《制桶工培训教程》
杨文亮 辛巧娟 编著
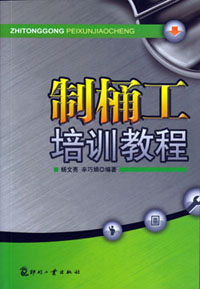
第九章 制桶辅助设备的操作维护
第二节 制桶设备液压传动系统
目前大多数制桶设备都采用液压传动,所以液压传动已经成为制桶设备不可缺少的辅助装备。
一、制桶设备液压传动系统的工作原理
常见的制桶设备,有很多的机构动作都采用液压传动,其中使用最广泛的就是两边机座的移动,如挤压翻边机两侧机座的挤压动作、卷边封口机两侧机头的夹紧动作。图9-2就是制桶设备典型的机座移动液压系统工作原理图。
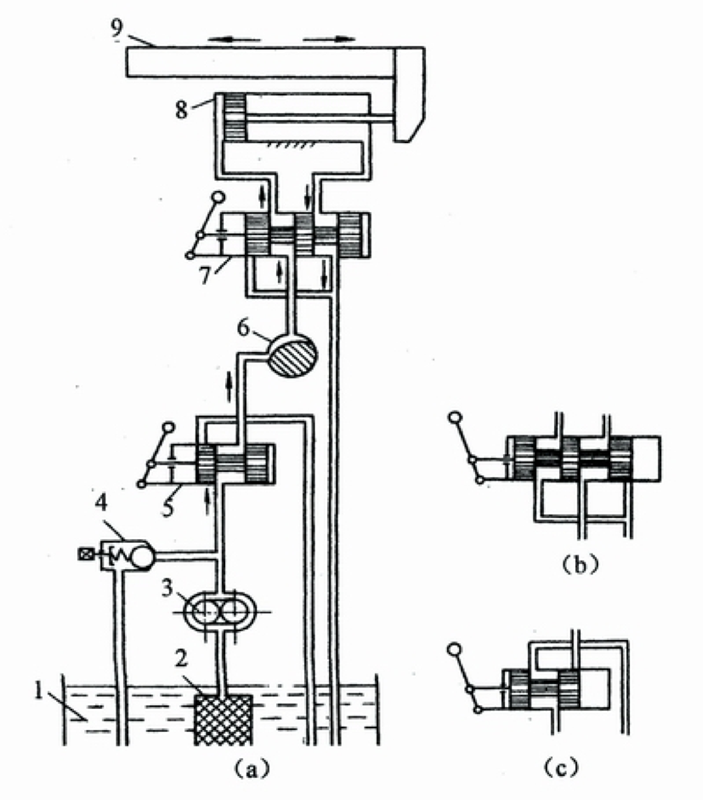
图9-2 制桶设备液压系统工作原理图
1-油箱;2-过滤器;3-液压泵;4-溢流阀 5、7-换向阀;6-节流阀;8-液压缸;9-移动机座
制桶设备液压系统主要由油箱、过滤器、液压泵、溢流阀、换向阀、节流阀、液压缸以及连接这些元件的油管、管接头等组成。该系统的工作原理是:液压泵由电动机带动旋转后,从油箱中吸油,油液经过滤器2进入液压泵的吸油腔,当它从液压泵中输出进入压力油路后,右图9-2a所示状态下,通过换向阀5、节流阀6,经换向阀7进入液压缸左腔,此时液压缸右腔的油液经换向阀7和回油管排回油箱,液压缸中的活塞推动机座9向右移动。
如果换向阀7的手柄移动成图9-2b所示的状态,则经节流阀的压力油路将由换向阀7进入液压缸的右腔,此时液压缸左腔的油经换向阀7和回油管排回油箱,液压缸中的活塞将推动机头向左移动。因而,换向阀7的主要功用就是控制液压缸及机座的运动方向。系统中换向阀5若处于如图9-2c所示的位置,则液压泵输出的压力油将经换向阀5直接回油箱,系统处于卸荷状态,液压油不能进入液压缸,所以换向阀5又称为开停阀。
机座的移动速度是通过节流阀6来调节的,当节流阀的开口大时,进入液压缸的油液流就大,机座移动速度就快;反之,机座移动速度将减小。因此,节流阀6的主要功用是控制进入液压缸的流量,从而控制液压缸活塞的移动速度。
液压缸推动机座移动时必须有一定的油液压力,在图9-2所示系统中液压泵出口处的油液压力是由溢流阀4决定的,所以溢流阀在液压系统中的主要功用是控制系统的工作。
通过上述介绍可以看出,液压传动的基本特征是:以液体为工作介质,依靠处于密封工作容积内的液体压力能来传递能量;压力的高低取决于负载;负载速度的大小取决于进入液压缸的流量;压力和流量是液压传动中最基本、最重要的两个参数。
液压传动是利用流体的压力能来传递动力的一种传动形式,液压传动的过程是将机械能进行转换和传递的过程。
二、液压系统的使用与维护
液压系统发生的故障有90%是由于使用管理不善所致,因此在生产中合理使用和正确维护液压设备,可以防止元件与系统遭受不应有的损坏,从而减少故障的发生,并能有效地延长使用寿命;进行主动保养和预防性维护,做到有计划地检修,可以使液压设备经常处于良好的技术状态,发挥其应有的效能。
1、液压系统的使用要求
按设计规定和工作要求,合理调节系统的工作压力和工作速度。压力阀和流量阀调节到所要求的数值后,应将调节机构锁紧,防止松动。不得随意调节,严防调节失误造成事故。不准使用有缺陷的压力表,不允许在无压力表的情况下调压或工作。系统运行过程中,要注意油质的变化状况,要定期进行取样化验,当油液的物理化学性能指标超出使用范围,不符合使用要求时,要进行净化处理或更换新油液。新更换的油液必须经过过滤后才能注入油箱。为保证油液的清洁度,过滤器的滤芯应定期更换。随时注意油液的温度,正常工作时,油液温度不应超过60℃,一般控制在35~55℃之间,冬季由于温度低,油液黏度较大,应升温后再启动。当系统某部位出现异常现象时,要及时分析原因进行处理,不要免强运行,造成事故。不准任意调整电控系统的互锁装置,不准任意移动行程开关和限位挡铁的位置。液压设备若长期不用,应将各调节手轮全部放松,防止弹簧产生永久变形而影响元件的性能。
2、液压设备的维护和保养
液压设备的维护保养分日常维护、定期检查、综合检查三个阶段进行。日常维护通常用目视、耳听及手触感觉等较简单的方法。在泵启动前、后和停止运转前,检查油量、油温、威力、漏油、噪声及振动等情况,并随之进行维护和保养,对重要的设备应填写“日常维护卡”。定期检查包括调查日常维护中发现异常现象的原因并进行排除。对需要维修的部位,必要时进行分解检修。一般与过滤器的检修期相同,通常为2~3个月。通过日常维护、定期检查可以把液压系统中存在的问题排除在萌芽状态,还可以为设备维护提供第一手资料,从中确定修理项目、编制检修计划,并可以找出液压系统出现故障的规律,以及液压油、密封件和液压元件的更换周期。综合检查主要内容是检查液压装置的各元件和部件,判断其性能和寿命,并对产生故障的部位进行检修,对经常发生故障的部位提出改进意见,大约一年一次。
三、液压系统常见故障的分析和排除方法
1、液压系统发生故障的规律
建立严格的维护保养制度虽然可以减少故障的发生,但不能完全杜绝故障。液压设备发生出现故障的概率随使用时间而变化,大致可分为三个阶段,即初期故障阶正常工作阶段和寿命故障阶段。初期故障阶段故障频率高,但持续时间不长。此阶段发生故障的主要原因,一是新系统设计可能存在一定问题,这时要按对系统的性能要求进行改进设计;二是系统安装工艺不合理及系统调试不当。对于此类故障,一般由泵站到执行元件依次进行诊断。保证安装精度并进行合理调试后,故障会逐渐减少,从而转入正常工作阶段。在正常工作阶段中,系统故障只有偶然发生。对于此类故障,可根据发生故障的现象录找造成故障的元件,给予修复或更换,不一定非得从液压泵开始依次查找。由于液压元件的磨损和疲劳等原因,使系统进入一个新的故障阶段,即寿命故障阶段。原本在安全使用期处于隐发状态的故障此时就显露出来,以致系统的效率和精度都将随时间的推移而下降。这就要对液压元件和系统进行全面检查和彻底维修,已严重磨损的元件必须更换。随着时间的延长,发生故障的机率越来越高。
2、液压系统常见故障的分析和排除方法
掌握故障发生的规律,有助于针对性地做好各个时期的使用维护工作。一个液压系统产生故障的原因是多方面的,而且液压传动是在封闭情况下进行的,不能从外部直接观察,不像机械传动那样看得清楚;在测量和管路连接方面也不如电路那样方便。因此,当系统出现故障时,要寻找故障生产的原因往往是有一定难度的。能否分析故障产生的原因和排除故障,一方面取决于对液压传动基本知识的理解程度,另一方面有赖于实践经验的不断积累。
(1)液压系统故障的分析方法
当液压系统发生故障时,应进行认真仔细的分析,列出可能产生故障的一切原因,再逐个分析,排除次要因素,最后找出产生故障的主要原因。有时一种故障可能是由某一元件的毛病所引起的,也可能是几个问题的综合。这不仅要了解液压系统的工作原理,而且还要了解每个元件的结构原理及其作用。熟悉液压系统原理图,搞清各回路和液压元件的功能是分析故障的基础;深入实际,了解液压设备的使用及维修状况,是找出故障产生原因的关键。诊断方法有耳听、目测、手感等方式,必要时可用专用仪器和试验设备进行检测。一般应在做出正确结论之后,才考虑排除故障的具体方法。总之,通过理论知识的学习和不断积累实践经验,便可逐渐学会液压系统故障的分析和排除方法。
(2)液压系统常见故障的排除方法
液压设备在运行中常见出现的故障大致有五类,即漏油、发热、振动和噪声、压力、速度不稳定。液压系统的故障发生有相当一部分是由液压元件的故障所致,因此,应首先熟悉和掌握各种液压元件的常见故障及排除方法。表9-1为液压系统常见故障的分析和排除方法。
表9-1 液压系统常见故障和分析和排除方法
故障类别 |
故障现象 |
故障元件 |
故障原因 |
排除方法 |
振动和噪声 |
产生振动和噪声 |
液压泵 |
进油口密封不严,以致空气进入 |
拧紧进油管接头螺帽,或更换密封件 |
液压泵轴径处油封损坏 |
更换油封 |
进口过滤器堵塞或通流面积过小 |
清洗或更换过滤器 |
吸油管径过小、过长 |
更换管路 |
油液黏度太大,流动阻力增加 |
更换黏度适当的液压油 |
吸油管距回油管太近 |
扩大两者距离 |
油箱油量不足 |
补充油液至油标线 |
固定管卡松动或隔振垫脱落 |
加装隔振垫并紧固 |
压力管路管道长且无固定装置 |
加设固定冒卡 |
溢流阀阀座损坏、调压弹簧变形或折断 |
修复阀座、更换调压弹簧 |
电动机底座或液压泵架松动 |
紧固螺栓 |
泵与电动机的联轴器安装不同轴或松动 |
重新安装,保证同轴度小于0.1mm |
压力不稳定 |
系统无压力或压力不足 |
溢流阀 |
在开口位置被卡住 |
修理阀芯及阀孔 |
阻尼孔堵塞 |
清洗 |
阀芯与阀座配合不严 |
修研或更换 |
调压弹簧变形或折断 |
更换调压弹簧 |
液压泵、液压阀、液压缸等元件磨损严重或密封件破坏造成压力油路大量泄漏 |
修理或更换相关元件 |
压力油路上的各种压力阀的阀芯被卡住导致卸荷 |
清洗或修研,使阀芯在阀孔内运动灵活 |
动力不足 |
检查动力源 |
速度不稳定 |
系统流量不足 |
液压泵吸空 |
修理液压泵 |
液压泵磨损严重,容积效率下降 |
修复达到规定的容积效率或更换 |
液压泵转速过低 |
检查动力源将转速调整到规定值 |
变量泵流量调节变动 |
检查变量机构并重新调整 |
油液黏度过小,液压泵泄漏增大,容积效率降低 |
更换黏度适合的液压油 |
油液黏度过大,液压泵吸油困难 |
更换黏度适合的液压油 |
液压缸活塞密封件损坏,引起内泄漏增加 |
更换密封件 |
液压马达磨损严重,容积效率下降 |
修复达到规定的容积效率或更换 |
液压缸爬行(或液压马达转速不均匀) |
液压泵吸空 |
修理液压泵 |
接头密接不严,有空气进入 |
拧紧接头或更换密封件 |
液压元件密封损坏,有空气进入 |
更换密封件保证密封 |
液压缸排气不彻底 |
排尽缸内空气 |
发热 |
油液温度过高 |
系统在非工作阶段有大量压力油损耗 |
改进系统设计,增设卸荷回路或改用变时泵 |
|
|
压力调整过高,泵长期在高压下工作 |
重新调整溢流阀的压力 |
|
|
油液黏度过大或过小 |
更换黏度适合的液压油 |
|
|
油箱容量小或散热条件差 |
增大油箱或增设冷却装置 |
|
|
管道过细、过长、弯曲过多,造成压力损失过大 |
改变管道的规格及管路的形状 |
|
|
系统各连接处泄漏,造成容积损失过大 |
检查泄漏部位,改善密封性 |
【返回目录】