《设备管理与维修》
主讲/辛巧娟
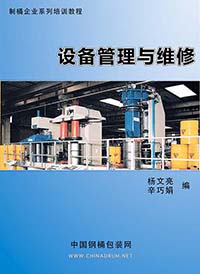
第五讲 设备定期点检作业
设备定期点检是按设备预防维修计划,定期对设备功能性和技术性进行检查,通过定性与定量的掌握设备运行状态,准确把握设备潜在的故障,采取针对性强的预防措施,把故障消除在萌芽状态之中。
本讲学习目标是:
(1)正确认识设备定期点检的作用和意义。
(2)掌握设备定期点检的工作内容与工作流程。
(3)能够进行数控机床定期点检作业。
一、设备定期点检的作用和意义
设备定期点检也就是通常所说的预防检查。按照设备不同的特性,间隔一定时间,依靠人的五感及检测仪器,对其运行的状态定期地进行检查,再根据测量的数据和检查的结果、作业动态的过程记录,进行综合性的分析、研究,预测故障的发生,及早地发现隐患,采取适当的预防措施,把设备故障消灭在萌芽状态。
定期点检的主要项目在时间间隔上相对较长,检查、检测的劣化主要是设备运行过程中,由于受到各种力的作用、运行环境、工作条件的影响,导致零件、部件、机构会逐渐磨损、松动,损耗周期相对较长,精度的变化等。
二、设备定期检查的对象、目的及内容
设备定期点检主要是对设备进行定期的功能性、精度性、可靠性检查和检测,通过对设备状态的定量和定性数据收集,进行综合性的分析、研究,预测故障的发生,及早地发现隐患,预防设备故障的发生。一般设备定期检查的对象、目的及内容见表5-1。
表5-1 设备定期检查的对象、目的及内容
序号 |
名称 |
执行人 |
检查对象 |
检查内容和目的 |
检查时间 |
1 |
性能检查 |
主要:维修工、点检员;协作;操作员 |
主要生产设备(包括重点设备及质控点设备) |
掌握设备的故障征兆及缺陷,消除在一般维修中可以解决的问题,保持设备正常性能,并提供为下次计划修理的准备工作意见 |
按定检计划规定时间 |
2 |
精度检查 |
主要:维修工、点检员;协作;操作员 |
精密机床、大型、重型稀有及关键设备 |
掌握设备的故障征兆及缺陷,消除在一般维修中可以解决的问题,保持设备正常性能,并提供为下次计划修理的准备工作意见 |
每6~12个月进行一次 |
3 |
可靠性试验 |
指定试验检查人员、持证检验人员 |
起重设备、动能动力设备、高压容器、高压电器等有特殊试验要求的设备 |
按安全规程要求进行负荷试验、耐压试验、绝缘试验等,以确保安全运行 |
以安全要求为准 |
但设备定期点检具体内容还与企业的生产性质、设备类型、设备故障频率、设备故障停工影响、维修人员数量、设备使用状况等有关。
设备定期点检针对设备故障是以磨损、腐蚀为主或松动等类型。这类项目平时检查比较困难或需要时间较多:如刹车片(制动片)、离合片的磨损、离合器行程;轨道水平、机床精度等;滑触线接口、电线电缆接头的松动;集电器、电机电刷等的磨损消耗;电机的绝缘电阻、接地点的接触检查;轴承润滑、油质测试;油气密封圈等。
(1)点检标准值是按设备技术状态的完好标准,设备完好标准的一般要求和电控系统完好标准(详见第四讲)要求进行检查。
(2)设备定期点检是按标准作业指导书中的项目进行,主要分为两大部分:一是设备的机械部分,包含液压、机械传动、气动等部分;二是设备的电控部分。
由于行业、企业产品、设备不同,设备定期检查的对象、目的及内容也就不同。如设备定期检查内容及判定方法见表5-2。
表5-2 金属切削机床定期检查内容及判定方法
检查部位 |
检查重点 |
检查内容 |
检查方法及判定标准 |
设备主体、主工作部件、主传动装置及变速、换向装置 |
机体 |
振动、裂纹、破损、腐蚀 |
检查机身、支柱、机架等有无异常振动、破损、裂纹、腐蚀等 |
用目视及接触 |
加工部件(胎模等) |
振动、破损 |
检查运转中有无异常振动及主轴的振摆,必要时用千分表测定 |
以有无异常振动及加工件精度为标准,判定微动的振动情况 |
主机轴承 |
温度、破损 |
用触觉检查转动中的轴承温度,用工作精度检查轴承的磨损 |
如温度较高时可用测温计,正常测试应在室温30℃之下;不允许有影响精度的波纹存在 |
齿轮变速装置 |
噪声、振动、破损、损伤 |
检查运转中齿轮的噪声、振动、齿轮啮合情况,磨损和损伤程度 |
用视觉、听觉和触觉检查噪声、振动和磨损。异常的噪声、振动、啮合误差及磨损不得超出规定标准 |
操作装置 |
操纵动作 |
检查操作动作是否灵敏、各级变速是否正确可靠 |
进行运转操作,正反向动作应平稳灵敏可靠 |
换向装置 |
操纵动作 |
检查操作动作的性能是否灵敏 |
进行运转操作,正反向动作应平稳录敏可靠 |
启动/停止装置 |
操纵动作 |
启动、停止装置是否灵敏、正确、可靠 |
进行操作,启动、停止时不应有冲击现象;启动、停止动作要灵敏可靠 |
传动装置 |
磨损、损坏、变形、松弛 |
检查三角皮的根数、磨损、变形、松弛;检查皮带轮、链轮、链条的磨损变形;传动用的连接器、齿轮、丝杆副的磨损情况 |
修整 |
滑动面进给操纵 |
伤痕、磨损、保护装置操纵动作 |
检查滑动面有无新的伤痕、磕碰及磨损;检查润滑情况;检查导轨行程的保护装置是否良好;进行手动和自动进给,检查全行程的进给行程 |
进行操作,启动、停止时不应有冲击现象,启动、停止动作要灵敏可靠;操给检查,自动进给时应均匀,不得出现中断、停滞现象;中断时不得出现进给 |
电气装置 |
电气控制线路与接地 |
异声、温度、振动、绝缘动作 |
电动机运转时有无异声、振动及不正常发热;控制线路是否完整,绝缘是否良好,动作是否可靠,接地是否良好 |
用听觉及触觉检查应无异声和异常振动,温度要符合规定要求;目视和万能秒表检查,线路应完整、动作可靠,绝缘在0.2MΩ以上,保险元件符合规定接地装置 |
液压、润滑系统 |
液压及润滑装置 |
压力、动作、油质、泄漏 |
检查系统压力是否正常,动作是否平稳,油质是否良好清洁,有无泄漏 |
目视检查,压力符合规定,液压传递平稳,油质清洁良好,无泄漏现象 |
三、设备定期点检周期的选取
1、与设备性能劣化过程过程有关。
点检周期与P-F间隔有关。P-F间隔期是指设备性能劣化过程,从潜在故障发展到功能故障的时间间隔。潜在故障不是故障,但已经存在可感知的迹象,相当于人处于亚健康状态;功能故障是使设备丧失功能的故障,是真正意义上的故障。
P-F间隔的理论是指导确定点检周期的根据。设备性能曲线上的P-F间隔如图5-1所示。从图5-1中可以看出,不同的设备其设备性能曲线的斜率是不一样的,因此点检周期的长短也是不相同的。一般而言,点检周期不应超过P-F间隔,而且要留出预防维修的准备时间。例如,如果P-F间隔为3.5个月,留有0.5个月的预防维修准备时间,点检周期为3个月为宜。
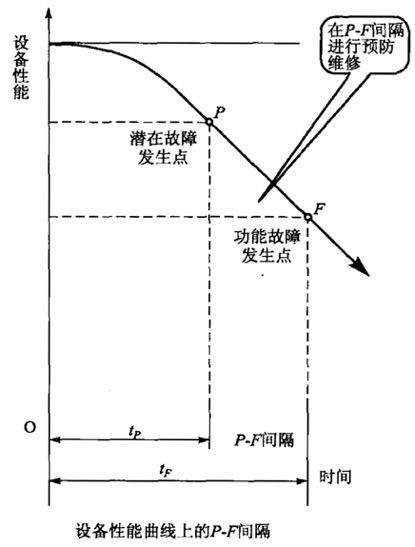
图5-1 设备性能曲线图
2、与设备运行的生产制造工艺有关。
设备是为生产、制造产品服务的,生产制造工艺简单,设备功能相对也就单一,点检周期可长一些;反之,产品精密,生产制造工艺繁杂,对设备要求高,点检就也得勤一些,几乎每班,甚至在一个8小时内就要点检数次才行。其次,点检周期还与工艺的可行性有关,如旅客列车、航班飞机的点检,必须在停站时才能进行,这时的点检周期,就必须是这站路程的时间。所以,在火车在停站时,人们经常会昕到有铁路员工拿着点检锤,在点检敲击机车的避振弹簧、机车轮毅等的声音。
3、与设备的安全运行有关。
必须保证设备运行安全,点检周期的长短不能超过设备功能故障发生的时间,否则就失去意义了。
总之,设备定期点检周期是与设备性能劣化过程、企业的生产性质、设备类型、生产班制、工作环境等因数来定的,既要达到解决问题又要防止维修过剩,节约成本。
四、设备定期点检的方法和手段
1、对于设备功能性的检查。
主要通过人的五感(视、听、嗅、味、触)或简单的工具、仪器,按照预先定期点检标准规定的周期和方法,对设备上的规定部位(点)进行有无异常的预防性周密检查。通常为平时检查比较困难或需要检查时间较多的设备部位。
2、设备技术性能的检查。
主要是运用设备故障诊断技术,如图5-2所示。设备诊断技术就是利用各种检测器械、仪器仪表对设备重要部位进行检测,以获得设备运行的技术状态变化的数据、参数等准确信息,再通过数据统计分析,发现设备异常,进一步分析产生设备故障的原因,及时把故障消除在萌芽状态之中。应尽可能在不拆卸设备的情况下,准确把握设备的现状,定量地检测的评价设备性能、设备的可靠性。因此,定期系统地检查设备的状态,及时掌握设备运行时的精度情况,从而保证产品的质量。
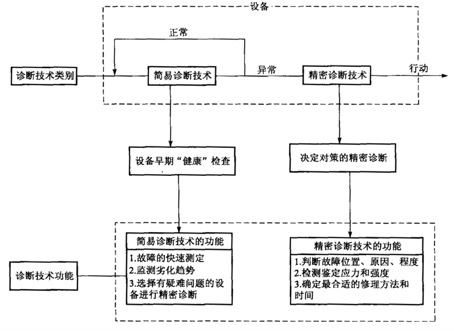
图5-2 设备诊断技术功能图
(1)静态检测法。检查、测量设备处于静态下的几何精度等参数,如机床的平行度、水平度、垂直度、导轨间隙等。
(2)油样分析法。一般情况下,机械设备的磨损过程也是其材料表面剥落成微粒的过程,特别是以油为工作媒介的设备,如油压机、机械压力机的油路部分等。通过分析油样中所含的磨损的微粒或油质,在不拆卸设备的情况下了解设备表面、密封等磨损的程度,主要运用于液压设备液压油或润滑油等。采用油质质量测试仪,可以检测油中的水分含量、某种直径(如60μm以上)的金属颗粒,如图5-3所示。
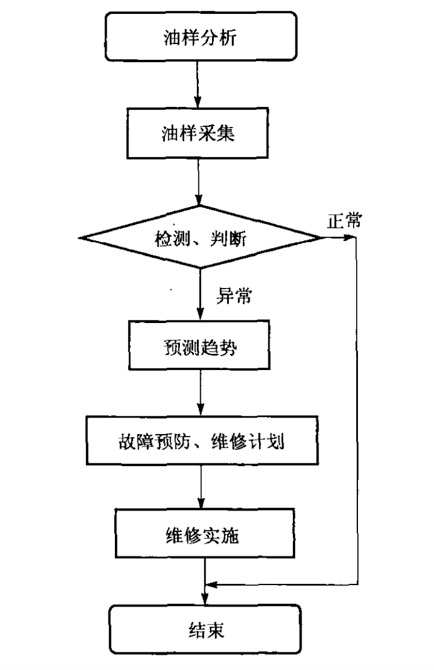
图5-3 分析油样的步骤
五、设备诊断技术运用步骤
1、检测。运用各种检测手段对设备的重点部位进行检测,并记录相关数据。
2、判断。根据检测数据结果,对照设备完好标准、出厂参数、验收参数记录等进行判断得出设备状态的结论:正常、异常。
3、分析异常原因。
4、谋求对策。
六、设备诊断技术的运用范围
设备诊断技术运用范围很广,几乎所有的设备都可以运用,但设备诊断技术的运用主要依赖于价格不菲的检测设备,这就在一定程度上限制了其广泛应用。企业设备管理部门应从厂情出发,结合实际,推广和使用一些设备诊断技术。一般情况下,以下四种类型的设备应尽可能考虑使用。
1、发生故障影响很大的设备,特别是自动化程度很高、节拍快的流水生产线以及相关的联动设备。
2、安全性能要求高的设备,如动力设备、锅炉飞压力容器等。
3、精、大、稀设备。
4、停机维修费用高、损失大的设备。
七、设备定期点检作业流程图
1、按预防维修计划,依据《设备定期点检标准作业指导书》,组织和安排维修工,明确职责。
2、从《设备定期点检标准作业指导书》中,了解从设备定期点检的项目、完好的标准(参数)和检查的方法、检查的时机(停机状态还是运转状态),检查的周期。
3、状态检查和监测。点检员依据《设备定期点检标准作业指导书》逐项检查、检测,并做好记录。
4、分析判断。收集到检测数据后,通过比较、对照,分析、判断有无异常。
5、差距调整。标准-实测=差距。差距不在正常值范围之内时,就要对其进行调整,某些设备如果确实无法达到出厂值或者验收标准,就需要工艺部门进行确认能否满足企业的生产工艺要求。如果仍然无法达到生产工艺要求,就要考虑大修或改造了。为了提高设备定期点检作业效率,进行规范管理,制定了设备定期点检作业流程如图5-4所示。
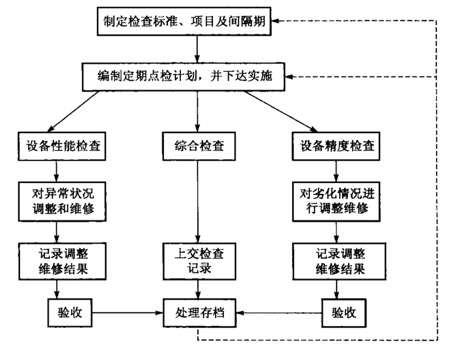
图5-4 设备定期点检作业流程图
返回目录