《钢桶制造技术》
杨文亮 辛巧娟 编著
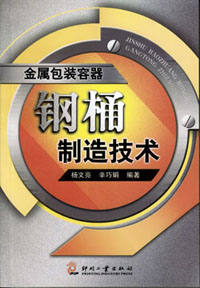
第十六章 钢桶的检验与质量分析
第二节 钢桶成品的标准性能检验
一、气密试验
(一)试验原理
本试验是把样品充气至预定压力,将其浸没于水中或涂一薄层规定的液体。通过检查有无气泡产生而判定样品有无渗漏。
(二)试验设备
1.可提供10kPa~30kPa压缩空气的压力气源。
2.压力表其量程为0kPa~100kPa,分度值为1kPa,精度2级。
3.U型管。
4.水槽。
5.盛装检测溶液的器皿和刷涂工具。
(三)试验程序
1.试样制备:进气孔位置应设置在下列位置之一。
①设在封闭器上;
②在桶体或桶底上开孔;
③设在可替代封闭器并确保密封的专门装置上。
2.装好金属桶封闭器,任意放置,不得使用任何外加固装置。
3.对试样充气至规定气压。
4.将金属桶完全浸没在水槽中,观察有无气泡产生或在金属桶外表面刷涂检测溶液观察是否产生气泡。
5、试验持续时间为5min。应确定气泡是否为金属桶外部结构携带空气所产生。
二、液压试验
液压试验与气密试验方法大致相同,所不同的是不用压缩空气,而是由液压机提供高压水送入桶内。试验时,将桶内注满水,把压力表与加压泵连接,并通过连通部件固定在注入口上,往桶内加压,达到试验压力后,保压,试验压力达到规定值后,保压5min,检查样桶有无渗漏。
三、跌落试验
(一)试验原理
提起试验样品至预定高度,然后使其按预定状态自由落下,与冲击台相撞。
(二)试验设备
1.冲击台:冲击台面为水平平面,试验时不移动,不变形,并满足下列要求。
(1)为整块物体,质量至少为试验样品质量的50倍;
(2)要有足够的面积,以保证试验样品完全落在冲击台面上;
(3)在冲击台面上任意两点的水平高度差不得超过2mm。
(4)冲击台面上任何100mm2的面积上承受10kg的静负荷时,其变形量不得超过0.1mm。
2.提升装置:在提升或下降过程中,应损坏试验样品。
3.支撑装置:支撑试验样品的装置在释放前应能使试验品处于所要求的预定状态。
4.释放装置:在释放试验样品的跌落过程中,应使试验样品不碰到装置的任何部件,保证其自由跌落。
(三)试验程序
1.提起试验样品至所需的跌落高度位置,并按预定状态将其支撑住。其提起高度与预定高度之差不得超过预定高度的±2%。跌落高度是指准备释放时试验样品的最低点与冲击台面之间的距离。
2.按下列预定状态,释放试验样品:
(1)面跌落时,使试验样品的跌落面与水平面之间的夹角最大不超过2°;
(2)棱跌落时,使跌落样品的跌落面与水平面之间的夹角最大不超过2°,试验样品上规定面与冲击台面夹角的误差不大于±5°或夹角的10%(以较大的数值为准),使试验样品的重力线通过被跌落的棱;
(3)角跌落时,试验样品上规定面与冲击台面之间的夹角误差不大于±5°或此夹角的10%(以较大数值为准),使试验样品的重力线通过被跌落的角;
3.实际冲击速度与自由跌落时的冲击速度之差不超过自由跌落时的±1%。
4.试验后按有关标准或规定检查包装及内装物的损坏情况。并分析试验结果。
(四)标准钢桶试验条件
1.小开口钢桶内灌装98%的清水,选钢桶边缘最薄弱部位跌落,跌落后在钢桶最高部位钻孔;
2.中开口和全开口钢桶内盛装95%、密度为1.2g/cm3的沙子和木屑混合物,选钢桶边缘最薄弱部位跌落。
四、堆码试验
(一)试验原理
将试验样品放在一个水平平面上,并在其上面施加均匀载荷。
(二)试验设备
1.水平台面:水平台面应平整坚硬。任意两点的高度差不超过2mm,如为混凝土地面,其厚度应不小于150mm。
2.加载装置:加载装置按照所选定的方法(方法1、方法2或方法3)而定。
(1)方法1(包装件组):该组包装件的每一件都应与试验中的试验样品完全相同。包装件的数目则以其总质量达到合适的载荷量而定。
(2)方法2(自由加载平板):该平板应能连同适当的载荷一起,在试验样品上自由地调整达到平衡。载荷与加载平板也可以是一个整体。加载平板置于包装件试样顶部的中心时,其尺寸至少应较包装件的顶面各边大出100mm。该板应足够坚硬以保证能完全承受载荷而不变形。
(3)方法3(导向加载平板):采用导向措施使该平板的下表面能连同适当的载荷一起始终保持水平,所采用的措施不应造成摩擦而影响试验结果。加载平板置于试验样品顶部的中心时,其尺寸至少应较包装件的顶面各边大出100mm,该板应足够坚硬,以保证能完全承受载荷而不变形。
3.偏斜测试的装置:所有偏斜测试装置的误差,应精确到±1mm。
4.安全设施:在试验时应注意所加负载的稳定和安全,为此,必须提供一套稳妥的试验设施,并能在一旦发生危险的情况下,保证载荷受到控制,以便防止对附近人员造成伤害。
(三)试验程序
1.将试验样品按预定状态置于水平平面上,再将加载用包装件组成或自由加载平板或导向加载平板置于试验样品的顶面中心位置。
2.如果使用方法2或方法3,则在不造成冲击的情况下将作为载荷的重物放在加载平板上,并使它均匀地和加载平板接触,以保证载荷的重心恰好处于包装件顶面中心的上方。重物与加载平板的总质量与预定值的误差应在±2%之内。载荷重心与加载平板上面的距离,不得超过试验样品高度的50%。如在试验特殊加载时,可将合适的仿模放在试验品的上面或者下面,也可以根据需要上下都放。
3.载荷应保持预定的持续时间或直至包装件压坏。
4.试验其间按预定的测试方案记录试验样品的变形,必要时,也可以随时对试验样品的变形情况进行测定。
5.去除载荷,并按有关标准规定检查运输包装件及内装物的损坏情况,并分析试验结果。
(四)标准钢桶堆码试验要求
按照以上的试验设备和试验方法,试验时间为24h,经检查钢桶不应有可能降低强度或引起堆码不稳定的任何变形和严重破损。
堆码负载按下式计算:
(16-3)
式中:P——钢桶容器上施加的堆码负载,N;H——单件钢桶高度,m;h——单件钢桶高度,m;M——单件钢桶盛装物品后的质量,kg;K——劣变系数为1。
五、漆膜附着力测定
漆膜划痕测定法适用于钢桶漆膜附着力的测定。漆膜对钢桶桶体底材粘合的牢度即附着力,按正方格线划痕范围内的漆膜完整程度评定,以级表示。
(一)检验工具
1.单刃划刀:具有30°角圆片刀刃,形状和尺寸如图16-4。
2.导向器刀刃间距宽度1mm,形状如图18-5所示。
3.漆刷:宽25~35mm。
4.四倍放大镜。
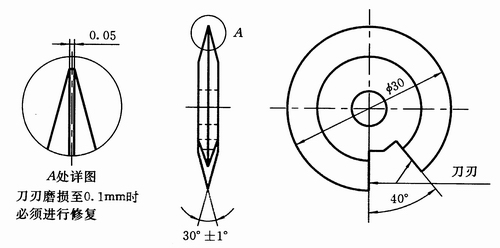
图16-4 单刃划刀
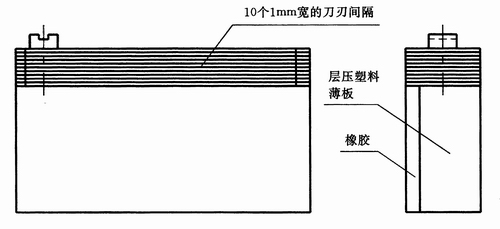
图16-5 导向器
(二)测定方法
1.样板:按GB/T1727制取;或在钢桶的漆膜平整面上直接进行测定。
2.漆层应实干,在室温条件下测定。
3.划痕:用手夹持单刃划刀,使刀的前刃垂直于样板表面或钢桶的平整面,利用导向器,保持平稳,均匀用力,以20~50mm/s的速率,在漆膜上划割长约10~20mm间距为1mm的六道平行划痕。然后转90°,用同样方法划割成正方格。划痕须齐直,并应割穿漆膜的整个深度;划痕应在三个不同的部位进行。若测定结果不一致,应在更多的部位重复进行,否则测定无效。
4.清理划痕:用漆刷沿正方形网格的两对角线方向,来回各轻刷5遍。
5.检验评级:以目侧或用4倍放大镜检查正方形网格划痕,按表16-7的分类,评定漆膜附着力的级别。
表16-7 漆膜附着力测定结果分类
级别 |
说明 |
划痕网格示例 |
0 |
漆膜划痕网格牢固地贴于桶体底材上。划痕网格线完整、光滑、清晰、无剥离 |
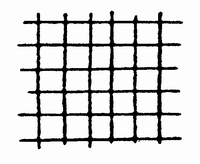
|
1 |
漆膜划痕网格牢固地贴于桶体底材上。但划痕网格边缘或交叉处,不清晰地有小片剥离。破损面积不大于5% |
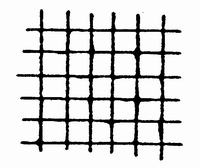
|
2 |
在漆膜划痕网格线边缘或交叉处,可以清晰地看到有小片剥离。但划痕网格破损面积大于5%,小于15% |
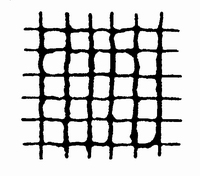
|
3 |
在漆膜划痕网格线边缘或交叉处,出现片状或长条破损,部分小方格剥离。但划痕网格破损面积大于15%,小于35% |
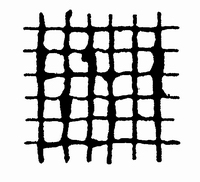
|
4 |
在漆膜划痕网格线边缘有长条破损,网格中的小方格,全部或部分连接成块剥离。但破损面积大于35%,小于65% |
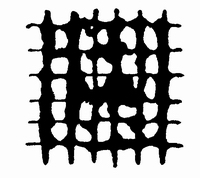
|
5 |
其他,任何超过第4级别的现象,均属此级 |
|
(三)评定标准
漆膜划痕检验级别分为6级(0~5级)。附着力最佳为0级,最差为5级。2级或2级以上能满足钢桶漆膜附着力要求。
【返回目录】