大时,也会由于材料起皱而使制件破裂。
⑤ 拉伸方式的影响。无压边圈拉伸时的拉伸系数取大些,有压边圈拉伸时,拉伸系数取小些。
⑥ 制件形状的影响。如果拉伸件形状比较复杂,在拉伸时材料变形较为急剧,拉伸系数应取大些。如果拉伸件形状比较简单,在拉伸时材料变形较为平缓,拉伸系数可取小些。
⑦ 拉伸速度的影响。当拉伸速度大时,拉伸系数也会相应增大。拉伸速度慢。材料在拉伸过程中变形均匀,不易造成破裂。此时拉伸系数可取小些。
⑧ 润滑对拉伸系数的影响。适当的润滑可以减少拉伸时材料表面的摩擦,拉伸系数可取小些。
综上所述,影响拉伸系数的因素很多,从理论上计算拉伸系数很复杂,一般常采用经验值。
(3)拉伸系数的确定。拉伸筒形制件,应采用最少的拉伸次数,也就是说使每次的变形程度尽可能达到最大。变形程度K=D/d,是拉伸系数的倒数,即m=1/K。它是根据试验而定的。为了便于计算,列出拉伸系数便于选用。
第一次拉伸:m1=0.48~0.5
第二次拉伸:m2=0.73~0.75
桶底盖、封闭器的拉伸系数:
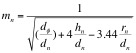
式中 dΦ/dn——凸缘的相对直径;
hn/dn——相对拉伸高度;
rn/dn——相对圆角半径;
mn——拉伸系数;
n——拉伸次数。
由式可知:拉伸系数mn的大小取决于dΦ/dn、hn/dn、rn/dn的大小,其中dΦ/dn影响最大,而rn/dn的影响最小。
除了TM×2螺圈需二次拉伸外,其余均一次拉伸即可。
如图7-24所示是桶顶底盖、封闭器的拉伸件。
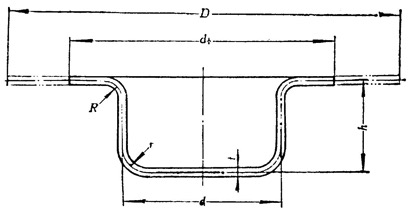
图7-24 桶顶底盖、封闭器的拉伸件
如图7-25所示是TM×2螺圈的拉伸方法。它是以减小拉伸直径,增加拉伸高度来达到制件要求的。
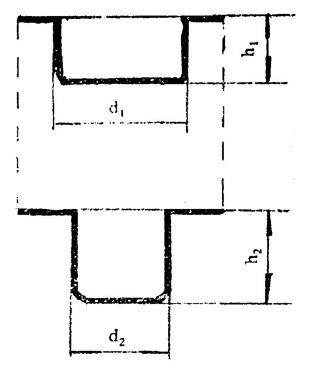
图7-25 TM×2螺圈的拉伸方法