《设备管理与维修》
主讲/辛巧娟
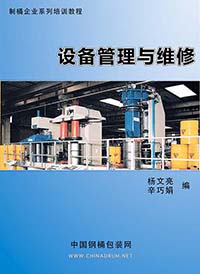
第十三讲:运用分析方法处理故障
现代化的企业,必须配备现代化的设备。要使先进的技术装备充分发挥效能,就必须提高设备管理人员的管理理念、管理思想和管理水平,充分运用现代管理方法和手段,实施科学化的设备管理。
本讲的学习目标是:
(1)了解现代设备管理常用的管理方法。
(2)会运用管理分析法对收集到的资料进行简单分析。
(3)会综合运用管理分析法。
一、点检数据的收集
点检业务是一项检查工作,也是一项管理工作,不但要按点检标准作业书进行规范作业,查找设备的异常和隐患,发现问题及时采取措施,使设备保持最佳运行状态还要正确收集设备在点检中的各类数据,整理实绩,分析点检的结果,从而为做好设备预防维护管理打好基础。
点检实绩记录有固定的格式,包括作业记录、异常记录、故障记录和倾向记录等。完整的记录为制定设备预防维修计划等设备管理工作提供了有价值的原始数据。因此,认真填写各种数据表格,以确保设备数据的准确性。
具体内容如下:
(1)点检结果的记录。
(2)点检日志。
(3)缺陷和异常的记录。
(4)故障和事故的记录。
(5)设备倾向管理的记录。
(6)设备检查和修理记录。
(7)设备的状态记录。
(8)失效记录。
二、点检的分析方法
通过点检工作获得设备运行的原始数据,运用现代信息技术和管理手段,开发各种设备管理的系统软件,可对设备运行的数据进行统计、分析、处理,产生各种设备管理报表表格、数据信息等,为分析、处理设备故障,制定点检计划、设备劣化倾向管理、制定预知维修计划等提供可靠、准确、科学的研究数据信息。
但对于设备点检员和管理员来说,还需要掌握设备管理常用的基本分析方法,如鱼骨分析法、问5个为什么法、5W1H分析法、图表分析表、FMEA及故障树、FTA分析法;排列图法、关联图法、系统图法、直方图法、焦点法等。
1、鱼骨分析法。
就是将所有能导致故障的原因,按主要类别(人、机、料、法、环)列出,这个方法适用于分析复合因素的故障原因。方框里是大类,箭头上是小类,尽量将所有能导致故障的原因罗列出来,如图13-1所示。
例如,运用鱼骨分析法对某公司生产效率低进行的分析,如图13-2所示。
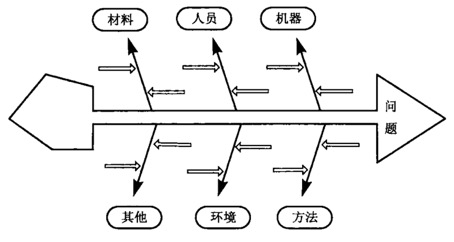
图13-1 鱼骨分析法
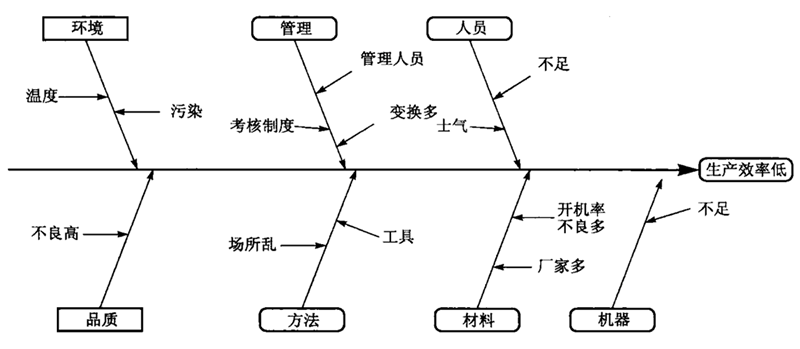
图13-2 某公司生产效率低鱼骨分析图
2、问5个为什么法。
就是连续不断地问“为什么”,将问题追根刨底,直到有答案,这方法适用于因果关系的问题。在分析隐患和故障原因的过程中,通过不断地自问,就能深入地追查到问题的根源。
例如,一位点检员接到指令,匆忙地奔赴生产现场,车间较黑暗,他眼睛不适应,地上的油污使他摔了跤。为什么会摔跤?地上有油,为什么有油?漏油,为什么会漏油?油嘴松,为什么油嘴松?密封圈坏。密封圈坏,为什么会坏?
3、5W1H分析法。
是取6个英文单词why(为何)、what(何事)、where(何地)、when(何时)、who(何人)、How(如何)的第一个字母后的合称,是一种有助于人们将工作内容与当事人联系在一起,并对工作的程序进行思考、研究、分析而进一步落实责任制的好方法。
表13-1 5W1H分析法
原文 |
中文含义 |
主要涉及的对象 |
理解为 |
相当于 |
用于思考 |
用于改造 |
Who |
何人 |
责任人、牵头人、负责人、担当者、作业的操作人员 |
给谁、使谁、和谁 |
定人员 |
为什么要他干? |
能否换别人干? |
Why |
为何 |
理由、原因、动机、出发点 |
为何做、为何改 |
定理由 |
有没有必要干? |
理由充分吗? |
What |
何事 |
内容、标的、项目、目的、目标 |
是什么、使什么、做什么 |
定标准 |
为什么要干? |
能否不干? |
Where |
何地 |
场所、施工点方向 |
在哪里?到哪里?把哪里 |
定地点 |
为什么此时干? |
改个地点干行吗? |
When |
何时 |
时间、日期、期限 |
从何时、到何时、处何时 |
定时间 |
为什么此时干? |
换个日期干行吗? |
How |
如何 |
手段、工序、方法 |
如何做、怎样做 |
定方法 |
为什么这样干? |
有更好的办法吗? |
4、图表分析法。
优点在于能进行优先排序,优先排序可以将问题主要矛盾显现,删除不重要的问题,以利迅速分析查找问题的主要原因。
现运用图表分析法对“手电筒为什么不亮”进行分析、判断,如图13-3所示。
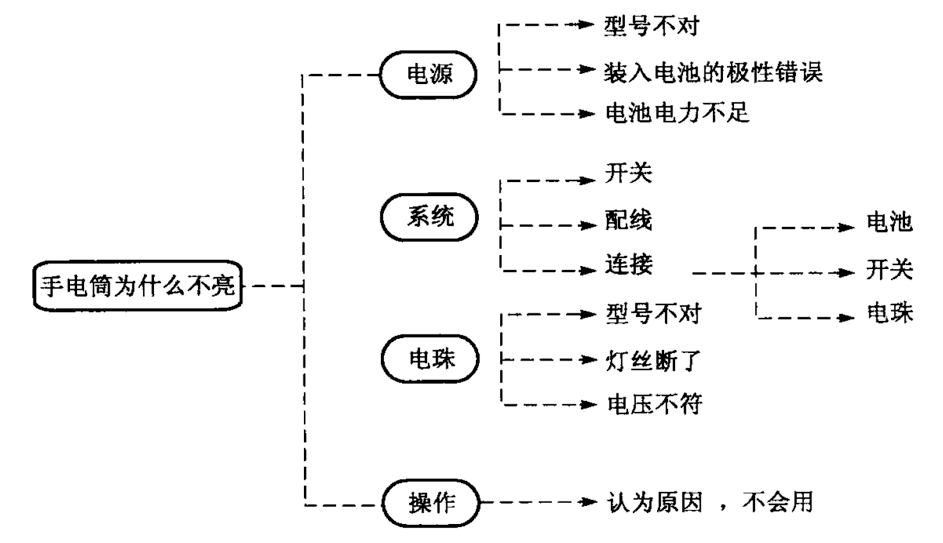
图13-3 “手电筒为什么不亮”图表分析法
现以某厂设备故障统计表的数据为例,运用图表分析法对处理设备故障进行优先排序,图13-4中的X轴代表故障的可能性。图13-4中的Y轴代表点检作业的难易程度,通过二维坐标的排列,可以按照工作的轻重缓急来安排点检工作。
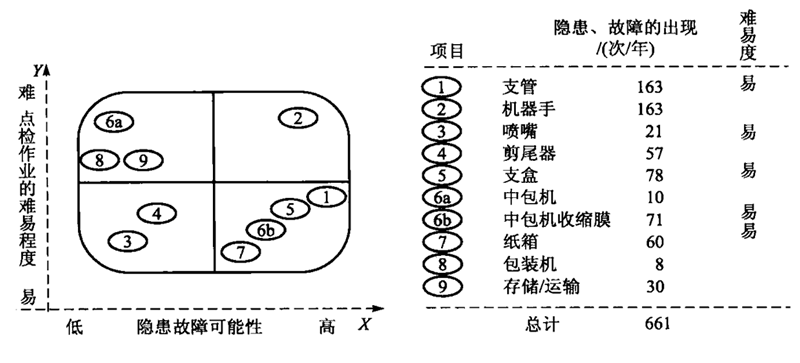
图13-4 优先排序的图表分析法的运用
5、FMEA及故障树。
这种方法又成为故障模式与影响分析或失效模式与后果分析方法。如某年美国航天飞机升空时发生爆炸,造成机毁人亡,灾害性的根本原因不是航天飞机都坏了,仅仅是一个零件的失效引起了严重的后果。类似这样的情况在企业生产现场也有很多。FMEA是一种单因素分析法,通过对其可能性和严重性的分析、评估,以确认风险并采取措施避免它。FMEA分析方法见表13-2所示。
表13-2 FMEA分析方法
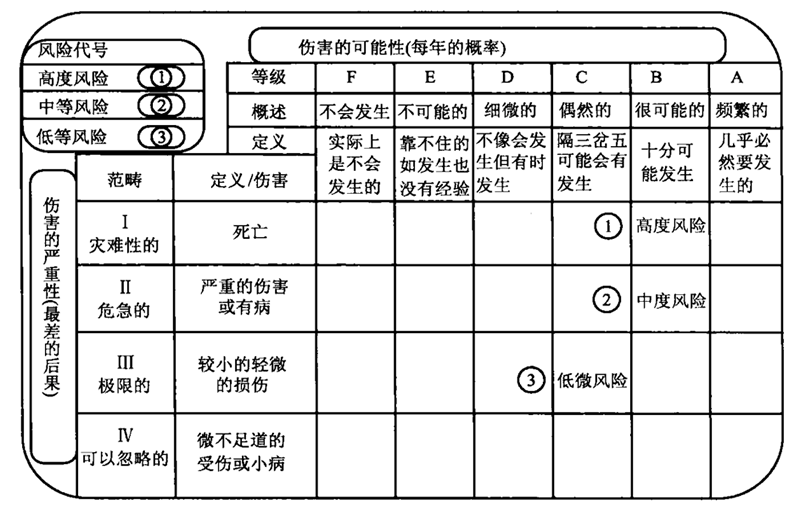
6、FTA分析法。
是将系统故障或灾害的发生要因分解成树的形状,从上往下分解到部分要素,以逻辑图形式进行解析的一种方法。可用于分析多种故障因素的组合对系统的影响,是在FMEA基础上的一种逻辑关系图。在工程中这是一种比较有效的逻辑分析方法。
例如,当零件1和2同时失效时,造成部件1故障,零件3和4之一失效即使部件2故障。设备故障是由于部件1和2一起失效的结果,如图13-5所示。
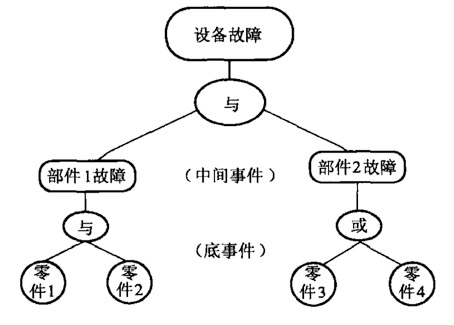
图13-5 运用FTA分析法分析设备故障的原因
7、排列图法。
排列图法是寻找主要问题的方法。寻找主要矛盾,找出主要问题,排列图法较为有用。如用排列图找出故障的主要原因以便采取对策。同样,也可以作出故障停机时间排列图或故障处理排列图,找出故障停机时间的主要问题和处理故障对策的主要问题。
8、关联图法。
将问题和影响该问题的要因之间的关联用带箭头的线连接起来,形成一个理论性的关联图,用该图解析一些很模糊的大问题或者要因错综复杂的问题时适合用这种手法。
9、系统图法。
为了达到某一目的,将其方法细分解成树形图,针对某个课题,通过该树形图得出具体的对策时使用系统图法。
10、直方图法。
将预先设定的计划目标的计划值按比例记入到图表里,构成直立的方块图;同时在相应处,记入相同比例的实绩值。这样,计划值与实绩值相对比,可以看出计划与实绩的差距,以证实计划精度的高低,同时也可与历史实绩进行对比,看其计划性如何。它基本可以说明工作效率如何,效率在提高还是下降找出存在的问题点进行分析评价。
11、焦点法。
是找出问题点、便于分析的好方法,简单明了、问题突出、分析效果显著。一般也可以用于设备故障分析之中。把一个整圆等分,分割成数块(6块或8块),每一块都表示了点检区设备的有标准化问题点的一部分,每一部分引起的故障次数均用有量度线段表示,这样把有量度线段的顶点连成多边形,即形成了具有评价的分析图。
在设备管理过程中,通常会采用一种或多种管理方法进行分析,找出、制定解决问题的原因和方法。解决问题的各种管理方法运用对应见表13-3所示。
表13-3 解决问题新旧管理手段运用对应表
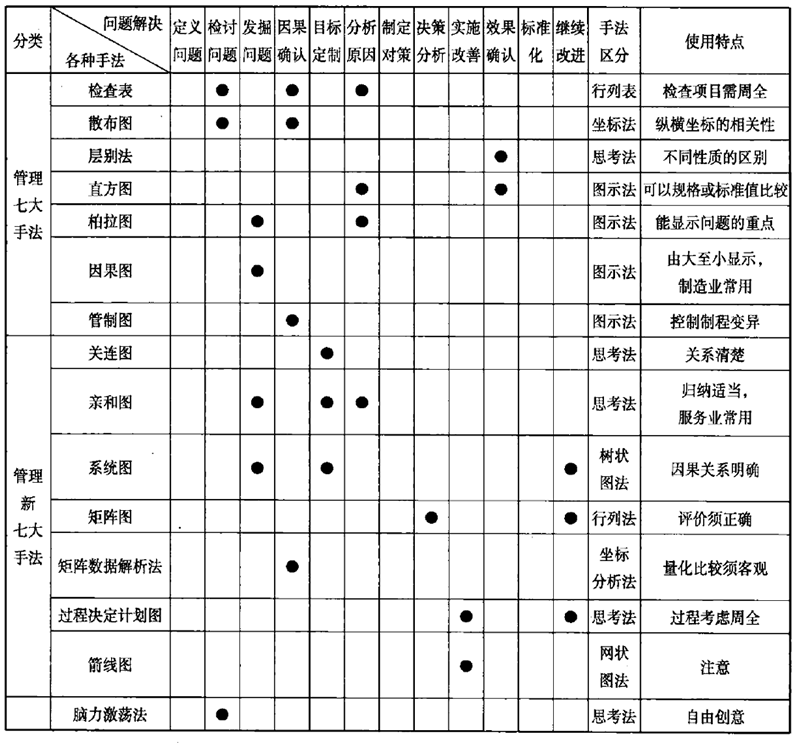
三、综合运用管理方法,实施科学管理
当设备出现了故障,首先要做的就是针对故障实施修理或者复原,使设备运转起来,其次要做的就是查找问题发生的根本原因,采取有效和针对性强的预防措施,杜绝问题的再次发生,确保设备的正常运转,提高设备的综合效率.
下面是介绍几种管理方法:
1、PM分析(代表性的2P5M5W方法)。
该手法在解决要因错综复杂的慢性问题时发挥威力,它的特点是用物理的角度去解析现象,结合设备的原理、人、机、料、法、环等多方面因素,从变化因素与设备现象之间的关系层层追问什么,直至找到根本的原因。
(1)2P
Phenomenon (现象):最直观的客观存在,现象的明确化,如生产线停了、设备坏了,加工的零件尺寸超差等。
Physical (物理):现象的物理分析,把握问题的真正意味,遵循现场、现物、现实的原则,用物理的原理对故障现象进行分析,避免简单的想当然。
(2)5M
Mechanism (机理):从机理或原理出发,找出与故障现象存在相关的所有条件。
Man (人):研究问题的产生和人员的变化导致操作变化、差异之间的联系。
Machine (机器设备):研究故障、问题的产生是否与设备的变化(如老化、变形、性能失真)有关。
Material (材料、零件、部件):了解材料性能的变化。
Method (工作方法):研究问题的产生和工作方法之间的因果关系,是否存在没有按正确的方法作业。
(3)5W
Why (为什么):连续追问5次问什么,层层深究。
(4)找出发生问题的真正原因:试验法、排除法、替代法等。
(5)改善(解决)方案的提出:根据不同的原因提出具体可行的改善方案。
(6)改善(解决)方案的实施。
2、PDCA循环管理法如图13-6所示。
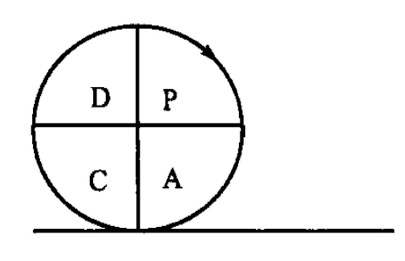
图13-6 PDCA循环管理法
P (Plan):策划、计划。为达到确定的目标,而编排的设想和步骤。
D(Do):做、执行、实施。按照计划而定的具体实施事项。
C (Check):检查、确认。对实施的结果,是否按照计划执行,进行检查飞评价。
A (Action):对策。当执行的结果与计划有差距时,再次确定行动的方法。
运用PDCA循环解决问题的步骤:
图13-7为运用PDCA管理循环解决问题的8个步骤,即称小组四段八步法。
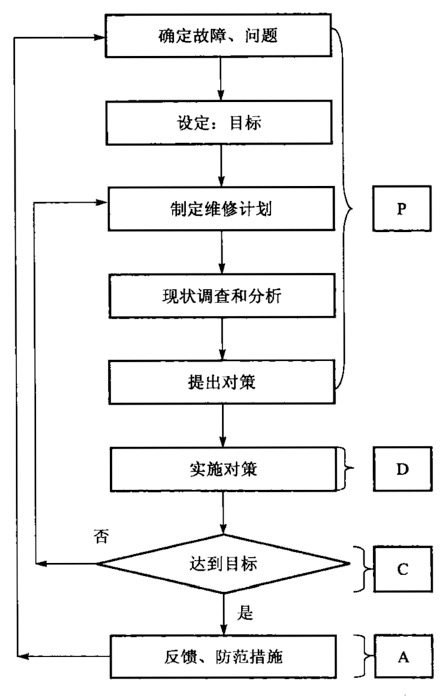
图13-7 解决问题的PDCA
第一步,对象:确定故障、问题。
从问题中选择希望解决以及那些迫切需要解决的问题、故障,准确描述要解决问题、故障的现象。
第二步,目标:设定目标。
目标的设定要求现实、可行和具有挑战性,并且是可以衡量的。
第三步,计划:制定维修计划。
制定维修计划,确定负责人和有关成员,实施时间。
第四步,分析:现状调查和分析查找、选择与问题、故障相关的记录、特性指标等,分析并识别影响特性值变化的因素和主要因素、原因。
第五步,对策:提出对策和确定对策。
针对主要因素和主要原因,提出具体多种的改善方案或者对策,并确定选择的对策或者方案。
第六步,实施:实施对策或方案。
第七步,效果确认:是否达到预定的目标?
对实施对策或方案取得效果进行检查确认,是否达到预定目标。如果没有达到目标,需要重新制定维修计划,采取对策。
第八步,反馈、防范措施。
制定必要的防范措施,重新制定或修改点检、巡检的标准及相关的设备文件。
横向展开类似设备、故障的防范和整改。
设备管理运用PDCA管理实施步骤与其他管理方法的综合运用关系见表13-4。
表13-4 PDCA管理实施步骤与管理方法关系
阶段 |
步骤 |
主要管理方法 |
P |
分析现状,找出问题 |
排列图、直方图、控制图 |
分析影响因素,找主要原因 |
因果图、排列图、关联图 |
寻找解决方案,优化方案 |
头脑风暴、水平对比、试算平衡 |
制定详细计划 |
流程图、5E1H |
D |
执行落实计划 |
检查表、反馈制、雷达图 |
C |
检查计划执行效果 |
排列图、直方图、控制图、散布图 |
A |
总结经验,制订标准 |
规章制度化 |
提出新问题,进入下个PDCA |
|
返回目录