制桶工艺学
第七章 冲压
第三节 冲压常见缺陷与改善措施
7.3.2 拉伸件的常见缺陷与改善措施
拉伸件的常见缺陷、产生原因以及改善措施如表7-8所示。
表7-8 拉伸件的常见缺陷与改善措施
序号 |
质量缺陷 |
简图 |
产生原因 |
改善措施 |
1 |
凸缘起皱且零件壁部破裂 |
B7-8-1 |
压边力太小,凸骑驴觅驴部分起皱,材料无法进入凹模型腔而拉裂 |
加大压边力 |
2 |
凸缘平而壁部拉裂 |
B7-8-2 |
材料承受的径向拉应力太大,造成危险断面拉裂 |
减小压边力;增大凹模圆角半径;加用滑润剂,或增加材料塑性。 |
3 |
危险断面显著变薄 |
B7-8-3 |
模具圆角半径太小,压边力太大,材料承受的径向拉应力接近σb,引起危险断面缩颈 |
加大模具圆角半径和间隙,毛坯涂上合适的润滑剂 |
4 |
零件底部拉脱 |
B7-8-4 |
凹模圆角半径太小,材料实质上处于被切割状态(一般发生在拉延的初始阶段) |
加大凹模圆角半径 |
5 |
锥形件或半球形件侧壁起皱 |
B7-8-5 |
拉延开始时,大部分材料处于悬空状态,加之压边力太小,凹模圆角半径太大或润滑油过多,使径向拉应力减小,而切向压应力加大,材料失去稳定面而起皱 |
增加压边力或采用拉延筋;减小凹模圆角半径;亦可加厚材料 |
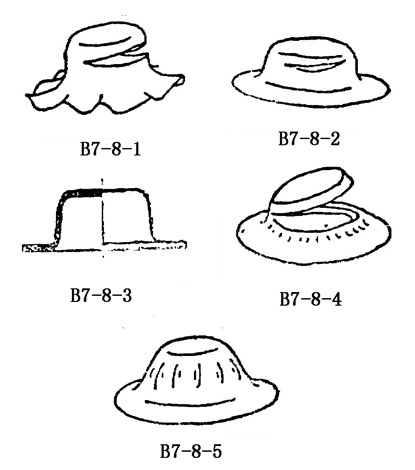
表7-8图例
7.3.3 弯曲件的常见缺陷与改善措施
弯曲件的常见缺陷、产生原因以及改善措施如表7-9所示。
表7-9 弯曲件的常见缺陷与改善措施
序号 |
废品或缺陷 |
产生的原因 |
改善措施 |
1 |
弯裂
(图例B7-9-1) |
凸模弯曲半径过小;
毛坯毛刺的一面处于弯曲外侧;
板材的塑性较低;
下料时毛坯硬化层过大 |
适当增大凸模圆角半径,将毛刺一面处于弯曲内侧用经退火或塑性较好的材料弯曲线与纤维方向垂直或成45°方向 |
2 |
U形弯曲件底部不平
(图例B7-9-2) |
压弯时板料与凸积底部没有靠紧
(图例B7-9-3) |
采用带有压料顶板的模具,在压弯开始时顶板便对毛坯施加足够的压力 |
3 |
弯曲件擦伤
(图例7-9-4) |
金属的微粒附在工作部分的表面上;
凹模的圆角半径过小;
凸凹模的间隙过小 |
适当增大凹模圆角半径提高凸、凹模表面光洁度采用合理凸凹模间隙值清除工作部分表面脏物 |
4 |
弯曲件尺寸偏移
(图例7-9-5) |
毛坯在向凹模滑动时,两边受到的摩擦阻力不相等,故发生尺寸偏移 |
毛坯在模具中定位要准确 |
5 |
弯曲角度变化
(图例7-9-6) |
塑性弯曲时伴随弹性变形,当压弯的工件从模具中取出后,便产生了弹性恢复,从而使弯曲角度发生了变化 |
以校正弯曲代替自由弯曲,以预定的弹复角度来修正凸凹模的角度 |
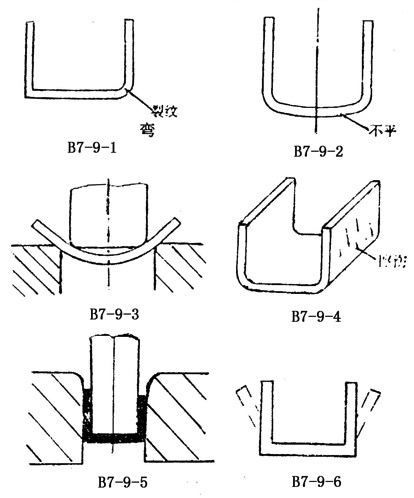
表7-9图例
7.3.4 锁装件的常见缺陷与改善措施
锁装件的常见缺陷、产生原因以及改善措施如表7-10所示。
表7-10 锁装件的常见缺陷与改善措施
工序名称 |
常见缺陷 |
产生原因 |
改善措施 |
拉伸翻边复合工艺 |
翻边裂口 |
翻边凸模不光滑或圆角过小 |
修磨凸模,使凸模圆角光滑过渡或适当增大凸模圆角 |
翻边尺寸高度超差(高) |
冲孔凸模高 |
修磨凸模,使凸模达到正确的高度尺寸 |
翻边尺寸高度不够 |
冲孔凸模低 |
加上垫片,使凸模达到正确的高度尺寸 |
卷缘 |
形状及尺寸不对 |
卷缘模曲线形状及尺寸不对 |
修磨卷缘模曲线形状及尺寸使之达到正确的形状入尺寸 |
卷缘件尺寸超差(高);
卷件尺寸高度不够 |
螺圈制件高度尺寸超差(高);
螺圈制件高度尺寸不够 |
严格检验上道工序的制件尺寸;
剔除不合格产品严格检验上道工序的制件尺寸,剔除不合格产品 |
复习题
1. 冲压过程是怎样一个加工过程?它的冲压力如何计算?
2. 冲床由哪些主要零部件组成?各起什么作用?
3. 冲床有哪些基本技术参数?
4. 简述辊式送料装置的基本结构。该送料装置是如何工作的?
5. 冲压工艺如何分类?它有哪几种基本变形方式?
6. 冲压的单工序、多工位工序、复合工艺是如何区别的?各有哪些特性?
7. 转键式刚性离合器和气动摩擦片离合器有什么不同?各是如何工作的?
8. 滑块由哪些零件组成?它们各起什么作用?
9. 冲裁是如何加工的?哪些因素影响冲裁力?
10. 拉伸怎样进行?拉伸毛坯尺寸如何计算?
11. 弯曲是如何变形的?造成弯曲回弹的因素有哪些?
12. 简述模具的基本结构。
13. 冲裁模工作尺寸及制造公差是怎样确定的?
14. 螺圈和桶塞的拉伸模工作部分尺寸取法有什么不同?为什么?
15. 弯曲模的工作部分尺寸怎样计算?如何消除回弹?
16. 冲压件可分为哪些类型?各有哪些常见缺陷,如何产生的,怎样采取措施加以改善?