《钢桶制造技术》
杨文亮 辛巧娟 编著
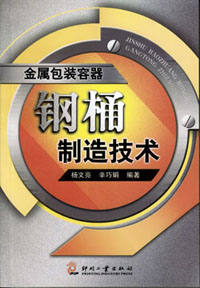
第十六章 钢桶的检验与质量分析
钢桶的质量检验是钢桶生产过程中一道必不可少的重要工序,它不仅存在于钢桶的成品检验,而且存大于钢桶生产的全过程。产品质量的好坏,决定着企业的声誉和命运,所以,质量检验是一定要引起重视的。采取切实可行的方法,始终如一的坚持下去,不让一个不合格的产品出厂。在钢桶的质量管理中,针对质量问题的分析始终是这一领域的最高技术和经验积累。
第一节 钢桶原材料的质量检验
一、钢桶用薄钢板原材料的质量要求
根据行业标准YB/T 055的规定,对200升钢桶用冷轧及镀锌薄钢板要求如下:
1.尺寸、外形
(1)钢板(带)的尺寸应符合表16-1的规定。
表16-1 薄钢板的尺寸要求(mm)
尺寸规格
用途 |
厚度 |
宽度 |
长度 |
桶盖用 |
1.0
1.2
1.5 |
660 |
1980 |
1320 |
桶身用 |
930 |
1800 |
(2)尺寸允许偏差
①钢板(带)厚度允许偏差应符合表16-2的规定。
表16-2 钢板厚度偏差(mm)
公称厚度 |
厚度允许偏差 |
冷轧板(带) |
镀锌板(带) |
1.0 |
±0.09 |
±0.10 |
1.2 |
±0.10 |
±0.11 |
1.5 |
±0.12 |
±0.13 |
②宽度和长度允许偏差:宽度和长度允许偏差为+8mm。
(3)外形
①不平度:钢板的每米不平度不大于8mm。
②镰刀弯:钢带的镰刀弯每2m内不大于6mm。
(4)锌层表面结构:
镀锌板(带)的锌层结构为正常锌花。锌层重量XT1为200g/m2,XT2为275g/m2。XT1和XT2为镀锌板按锌层重量分类的二个牌号,LT为冷轧钢板。
2.技术要求
(1)牌号和化学成分
①钢的牌号和化学成分应符合表16-3的规定。
表16-3 钢的牌号和化学成分
牌号 |
化学成分,% |
C |
Si |
Mn |
P |
S |
Als |
不大于 |
LT |
≤0.10 |
≤0.07 |
0.20~0.55 |
≤0.035 |
≤0.035 |
≥0.015 |
XT1
XT2 |
由供方选择,需方有要求时,可提供化学成分 |
②成品钢板和钢带的化学成分允许偏差应符合GB222的规定。
(2)交货状态:
冷轧钢板(带),经过热处理(再结晶退火)和平整后交货。除特殊要求外,一律涂油。冷轧热镀锌钢桶(带),经过热处理(再结晶退火)和表面处理后交货,除有特殊要求外,应钝化加涂油。
(3)力学性能和工艺性能
①冷轧板和镀锌板的力学性能应符合表16-4的规定。
表16-4 钢板力学性能指标
牌号 |
抗拉强度σb
(MPa |
伸长率δ
(%,不小于) |
LT |
295~410 |
≥30 |
XT1
XT2 |
295~450 |
≥27 |
②桶盖用钢板(带)的杯突试验应符合表5的规定。
表16-5 钢板的杯突试验指标(mm)
公称厚度 |
杯突试验冲压深度,不小于 |
冷轧板(带) |
镀锌板(带) |
1.0 |
10.1 |
9.0 |
1.2 |
10.6 |
9.4 |
1.5 |
11.2 |
9.9 |
④镀锌板(带)应做180°锌层弯曲试验,弯芯直径等于零,弯曲后距试样边部5mm以外不允许出现锌层脱落,但允许出现不露钢基的裂纹。
(4)镀锌板(带)的锌层重量应符合表16-6的规定。
表16-6 锌层重量
牌号 |
表面结构 |
锌层重量 |
三点试验平均值(双面),不小于 |
三点试验最小值 |
双面 |
单面 |
XT1 |
正常锌花 |
200 |
200 |
170 |
68 |
XT2 |
275 |
275 |
235 |
94 |
⑤表面质量
钢板(带)的表面不允许有裂纹、结疤、折叠、气泡、夹杂和其他影响使用的缺陷。钢板(带)不得有分层。允许有厚度公差一半范围内的下列缺陷:轻微的麻点、划痕、压痕和局部轻微氧化色。
冷轧热镀锌钢板(带)不得存在影响使用的缺陷,允许有小腐蚀点,轻微的条痕、划伤、压痕、小的锌粒、锌疤、宽度不大于20mm的轻微锌厚边及因原板锈点而形成的轻微麻点。
3.试验方法
(1)钢板(带)的尺寸测量方法应符合GB708的规定。
(2)钢板(带)的检验项目、取样数量和试验方法应符合表16-7的规定。
表16-7 钢板的检验项目、取样数量和试验方法
序号 |
检验项目 |
取样数量,个 |
取样方法 |
试验方法 |
1 |
化学分析 |
1(每炉罐号) |
GB 222 |
GB 223 |
2 |
拉伸试验 |
1 |
GB 2975 |
GB 6397,GB228,LT试样04,XT试样9 |
3 |
冷弯试验 |
1 |
GB 2975,试样宽度20mm |
GB 232 |
4 |
锌层重量 |
1 |
每个试样面积50cm2,距边缘等于50mm内侧在边、中、边三个部位取样 |
GB/T1839 |
5 |
锌层弯曲 |
1 |
GB2975,试样宽度20mm |
GB232 |
6 |
杯突试验 |
1 |
试样长度同板宽,试验在试样中心与边部三点进行 |
GB4156 |
4.检验规则
(1)钢板和钢带应成批验收。每批应由同一炉罐号、同一厚度、同一炉次或同一热处理规范的钢板或钢带组成,冷轧钢板(带)重量不得大于45t,冷轧热镀锌板(带)重量不得大于10t。
(2)用于检验的钢板应从板卷的头部或尾部切取。
(3)钢板的复验按GB247进行。
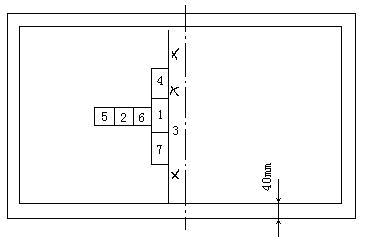
图16-1 材料形状尺寸检验
二、薄钢板的化学成分检验
对原材料的分析检验,是每一个钢桶制造企业都必须认真做的原材料入厂检验程序,它是保证产品质量的基础。钢材化学成分的分析检验一般采用化学分析法,化学分析是以化学反应为基础的分析方法,常用方法主要又可以分为以下两种:
重量分析法。通常是使用被测组分与试样中的其它组分分离后,转变为一种纯粹的、化学组成固定的化合物,称其重量,从而计算被测组分含量的一种分析方法。这种方法的分析速度较慢,但其准确度高,目前它是在钢材分析中仍用作标准方法。
滴定分析法。此法是用一种已知准确浓度的试剂溶液(即标准溶液),滴加到被测组分溶液中去,使之发生反应,根据反应恰好完全时所消耗标准溶液的体积计算出被测组分的含量。这样的分析方法称为滴定法,又称容量分析法。此法操作简单快速,测定结果的准确度比较高,有较大的实用价值。
下面介绍钢材中各成分的常用分析方法。
(一)碳的测定
1.燃烧-容积法。又称气体容量法,最目前测定碳应用最广泛的分析方法。将试样置于约1200℃的氧气流中燃烧,生成的CO2和过量的氧气经导管导入量气管,定容后将气体压入装有KOH溶液的吸收器中将CO2吸收,然后使剩余氧气返回量气管,根据前后体积之差即可计算钢中的碳含量。
试样在高温燃烧时,其中的硫也被氧化,生成的二氧化硫也能被氢氧化钾吸收,因此必须事先用特制的、组织疏松的二氧化锰把二氧化硫吸收将其去除。
2.非水滴定法。试样在高温下通氧燃烧生成CO2和SO2,首先导入硫吸收杯中,SO2被淀粉溶液吸收后生成亚硫酸消除干扰,未被吸收的CO2和O2导入含有百里酚酞指示剂的乙醇-乙醇胺-氢氧化钾混合液中被吸收。随后用碘酸钾溶碱性非水溶液(标准溶液)滴定,使之完全反应。根据标准溶液消耗的体积可计算出碳的百分含量。
(二)锰的测定
1.过硫酸铵容量法。试样溶解后,在酸性溶液中并有硝酸银存在的情况下,用过硫酸铵将锰氧化为七价锰(高锰酸),然后加入氯化钠溶液使银离子沉淀,再用亚砷酸钠-亚硝酸钠标准溶液滴定,据此测定钢中的锰含量。
2.三价锰容量法。试样溶解后,在加入大量磷酸的条件下,用固体硝酸铵将锰氧化为三价锰,然后以二苯胺磺酸钠为指示剂,用硫酸亚铁标准溶液滴定,据此测定钢中的锰含量。
(三)硅的测定
1.重量法。试样经酸溶解,用高氯酸蒸发冒烟,使硅酸脱水转变成难溶的硅酸凝胶,过滤洗净后将其灼烧成二氧化硅。用硫酸-氢氟酸处理,使硅生成四氟化硅挥发除去。根据除硅前后的重量差可计算出硅的百分含量。
2.硅氟酸钾滴定法。试样以酸及氢氟酸分解,使硅转化为硅氟酸,加入硝酸溶液时即生成硅氟酸钾沉淀,然后滤出并洗净沉淀物,用热水溶解使之水解而释放出氢氟酸,再用氢氧化钠标准溶液滴定其释放出的氢氟酸,由消耗氢氟化钠标准溶液的量计算硅的含量。
(四)硫的测定
1.燃烧碘量法。试样在高温下氧气流中燃烧,生成的二氧化硫随氧气流通入吸收器,被水吸收形成亚硫酸,再以淀粉作指示剂用碘标准溶液滴定,根据碘液的消耗量即可求得硫的含量。
2.重量法。将试样用硝酸或盐酸溶解,使硫转变成硫酸盐,往硫酸盐中加氯化钡使之生成硫酸钡沉淀物,然后将沉淀的硫酸钡过滤、灼烧、称重,以测定钢中的硫含量。
(五)磷的测定
碱容量法。将试样用酸分解使磷转变为正磷酸后,加钼酸铵使之生成磷钼酸铵沉淀物,过滤后将沉淀物用一定数量的氢氧化钠标准溶液溶解,然后用酸(硝酸)标准溶液回滴过剩的氢氧化钠溶液,根据所消耗的氢氧化钠标准溶液计算钢中的磷含量。
(六)铬的测定
过硫酸铵容量法。试样经硫磷混合酸分解,在硝酸银溶液中用过硫酸铵将铬氧化为六价,然后用硫酸亚铁标准溶液滴定,根据硫酸亚铁的消耗量即可求得铬含量。或者试样直接用高氯酸溶解并蒸发至冒烟将铬氧化,再用硫酸亚铁滴定。
(七)镍的测定
重量法。试样用盐酸溶解后,置于加酒石酸(或柠檬酸)和氢氧化铵的弱碱性溶液中,用丁二肟溶液使镍沉淀。经过滤、洗涤、烘干或灼烧成氧化镍后,进行称量,再计算镍的含量。
三、薄钢板的力学性能检验
1.抗拉强度
钢的强度是通过拉伸试验测定的。拉伸试验一般是在万能试验机上进行的。拉伸试验时,试样在负荷平稳增加下发生变形直至断裂。此时利用万能试验机上的自动绘图装置,可以绘出试样在拉伸过程中伸长与负荷之间的关系曲线。习惯上称此曲线为试样的拉伸图,即F-△L曲线。图16-2为低碳钢试样的拉伸图。
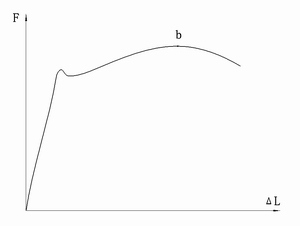
图16-2 低碳钢拉伸图
钢材试样在外力作用下发生的形状变化,称为变形。而恢复变形的能力则称为弹性。当外力去除之后,而恢复变形的能力则称为弹性。当外力去除之后,试样的变形即随之消失,而无残余变形,这种变形称为弹性变形。由拉伸图可知,弹性变形呈一直线段,这说明试样的伸长与外力的增加成正比关系。
当试样在试验过程中拉伸力不增加(保持恒定)时,仍能继续伸长时的应力称为屈服点。试样经过屈服阶段再除去负荷,部分变形不能恢复,这部分不能恢复的残余变形称为塑性变形。
试样屈服后,若要使其继续发生变形,则需增加外力以克服其中不断增长的抗力,这是因为材料在塑性变形过程中不断发生强化。在强化阶段中,试样的变形主要是塑性变形,其变形时要比弹性变形阶段的变形大得多,试样的变形仍是均匀的,但可以看到整个试样的横向尺寸有显著缩小。当外力继续增加到某一最大值(图16-2曲线b点对应的力)时,试样的局部面积缩小,产生了所谓“缩颈”现象,故载荷也逐渐降低,直到试样被拉断。
抗拉强度是指试样在拉断过程中最大力所对应的应力,即
(16-1)
式中:σb——抗拉强度;Fb——试样承受的最大力;S0——试样平行长度部分的原始横截面面积。
抗拉强度的测定,是在测定屈服点后,对试样继续加荷至拉断试样为止。从测力盘上读取最大力Fb。按照上式计算出抗拉强度值。
2.伸长率
伸长率是试样在一定应力下的标距增长量与原标距长度之比。标准意义上的伸长率是指断后伸长率,就是试样拉断后,标距的增长时与原始标距长度的百分比,即
(16-2)
式中:δ——断后伸长率; L1——试样拉断后的标距长度;L0——试样原始标距长度。
断后伸长率的测定,是将拉断后的试样断裂处紧密对接,尽量使其轴线位于一直线上,以测量断后长度。然后按上式计算出伸长率。
四、薄钢桶的工艺性能检验
标准规定的工艺性能检验是进行杯突试验。杯突试验就是用端部为球形的冲头,将夹紧的试样压入压模内,直至出现穿透裂缝为止,此时的杯突深度即为试验结果,以此来检验钢板的塑性变形性能。
1.试样要求:杯突试验用试样是从表面无缺陷的钢板上选取的。试样必须平整,不得扭曲,边缘无毛刺,不得进行冷热加工或锤击,应不经矫直进行试验。试样厚度为原材板厚,宽度或直径为90~95mm。
2.试验方法:杯突试验在杯突试验机上进行,试验部分见图16-3。
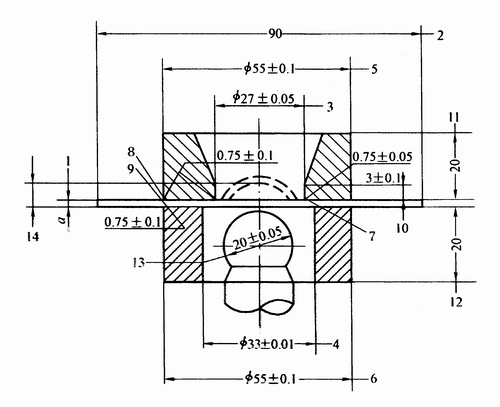
1—试样厚度;2—试样宽度或直径;3—压模孔径;4—垫模孔径; 5—压模外径;6—垫模外径;7—压模孔内侧圆角半径; 8—压模外侧圆角半径;9—垫模外侧圆角半径;10—压模孔深度; 11—压模厚度;12—垫模厚度;13—冲头球形部分直径;14—杯突深度
图16-3 杯突试验
试验就在10~35℃的温度下进行。若要求严格,则就在23±5℃下测试。
试验前,就应在试样两面和冲头上涂以一薄层石墨润滑脂或其类型的润滑脂。试样厚度的测量应精确到0.01mm。相邻两个压痕的中心距离不得小于90mm,任一压痕的中心至试样任一边缘的距离不得小于45mm。
试验时,把试验机调至零点后,将试样置于压模和垫模之间予以夹紧,夹紧力约为10kN。在无冲击的情况下进行杯突试验,试验速度控制在5~20mm/min。试验接近结束时,将速度降低到下限速度,以便正确地确定裂缝出现的瞬间。当裂缝开始穿透试样厚度(透光)时,试验即告终止。
试验过程中,冲头不得转动,冲头部分应与试样接触。
【返回目录】