制桶工艺学
第四章 桶身整形
第一节 桶身整形设备和工艺
三、涨筋机
涨筋机的功用是在桶体壁上挤压出两条环形加强筋。涨筋机是制桶生产设备线中的一个重要组成环节。涨筋工序完成质量的好坏,影响钢桶的成品率,关系着钢桶的最终强度和刚度能否符合使用需要,能否在运输过程中“胜任”,因而除去桶身板材质地优劣的因素,涨筋机的结构与工作性能,对提高钢桶的成品质量、生产效率和水平均起重要作用。
涨筋机属于制桶整形工艺的特殊的专业机械。其主要工作原理是利用斜面机构使刚性分块凸模(即涨块)径向伸出,在桶壁内表面向外挤出突起的环形筋,也就是使桶身壁产生径向增大的凸肚变形。在挤压成形时,桶身固定套在环状刚性分块凸模上,静态挤压。涨筋机的传动特点是采用曲轴连杆机构(其上固连推动斜面机构的主轴),将动力源传送的匀速旋转运动转换成匀速直线往复运动。
1. 涨筋机的运动
涨筋机的运动亦分为成形运动和辅助运动。以下运动框图示意说明其运动关系构成(见图4-13):
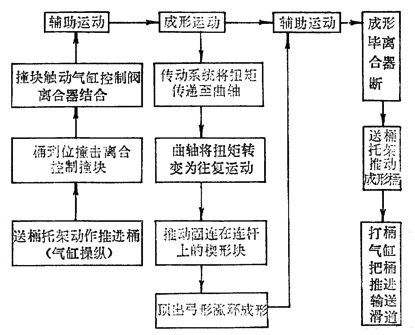
图4-13 涨筋机运动系统框图
2. 涨筋机构的传动系统
如图4-14所示,传动系统示意图展示了传动关系及有关构成件和动力传送过程。
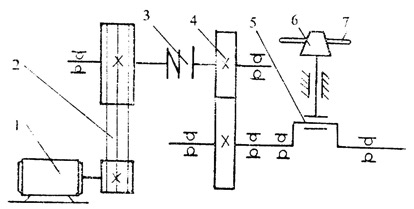
图4-14 涨筋机传动系统图
1-电机;2-带传动;3-离合器;4-齿轮传动;5-曲轴传动;6-楔形块;7-刚性分块凸模
该机传动系统的构造原则是基于下列设想:为使执行机构简单紧凑,尽量减少机构的构件数和运动副数,缩小所占空间位置和机器的几何尺寸,执行构件尽可能地靠近原动件,为简化传动系统,便于调试与维修和减少传动件磨损对传动精度的影响,原动件尽可能地集中布置在少数轴上。
涨筋机的动力系统由电机、回转传动系、曲轴等组件构成。电机作为原动件输出回转扭矩,然后经皮带传动至齿轮传动再至曲轴连杆传动、径曲轴连杆传动输出的运动形式已由匀速旋转运动变为往复直线运动,再经涨筋机主轴将动力递送至楔形块,使轴向移动改变方向而成径向伸缩运动,在楔形块斜面上滑动的刚性分块凸模组件便随之径向移动完成涨筋成形。在涨筋机的动力传递过程中运动经过了两次转变:一次是由曲轴传动致使的运动形式的改变——回转运动→直线运动,另一次是由楔形块致使的运动方向的改变轴向运动→径向运动。
3. 涨筋机的构造
(1)传动件。传动件的组成是带轮、离合器、齿轮和曲轴连杆等构件。
曲轴连杆是涨筋机传动系统中的重要组件也是最后一段。它承担着转换运动形式并传递运动的作用。曲轴连杆机构使电机经回转传动系传递的匀速旋转运动变为单停留往复直线运动,使电机输出的扭矩转换为推力而推动涨筋机头主轴轴向往复移动。其运动规律与曲柄滑块机构类似。在其行程的终止端停留——涨筋。
涨筋机主轴移动速度的计算如下:
图4-15中的导杆就是涨筋机主轴;R-曲轴回转半径;ω-曲轴回转角速度;s-主轴往复移动行程;s=2R。
因而主轴的位移:X=R(1-cos?)=R(1-cosωt)
主轴位移速度;V=Rωsinωt
式中:ω=πn/30;n——曲轴转速:
n=n电×i皮×i齿
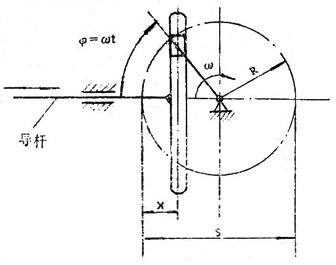
图4-15 涨筋机主轴速度计算结构图
(2)工作部件。工作部件的构成是楔形块、涨筋机头盘、刚性分块凸模及其安装基座、弹簧等主要构件。楔形块作为运动末端的执行构件起着改变运动方向并传递动力的作用。楔形块相当于斜面机构,它与主轴固连,另一面刚性分块凸模组件又可在其斜面上滑动,使主轴所作的轴向往复移动经楔形块使刚性分块凸模作径向伸缩,从而达到涨筋的目的。
涨筋所需力的基本数值可按以下方法确定。为简化计算,我们建立一个计算模式。如图4-16所示,将模形块与涨筋机主轴视为一个构件;将刚性分块凸模与安装基座及机头盘视为一个构件,涨筋后的桶径(指凸起最大处)为D;涨筋宽度为H(指两根环筋的宽度和);刚性分块凸模个数为N;力用P表示,则作用于每一刚性分块凸模上的力是P/N,锥形轴(其锥角为β)对于凸模的反作用力是Q;桶身对于每一模块的箍紧力是PH(D/2)α(P为桶身与模块间的单位压力,α为每凸模块的弧度,H(D/2)α为桶身与模块的接触面积);摩擦力μ(P/N)与μQ。
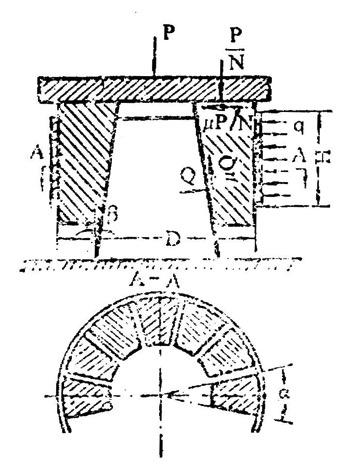
图4-16 涨筋力计算模式简图
根据一个凸模块的力平衡条件,可以列出下列平衡方程式:
在垂直方向:-P/N+Qsinβ+μQcosβ=0
在水平方向:-μP/N+Qcosβ-μQsinβ-pH(D/2)a=0
联立求解以上二式得:

σ而p=2t0σ0/D,N=2π/a(t0为板厚)代入上式,,整理得:
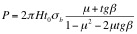
μ的数值一般为0.15~0.20;锥角β一般为8°、10°、12°和15°,σb是材料的强度极限,若采用08F钢板,则σb不小于330MN/m2,t0一般为1.0mm、1.2mm1.5mm。
工作部件的相互关系与位置可看工作部件装配图,如图4-17所示。
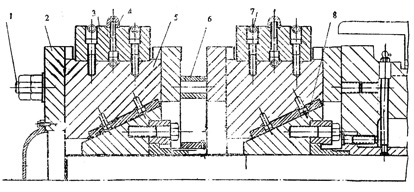
图4-17 工作部件装配图
1-调整螺栓;2-滑轨;3-涨块基座;4-弓形涨环;5-滑块;6-隔套柱;7-弹簧;8-楔形块
工作部件中主轴选用45#钢制造,采用调质处理,使其能过到优良的综合机械性能。棱形块因其具有滑动导轨的作用,故材料选用高碳钢,滑动斜面的硬度要求HRC60~62,需淬硬磨光。刚性分块凸模是执行机构的直接整形件。因而要求具有高硬度与高强度的性能,故其材料选用9硅铬工具钢,硬度达HRC62。刚性分块凸模数块(数目可视具体要求定,现在一般采用8块凸模)安装在机头盘的凹环形圆周槽内。
(3)工作部件的轴承选择
工作部件中主要的运行件是主轴,它的运行速度不高,且涨筋机头的径向安装尺寸受限制,因而采用静压滑动轴承较为适宜。材料选用锡青铜轴瓦。
(4)支承件
涨筋机的支承件主要是承重和支撑作用,没有移动或滑动支承件。涨筋机为卧式床身,铸铁制造,采用回火热处理工艺。但涨筋机的主轴伸出端执行构件组合是悬臂结构,因而对它起固定支承作用的涨筋机床头箱的刚度与强度性能必须确保,不然则会影响涨筋工艺的完成质量。
四、输送机构
输送机构是整个成形工艺设备的“咽喉”,它承担着各工序间的“供送”责职。对输送机构的设计要求是:它在工作过程中,能适当控制桶的推列、间距以及稳定可靠的输送速度等。目前输送形式仍较多采用由前段链输送与三机的卸料输送机构配合使用的供送系统。从焊机至三机(指整形设备的总称)间有一段直线距离需配置输送带。一般采用传送链运送。传送链的配置有以下几个方面要注意:
(1)为使链条联接方便和链节磨损均匀,大都采用偶数链节的链条与奇数齿的链轮相配合。
(2)为减轻链传动特别是在高速运动状态下所产生的冲击和振动,要选择链节距尽可能小的链条和齿数尽可能多的链轮。
(3)为保证从动链轮转速稳定,尽量使主从动链轮的密数相等,而且紧边长度应等于链节距的整倍数。
(4)为保持适宜的链条张紧程度且又容易拆装起见,要配备相应的调节措施。三机间因其一般没有直线段输送距离,不需配置输送带,只是在三台设备间设置分别由三个气缸直接推动的摇臂与滑道。有些厂也仍用连杆摇臂卸料输送机构来承担三机间的供送桶,但这较前者结构要复杂些,且连杆机构易于“卡死” 。不如前者准确简单。
供送顺序是与整形工艺流程相对应的。前段焊接好桶身直缝的筒形毛坯经扳边→波纹→涨筋。具体过程是:钢桶桶身经输送链送入扳边机后,下扳边滚轮托住桶身端边,而离合器接合带传动机构,由此凸轮机构动作,使上扳边滚轮下压,扳出桶端凸缘,完成后上扳边滚轮随凸轮动作而上抬,出料机构动作,将扳好边的桶身送出,进入波纹机。波纹工序的动作顺次与扳边基本相同。完成波纹成形后,桶身被送入涨筋机,由涨筋机上的长气缸将托盘上的桶身送入涨筋机头内;桶身撞击行程开关,使控制离合器操纵杆的气缸动作,驱动离合器,经传动系统将扭矩递送至曲轴,曲轴推动涨紧杆,完成桶身两道环形凸筋成形。至此桶身整形工艺结束。