《设备管理与维修》
主讲/辛巧娟
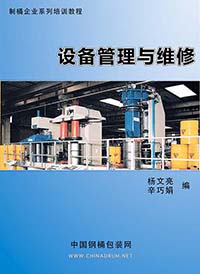
第八讲:管理指标和管理流程图(下)
四、设备管理指标体系
1、设备管理的指标体系。
由于设备管理与维修工作涉及物资、财务、劳动组织、技术、经济和生产计划等诸方面,要检验和衡量各个环节的管理水平和经济效益,就必须建立和健全设备管理的技术经济指标和指标体系。
指标体系由一系列具体的技术经济指标构成。这些指标设置的目的是对设备管理和维修工作进行控制、监督、显示、评价和考核。
传统的设备管理与维修指标体系主要由技术指标和经济指标两大部分构成:
(1)技术指标如下:
·设备完好指标主要有:主要生产设备完好率和设备泄漏率,完好率的考核线条较粗,逐渐被淘汰,取而代之的是设备综合效率(OEE)和完全有效生产率(TEEP)等。
·设备利用指标主要有:反映设备数量利用指标,如实有设备安装率;反映设备时间利用的指标,如设备利用率、设备可利用率等;反映设备能力利用的指标,如设备负荷率。
·新度指标主要有:设备有形、无形以及综合磨损系数,设备新度系数。
·设备精度指标主要有:设备精度指数。
·设备故障控制指标主要有:设备故障率、故障停机率、平均故障间隔期以及事故频率。
·设备构成指标包括:设备数量构成百分数和设备价值构成百分数。
·维修质量指标主要有:大修理设备返修率、新制备件废品率、一次交验合格品率以及单位停修时间。
·维修计划完成指标主要有:设备大修理计划完成率、设备大(小)修理任务完成率等。
·维修效率指标:如钳工年修复杂系数。
·更新改造指标:如设备数量更新率、设备资产更新率、设备资产增产率的等。
·备件适用指标:如备件品种适用率、备件数量造用率、备件图册满足率。
(2)经济指标如下:
·设备折旧基金指标:如设备折旧率。
·维修费用指标:如净产值设备维修费用率、设备平均大修理成本、单位产品维修费用等。
·备件资金指标:主要有备件资金占用率、备件资金周转率、备件资金周转天数等。
·维修定额指标:如工时定额、费用定额、停修定额、材料消耗定额等。
·能源利用指标:如产值花能率、成本耗能率、单位能耗率、综合能耗率等。
·设备效益指标:如设备资产产值率、设备资产利税率、设备资产利润率。
·设备投资评价指标:如投资回收期、投资效果系数等。
2、设备管理考核指标。
依据《设备管理条例》的规定和企业制定的设备管理制度,对设备管理工作都有一定的考核指标。由于行业不同,企业的设备管理考核指标也不相同,但考核的项目基本相同。
(1)考核企业的指标如下:
·主要生产设备完好率:要求机械设备90%以上;动力设备95%以上。
·设备可利用率:要求达到95%以上。
·设备故障停机率:控制在1%以内。
·设备大修理成本:控制在300元/F~350元/F(F为修理复杂系数)。
·万元产值维修费用:要求逐年下降,达到同行业先进水平。
·大修理停修天数:平均在3天/F以内。
·大修理设备返修率:要求控制在1%以内。
以上为制造行业的部分考核指标,其中完好率与复杂系数的概念比较陈旧,仅作为考核指标推陈出新的参考和过渡。
·设备大修理计划完成率。
·主要生产设备事故频率。
·设备固定资产利税率。
·备件资金周转率。
·企业能源利用率。
(2)考核使用部门的指标如下:
·主要生产设备完好率。
·设备事故频率。
·定期保养完成率。
·设备故障停机率。
·设备利用率。
(3)考核设备管理和维修部门的指标如下:
·大修理计划完成率。
·维修成本费用。
·大修理质量返修率。
·主要生产设备完好率。
·重大设备事故。
上述指标在引导企业设备管理进步方面曾起到积极的作用。随着生产力的进步,有些指标已陈旧过时,甚至被淘汰;有些指标仍发挥着有益的评价作用。随着企业管理的深化,对设备管理评价指标体系也在不断完善,正沿着科学性、系统性、准确性、公正性等方面发展,使其更好地引导和激励人们关心设备管理工作。
3、目前运用的设备管理指标
现代设备管理强调获得较高的设备综合效率和降低设备的寿命周期费用,追求的目标是最佳经济效益,是把技术管理与经济管理相结合起来。设备综合效率和设备的寿命周期成为是现代设备管理指标的重点。
(1)设备综合效率。
设备的综合效率(OEE,Overall Equipment Effectiveness)通常在设定的OEE=时间开动率×性能开动率×合格品率计算公式中,由时间开动率、性能开动率和合格品率来反映影响设备综合效率的停机损失、速度损失和废次品损失,使各类损失定量化,并可及时用量化的数据来描述改善的效果。时间开动率反映了设备的时间利用情况;性能开动率反映了设备的性能发挥情况;而合格品率则反映了设备的有效工作情况。反之,时间开动率度量了设备的故障、调整等项停机损失;性能开动率度量了设备短暂停机、空转、速度降低等项性能损失;合格品率度量了设备加工废品损失。设备的综合效率(OEE)计算公式为
设备综合效率(OEE)=时间开动率×性能开动率×合格品率
只有综合效率才能反映设备的管理水平,提高设备综合效率,就是要充分利用和发挥企业现有设备的潜力,为发展生产和搞好建设,以及为增加社会财富服务。一般设备综合效率大于或等于80%为好的设备综合效率越大越好,表明设备的管理水平越高。
针对设备中的浪费内容进行分析、采取对策,将设备维持、管理在无浪费( “零不良”、“零故障”、“零灾害”)的极限状态。设备综合效率与六大损失的关系如图8-3所示。
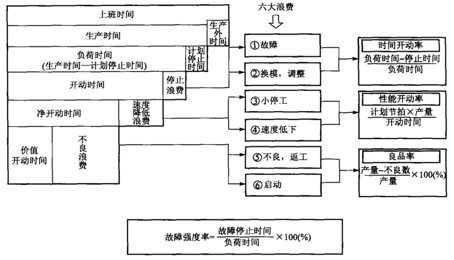
图8-3 设备综合效率与六大损失的关系
设备综合效率指标用语见表8-1所示。
表8-1 设备综合效率指标用语
用语 |
定义 |
设备综合效率 |
设备在负荷时间中有多少时间是有价值的开动。是衡量设备综合性时间浪费大小的指标 |
上班时间 |
一般指8小时制度工作时间。如果有延点时间,应该计算在上班时间内。如果未满8小时则按实际时间计算 |
生产时间 |
是必须从事生产活动的时间,要减去午休时间和生产完成后的生产外停止时间(如生产完成后的清扫、学习、会议等时间不能计算在内) |
负荷时间 |
为了完成生产计划而必须开始设备的时间。
负荷时间=生产时间−计划停止时间 |
计划停止时间 |
在生产时间内有计划地停止的时间。如日常管理上必要的早晚会、休息时间、点检时间、试制时间等 |
开始时间 |
设备实际开始的时间,要从负荷时间减去故障、换模、调整、待料等的停止时间 |
净开动时间
价值开动时间 |
从开动时间中减去空转、小停工以及因速度降低导致的浪费时间。一般按以下公式计算:
净开动时间=计划节拍×产量
从净开动时间中减去因不良品而追加生产的所需时间。一般按以下公式计算:
价值开始时间=计划节拍×良品数 |
时间开始率 |
是衡量因故障、换模、调整而发生停止浪费大小的指标为
时间开动率(%)=(负荷时间−停止时间)×100/负荷时间
=负荷时间×100/负荷时间 |
性能开动率 |
是衡量因空转、小停工以及速度降低导致时间浪费大小的指标为
性能开动率(%)=速度开动率×净开动率
=计划节拍×产量×100/开动时间 |
速度开动率 |
是衡量在性能开动率中因速度降低而发生时间浪费大小的指标为
速度开动率(%)=实际节拍×100/开动时间 |
净开动率 |
是衡量在性能开动率中因空转、小停工而发生时间浪费大小的指标为
净开动率(%)=实际节拍×产量×100/开动时间 |
设备中的六大损失的内容见表8-2所示。
表8-2 设备中的六大损失的内容
序号 |
损失名称 |
损失内容 |
目标 |
备注 |
1 |
故障损失 |
因突发性或慢性发生故障而引起的时间损失 |
零 |
|
2 |
准备停止损失 |
伴随着准备替换而发生的损失,指的是直到生产出合格品为之所需的时间损失 |
最小化 |
|
3 |
突然停止损失 |
因临时故障而停止或者空转相伴的时间损失 |
零 |
|
4 |
速度降低损失 |
根据相关于设备计划周期时间和实际周期时间之差而引起的时间损失 |
零 |
|
5 |
不良修理、修理损失 |
因错误和修理而产生的物品损失和工时损失,以及再生产所需时间的时间损失 |
零 |
|
6 |
启动损失 |
从开始生产到产品稳定之间所发生的损失,起因主要是加工条件不稳定,模具、辅助夹具维护不良,作业者不最小化熟练等 |
最小化 |
|
(2)设备寿命周期。指设备从开始投人使用时起,一直到因设备功能完全丧失而最终退出使用的总的时间长度。设备寿命周期费用是设备从研究、设计、制造、安装、调试、使用、维护、修理、改造和报废的整个寿命周期内所消耗费用的总和。
五、运用管理流程图提高工作效率
1、运用管理流程图可提高设备管理的工作效率。
流程管理可以在企业内部让所有部门和员工看到彼此的联系并且按照这种方式工作,具有目标导向和绩效导向作用。
在设备管理中,充分利用管理流程图,对设备的日常管理起到快速、高效、规范的作用,能满足车间快节拍的生产需要。管理流程图对设备运行过程中各种要素进行梳理,衔接各环节,明确各自的职责、及时进行信息反馈。同时,运用管理流程图绘制车间产品工艺流程,能清楚设备布局是否能消除人、机、料、法、环各个环节上的浪费,是否有利于提高工序能力、减少搬运、提高设备使用率、提高空间利用率、减少作业量,适宜作业环境的改善等,符合精益设备布局要求,管好、用好设备,减少设备故障、提高设备综合效率,从而提高企业经营效益。
2、掌握管理流程图的绘制原则及方法。
设备管理流程图的绘制原则如下:
(1)遵循企业实行的质量管理体系中的设备管理程序文件。
(2)熟知企业不同的部门(或岗位)在设备管理过程中的职能,分清主流程和旁路流程。
(3)不同部门或岗位的衔接和配合要有清楚的横向关系以及准确的“接口”描述。
(4)遵循计划、实施、检查、改进的PDCA工作循环。
(5)绘制尽量简单、清晰、有步骤、便于阅读,有条理地表达设备工作流程和车间工艺流程图。
管理流程图的绘制方法如下:
(1)选择和确定绘制对象。
(2)收集资料,分列工作步骤,即先不考虑每项处理由谁做和根据什么做以及有何具体要求,只是单一列举工作内容。
(3)加入信息资料的输入和输出,此处的信息包括内部环节之间的交流,也包括与外界的交流。前者一般只列正式的部分,后者则应具体。
(4)列入部门,即按实际情况将每一处理步骤安排在相应的部门/岗位的位置之下,也是确定由谁做的问题。至此已形成了流程图的草图。
(5)反复核实和修正草图,应仔细斟酌其中的每一步骤和环节。
(6)加人有关的要求或说明,绘出正式的业务流程图。绘图时,对现状的调查、了解是最主要的工作量。
绘制流程图的常见符合和错误如图8-4所示。
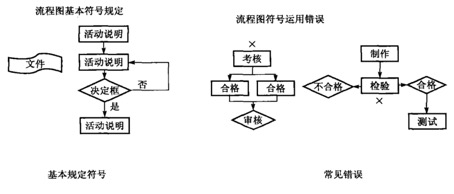
图8-4 流程图的常见符号和错误
返回目录