《钢桶制造技术》
杨文亮 辛巧娟 编著
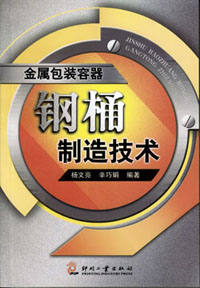
第五章 钢桶的下料工艺
第四节 钢桶毛坯剪切下料工艺
一、下料工艺参数的确定
裁剪下料工艺有尺寸、形状及裁剪口三个方面的要求。
1.尺寸要求的精确计算
裁剪下料工艺对尺寸的要求主要是钢板的长度与宽度。不同规格的钢桶,其长度、宽度当然也不同,即使是一样大小的钢桶,由于制造工艺、设备等不同,钢板的长度、宽度也不尽相同。
钢桶桶身板的长度是根据钢桶的内径和焊接搭接量来确定的,按上节的计算公式进行计算并根据实际进行验证。
2.形状要求
裁剪下料工艺对板材的形状要求是对边平行,邻边垂直,即要求板材呈矩形。制桶生产中,一般不作具体的平行度要求,而是取一个容易测量的综合性指标,即对角线偏差来综合评价。对角线偏差是指板材的两条对角线长度之差。一般来说,板材在尺寸符合要求的前提下,形状不合要求多数呈现平行四边形,因为对边相等已是平行四边形的充要条件。平行四边形的对角线偏差就能确定其邻边的垂直度。比如200升闭口钢桶裁剪下料工艺要求板材的对角线偏差不大于6mm,这个偏差对垂直度的影响有多大呢,我们可以来计算一下。如图5-11所示,钢板长1775mm,宽930mm,对角线即可用勾股定理求得为2003mm。取其最大偏差值6mm,则两对角线分别为2006mm与2000mm。则在△ABC中运用余弦定理即可求得∠BAC=89.58°,也就是说与90°只相差半度也不到,基本上能满足钢桶制造工艺的要求。由此可知,对角线最大偏差值是与板材的尺寸有关的,而其基本要求是邻边垂直公差在±0.5°以内。
3.裁剪口的要求
裁剪下料工艺对裁剪口的要求是平直,无裁剪扭曲,并要求裁剪口毛刺不大于0.5mm。对毛刺的要求是针对200升闭口钢桶而言的。毛刺要求的极限值通常与钢板厚度有关,若采用较薄的钢板制造,该极限值还应该要求小些。
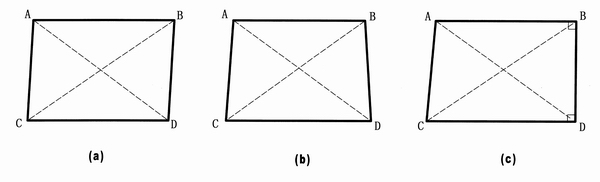
图5-11 下料形状误差
二、钢桶毛坯剪切下料工艺要求
钢桶毛坯剪切下料主要是桶身下料、桶底顶下料和小桶件下料,工艺要求主要有以下几点:
1.长宽尺寸。下料的长宽尺寸是由钢桶的结构及工艺要求计算出来的,误差不能太大。误差太大会影响后道工序的进行,甚至会造成废品。对于80升以上的钢桶,一般桶身料长宽误差不起过±0.5mm;对于80升以上的钢桶,桶身料长宽误差在±0.2~±0.3mm之间为合适。
2.形状误差。有时在保证了料片的长宽尺寸的情况下,并不能算符合要求,因为料片本为矩形,而裁成的形状可能会是平行四边形、梯形等(如图5-11所示),这就是下料产生了形状误差。按要求料片四角应为90°角。对于80升以上的桶身料,两对角线长度之差不得大于5mm;对于80升以下的桶身料,两对角线长度之差不得大于3mm。
3.切口毛刺。为了使桶身料在后几道工序中对设备、模具及工装等有较小的磨损,下料剪切口不能有太大的毛刺,一般要求切口平整,毛刺高度不得大于0.3mm。
4.裁剪方向。一般要求桶身下料的方向要使材料的轧制方向与钢桶轴线平行,这样可使钢桶在波纹、环筋及卷封等处有更好的加工性能和强度。
5.扭曲。有时所剪的毛坯扭曲不平,影响磨边等后道工序不能正常进行。一般不允许有太严重的扭曲,以保证后道工序顺利进行。
二、剪切件常见缺陷及其原因分析
剪切件常见缺陷及原因分析见表5-1。这些缺陷不仅引起材料消耗的增加,更严重的还可能产生废品,影响后道工序的顺利进行和产品质量。
表5-1 剪切件常见缺陷及原因分析
剪切缺陷内容 |
产生原因分析 |
解决方法 |
1、外形尺寸及形状超差 |
1、定位和导板不准确 |
1、重新调整定位 |
2、操作时靠不到位 |
2、认真操作 |
3、板形翘曲度大,有侧弯、端头斜 |
3、采用临时工艺校直和先剪出一基准面 |
2、弯曲线与毛坯板料轧纹方向的夹角不对 |
1、操作不认真 |
1、认真按工艺要求操作 |
2、管理不善 |
2、加强管理 |
3、工艺排样错误 |
3、改进工艺排样 |
3、毛刺大 |
1、剪刃间隙过大 |
1、调整刃口间隙 |
2、剪刃钝 |
2、磨锋或更换刃片 |
4、扭曲 |
1、剪床斜角过大 |
1、调整剪刀角度 |
2、剪切板料窄而厚 |
2、采取校平措施或使用平口剪床 |
【返回目录】