《制桶工培训教程》
杨文亮 辛巧娟 编著
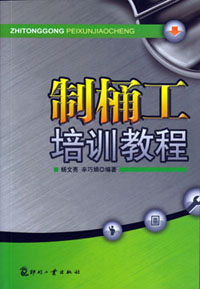
第四章 钢桶的焊接
第二节 缝焊工序
缝焊是采用缝焊机对卷圆后的桶身纵缝进行焊接,目前常见的缝焊机有半自动缝焊机和全自动缝焊机,另一种就是介于半自动与全自动焊机之间的半自动改型焊机,虽然设备不同,但焊接要求是一样的,主要要求焊缝要有足够的强度和密封性。
一、缝焊工艺要点
以焊接200L钢桶桶身为例,一般钢材为08号优质碳素钢板、热轧板或A2、A3普通碳素钢冷轧板,材料厚度多为1~1.2mm。
采用FN1-150-5型缝焊机进行缝焊时,焊接速度为1.5~3m/min;焊接电流为14~18kA,电极压力为2~3kg/cm2,焊缝宽度为5.5+0.5mm。
工艺要求一般为:
(1)焊缝两端应脱焊,但脱焊处长度不得超过3mm。
(2)焊缝两端不允许出现拉长凸嘴。
(3)焊缝强度不得低于原材料的抗拉强度。
(4)焊缝要平直,不得偏斜或脱出搭边,无开焊或裂边。
(5)焊缝外观要均匀,不得出现起泡、飞剌、烧黑或起皮现象。
(6)缝焊搭边尺寸应符合工艺要求。
二、缝焊机原理及结构
1、缝焊机的工作原理和特点
缝焊机的焊接原理与点焊机基本相同,即将准备好的桶身工件置于两极之间加压,并对焊接处通以电流,利用桶件电阻产生的热量加热并形成局部融化(或达到塑性状态),断电后,在压力继续作用下,形成牢固接头,这是电阻焊的一种型式。
与点焊不同的是,缝焊时,电极是滚盘型式的,因电极轮不断转动,电极轮与板件相对位置不断变化,形成了一个个重叠的焊点。按核心熔化重叠度不同,可以分为滚点焊和气密缝焊。缝焊一般采用交流脉冲电流或调幅电流,也可用高频或直流电流。钢桶生产中以气密缝焊占多数,组成气密缝焊的各个焊点的形成过程,同样存在加压、加热熔化和冷却结晶三个阶段,但与点焊过程有两点最主要的区别,其一是传递压力、通电加热的电极轮不断转动变换焊接位置,所以焊缝密封性能与焊接速度关系较大;其二是不可避免的分流使熔化区尺寸减小。
2、缝焊机的结构
(1)半自动缝焊机
国内大多数制桶企业都是采用通用型半自动缝焊机进行钢桶的桶身焊接,虽然各企业都为了提高生产效率和质量,对半自动缝焊机进行了不同程度的改造,但主要结构并没有太大的改变。
半自动缝焊机一般由机身、焊接变压器、焊轮加压装置、气路系统、上下焊头系统、传动系统、冷却水系统、控制系统等组成。如图4-2所示为通用半自动缝焊机结构示意图。
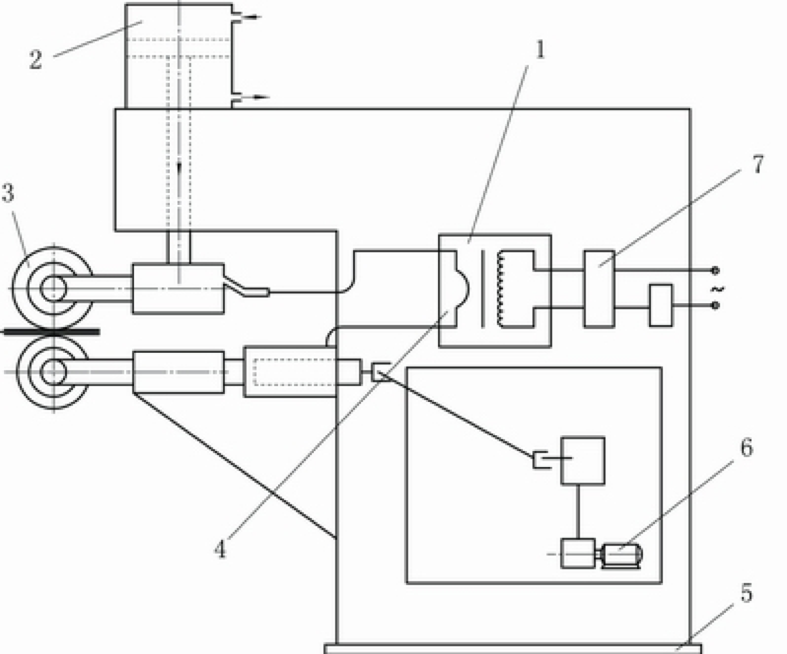
图4-2 半自动缝焊机结构示意图
1-变压器;2-加压系统;3-上下电极轮;4-焊接回路;5-机身;6-传动系统;7-控制系统
半自动缝焊机的减速系统一般采用可调速的直流电动机,也有采用交流电动机,通过齿轮减速箱由刚性连轴器带动摩擦轮支架的锥齿轮,再由锥齿轮传动驱动一对正齿轮转动,正齿轮再带动摩擦轮。由弹簧压紧在电极焊轮上的磨擦轮使焊轮旋转。这种传动使得电极轮无论直径如何变化都能获得相等的线速度。
半自动缝焊机的气动加压系统属固定行程的气缸装置,只有一个活塞,但活塞的行程由气缸活塞杆另一端的螺杆确定。另外,气压系统中还装有压力继电器,此装置是保证气路达到一定压力值时才能接通焊接电流。此压力须根据焊接需要加以调节。
半自动缝焊机的导电系统一般采用滑动接触导电方式,导电间隙内用石墨、蓖麻油或锭子油保证其润滑导电。也有用银合金斜面滑块作导电块的,此方法接触面好,磨擦小,对于型面接触不良处,能自动补偿,接触面能达到80%以上。
缝焊机的电极是电极轮。电极轮的缘面形状、宽度、直径、冷却方式和安装方法均与焊接质量有直接关系。
(2)全自动缝焊机简介
全自动缝焊机与半自动缝焊机的原理基本相同,不同的是全自动缝焊机实现了自动送料、卷圆、搭边定位和焊接。其桶身周向定位机构、桶身导向机构和桶身推进机构是自动缝焊机完成自动送料的三大关键装置。有了这三大机构,不但实现了进出料自动化,而且省去了点焊定位这一环节,大大简化了钢桶焊接工艺。此外,全自动缝焊机还将钢板卷圆、桶身输送、直缝焊接、焊缝滚压集为一体,真正实现了从平直钢板进入到缝焊完成及桶身送出的自动化生产。
全自动缝焊机主要由机身、自动进料系统、桶身卷圆系统、输送系统、寻缝推进系统、定位电极系统、滚压卸料系统、气动系统、冷却系统、电源及控制系统等组成。如图4-2为全自动缝焊机外型结构示意图。
全自动缝焊机的工艺流程分为自动进料、卷圆、待焊、焊接、滚压焊缝、卸料等六个工位。进料的推进方向与卷圆成形轴线垂直;卷圆、待焊、焊接、焊缝压平、卸料各工位上的零件轴线均同轴或平行。
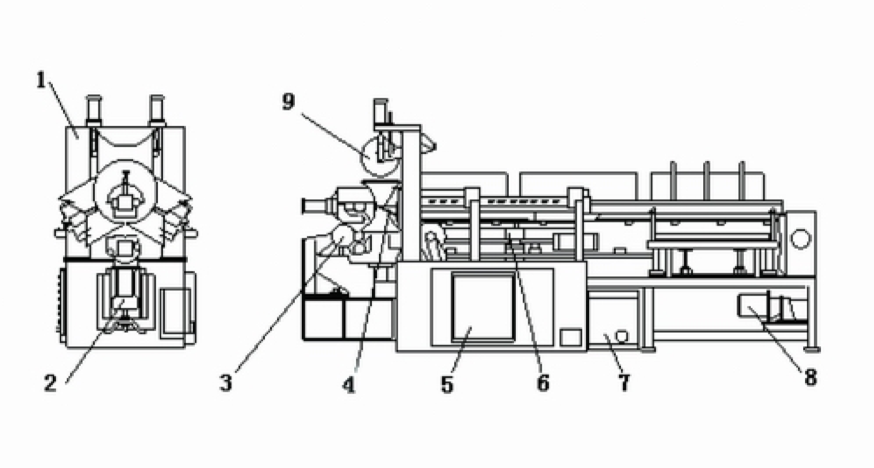
图4-3 全自动缝焊机结构示意图
1-机身;2-加压系统;3-滚压系统;4-焊轮系统;5-传动系统; 6-推进系统;7-电源控制系统;8-卷圆系统;9-定位系统
自动进料系统由自动上料机构、驱动机构、抽真空装置和两段输送滚道等组成。钢板毛坯由叉车运送到自动上料机构的辊筒平台上,自动上料机构即可把钢板自动吸送到卷圆机构中,并开始工作循环。
桶身料毛坯在三辊卷圆机构中被加工成圆筒状。桶的直径可以通过调整活动辊与固定辊及压紧辊的距离相应改变。
输送机构把圆筒状的工件,由拨爪推至待焊工位短暂停留,待焊接工位的工件焊接完毕后,推进部件可将工件再次从待焊工位推至焊接工位,进入焊接状态。随后快速退回原位,等待下一个循环。
上电极轮安装在上电极部件的前端,其后端为悬臂支架。下电极气缸通过下支座对上电极轮施加电极压力。上、下电极轮中间均装有电极冷却管路。
焊完的焊缝随即经过两组滚压轮的滚压,提高熔缝熔核的搭接量,并使焊缝外形表面平整光滑。焊接完毕的工件通过卸料部件的输送带及滚道,送到卸料位置,然后,卸料气缸将工件顶出,完成一个工件的焊接循环。
底座部件上的龙门框配有三个定型压轮组,可与定形滑道一同保证施焊工件的直径和搭接量。缝焊机的进料、电极轮轴向移动、产生电极压力、卸料等运动均以压缩空气作动力源。润滑系统分导电脂润滑部分和普通润滑脂润滑部分,两部分分别用各自的干油泵自动供给润滑脂。
控制部分采用PLC编程控制器和人机界面组成,整个操作系统由最新技术触摸屏式控制,全中文显示,直接显示故障原因,维修方便快捷。
三、缝焊机的操作与维护
这里我们以国内常用的半自动缝焊机为主进行说明。全自动焊机各种机型区别较大,应以焊机使用说明书为准进行操作和维护。
1、缝焊机的操作规程
(1)先打开气路系统,用调压阀确定电极压力,在无焊接电流的情况下调好压力继电器。
(2)开机前,检查设备的传动件、紧固件是否正常,安全防护装置是否完好,气路、水路是否畅通,特别是焊接变压器更要注意。确保焊机的控制器可靠接地。一切正常后,按规定对设备进行全面润滑。
(3)接入电源,将控制箱上电源控制开关转到“通”位置,并接通可控硅冷却水。
(4)选择好焊接变压器级数,将机身上控制电路、压力、电流开关置“通”位置,此时踩脚踏开关上面的开关焊接就开始,踩脚踏开关踏板焊接就结束。
(5)根据所缝焊的材料厚度、材质,调定焊接电流、电压、压力等参数。运行过程中,应注意观察冷却水量是否充足,绝缘是否良好,发现异常,应立即停机检修。
(6)先不带电试运行,将电流开关置于“断”位置,如需修整焊轮,上电极置于上升位置,则压力开关置于“断”位置,上下电极焊轮空转。
(7)工作时,应在接通水路和气路后方可接通电源。焊机温度不得超过规定温度(75℃)。
(8)工作时焊机和控制箱的门必须关闭。在电源和气源未切断以前,禁止在焊机上进行任何安装检修工作。
(9)工作完毕后,切断电源、气源,等设备冷却后,切断水源,并清理设备及现场。
2、缝焊机的调试与使用
(1)焊接压力调节:焊接压力的调节是通过调节调压阀来实现,并由气压表指示其气压,焊接压力须视焊件的材料与厚度作相应调节,以免因压力不够造成飞溅或因压力过大造成焊接不良。
(2)电极焊轮下压速度调节:将功能选择旋扭置于电极调整位置,踏动、松开脚踏开关,焊轮将上下运动,此时,根据上焊轮上升与下降速度调节限流阀及气缸座处的缓冲调节钮,直至焊轮上下速度适当。
(3)上下焊轮间距调节:上下焊轮间应小于焊轮的最大工作行程,调节上下焊轮之间距至适当(约25mm)。注意在以上过程中,不要踏动脚踏开关,以免造成误通电而烧毁焊轮,发生危险。
(4)焊接速度调节:可根据不同材料,厚度的桶件调节电动机转速,电机转速由电机控制器控制,速度控制参数可调定范围一般为1~60,设定参数为60时为最大。
(5)焊机按程序动作:
a.根据桶身的材料及厚度,选择适当的规范(可参照《钢桶制造技术》或焊机说明书),分别调节程序1、2、3十个功能项的参数值;
b.将功能选择旋钮置于运行位置,踏动脚踏开关,焊机按程序动作,但没有焊接电流通过;
c.程序1、2、3各动作一次。注意桶身的焊接质量与焊接电流、焊接时间、焊接压力等焊接工艺规范有着直接关系,因此在焊接时应根据具体情况作相应调整,焊接电流与焊轮压力的调节应同步进行。
(6)焊机正常焊接:
a.动作完全正常之后,将功能选择旋钮置于焊接位置,就可以进行焊接;
b.踏动脚踏开关一次,焊机焊接一次;
c.需进行循环焊接时,将休止时间设置成大于1的数值(休止时间的数值根据实际情况设定),一直踏下脚踏开关,则焊接可进行多次,直至松开脚踏开关(这种循环可配合自动送料机或机械)。
(7)电极焊轮的修整:电极焊轮必须保持光洁,使用一定时期后电极焊轮出现磨损,可用细锉刀或砂纸修平或卸下在车床上加工平整。
(8)每天工作结束后,应依次进行以下操作,保证焊机长期安全运行。
a.关掉总机电源开关;
b.按动滤水器下的排水按钮,排出贮存在里面的水;
c.关掉气源,如果油雾器中的润滑油太少,低于最低刻度,应向油雾器中添加润滑油(应使用适于气缸使用的润滑油);
d.关掉冷却水水源。注意在冬天,环境温度低于0℃时,需将冷却水管中的水排掉并用压缩空气吹去冷却水管内的剩水,以免水管冻裂。
3、焊机的维护和保养
在缝焊机维护保养时,必须关掉总电源,以免发生危险。
(1)日常保养:这是保证焊机正常运行,延长使用期限的重要环节。
a.焊机须在干燥且少灰尘的环境中工作,切忌腐蚀性气体的侵蚀;
b.注意冷却水的流通情况;
c.注意保持焊机的清洁;
d.检查各部位的接触与绝缘情况;
e.焊机使用完毕后切断电源且停止压缩空气及冷却水的供应;
f.为确保良好的焊接效果,在修整氧化和磨损的焊轮表面时,应使用优质锉刀和砂纸。
(2)定期维护检查
a.每天用机后排掉过滤器中的水;
b.每周往油雾器中注入一定量的润滑油,选用纯度较高的润滑油;
c.定期检查机械部分配合是否正常,有无漏水;
d.检查连接是否紧固,特别是电气连接处需定期紧固;
e.检查水路管道有否堵塞,为防止水路堵塞,每月将压缩空气通入冷却管清理水路;
f.检查绝缘是否有损坏,气管和水管是否老化。
四、缝焊质量的控制
1、焊接质量的影响因素
影响缝焊质量的因素很多,一般可归纳为设计、工艺和使用三类。当搭边设计不合理时或材料不合焊接要求时,就会使焊接不易达到质量标准的要求;工艺参数选择不当,电极或夹具不合要求,设备工作不正常,材料表面质量差,以及搭接不良等,都直接影响焊接质量;焊缝的质量要求是否正确,同样会对缝焊质量有影响,当钢桶不在规定技术条件下使用时,则会因环境的恶化而使焊缝性能迅速降低。由于焊接过程机械化、自动化程度较高,故缝焊质量同设备的稳定性及调整水平的关系更为密切。图4-4列出了对焊接质量影响较大的几个因素及相互之间的关系。
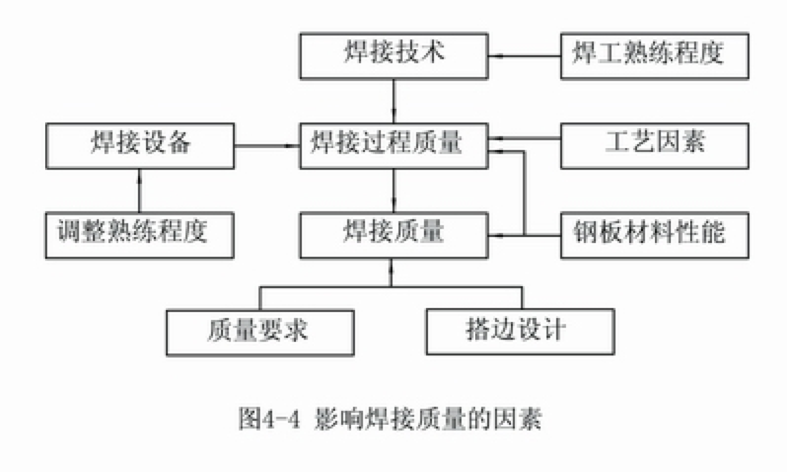
2、常见焊接缺陷及解决措施
如表4-2所示,为钢桶缝焊常见缺陷及解决措施。
表4-2 钢桶缝焊常见缺陷及解决措施
序号 |
缺陷 |
原因 |
改进措施 |
1 |
焊缝表面压痕形状及波纹度不均匀 |
焊轮工作表面形状不正确或磨损不均匀 |
修整焊轮 |
焊接时,焊件与焊轮倾斜 |
检查机头刚度,预调焊轮倾角 |
焊速过快 |
调整焊速 |
2 |
焊点压坑过深及表面过热 |
通电时间过长 |
调整规范 |
电极压力不足 |
改变焊轮端面锥角角度 |
电流过大 |
改善冷却条件 |
3 |
表面局部烧穿或金属强烈外溢 |
焊缝搭边及电极表面不干净,污物多 |
清理板料及电极表面 |
焊轮压力不足,或焊轮与电极间未真正接触 |
提高焊轮压力,更换磨损过度的焊轮 |
焊轮接触表面形状不正确 |
修整焊轮 |
焊整过快,焊轮过热 |
改善冷却条件 |
4 |
焊缝表面发黑,包覆层破坏 |
桶身搭边及焊轮表面清理不良 |
注意及时清理表面 |
焊轮压力不足 |
调整规范 |
通电时间过长,电流过大 |
降低焊轮或改善冷却条件 |
5 |
焊缝边缘压溃或开裂 |
边距过小,焊轮未对中 |
调整规范 |
电流过大,时间过长 |
改进搭边设计 |
大量焊后飞溅 |
注意焊轮安装及桶身放平 |
6 |
焊缝脱开 |
搭边不良,焊接时搭边有错位 |
注意定位,调整板间间隙。 |
7 |
焊缝发脆 |
通电时间短,焊接循环不合理 |
调整规范 |
改变热循环形式 |
8 |
焊缝不气密 |
焊接规范不稳定 |
调整设备与控制装置 |
定位点焊烧穿 |
调整点焊,改善点焊质量 |
上、下焊轮直径相差过大 |
适当改善两焊轮直径或散热条件 |
复习题
1、点焊和缝焊的基本原理是什么?点焊机和缝焊机的基本结构是由哪些部分组成的?
2、缝焊机的工艺参数有哪些?如何调整这些参数?
3、全自动缝焊机与半自动缝焊机有哪些区别?优点是什么?
4、缝焊机的调试和使用应注意哪些环节?
5、如何进行缝焊机的维护和保养?
6、焊接质量与哪些因素有关?
【返回目录】