《钢桶制造技术》
杨文亮 辛巧娟 编著
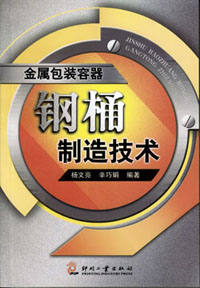
第十四章 钢桶的涂装工艺
第二节 涂装前表面预处理
要保证钢桶涂层经久耐用,符合使用要求,充分发挥涂料的保护和装饰作用,除涂料本身的质量外,其施工也是一个很重要的关键因素。钢桶的表面处理是涂装前的准备工作,表面处理关系着涂层的附着力和使用寿命,直接影响涂装质量,因此,这道工序应受到重视。
表面准备工序,主要是清除钢桶表面的油脂、锈蚀、有机物污物和尘土等,以改善钢桶表面状态。表面处理的目的,主要有以下三个方面:
1.增强涂膜对钢桶表面的附着力。钢桶表面上存在着尘埃、油垢、水、氧化层、铁锈或预卷喷上的胶等,会影响涂膜与钢桶表面的附着力。表面处理的目的,就是要除净这些杂质,使表面平整且有一定的粗糙度,以提高涂膜的附着力。
2.为涂膜的美观平整准备条件。钢桶表面的粗糙度,有时受到钢板上的污物影响,显得太粗糙而不够平整,表面处理可使钢桶表面平整。
3.增加表面抗腐蚀能力。钢桶表面有水汽存在时,形成微电池,它是钢桶腐蚀的主要因素,铁锈的比容积大,存在于涂膜和钢板之间,就会导致涂膜耐水性降低,使表面很快锈蚀。如果用表面处理的方法,去掉铁锈,就能提高耐水性。
涂装前表面处理的程序是:先除油,其次去锈,根据使用要求,还可以进行机械处理和化学处理。
一、钢桶表面的除油方法
脱除油脂主要是利用溶解、皂化、乳化作用将钢桶表面油污去掉。常用的除油方法如下。
1.有机溶剂除油
对于没有设备或生产批量小的企业,人工除油常用有机溶剂和人工擦拭相结合的办法除油。要求所用的溶剂溶解力强、不易着火、毒性小、便于操作、挥发性慢。实际上所用的溶剂很难完全符合以上要求。常用的溶剂有:汽油、石油溶剂、松节油、甲苯、二甲苯、二氯乙烷、三氯乙烷、四氯乙烷等。
操作时,人工用抹布蘸取有机溶剂,在钢桶表面进行擦拭,一般来说,经过两遍擦拭即可达到除油要求,待表面有机溶剂挥发掉后再进行涂装即可。
2.碱液除油
碱液除油主要借助碱的化学作用来清除钢桶表面的油脂及轻微锈蚀,达到表面净化的目的。碱液的组成有氢氧化钠、碳酸钠、磷酸三钠、碳酸钾、硅酸钠(水玻璃)、肥皂等。在这些组分中氢氧化钠起皂化作用、洗涤清理作用,磷酸三钠起软化水的作用,碳酸钠主要是起调节pH值作用,硅酸钠加强润湿和乳化作用等。
这种方法在国内制桶行业中应用广泛。碱液除油在施工中有两种方法,一是将钢桶浸入碱液中除油,二是采用喷淋的方法除油。后者应用较多,效果也较好,适合于大批量流水线生产。
3.乳化除油
乳化除油是利用能促使两种互不相溶的液体(如水和油),形成稳定乳浊液的物质(乳化剂),来除去钢桶表面上的油脂及其它污物,达到除油的目的。它能在室温下进行,温度对其清洗效果影响不大,除油比碱液除油效率高,它可使油脂在乳化剂中被溶解除掉,水溶性的污物则在水中得到溶解被清除。
乳化除油可采用喷淋或浸渍的方式进行。一般以喷淋的方式除油效果较好,但浸渍式较简单,各有所长。
二、钢桶表面的除锈方法
1.机械处理法
机械处理法较为简单,最古老的方法是手工处理,即利用钢刷、砂布、砂纸、布等工具手工除锈,工作效率极低,质量也不好。另一种方法是用擦桶机进行擦桶,效果较好。如图14-1和图14-2所示为钢桶内外表面擦桶机示意图。
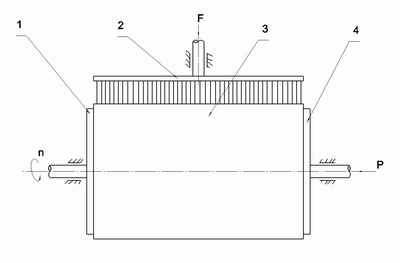
1—转盘;2—钢刷、布刷;3—钢桶;4—压盘
图14-1 外表面擦桶机
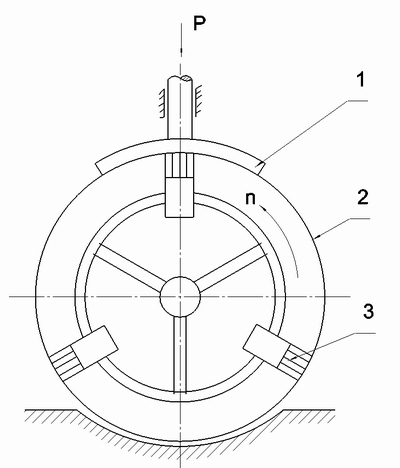
1—压盘;2—钢桶;3—钢刷
图14-2 内表面擦桶机
外表面擦桶机由转盘、压盘、钢刷、布刷等组成。钢桶由转盘和压盘夹紧,并随着转盘转动,两排刷紧贴在钢桶表面进行擦桶。
内表面擦桶机由压盘和钢刷等组成,内转子三排钢刷,随着离心力的作用与钢桶内壁压紧,钢桶由压盘紧压于底座上不动,钢刷转动刷桶。
对于锈蚀太严重的钢桶表面,最好采用喷砂、抛丸等方法较为理想,对于旧漆清除,这种方法也是最理想的。
2.化学除锈
化学除锈的原理是:金属的锈蚀产物主要是金属的氧化皮,化学除锈就是用酸溶液与这些金属氧化物发生化学反应,使其溶解在酸溶液中。另外,酸与金属作用产生氢气,使氧化皮机械地剥落。
在工厂里除锈习惯上叫酸洗,酸洗的方式目前广泛应用的是浸渍酸洗和喷淋酸洗。一般当金属经脱脂处理后,再进行酸洗除锈,接着用水洗净,再以碱液进行中和处理,其工艺一般是:酸洗除锈→冷水冲洗→热水冲洗→中和处理→冷水冲洗→热水冲洗(或继之进行磷化处理)。
三、磷化处理
磷化是指钢桶表面经含有锌、锰、铬、铁等磷酸二氢盐的酸性溶液处理后发生化学反应,在金属表面形成一层主要成分为不溶于水的稳定的磷酸盐保护膜的过程。
1.磷化的作用
(1)提高耐蚀性:磷化膜是一层不导电的隔离层,使金属表面由原来的优良导体变成不良导体,抑制金属表面微电池的形成,有效阻止涂膜的腐蚀。
(2)提高附着力:磷化处理能使基体与涂层间的附着力大大提高。这是因为磷化膜与金属可形成紧密结合的整个结构,其间没有明显分界面,而且磷化膜具有多孔性,涂料可以渗透到其孔隙中互相渗透,形成“抛锚效应”紧密结合,提高了附着力。
(3)提供洁净的表面:由于磷化膜只能在无油污、无锈层的洁净金属表面上形成,所以磷化处理后的金属表面是清洁、均匀、无油、无锈的。
(4)可改善金属材料的冷加工性能:经磷化处理后的金属更易进行冷加工。
(5)改进表面摩擦性能:磷化后的金属表面平整平滑度提高,易于滑动。
因此目前钢桶涂装,几乎100%采用涂装前磷化处理,磷化处理是钢桶涂装前处理工艺中不可缺少的重要环节。
2.磷化处理工艺
磷化工艺可采用浸渍、喷淋、涂刷等几种方法。在钢桶生产中,最常用的方法是喷淋法。喷淋法是用泵将磷化液加压,并以0.1~0.2MPa压力将磷化液喷成雾状喷淋在钢桶表面,只需经1~2min处理即可达到磷化目的。利用喷射的冲击力与磷化时的化学作用相结合,使磷化速度提高,喷淋液浓度较低,形成的膜层结晶细密、均匀。
四、钝化处理
金属表面在完成除油、除锈等表面处理后,往往容易重新生锈。 为了防止发生返锈,通常要进行化学处理,使金属表面形成一层保护膜。钝化处理就是其中一种方法,形成的钝化膜不活,因此有增强防锈的功能。另外,钝化也常是磷化处理工艺中的后处理工序。把金属与铬盐作用生成三价铬离子(Cr3+)与六价铬离子(Cr6+)组成的铬化层的过程称为钝化。
长期以来,钝化剂使用的主要成分是铬酸盐,由于它存在毒性大、污染环境的缺点,使用受到限制。含铬污水在排放前需经严格治理。目前使用的大多是低含铬量的钝化液配方,并配合严格的废水治理措施。
五、钢桶表面综合处理法
1.综合除油除锈处理(配方见表14-1)
这种方法的特点是,乳化除油和酸洗除锈相互促进,酸洗产生的氢气促进乳化剂的乳化作用,将氧化皮或锈表面的油污去掉,便于酸与铁锈产生接触,因此时间快、效果好、能简化工艺、减轻劳动强度。
2.综合防锈处理(配方见表14-1)
这种处理法具有较高的防锈能力,一般四小时内可保持不生锈,即使用水冲洗干净,也有较好的防锈能力。适用于钢桶处理后不能及时烘干或涂漆的情况,钢桶短时间隔置不会重新起锈。
3.除油、除锈、钝化“三合一”处理(配方见表14-1)
这种处理方法可同时达到除油、除锈、钝化的要求。但钢桶表面带有氧化皮和严重的锈斑时,此法不太适宜,用这种方法处理后,经热水冲洗,烘干后即可涂漆。
表14-1 综合处理配方表
处理液功能 |
处理液组分 |
含量(g/L) |
综合除油除锈修理 |
硫酸 |
15~25份 |
若丁 |
0.06~0.1份 |
平平加或OP缓蚀剂 |
0.6份 |
烷基苯磺酸钠 |
0.6份 |
水 |
100份 |
综合防锈处理 |
磷酸氢二钠 |
4份 |
亚硝酸钠 |
7份 |
碳酸氢钠 |
1.2份 |
甘油 |
1.8份 |
水 |
100份 |
除油、除锈、钝化“三合一”处理 |
磷酸 |
50~300g/L |
硫脲 |
3~5g/L |
M-7有机硅酸盐溶液 |
0.1g/L |
OP-7乳化剂 |
3~5g/L |
处理条件:槽液温度85℃以上。处理时间:2~3分钟。 |
4.除油、酸洗、磷化、钝化“四合一”处理
四步工序一步完成,大大减少设备和作业面积,可提高效率,降低成本,但质量控制技术要求较高,两种比较成熟、在生产中使用已取得较好处理效果的配方见表14-2。
表14-2 “四合一”处理液配方
序号 |
组分名称 |
使用量
(g/L) |
处理条件 |
处理方式 |
温度(℃) |
时间(min) |
1 |
相对密度1.66的磷酸(80%) |
110~180ml/L |
40~60 |
10~15(浸渍)
1~2(喷射) |
浸渍或喷射 |
氧化锌 |
30~50 |
硝酸锌 |
150~170 |
氯化镁 |
15~30 |
钼酸铵 |
0.8~1.2 |
烷基苯磺酸钠 |
20~40ml/L |
酒石酸 |
5~10 |
重铬酸钾 |
0.2~0.4 |
水 |
余量 |
2 |
磷酸二氢锌 |
50~70 |
50~70 |
10~20(浸渍)
1~2(喷射) |
浸渍或喷射 |
硝酸锌 |
100~140 |
亚硝酸钠 |
0.1~1 |
硝酸钙 |
0.2~1 |
酒石酸 |
5~8 |
烷基苯磺酸钠 |
5~15 |
重铬酸钾 |
0.3~0.5 |
水 |
余量 |
六、表面处理常见缺陷及改善措施
目前国内大多数钢桶生产企业采用的原材料钢板是冷轧薄钢板,对于冷轧薄钢板,表面处理主要是除油和磷化,其它处理表面处理根据材料和需求的具体情况酌量取舍。
1.除油中常见的问题及解决方法(见表14-3)
表14-3除油中常见的问题及解决方法
问题 |
出现原因 |
解决方法 |
除油效果不佳 |
脱脂剂选择不当 |
根据油污的具体情况合理选择脱脂剂。 |
脱脂工艺选择不当 |
可采用二次脱脂工艺。可多级脱脂,多级清洗 |
表面油污过厚,脱脂不均匀 |
一般要先进行手工预擦洗,先除去钢板上严重的油污、灰尘、泥沙等 |
除油时间过短 |
延长除油时间 |
除油温度偏低 |
提高除油温度 |
脱脂剂浓度偏低 |
按照使用要求提高浓度至工艺范围 |
机械作用不够 |
提高喷射压力 |
喷嘴堵塞,流量不足 |
定期清理喷嘴 |
工作液中含油量太高 |
定期更换槽液,采用二槽或多槽清洗 |
脱脂后水洗不彻底 |
加强水洗,水洗水要连续溢流 |
工作液泡沫高 |
温度过低 |
提高温度至规定范围 |
循环泵密封处磨损而进空气 |
更换泵的密封材料,最好选用立式泵 |
脱脂剂选择不当 |
更换脱脂剂,选用低泡或无泡型新型脱脂剂 |
喷射压力过高 |
降低喷射压力,调整喷嘴位置等 |
没采用消泡工艺 |
采用消泡剂,如醇类、硅油类、聚醚类等 |
水洗槽泡沫过多 |
水洗槽溢流量太小 |
加大溢流水量 |
循环泵密封处磨损而进空气 |
更换泵的密封材料,最好选用立式泵 |
槽液使用时间长 |
定期更换槽液 |
水洗槽碱度过高 |
碱槽向水洗槽窜溶液 |
改造设备,避免窜液 |
钢桶带太多的碱液进入水洗槽 |
改变夹持形式,延长滴液时间 |
水洗槽的溢流量太小 |
加大溢流量 |
槽液使用时间长 |
定期更换槽液 |
钢桶水洗后生锈 |
工序间隔时间过长 |
工序间增加喷湿 |
钢桶在水洗段时间过长 |
零件不允许在此长时间停留,加缓蚀剂。 |
2.磷化常见弊病及解决措施(见表14-4)
表14-4磷化常见弊病及解决措施
故障现象 |
产生原因 |
解决措施 |
磷化膜结晶粗糙、多孔 |
游离酸度过高 |
降低游离酸度 |
磷化液中氧化剂不足 |
增加氧化剂比重 |
亚铁离子含量过高 |
加双氧水调整 |
钢桶表面有残酸 |
加强中和及水洗 |
钢桶表面过腐蚀 |
控制酸洗液浓度和酸洗时间 |
膜层过薄,无明显结晶 |
总酸度过高 |
加水稀释 |
钢桶表面有硬化层 |
用强酸侵蚀或喷砂处理 |
亚铁离子含量过低 |
补加磷酸二氢铁 |
温度低 |
提高槽液温度 |
钢桶表面黏附白色粉状沉淀 |
游离酸度低,游离磷酸量少 |
补充磷酸二氢锌,在特殊情况下,可加磷酸调整游离酸度 |
含铁离子少 |
磷化液中应留一定量的沉淀物,新配溶液与老溶液混合使用 |
钢桶表面氧化物未除净 |
加强酸洗,充分水洗 |
溶液氧化剂过量,总酸度过高 |
停加氧化剂,调整酸比 |
槽内沉淀物过多 |
清除过多的沉淀物 |
磷化膜不均匀、发花或有斑点 |
除油不干净 |
加强除油、清洗 |
温度过低 |
提高槽液温度 |
钢桶表面钝化 |
加强酸洗 |
酸比失调 |
将酸比调整到工艺范围 |
磷化膜不易形成 |
钢桶表面有硬化层 |
改进加工方法,除去硬化层 |
溶液中硫酸根过高 |
用钡盐处理,使其降至工艺规范要求 |
溶液中混入杂质 |
更换磷化液 |
五氧化二磷含量过低 |
补充磷酸盐 |
磷化膜耐蚀性差与生锈 |
磷化膜晶粒过粗或过细 |
调整酸比 |
游离酸含量过高 |
降低游离酸,可加氧化锌或氢氧化锌 |
钢桶表面过腐蚀 |
控制酸洗过程 |
溶液中磷酸盐含量不足 |
补充磷酸二氢盐 |
钢桶表面有残酸 |
加强中和与水洗 |
磷化膜发红,耐蚀力下降 |
酸洗液中杂质附在金属有面上 |
加强酸洗质量控制 |
铜离子混入磷化液 |
用铁屑置换除去或用硫化物处理,使之沉淀去除,调整酸度 |
磷化溶液发黑 |
槽液温度低于规定温度 |
停止磷化,升高槽液温度至沸点,保持1~2h,并空气搅拌,直至恢复原色 |
溶液中亚铁离子过高 |
加氧化剂如双氧水、高锰酸钾 |
总酸度过低 |
补充硝酸锌等,提高总酸度 |
【返回目录】