《钢桶制造技术》
杨文亮 辛巧娟 编著
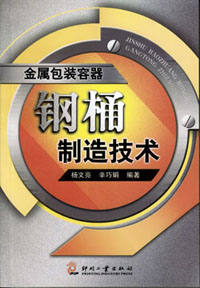
第八章 钢桶桶身焊接工艺
第四节 钢桶焊接设备
三、钢桶全自动缝焊机
1.基本工作原理及对材料的要求
钢桶全自动缝焊机实际上是配以桶身卷圆机的全程自动焊接的专用缝焊机,其焊接工作原理与上述的半自动缝焊机相同。如图8-10是一台钢桶全自动缝焊机的结构示意图。钢板经过裁剪和处理边缘后,在焊机前部自动进料,经卷圆和初步定位后,由推进器沿“Z”形导轨送入定位辊轮和上下焊轮之间。当几万安培的电流通过时,由于桶身搭接处有较高的界面电阻,其热效应造成局部温升。随着温度的增加,钢板内部的电阻迅速上升,两者相互作用,使得焊接部位的金属软化成塑性状态。此时,在上、下焊轮的压力作用下,通过匀速直线运动,因50Hz的电流按正弦波作周期的变化,则形成一个个连续的焊点,这样就将卷圆后的桶身两侧之间,形成一个具有共同晶粒的结合面。在焊缝修正辊的进一步压力作用下,则形成均匀、紧密、牢固的熔接焊缝,因而能承受翻边、压波纹、胀筋和封口过程中的应力,取得理想的工艺效果。
目前各国生产的钢桶全自动缝焊机的工作过程大同小异。一般包括卷圆、输送、焊接、焊缝修正。由于自动化程度和焊接速度均较高,对制作桶身的钢板要求较高:桶身板长、宽误差不得超过±0.5mm,两对角线误差不得超过±1.5mm。钢板焊接边缘应无氧化皮等杂质。对于热轧钢板,边缘要经过除锈处理,以免焊接时电阻增加,出现飞溅和毛刺。根据国外有关研究资料,焊接钢板的几种主要化学元素可按下列公式折算为当量含碳量,来确定其焊接性能。
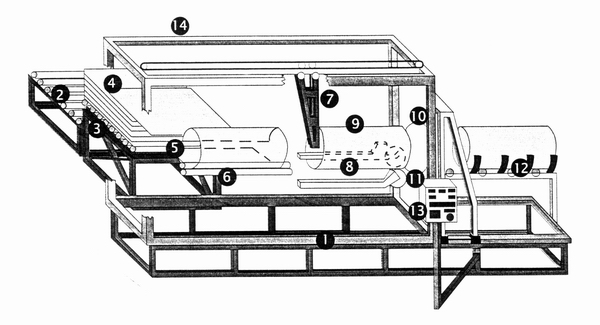
1—机架;2—装卸台;3—升降台;4—有双张控制的分张装置;5—卷圆机构; 6—成圆后的桶身定位;7—桶身传送器;8—中间传送链;9—桶身导向轨; 10—焊缝校准器;11—焊接辊轮及焊缝修正器;12—出桶输送机和卸料台; 13—控制器显示屏;14—控制柜
图8-10 全自动缝焊机结构示意图
当量含碳量E为:
(8-4)
等式右边的字母为化学元素符号,代表元素的分子量。当量含碳量E在0.09左右时,其焊接性能最佳。
2.主要部件及其工作过程
对照图8-10,全自动缝焊的全程工作过程将完成下列各道工序:
(1)卷圆成型:裁剪好的桶身板送入三辊卷圆机构中卷圆,成型辊的送料口通过气动阀门按一定的程序自动开启,可避免向焊机重复送料。在三辊卷圆机构的出口处还有一组小直径的轧辊,以防止卷成的桶身边缘出现过于明显的直线段。
(2)输送桶身:利用直线推进器向焊接工位送进桶身。目前,各国焊机一般采用以下两类推进机构:其一是曲柄式推进器,这种推进器运动过程的起、止阶段机构速度变化平缓,而保证了桶身运动的平稳性。其二是链条,棘爪式推进器,为了减少起动和到位的惯性力,链条传动由双速马达驱动。
(3)定位和焊接:焊接工位由“Z”形导轨、定位辊和上、下辊轮组成。桶身由气动的棘爪推杆沿“Z”形导轨推入上、下辊轮之间。桶身依靠“Z”形导轨两侧定位槽的逐渐接近,桶身两侧边缘逐渐靠拢。当桶身离开导轨而进上、下辊轮时,桶身两侧顺利重叠,同时依靠“Z”形导轨确保重叠部位与辊轮中心对齐。上、下辊轮和外径定位辊是焊接和稳定桶身位置的重要部分。辊轮是由高硬度和高导电率的铜合金制成(一般要求其硬度达到HB65以上,导电率达到75IACS以上)。为了使辊轮不致因大电流发热而变形损坏,上、下焊接回路连同上、下焊轮采用了循环水内冷却系统。另外,上、下焊轮均安装了侧向移位机构。每焊一个桶身,上、下焊轮的散热效果和表面的质量均匀一致。外径定位辊一般由一组铜辊组成,通常有单排三辊和双排六辊两种结构。桶身被送入焊轮时,也同时进入定位辊,以保证焊缝焊接时不致偏移。桶身进入和离开焊接工位时,焊接电源的导通和裁止,是通过一组红外线桶身位置检测装置控制的。
(4)焊缝修正:由于采用搭接焊工艺,普通焊机焊接过的桶身焊缝正、反两面均有一定台阶,致使搭接处的厚度约为钢板厚度的两倍。这给以后钢桶内、外涂装工艺和底、盖与桶身的卷边装配都带来很不利的因素,因此,在钢桶全自动焊机上,紧靠着焊轮,有一组轧辊与焊轮以同样的线速度转动。当桶身的焊缝刚刚离开焊轮,尚处于红热状态时,即进入一组轧辊。在一吨左右的压力碾压下,不仅使焊缝的内部结构更加致密,而且消除了焊缝搭边的台阶,形成平整而光滑的平面焊缝。其厚度仅为桶身钢板厚度的1.2倍左右。
(5)热量和控制程序:因电阻焊工艺焊点形成时间极短,温度场分布窄,影响因素多,所以焊点质量的稳定性是电阻焊长期以来的关键问题。钢桶专用的全自动焊机也不例外,焊机的设计和焊接工艺的确定,其质量控制的内容都占据十分突出的地位。缝焊机质量控制的内容是十分广泛的,但就焊接过程中为保证一个特定精确的温度场而言,其热量控制显然是首当其冲的手段。为了实现这一控制,各种钢桶全自动缝焊机都配有专门的控制器。英国联邦公司的DW250/6型焊机是采用了其专用的UZDVR(上坡、阻抗、下坡、电压调整)部件进行控制。图8-11为该机的热量控制曲线。从这曲线的变化可反应出UZDVR部件具有下列功能:
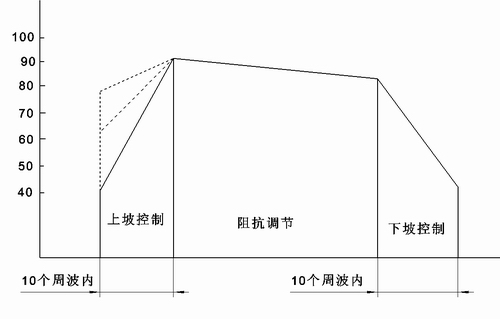
图8-11 热量控制曲线
a)热量控制:焊接电流采取无级调节从40%调到100%。
b)上坡控制:在焊接开始的10个周波内,无级调节焊接电流的起始百分值为40%调到所需的最高电流,形成一定的焊接电流上升曲线的斜率。
c)阻抗调节:在整个焊接过程中,保证了焊接电流逐步下降,以抵消由于桶身离开焊接回路而引起的焊接回路的阻抗变化(次级整流焊机不需进行阻抗调整)。
d)下坡控制:在焊接终了的10个周波内,无级调节焊接电流下降速度,形成一定的焊接电流下降曲线的斜率。
按照预先调定的电流变化曲线图,桶身在焊接过程中,基本能保持稳定的焊接电流和温度场,从而保证了焊缝的质量。
随着计算机技术的发展,焊机在整个工作过程中,各个程序动作已普遍采用了可编程控制进行控制,如英国联邦焊机公司生产的DW250/6型焊机是采用西德西门子公司U-105型可编程控制器。因而,不仅大大减化了传统的程序控制系统,而且还能通过编程器对焊机进行监控和迅速查寻故障,并能直接通过键盘修改程序。
四、钢桶激光焊接机
1.激光焊接机简介
为了解决钢桶传统焊机能耗高、焊接质量不稳定,对焊接材质适应范围窄等固疾而研制的激光钢桶缝焊机,激光钢桶环焊机,是将原电阻焊缝焊机升级换代为激光缝焊机,将原桶底桶盖的卷封机改为激光环焊机,将桶身、桶底、桶盖用激光焊接成一个整体。因为激光热能是将焊接部位的材料熔融而形成具有相当韧性的牢固焊缝,其抗拉强度等于或大于母材,所以其强度比传统焊接要高二倍以上,而且适应金属、非金属各种材质,由于熔融一体无缝隙,即使高温液体、危险品液体也不会产生泄漏,完全达到“零渗漏”的要求。而能耗仅为传统焊机的15%左右。
2.激光焊接的优点
(1)节能效果显著。传统型缝焊机能耗为150KW,而激光焊机能耗仅20KW左右,节约电力85%以上。
(2)加快传统产业技术改造,解除企业更新换代后顾之忧,由于节约了85%的电力每年可节约电费20多万,相当于二至三年的时间节约的电费,就可收回激光焊机的投资。
(3)节约钢材,实现包装减量化。由于激光焊接高强度、零渗漏的优良性能,钢桶板材就能实现薄型化,而且焊缝宽不足1mm,节约了钢材、重量减轻、生产成本下降、运输费用及能耗也相应下降。
【返回目录】