制桶工(中级技能培训教程)
第三章 常用制桶设备的中修技术
第一节 中修的目标和内容
二、中期修理的具体实施
1、设备部分拆卸和清洗
根据制桶设备生产运行状况以及修前预检的停修检查确定中修的检修对象后,中修的第一步工作就是将设备要修理的部分进行拆卸和清洗。拆卸时,应对拆卸的部件有充分的了解,应熟读该部件的装配图,分析各零部件的结构、性能、作用以及各零部件之间的联接装配关系。要懂得拆卸顺序,先拆卸外部附件,然后按与装配顺序相反的顺序一个一个地拆下零件。要选择合适的拆卸方法和工具,不许用手锤敲击零件工作表面,精密零件一定要用专用工具拆卸。互相配合的偶件应作标记,不可乱放。零件拆卸(按序号顺序)示例见图3-2。几种典型零件的拆卸方法如图3-3所示。
零件拆下后应进行清洗。常用的清洗方法有浸洗、手工擦洗和压力喷洗三种。清洗后的零件必须吹干,涂敷防锈油,以免生锈。
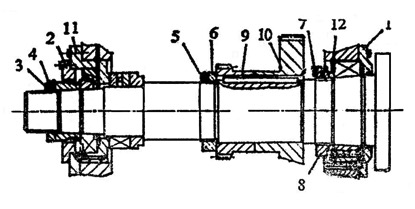
图3-2 零件拆卸顺序示例
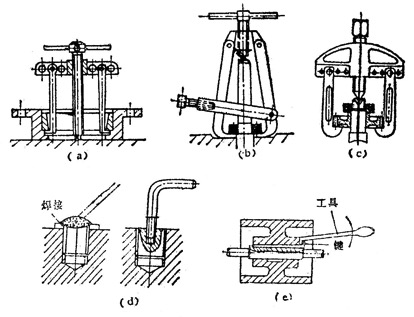
图3-3 几种典型零件拆卸方法
(a)拆卸轴承外环;(b)拆卸轴承;(c)利用大齿轮与轴承一起拆;(d)拆卸断螺钉;(e)拆楔键
2、鉴定更换件和修复件
零件拆下清洗后,必须认真检查,尤其对易损件以及一些重要零件要逐个测量鉴定。根据鉴定结果,部分修改预备检修单,使其变成真正的工作检修单。同时准确地确定哪些零件必须更换,制订更换零件明细表,确定哪些零件不需要更换,只须修复即可使用,对修复零件制订合理的有效的修复工艺单。
3、检修和装配
以上两项工作完成后,就可以对各零部件实施检修。更换零件按明细表一一配齐。有备件的采用备件,但也要检查是否符合更换零件的要求,有配合要求的,其尺寸公差和形位公差必须满足互换性要求。如果是标准件,就需要检查其型号、规格必须符合要求。如果某更换零件没有备件,就应反时按加工图纸制作。如果连图纸都没有,就需要重新翻绘该零件,绘出零件加工图,然后及时制作以供更换使用。修复零件则应按修复工艺单进行修复。关于易损件的更换和修复将在本章第二节详述。
更换零件全部配齐,修复零件也全部加工完毕后就可以进行装配。装配顺序正好与拆卸顺序相反,在装配过程中千万不能搞错。装配时要注意保证装配精度,不但要知道各零部件之间的装配关系,而且还要明确它们之间的相对位置要求,如平行、垂直、同轴、径向跳动、轴向窜动等等都不能超过设备工作精庭要求的许可范围。装配时,要边测量边装配,步步把关,不得马虎。
为了便于组织装配和分析装配中的问题,通常把设备的装配过程分为三个阶段。
先是组件装配,我们把将设备最基本的单元——零件连接组合成为组件的操作过程,称之为组件装配。
然后是部件装配,我们把将组件、零件连接组合成为独立的机构即部件的操作过程,称之为部件装配。
最后进行总装配,总装配是将部件、组件、零件连接组合成为整台设备的操作过程。
在制桶设备中修时,常用的组件装配有圆柱齿轮传动的装配、滚动轴承的装配和滑动轴承的装配。
①圆柱齿轮传动的装配。圆柱齿轮传动的装配是把齿轮装在传动轴上,然后将传动轴装入传动部件中。其主要技术要求有:保证齿轮的运动精度不降低,保证齿轮的接触精度,使沿轮齿的接触宽度和高度符合规定;保证两齿轮轮齿之间的侧隙符合规定。
为了保证齿轮的运动精度,首先要使齿轮正确地安装到轴上,使齿圈的径向跳动和端面跳动控制在公差范围以内。若发现不合规定时,可将齿轮取下,相对于轴转过一定的角度,再装到轴上。如果齿轮和轴用单键联接,就需要进行选配。
相互啮合的接触斑点可用涂色法检验,图3-4 所示为齿轮啮合接触斑点的不同情况:(a)为齿轮传动装配正确时的接触情况;(b)为齿轮传动副装配后的中心距大于加工时的齿轮中心距的情况,这是由于两齿轮轴的轴承座间距过大或是由于轮齿切得过薄所致,此时可调整轴承座间距或将齿轮更换;(c)所示的接触情况,是由于装配中心距过小或轮、齿过厚造成的,改进方法同(b);(d)表明了由于齿轮的齿向误差或齿轮轴线安装不平行引起的齿面接触情况。此时必须提高轴的安装平行度或齿轮副的齿向精度。
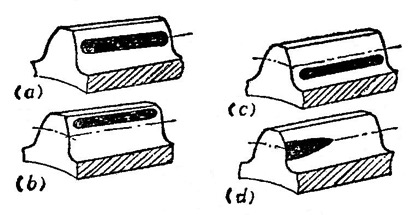
图3-4 齿轮啮合接触斑点
齿侧间隙的测量方法可用塞尺,对大模数齿轮则可用铅丝,即在两齿间沿齿长方向放置3至4根铅丝,齿轮转动时,铅丝被压扁,测量压扁后的铅丝厚度即可知其侧隙。侧隙不合要求的需要调整轴承座或更换齿轮来加以改进。
②滚动轴承的装配。径向滚珠轴承、圆锥滚子轴承和止推轴承在各种制桶设备中广泛采用,下面分述其装配方法和注意问题。
径向滚珠轴承的安装为了使轴承安装时均匀受力,常通过心棒使用手锤或压力机将轴承压入。如图3-5所示。(a)若要将轴承压到轴上时,要施力于内圈端面上;(b)压到机体孔中时,要施力于外圈端面上;(c)当同时压到轴上和机体孔中时,应能同时靠住内外圈的端面压入。
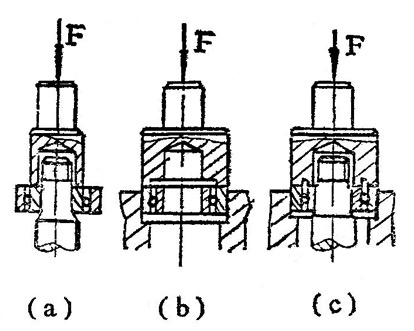
图3-5 径向滚珠轴承的安装
安装之前,应把轴承、轴、孔以及油孔等用煤油或汽油清洗干净,避免污物和硬的颗桂掉入轴承,以防擦伤滚珠表面。需用黄油润滑时也要涂上清洁的黄油。
轴承安装后要检查滚珠是否被咬住,是否有合理的间隙以补偿轴承工作时的热变形。检查径向间隙的最简单方法是用手沿轴向推动抽承的内环或外环,一般单列径向滚珠轴承的轴向移动量约为径向间隙的12~20倍,其值视轴承系列的不同约为0.1~0.7毫米,这是可以用手感觉到的。
圆锥滚子轴承的安装,圆锥滚子轴承是分开安装的,内环与保持器一起装在轴上,外环单独装在机体中,如图3-6所示。装配后,轴承间隙的大小与轴承在轴上或在机体中也的配合、无关,而是在装配时控制内外环沿轴向相对移动的距离C。径向间隙量e与轴向移动量C的关系为:
e=C?tgβ
式中β为轴承的安装角,如图3-7所示。
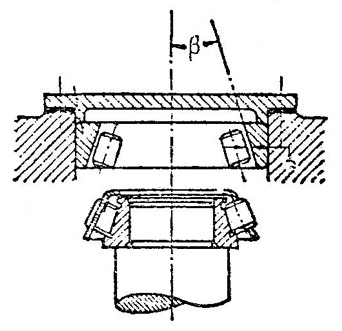
图3-6 圆锥滚子轴承的安装
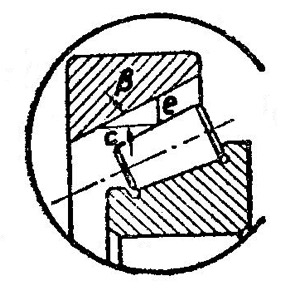
图3-7 圆锥滚子轴承的安装角
止推轴承的安装:安装止推铀承时,一轴承环紧装在轴上,另一轴承环装在机体的孔座内,且必须具有0.2~0.3毫米的间隙a,如图3-8所示。否则由于轴心线的对中误差将使轴承迅速磨损。
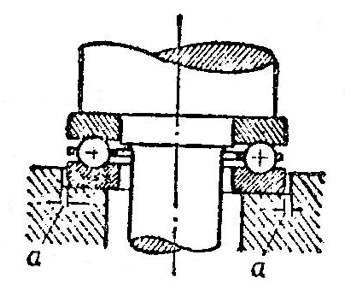
图3-8 止推轴承的安装
③滑动轴承的装配。滑动轴承分为整体式(轴套)和对开式(轴瓦)两种。下面分述其装配方法和注意要点。
整体式轴套的装配轴套装到机体内的顺序是:首先压入和固定轴套,然后作装配后的检验并进行修整。
装配时,根据轴套的尺寸和配合的过盈量大小以及轴套在机体上的位置,可采用冷压、加热机体或冷却轴套的方法装入轴套。图3-9所示是最简单的压入轴套的方法,即用垫板和手锤压入。开始时必须放正位置,使轴套和机体孔对正,边压边检查,待压正后,再加大力压入。否则会使压合表面擦伤或使轴套变形。较长的直筒轴套在压入时可在轴套外加一个导向套,防止轴套在压入过程中歪斜。
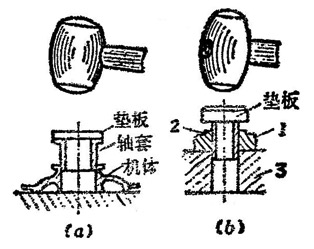
图3-9 轴套压入方法一
1-导向套;2-轴套;3-机体
为了保证轴套与机体孔的中心对正,可用如图3-10所示的工具。工作时, 轴套先套在特制的心轴上,然后拧上垫板,将心轴的下端放入孔内,经垫板来传递手锤或压力机的压力,将轴套压入孔内。对磨损厉害,经常要更换的轴套,采用这种专用工具很适合的。
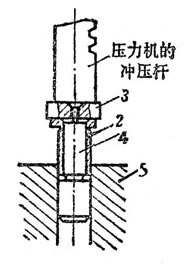
图3-10 轴套压入方法二
1-压力机的冲压杆;2-轴套;3-垫板;4-心轴;5-机体
在压入轴套前,必须仔细检查轴套和机体上的孔,修整端面上的夹角,擦净接触表面,并涂上润滑油,有油孔的轴套压入时要对准机体上的油孔。直径过大或配合过盈量大于0.1毫米时,可采用加热机体或冷却轴套的方法装配。
轴套压入后,为防止转动,可用螺钉、销钉或骑缝螺钉固定,如图3-11所示。不带凸肩的轴套压入机体要求与机体端面平齐。
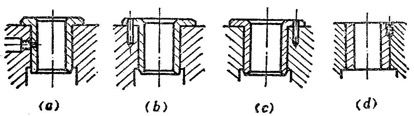
图3-11 轴套固定方法
(a)螺钉固定;(b)(c)销钉固定;(d)骑缝螺钉固定
轴套压入后,往往发生变形,如变成椭圆形、圆锥形或产生偏斜,也有可能损坏工作表面。因比在装配后需要进行检查和修整。修整时常采用铰孔和刮削的方法,使轴套和轴颈之间的间隙及接触点达到要求的质量。
对开式滑动轴承(轴瓦)的装配在安装轴瓦时应注意轴瓦上的润滑油孔与轴承座孔间的重合对齐。通常是按配合的轴颈修配轴瓦,先在轴颈上涂一层极薄的铅油,让轴颈在轴瓦中加压后回转2~3转。在轴瓦上的斑点大小在3毫米左右,斑点应布满全轴瓦表面的75~80 %左右,在每平方厘米上有三个或更多的接触斑点。如达不到这些要求则应该继续修刮轴瓦,直到达到要求为止。
④较复杂的组件装配过程可以采用图解的方法表示,这种图称为装配单元系统图,其绘制方法如下。
(a)先画一条横线。
(b)横线的左端画一个框格代表基准件,即组件中用来装配其它零件的基准零件。在框格中要注明装配单元的编号、名称和数量。
(c)横线的右端画一框格,代表装配的成品。在框格中注明组件的编号、名称和数量。
(d)横线自左至右表示装配的顺序,直接进入装配的零件画在横线的上面,直接进入装配的组件画在横线的下面。每个零件或组件都用框格表示,并在框格中注明该零件或组件的编号、名称和数量。
装配单元系统图的示例见图3-12。由图可见,装配单元系统图可以一目了然地表示出成品的装配过程,装配所需的零件、组件的名称、编号和数量,并可根据它划分装配工序。因此它起到指导和组织装配工艺的作用。
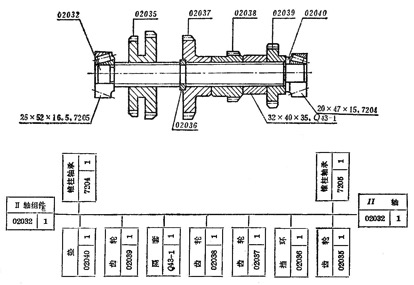
图3-12 装配单元系统图示例
在组件装配完成的基础上,即可进行部件的装配。在确定部件装配顺序时,要详细分析部件的装配图和传动系统图。根据基本结构和组合特点,初步拟定部件的装配程序。然后通过试装实践,进行修订,最后确定部件的装配程序。拟定部件装配程序的原则,大体是先下后上,先里后外,由主动到被动。因为部件是一个独立的机构,所以装配完毕的部件必须进行部件的空运转试验和精度检验。运转正常,精度合格后才能进入总装配。
总装配是将各部件用零件、组件连接成为一台完整的设备。在总装配过程中,除了也要注意装配顺序等问题外,最主要的是要保证设备的加工精度。在装配时,要做到边装配,边测量,边调整,使各项技术指标都达到要求为止。总装配完成后设备中修的具体检修工作也就完成了。
三、中修的试运验收
检修的制桶设备全部装配完毕后,必须经过试运验收后才能投入正常生产。由于中修是部分检修,因此对检修部分的检验就是中修后试运验收的重点。试运验收工作大体上包括以下五个方面。
①外表及附件的完整性。中修虽不是设备全部解体检修,但在部分解体时也要影响“左邻右舍”。所以在运行前先要检查一下所有附件全了没有,如果缺了什么要及时补上,以免影响设备正常运转。
②几何精度。在试运转前还要做的一件事,就是测量设备检修后的几何尺寸及其精度。几何精度包括各主要零部件之间的相对位置,如平行、垂直、位置距离等等;平移零部件的行程;各控制机构,如凸轮、挡块的安装位置等。测量所得尺寸不合要求的需要及时调整。
③空运转试验。做好以上两项工作后即可投入设备空运转试验。空运转试验中要注意传动系统的平稳,控制系统的协调合拍。尤其对中期修理部分的运转要特别关注。空运转中如发现问题,应及时调整解决。在空运转未正常之前,不得随意进入负荷试验。
④ 负荷试验。所谓负荷试验就是实际生产加工试验。主要检查设备在有负荷的情况下,其振动、冲击、.噪声、温升是否超过了许可范围。因为这些指标都可以反映出设备各方面的问题。有经验的操作工人可以直接从上述指标的异常中找出设备的问题所在。一旦发现问题,必须对症下药,及时解决。
⑤工作精度检验。工作精度检验可以在检验设备几何精度和空运转试验中作初步检验并及时解决存在的问题。但设备的工作精度最直接地是由生产的半成品或成品的质量上体现出来。因此,负荷试验生产出来的半成品或成品,必须作严格仔细的产品检验,并从中找出设备工作精度上的问题。以产品作为设备的一面镜子,及时调整设备,提高加工精度,直至达到工艺标准要求为止。在检验设备工作精度时要特别注意中期检修部分引起的质量问题,要掌握修前的工作精度状况并与之相对照,从而可以用来评价中修的检修质量。
至此,中修就全部完成了。检修后的设备即可投入正常制桶生产直至下一次计划检修。
|