《制桶工培训教程》
杨文亮 辛巧娟 编著
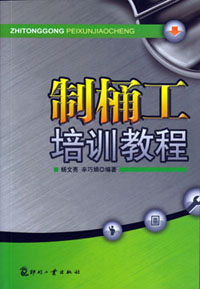
第六章 桶底顶冲压和预卷成形
本章主要学习桶底顶冲压成形、预卷边,以及封闭器的成形加工等工序的技术要求、设备结构、操作维护、质量控制等方面的内容。重点掌握冲压工艺的基本知识和设备的安全操作、维护保养等关键技术,掌握封闭箍式封闭器的生产方法和工艺要点。
第一节 桶底顶冲压成形
冲压加工在钢桶生产中有着很重要的地位,它是在钢桶生产中应用广泛的一种加工工艺,钢桶的桶底顶盖和封闭器等大量零部件均采用冷冲压方法加工。
一、冲压加工的工艺要点
(1)冲压生产应选择合适的材料组织生产,不能满足冲压工艺要求的材料(延展性差、表面粗糙、薄厚不均等)不能投入生产。
(2)冲压工艺设计时,应尽快选择复合模具生产,以便提高生产效率和产品质量。
(3)钢桶冲压件的尺寸必须符合产品的工艺要求,避免形状及尺寸精度超差,影响钢桶整体质量。
(4)桶底顶拉深不允许有破损、裂纹等致命缺陷,以免造成废品。
(5)冲压件表面不应有皱纹、翘曲不平等形状缺陷,以免影响产品美观和影响后道工序的质量。
(6)冲裁边缘不应有毛刺,以免对后道工序的设备造成过大磨损,影响设备寿命。
(7)冲压件表面不应有机械划伤,以免影响产品的表面质量。
二、冲压成形方法及设备
1、冲压成形的方法
冲压成形是利用冲压设备和冲模,使毛坯发生塑性变形或分离的加工方法。
所有冲压方法,从工作原理上基本可归纳为分离和变形两大基本工序。分离工序是使毛坯材料发生剪切破裂的冲压工序,如落料、切断、冲孔、切口等都属于分离工序,在冲压工艺上通常称为冲裁;变形工序是使毛坯材料产生塑性变形的冲压工序,如弯曲、拉深、翻边等都属于变形工序。在钢桶生产中,多数冲压加工工序都是多种冲压工序组合在一起的复合工序,是利用复合模具来实现的,例如桶底顶的成形是冲裁和拉深相结合的工序。
冲裁是利用冲模使材料分离的一种冲压工序。一般来说,冲裁工艺主要是指落料和冲孔工序。当冲裁以后,板料分成两个部分,即落料部分和带孔的部分。若冲裁的目的是为了制取一定外形的冲落部分,则该工序称为落料;若为了制取内孔,则称为冲孔。
拉深是利用模具使冲裁后得到的平面毛坯变成为开口的空心零件的冲压工艺方法。拉深时,其凸模与凹模和冲裁时不同,它们的工作部分都没有锋利的刃口,而是做成一定的圆角半径,并且其间的间隙也稍大于板料的厚度。在凸模的作用下,毛坯在凹模端面和压边圈之间的缝隙中变形,并被拉进凸模与凹之间的间隙里形成空间零件的直壁。
2、冲压设备的工作原理和结构
冲压设备通常有三种类型,即曲柄压力机、螺旋压力机和液压机。钢桶生产中最常用的是曲柄压力机。曲柄压力机是由机身、传动系统、离合器、制动器、曲轴滑块机构和下部拉伸垫等部件组成的。如图6-1为曲柄压力机的结构示意图。
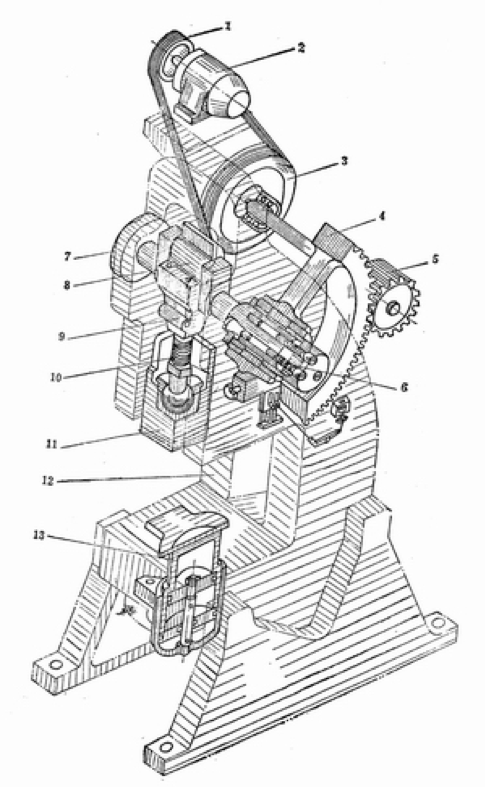
图6-1 曲柄压力机结构示意图
1-小皮带轮;2-电动机;3-飞轮;4-大齿轮;5-小齿轮;6-离合器;7-制动轮; 8-曲轴;9-边杆;10-螺杆;11-滑块;12-机身、13-位伸垫
曲柄压力机工作时,电动机通过飞轮驱动曲轴旋转,曲轴轴心线与其上的曲柄轴心线偏移一个偏心距r。连杆是连接曲柄和滑块的零件。连杆用轴承与曲柄连接,连杆与滑块的连接是通过球头铰接的。因此,曲轴旋转时就使滑块作上下的往复直线运动,这就是曲柄-连杆机构。这机构不但能使旋转运动变成往复直线运动,还能起力的放大作用,即增力作用,使滑块在最下位置时产生最大的压力。
冲压模具的上模固定在滑块的下平面上,下模固定在工作台板的平面上,因此,滑块每上下运动一次就完成一次冲压动作。虽然滑块的往复直线运动是由曲柄的回转运动促成的,曲柄也是匀速的转动,但是滑块在其行程中各点的速度是不一样的。在滑块向下行程时,滑块在上死点的速度等于零。滑块继续向下运动,其速度就增加到某一个最大值,到达下死点时,其速度又重新降至零。在向上行程时和向下行程时一样,滑块的运动速度重复由零至最大再由最大降至零这个范围内变化。
压力机的飞轮有着比较特殊的作用。压力机是一种间歇作功的机器,曲轴回转一周滑块进行一次冲压工作,而实际工作行程仅占整个行程很小的一部分,在这很小的一段行程中却要做很大的功,属于冲击负荷的性质。按照压力机做功的要求,需要选定一个非常大的电机,但是这样大的电机,只有在很短的工作时间里才满负荷,而在大部分空程时间里负荷很小,这样必造成很大的浪费,飞轮就是为了解决这一问题设置的。飞轮一般是装在第一级齿轮传动的高速轴上,这样电动机的功率可以大为减少,因为当滑块不动时,电动机带动飞轮空转,把电机供给的能量储存起来。在冲压制件的那一短暂时间内,主要靠飞轮释放能量。释放的方式是转速降低。当制件冲压完成之后,负荷减少,于是电机带动飞轮加速旋转,使它在冲压下一个制件之前恢复到原来的转速。这样一来,冲压制件所需的能量,也就是高峰负荷,便可以大大减少了。
离合器和制动器在压力机上的作用是,在飞轮不停止旋转的情况下,开动或停止压力机。离合器和制动器一般是设置在飞轮轴上。当滑块需要开动时,通过控制系统,使制动器脱开,离合器结合,电动机、飞轮的旋转运动和能量通过离合器传递给传动齿轮和滑块。当需要停止滑块时,通过控制系统使离合器脱开,制动器制动,将飞轮以下的运动件制动住,使压力机停车。压力机在不工作时离合器总是处在脱开状态,而制动器则总是处于制动状态。
滑块机构包括滑块体、闭合高度调节机构、平衡装置、过载保护装置、退料装置等组成。滑块本体是一个箱形结构,下平面上开有梯形槽或螺丝孔,用于固定冲模的上模板。闭合高度调节机构是为了适应不同闭合高度的模具能在一台压力机上安装而设置的。平衡装置是为了消除上模零件之间的应力和摩擦,减小振动和噪声而设置的。退料装置的作用是在滑块向上回程时,把制件从上模中顶出来。过载保护装置的作用是为了防预防压力机在生产和调整的过程中,可能发生过载现象而损坏设备。
拉伸垫的作用有两个方面,一是在拉深工序时把板料的边缘压紧,使制件在拉深过程中不致出现皱纹。二是在冲压工序终于时把成形的制件从下模中顶出。拉伸垫有橡皮式和弹簧式的,也有纯气式的和液气式的。
三、冲压模具的结构
1、冲压模具的基本结构
从冲模的结构来看,其主要零部件,依冲模类型不同而异。在钢桶生产中,结构比较典型的冲压模具有落料冲孔模、弯曲模、落料拉深模等,桶底顶冲压成形多为落料拉深模。从工艺上分析,落料拉深模是由一道落料基本工序和一道拉深基本工序复合而成。如图6-2为典型的落料拉深模结构示意图。它主要由上下模板、导柱导套、凸凹模,退料装置、挡料装置、压料装置等组成。
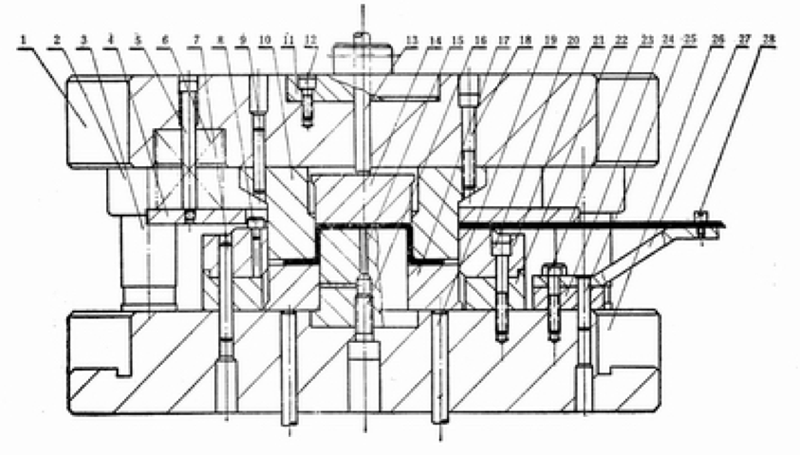
图6-2 落料拉深模结构示意图
1-上模板;2-衬套;3-导柱;4-退料板;5-退料板螺钉;6-弹簧;7、9、25-柱销; 8-定料销;10-凸凹模;11-模柄;12、16、18、20-内六角螺钉;13-推杆;14-顶出器; 15-凸模;17-压料圈;19-托杆;21-凹模;22-固定板;23-外六角螺钉;24-垫板; 26-下模板;27-托料板;28-挡料螺钉
落料拉深模的工作过程是:放入的毛坯托在凹模21、压料圈17和托料板27上。依靠定位销8和挡料螺钉28定好位置。上模下行时,由退料板4将毛坯压住,然后凸凹模10开始落料。此时压料圈17借托杆19紧紧的压住了毛坯,防止拉深时起皱。上模回程时,压料圈17将制件从凸模15上顶出,卡在凸凹模10内,直到推杆13碰到压力机的打料横梁,推动顶出器14将拉深工件顶出。
组成模具的全部零件,根据其功用可以分成工艺结构零件和辅助结构零件两大类。工艺结构零件直接参与完成工艺过程并和坯料直接发生作用,包括:工作零件(直接对毛坯进行加工的零件)、定位零件(用以确定加工中毛坯正确位置的零件)、压料、卸料及出料零件。辅助结构零件不直接参与完成工艺过程,也不和坯料直接发生作用,只对模具完成工艺过程起保证作用或对模具的功能起完善的作用,它包括:导向零件(保证模具上下部分正确的相对位置)、固定零件(用以承装模具零件或将模具安装固定到压力机上)、紧固及其他零件(连接紧固工艺零件与辅助零件)。
四、压力机和冲模的使用与维护
1、压力机的使用与维护
由于压力机操作事故率较高,所以冲压作业中,对冲压设备的维护保养和操作,必须特别强调安全。
(1)操作工必须了解压力机的型号、规格、性能及主要构造。了解模具对材料的要求,不应使用超过模具间隙厚度要求的材料。
(2)开机前,必须检查设备。设备的安全防护装置应齐全有效,离合器、制动器及其控制装置应灵敏可靠,紧固件应不松动,电器的接地保护应可靠。
(3)操作前,必须准备好个人防护用品,工具准备齐全,机器周围清理整洁,毛坯材料码放整齐平稳。
(4)严禁在设备工作台面和模具上放置量具及其他物件。
(5)当设备、模具和其他有关装置发生故障时,必须停机检查。当离开工作岗位时,应切断电源。
(6)两人以上同时操作时,要分工明确,配合协调,避免动作失误。
(7)做好交接班工作。开机前应查看交班记录,了解上一班设备的运行情况。按规定加油润滑,经试车运转正常后方可正式开机。
(8)规定用工具取放冲压件的作业,不得用手直接操作。
(9)规定用单冲的作业,不得连冲。单冲时,冲一次踏一次,并随即脱开脚踏板。
(10)工作期间,发生下列情况时应停机:
a.滑块停点不准或停止后自动滑下。
b.设备发生不正常的响声。
c.冲压件或废料卡在模具里。
d.模具上同时有一个以上毛坯。
e.模具上有废料未被及时清除。
f.控制装置失灵。
2、压力机常见故障及维修
表6-1为压力机常见故障及维修措施。
表6-1 压力机常见故障及维修措施
序号 |
故障现象 |
原因分析 |
维修措施 |
1 |
轴承(连杆支承、曲轴支承)发热 |
轴承配合间隙太小 |
重新调整配合间隙或刮研轴承 |
润滑不良 |
检查润滑情况 |
2 |
连杆球头处有撞击声 |
连杆环头配合松动 |
应拧紧连杆球头处的调整螺母,控制配合间隙到正常值 |
3 |
滑块导轨发热 |
润滑不良 |
检查润滑情况,立即润滑 |
导轨面拉毛 |
调整配合间隙到正常值 |
配合间隙太小 |
将拉毛的导轨面重新刮研修理 |
4 |
停机后滑块自动下滑 |
滑块导轨间隙太大 |
调整间隙 |
制动力不足 |
调整制动力 |
5 |
开机、停机时滑块动作不灵,或停机时停止位置不准 |
离合器和制动器失录 |
修理离合器和制动器 |
离离合器和制动器调整不适当 |
调整离合器和制动器 |
摩擦式离合器摩擦面有油污 |
清理摩擦面 |
易损件损坏 |
更换易损件 |
3、冲模的使用与维护
(1)操作工必须了解冲模的基本结构、冲模的特点和使用该冲模时应注意的事项。
(2)检查原料毛坯是否符合工艺要求,不符合要求时,应及时更换。
(3)清理工作现场,布置好工位,将需要用的操作工具及安全防护装置等都准备好,放到规定的位置上。
(4)检查冲模有无缺损零件和紧固螺钉有无松动现象。给润滑部位全面润滑。
(5)开空车运行数次,检查压力机和冲模的运转情况。正常后,开机正常工作。
(6)工作时,送料要平稳,定位要牢靠,不可用力冲击定位部件。及时清除冲裁废料,不可使异物落入冲模内。按规定在毛坯上擦抹润滑液。
(7)毛坯、成品应轻拿轻放。注意退料板、压料圈及顶出器等的运动情况。
(8)随时观察毛坯和冲压件有无质量缺陷。发现异常现象时,应立即停车检修,不得凑合使用。
(9)发生压力机或冲模事故,必须保留现场,及时报告设备管理人员处理。
(10)工作结束后,应及时清除冲模中的废料和污垢等,拭擦冲模。
(11)擦拭压力机,清理工位,收拾好生产所用的工具。
五、桶底顶冲压成形工艺质量控制
表6-2为桶底顶冲压成形常见缺陷、原因分析及解决办法。
表6-2 桶底顶冲压成形常见缺陷及解决措施
序号 |
缺陷 |
原因分析 |
解决措施 |
1 |
皱纹 |
毛坯厚度不均或材料拉深性能差 |
更换材料 |
模具拉深间隙大 |
修理模具间隙或更换较厚的材料 |
压料力太小 |
调整压料力 |
压料圈或凹模表面磨损严重 |
修理磨损的部件 |
毛坯上涂润滑油过多 |
适量涂抹润滑油 |
托料杆长短不一或压料弹簧布置不均 |
调整托料杆或压料弹簧 |
2 |
裂纹和断裂 |
材料拉深性能不好 |
更换材料 |
材料厚度超差 |
更换材料 |
材料表面质量不好 |
清理材料表面或更换材料 |
冲模压料力调整不当 |
调整压料力 |
凹模或压料圈局部磨损严重 |
修理磨损部件 |
冲模间隙过小 |
修理模具间隙 |
模具润滑不及时 |
按规定及时润滑 |
压力机下滑块端面与工作台的平行度超差 |
调整或修理压力机 |
3 |
形状和尺寸精度超差 |
模具间隙过大或过小 |
调整模具间隙 |
行程调整不当 |
调整滑块行程 |
4 |
拉深件表面擦伤 |
凹模材料不当或表面粗糙 |
更换凹模材料或修理表面 |
拉深间隙小 |
调整间隙或修理模具 |
毛坯表面质量不好 |
更换材料或加强润滑 |
【返回目录】