《现场管理跟我学》
主讲/辛巧娟
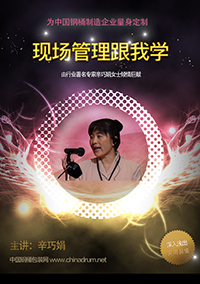
第二十七讲:三不原则
一、现场观念
现场管理的6个观念就是:以现场为中心,全员参与管理4MEI和QCDMSS;以下道工序为客户,持续改善达到零缺点。从现场质量管理的角度,“三不原则”(不接受、不制造、不流出)其实就是对这些观念的阐释和实施。质量是从组织内的每一个人,承诺绝不将不合格品或不完整的信息,送至下一流程开始。因为下一流程就是客户,绝不应把不合格品送至下一流程的客户,以免造成他们的不便。当每一个人都能认同、实现这个理念时,一个良好质量保证体系就能存在了。
“不接受不合棉品、小制造不合格品、不流出不合格品”的“三不原则”是许多公司的质量方针、质量目标、或者宣传口号,常在公司的墙壁或柱子上高高悬挂。
随着社会大生产的分工合作,任何产品都不太可能由一个人独立全部完成,产品总是分工序、分流程,包括职能部门间的工作协助,这些过程都是环环相扣,紧密相连。只要其中的某个环节出问题都将影响整个产品质量或工作质量。“三不原则”就是每个环节的质量保证原则。
“三不原则”的实施,意味着人人都要参与,人人都是主角,是全面质量管理(TQM)认真贯彻的要求和结果。“三不原则”的实施,导人了“供应商→客户”的市场关系,每个人既是供应商,又是客户,既是产品的使用者,也是制造者、供应者,因此每个人都要牢固树立“下道工序是客户”的观念。要实现“三不原则”,要做到“不制造不合格品”,这就要求我们第一次就把事情做对,要求我们以“零缺点”的观念和方式工作。因此,要实施“三不原则”,使“三不原则”不仅仅是顺溜的口号,现场管理还有很多工作要去做。
二、基本做法
“三不原则”的基本做法是:
不接受不合格品,指员工在生产加工之前,先对前道传递的产品按规定检查其是否合格,一旦发现问题则有权拒绝接受,并及时反馈前道工序。前工序人员需要马上停止加工,追查原因,采取对策,使质量问题得以及时发现、及时纠正。并避免不合格品的继续加工所造成的浪费。
不制造不合格品,指接受前道的合格品后,在本岗位加工时严格执行作业规范,确保产品的加工质量。对作业前的检查、确认等准备工作做得充分到位;对作业中的过程状况随时留意,避免或及早发现异常的发生,减少产生不合格品的几率。准备充分并在过程中得到确认是不制造不合格品的关键。只有不产生不良品才能使得不流出和不接受不良品变为可能。
不流出不合格品,指员工完成本工序加工,需检查确认产品质量,一旦发现不良品,必须及时停机,将不良品在本工序截下,并且在本工序内完成处置和防止对策。保证传递的是合格产品,否则会被下道“客户”所拒收。
每个员工必须对本工序的产品何为“合格”、“不合格”以及“异常”的三种状况界定得非常清楚明确。知道标准化作业是制造合格品的关键,但同时还必须知道制造不合格品的原因,也就知道避免不合格产生的措施,并进一步去认真落实这些预防措施,执行标准作业。
“三不原则”的实施使每一个岗位、每一个员工都建立起“生产出使自己和顾客都满意的产品”的信念,一根无形的质量链贯穿于生产的全过程,制约着每个操作者,使流程的各个环节始终处于良好的受控状态,进人有序的良性循环。通过全体员工优良的工作质量从而保证了产品的质量。
三、实施要点
“三不原则”是现场质量保证的一个运行体系,在实施过程中需注意以下要点:
1、谁制造谁负责的要点:一旦产品设计开发结束,工艺参数流程明确,则产品的质量波动就是制造过程的问题。每个人的质量责任从接受上工序合格产品开始,规范作业确保本工序的产品质量符合要求是员工最大的任务。一旦在本工序发现不良或后道工序反馈不良,该人员必须立即停止生产,调查原因,采取对策,对产品的质量负责到底。
2、谁制造谁检查的要点:产品的生产者,同时是产品的检查者,产品的检查只是生产过程的一个环节。通过检查,确认生产是否合格,也确保合格产品流人下道工序。通过自身检查,作业者对本工序加工产品的状态了解得更清楚,也有利于员工不断提升加工水平,提高产品质量。
3、作业标准化的要点:产品从设计开发、设定工艺参数开始,就要对所有的作业流程中的作业步骤、作业细节进行规范化标准化,并不断予以完善。每一个员工也必须严格贯彻标准化作业。标准化是该工序最佳的作业方法,是保证产品质量一致性的唯一途径,否则制造一大堆不良品并且找不到不良的根本原因,这个时候“三不原则”只有制造混乱,而不是质量。
4、全数检查的要点:所有产品所有工序无论采取什么形式都必须由操作者实施全数检查。
5、工序内检查的要点:质量是制造出来的,如果安排另外的检查人员在工序外对产品进行检查或修理不仅是浪费,也不能提高作业者的责任,反而姑息作业者对其产品质量的漠视。
6、不良停机的要点:在工序内一旦发现不良,操作者有权利也必须有责任立即停止生产,并立即采取调查对策活动。
7、现时处理的要点:在生产过程中,发生不合格品时,作业者必须从生产状态转变到调查处理状态,马上停止作业并针对产生不良品的人机料法环信等现场要素及时确认,调查造成不良的“真正元凶”并及时处理。
8、不良曝光的要点:在生产过程中出现的任何不良,必定有其内在的原因,只有真正解决了发生不良的每个原因,才能不制造不合格品,实现零缺点,才能让客户真正满意。因此,对于发生不良不仅作业者知道,还必须让管理阶层知道,让品质保证的人员知道,让设计开发的人员知道,大家认真分析对策,并改善作业标准。而不是简单地由作业者对不合格品自行返工或报废,否则下一次还会发生同样的问题。
9、预防和防错的要点:产品的质量不能够完全依赖于操作者的责任心来保证,任何人都会有情绪,会有惰性,会有侥幸心理,以及一些意外因素的干扰,从而使产品质量出现波动。因此必须尽可能科学合理地设计使用防错装置来防止疏忽。同时在现场管理中,认真进行细节管理,尽量把工作做在前面,周全的计划,充分的准备,事先的预防,减少各种差异变动,把质量控制在要求的范围内。
10、管理支持的要点:作业者承担产品的质量责任,但产品出现不良,管理阶层应该承担更多的责任,因为管理人员的职责就是帮助员工解决问题。当员工发现问题并报告问题,管理人员应第一时间出现在现场,一起调查处理问题。对于不良品,若只是轻率地推卸责任给作业者,不仅不能彻底解决不合格品的产生,而且易造成管理阶层与普通员工的对立。管理人员有责任培训教育员工,对员工进行指导,事先预防问题的产生,要和员工共同分析、调查解决问题,须提供配备员工所需的资源设施,须帮助解除员工生活上的后顾之忧……总之,管理人员必须是员工坚强的后盾,那么“兰不原则”才能真正在现场中落实。
返回目录