《设备管理与维修》
主讲/辛巧娟
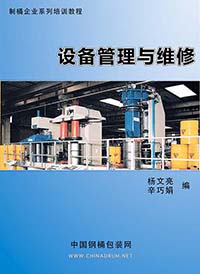
第十六讲:生产车间现场5S管理
5S是一种生产基础管理体系和方式,其宗旨是从工作习惯上提高现场工作效率,降低成本,防呆防错,提高质量,追求员工素质的整体优化,又是形成规范的、优秀的、创新的企业文化的前提基础。在设备管理中也是推行5S,改善设备操作环境,强化设备维护基础工作,养成按标准进行清扫、点检、紧固、加油的职业行为,提高工作效率和产品质量,努力实现“零浪费”。
本讲的学习目标是:
(1)了解开展5S活动作用和意义。
(2)掌握5S内容和方法。
(3)了解设备可视化管理作用。
5S是系统化改善工作系统和流程的方法,广泛应用于生产车间和办公区域,它是通过整理和清洁办公区域来达到提高效率和纪律的目的,是基于五个日语外来词汇的罗马文拼写单词,可以翻译成:整理、整顿、清扫、清洁、素养。
5S的精髓是管理标准化、制度化和员工修养,它使我们工作现场的作业标准化、制度化,防止意外事件(安全、质量、设备、物料等)的发生,提高现场管理水平,达到管理标准化、制度化。5S活动的目的不仅希望员工将东西摆好,设备擦干净,最主要的是通过本活动潜移默化地改变他们的思想理念,使他们养成良好的习惯,变成一个有高尚情操的优秀员工。
一、5S活动的主要内容
1、整理的含义。
(1)整理的含义。将必需物品与非必需品区分开,在岗位上只放置必需物品。清理“不要”的东西,可使员工不必每天反复整理、整顿、清扫不必要的东西,减少无价值的劳动时间,腾出空间,消除浪费。
(2)整理的步骤。所在的工作场所(范围)全面检查,包括看的到和看不到的;制定“需要”和“不需要”的判别基准;清除不需要物品;调查需要物品的使用频度,决定日常用量;制定废弃物处理方法;每日自我检查。
(3)整理就是清理废品,把必要物品和不必要的物品区分开来,不要的物品彻底丢弃,而不是简单的收拾后又整齐地放置废品。5S活动中的整理工作比较难,要克服一种舍不得丢弃而实际又用不成的吝惜观念。要有物品鉴别整理的能力,首先要有丢弃的眼光和智慧。
(4)需要和不要基准:制定“要”和“不要”的基准表,并召集相关部门开会讨论和决议基准表,同时反省不要物品产生的根源,见表16-1。
表16-1 “要”和“不要”的基准
类别 |
基准分类 |
要 |
①用的机器设备、电气装置;②工作台、材料架、板凳;③使用的工装飞模具、夹具等;④原材料、半成品、成品等;⑤擒板、周转箱、防尘用具;⑥办公用品、文具等;⑦使用中的看板、海报等; ⑧各种清沽工具、用品等; ⑨文件和资料、图纸、表单、记录、档案等;⑩作业指导书、作业标准书、检验用的样品等 |
不要 |
地板上 |
①杂物、灰尘、纸屑、油污等;②不再使用的工装、模具、夹具等:③不再使的办公用品; ④ 破烂的垃圾筒、周转箱、纸箱等; ⑤呆滞物料等 |
工作台 |
①过时的报表、资料;②损坏的工具、样品等;③多余的材料等;④私人用品 |
墙上 |
①蜘蛛网;②老旧元用的标准书;③老旧的海报、标语 |
空中 |
①不再使用的各种挂具;②无用的各种管线;③无效的标牌、指示牌等 |
2、整顿的含义
(1)整顿的含义。整顿就是消除无谓的寻找,缩短准备的时间随时保持立即可取所需要的物品的状态,减少“寻找”时间上的浪费。
“整顿”的消极意义为防止缺料、缺零件,其积极意义则为“控制库存”,防止资金积压,使工作场所井井有条、一目了然,消除寻找物品的时间。
(2)整顿的步骤。要落实前一步骤整理工作;布置流程,确定置放场所;规定置放方法;划线定位;标识场所物品(目视管理的重点)。
(3)整顿的三要素:
放置场所原则。物品的放置场所原则上要100%设定,物品的保管要定点、定容、定量,生产线附近只能放真正需要的物品。
放置方法原则。安全,易取放。
标识方法原则。放置场所和物品要一一对应,标识要统一。
(4)整顿的发展定置管理学科。目前,整顿发展为一门定置管理学科,定置管理是对生产现场中的人、物、场所三者之间的关系进行科学地分析研究,使之达到最佳结合状态的一门科学管理方法,其知识框架如图16-1所示。
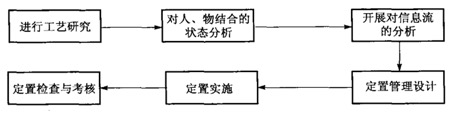
图16-1 定制管理科学的知识框架
(5)定置管理的要点是:三定原则、设置管理看板、画线标识、发现不合格处立即纠正。
其中,三定原则是定位置、定数量、定区域:定位置就是规定物品堆放、工具放置、通道、班组(个人)工作场地位置;定数量是对各区域堆放物品、设备、工具的数量加以限制;定区域是对产品堆放区可具体划分为合格品区、不合格品区、待检区等。
3、清扫的含义。
(1)清扫的含义。就是将岗位变得无垃圾、无灰尘,干净整洁,将设备保养得锃亮完好,创造一个一尘不染的环境。就是清除场所内的脏污,并防止污染的发生。
(2)清扫的目的。就是让员工保持良好的工作情绪,产品有稳定品质,设备达到零故障、零损耗。除了能消除污秽,确保员工的健康、安全卫生外,还能早期发现设备的异常、松动等,以达到全员预防保养的目的。
(3)清扫的步骤。建立清扫责任区;执行例行扫除,清除脏污;调查污染源,予以杜绝;建立清扫基准,作为规范。
4、清洁的含义。
清洁是将整理、整顿、清扫进行到底,并且标准化、制度化形成企业文化的一部分。
清洁的具体步骤:
①落实前览工作;
②把前览的工作标准化;
③制订目视管理、颜色管理基准;
④制订稽核方法;
⑤制订奖惩制度,加强执行;
⑥维持到意识;
⑦高级主管经常带头巡查,以示重视。
5、标准化、制度化含义。
标准化就是把安排变为规定,将前览实施的做法制度化、规范化,并贯彻执行及维持成果,通过制度化来维持成果,并显现“异常”之所在,它意味着建立相关的制度规定“整理”、“整顿”、“清扫”的方法、工具、活动评比的标准,以及相关活动的制度等队只有标准化,才能保证刚达到的水平不会回落得太快。
“标准”的其中一种定义,是指当前做事情的最佳方法。每一位员工遵照相同的标准、方法去工作,质量比较稳定,不会有变动和差异波动,使生产制造水平一直保持衡定。
6、素养的含义。
对于规定了的事情,大家都按要求去执行,并养成一种习惯。公司应向每一位员工灌输遵守规章制度、工作纪律的意识。此外,还要强调创造一个良好风气的工作场所的意义。绝大多数员工对以上要求会付诸行动的话,个别员工和新人就会抛弃坏的习惯,转而向好的方面发展。此过程有助于人们养成制定和遵守规章制度的习惯。
(1)素养的目的。是让员工成为遵守规章制度,有良好素质习惯的人才,并铸造团队精神。
(2)素养的步骤。维持推动前4S至习惯化;制订共同遵守的有关规则、规定;制订礼仪守则;教育和培训;推动各种精神提升活动。
(3)在“整理”、“整顿”、“清洁”工作标准化、制度化之后,还要确保并维护已达到的状态。为了维护、巩固和进一步提高前4S的成果,每个5S步骤的实施都要监控和审核,让员工养成良好的习惯,让日常的清洁和有序成为企业文化的一部分。
二、可视化管理
1、可视化管理的含义。
所谓可视化管理,就是通过视觉导致人的意识发生变化的一种管理方法;强调使用颜色,达到“一目了然”的目的是通过人的五感(视觉、触觉、听觉、嗅觉、味觉)能够感知现场的正常与异常状态的方法。如十字路口的交通信号灯、包装箱上的箭头、显示空调运转的布条、直通率推移图等。
可视化管理是5S活动中重要的管理技巧,能让企业的流程更加直观,使企业内部的信息实现可视化,并能得到更有效的传达,从而实现管理的透明化。可以说,可视化管理实施的如何,很大程度上反映了一个企业的现场管理水平。
2、可视化管理的目的。
可视化管理的目的,是明确告知应该做什么,做到早期发现异常情况,使检查有效;防止人为失误或遗漏,并始终维持正常状态;通过视觉,使问题点和浪费现象容易暴露,事先预防和消除各种隐患和浪费。
3、可视化管理的原则。
(1)视觉化。彻底标示、标识,进行色彩管理;
(2)透明化。将需要看到的、而被遮隐的地方显露出来,情报也如此;
(3)界限化。即标示管理界限,标示正常与异常的定量界限,使之一目了然。
4、可视化管理的三个水准。
(1)初级水准。有表示,能明白现在的状态;
(2)中级水准。谁都能判断正常与否;
(3)高级水准。管理方法(异常处置)都列明。
5、可视化管理的应用。
可视化管理在10大类方面的应用见表16-2,但这仅讲在设备电器和安全方面的简单应用。
表16-2 可视化管理的种类与实例
可视化管理种类 |
适用实例 |
颜色线条 |
基本颜色标准、常用线条规格、重点工序 |
空间地名 |
建筑编号、房间命名、区域名牌 |
地面通道 |
通行线、地面导向、门管理 |
设备电器 |
流体管道、物流方向、仪表阀门 |
物品材料 |
物品原位置、保管柜、定量标示 |
工具器具 |
各类工具、手套、绳索、搬运车辆 |
安全警示 |
消防设施、安全护栏、危险品 |
外围环境 |
车库、市政设施、道路路沿 |
办公部门 |
办公桌面物品、抽屉柜子、文件资料 |
管理看板 |
方针指标、公告栏、红牌 |
6、可视化管理的手法。
可视化管理最基本的手法是如下颜色和线条规格的使用:
(1)颜色在厂房和办公室方面的应用;
(2)颜色在运输管道和设备方面的应用;
(3)线条颜色在车间安全通道的应用。
7、可视化在设备管理方面的几点应用,如图16-2所示。
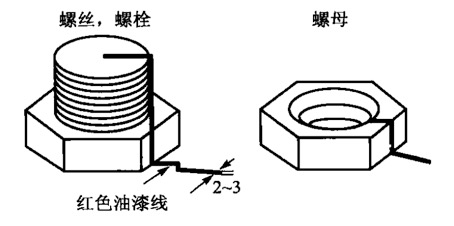
a)螺栓螺母松紧状态
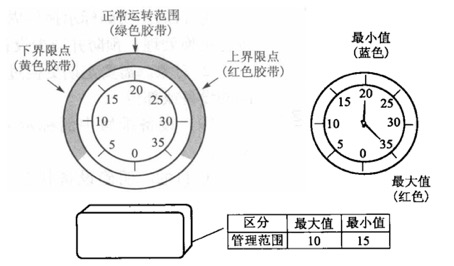
b)计量器界限
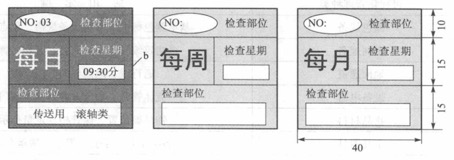
c)检查部位
图16-2 可视化在设备管理方面的几点应用
8、换件周期的标示方法,如图16-3所示。
(1)目的。明确标示换件周期,及时对消耗品进行更换处理,预防并减少设备的突发性故障。
(2)对象。需要定期更换过滤器、泵体等消耗品的设备或部位。
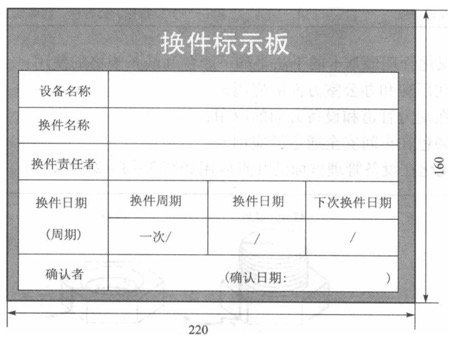
图16-3 换件周期标示方法
9、设备维修中的标示方法,如图16-4所示。
(1)目的。明确设备状态(运行/修理),预防发生安全事故。
(2)对象。所有设备的控制面板和其他需要注意安全的地方。
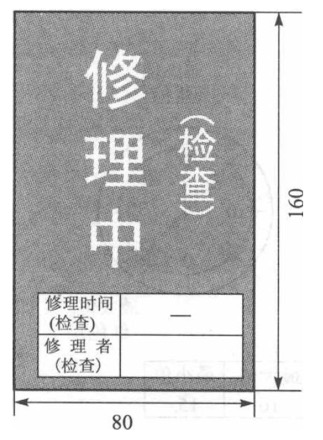
图16-4 设备维修中的标示方法
10、额定电压的标示方法,如图16-5所示。
(1)目的。为防止因110V、220V、380V等不同电源接错而造成设备的损坏。
(2)对象。所有容易混淆的电源插头和插座。
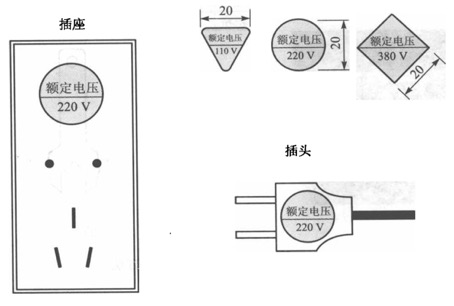
图16-5 额定电压的标示方法
11、开关控制范围标示方法,如图16-6所示。
(1)目的。预先把握开关控制的范围和电器。准确开关指定的电器,提倡节约意识。
(2)对象。所有电器开关和照明开关。
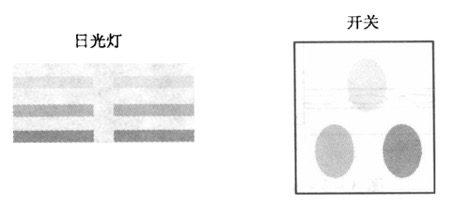
图16-6 开关控制范围的标示方法
12、一般工具的标示方法(工具陈列柜),如图16-7所示。
(1)目的。明确工具的放置位置,确保工具的安全保管数量,方便工具的取用及缩短查找时间,介高工作效率。
(2)对象。各种工具、器材类。
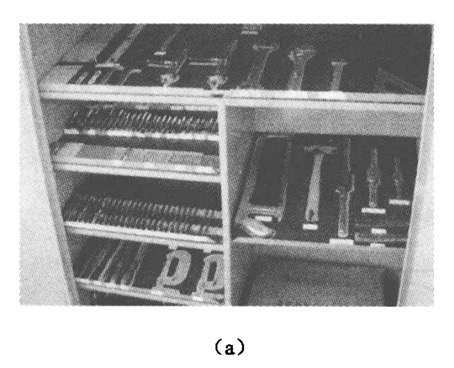
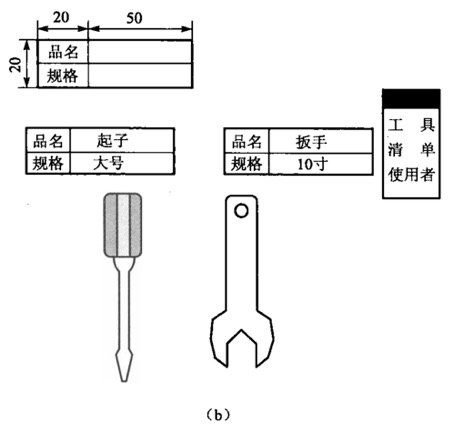
图16-7 一般工具的标示方法
(a)实物;(b)图例
13、撬棍类工具的标示方法(工具架)如图16-8所示。
(1)目的。明确专用工具的放置位置。确保工具的安全保管数量。方便工具的取用及缩短寻找时间,提高工作效率。
(2)对象。各种适合竖立摆放的工具、器具、非标准专用工具类。
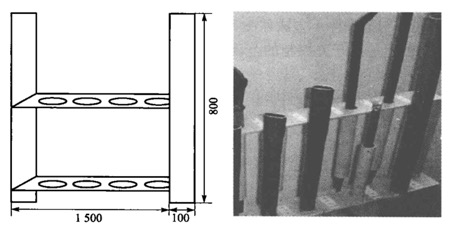
图16-8 撬棍类工具的标示方法
三、可视化在安全管理方面的几点应用
1、消防设施位置的标示方法,如图16-9所示。
(1)目的。明确标示消防设施的位置,消防设施固定化,减少不必要的移动,减少在发生火灾或紧急情况时因寻找而造成时间的浪费。
(2)对象。所有消火栓、灭火器和其他消防设施。
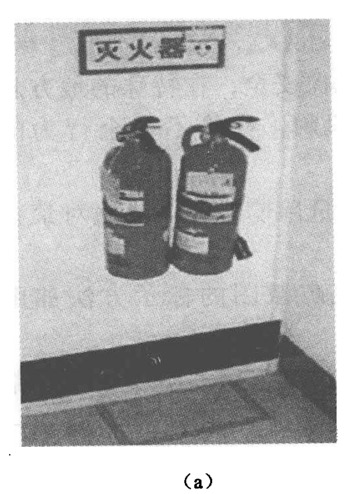
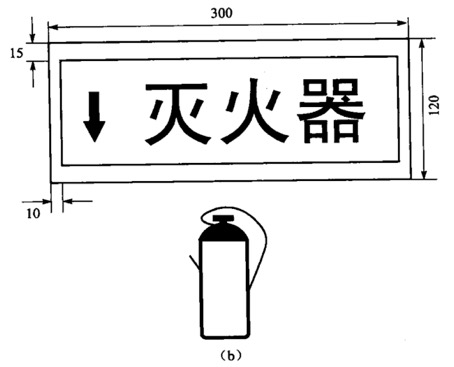
图16-9 消防设施的标示方法
(a)实物;(b)图例
2、保护性指令的标示方法,如图16-10所示。
(1)目的。在不许穿着或设备保护用品的地方悬挂相应的指令标识牌,目的是提示使用保护性用具,防止发生工业意外,确保安全。
(2)对象。化学用品、有毒物品的保管及使用场所、有放射性或飞散物质的场所、有高空坠落的场所、有潜在危险的场所。
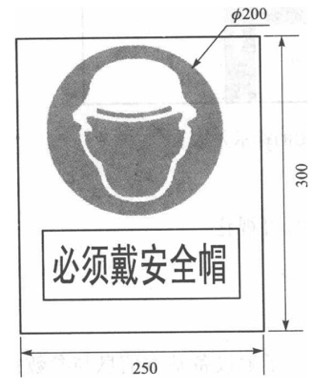
图16-10 保护性指令的标示方法
3、警示性指令的标示方法,如图16-11所示。
(1)目的。在存在安全隐患的地方悬挂相应的警示性标识牌,预告危险发生的可能,确保安全。
(2)对象。有放射性或尺散物质的场所,有高空坠落的场所,有机械伤害危险的部位;有潜在危险的场所。
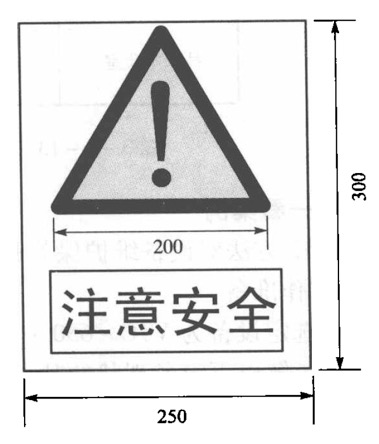
图16-11 警示性指令的标示方法
4、禁令性指令的标示方法,如图16-12所示。
(1)目的。为确保安全,在特殊的地方悬挂相应禁止的标识牌,杜绝不安全行为的发生。
(2)对象。存在危险隐患,需要绝对禁止某种行为的地方。
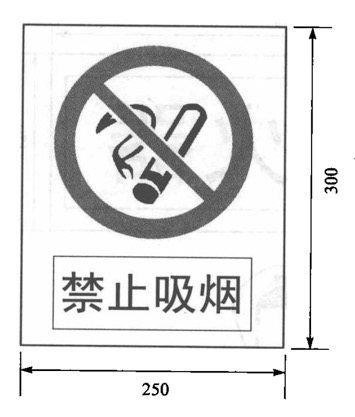
图16-12 禁令性指令的标示方法
5、消防紧急疏散图的标示方法,如图16-13所示。
(1)目的。提醒员工铭记消防安全逃生路线,预先了解各通道和出入门的位置,防止一旦发生火灾或紧急情况时发生慌乱而导致不必要的损失。
(2)对象。一般通道、主要出入门侧面。
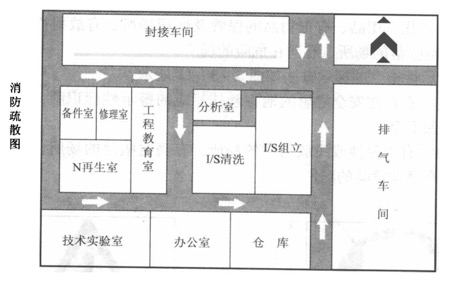
图16-13 消防紧急疏散图的标示方法
返回目录