《钢桶制造技术》
杨文亮 辛巧娟 编著
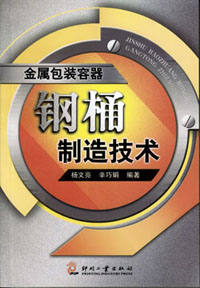
第十二章 钢桶封闭器制造工艺
第二节 封闭箍式封闭器
随着工业的发展,在化工、食品行业使用的包装桶类型中,全开口钢桶、开口缩颈钢桶、开口锥形桶等也得到了广泛的应用。这类钢桶有一个共同的特点,它们都是开口桶,桶顶即是桶盖,其桶盖的固定方式均采用封闭箍式的封闭器。如图13-13为封闭箍式封闭器的装配图。
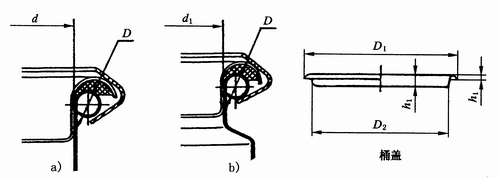
a)直开口钢桶;b)开口缩颈钢桶
图12-13 封闭箍式封闭器装配示意图
一、封闭箍式封闭器的结构及尺寸要求
封闭箍式封闭器分螺杆型封闭器和杠杆型封闭器两种。
1.螺杆型封闭器
封闭箍式螺杆型封闭器由封闭箍、紧耳、螺栓、螺母组成,其结构如图12-14所示,尺寸要求见表12-6。
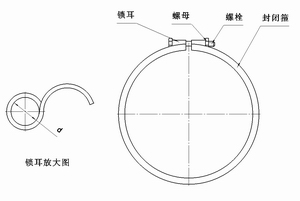
图12-14 封闭箍式螺杆型封闭器结构图
表12-6 螺杆型封闭器尺寸(mm)
d |
螺栓 |
钢板厚度 |
适用范围 |
12.0 |
M10 |
1.5~2.0 |
200L~100L |
10.0 |
M8 |
1.2~1.5 |
80L~45L |
8.0 |
M6 |
1.2~1.5 |
<45L |
2.封闭箍式杠杆型封闭器
封闭箍式杠杆型封闭器结构及尺寸如图13-15所示,零件构成见表12-7及表12-8(对照图4-8)。
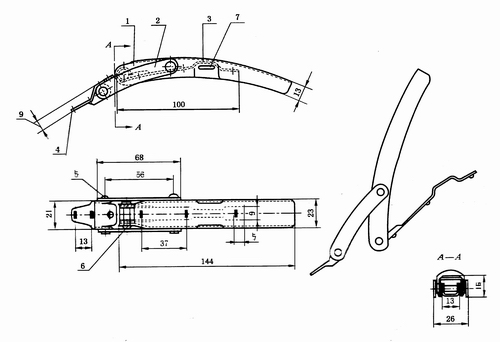
图12-15 封闭箍式杠杆型封闭器结构图
表12-7 杠杆型封闭器构成表1(mm)
件号 |
名称 |
件数 |
规格 |
1 |
拉手 |
1 |
钢板厚度1.5 |
2 |
连接片 |
2 |
钢板厚度1.5 |
3 |
接头 |
1 |
钢板厚度1.5 |
4 |
接头 |
1 |
钢板厚度1.5 |
5 |
扁圆头铆钉 |
2 |
φ4×28 |
6 |
扁圆头铆钉 |
2 |
φ4×22 |
7 |
安全板 |
1 |
钢板厚度0.5 |
表12-8 杠杆型封闭器构成表2(mm)(对照图4-8)
件号 |
名称 |
件数 |
规格 |
1 |
拉手 |
1 |
钢板厚度1.5~1.2 |
2 |
连接片 |
2 |
钢板厚度1.5~1.2 |
3 |
扁圆头铆钉 |
2 |
φ4×22 |
4 |
扁圆头铆钉 |
2 |
φ4×28 |
5 |
安全板 |
1 |
钢板厚度0.5 |
二、封闭箍的成形特征及原理
如图12-16为封闭箍零件产品图。它的成形原理是板料的滚压成形原理。
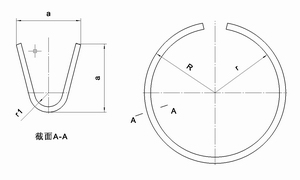
图12-16 封闭箍零件图
桶箍的滚压成形是将带钢,送进于前后直排的数组成形辊轮中通过,随着辊轮的回转,在将带料向前送进的同时,又顺次进行弯曲加工,以成形出所需断面形状的加工方法。在最后一对辊轮的前方(即成形件出来的位置),放置一只卷圆辊轮,挡住了成形后带料前进的去路,随着卷圆辊轮的旋转拨动,成形带料转向上走,于是圆环形的桶箍便成形了、这最后卷圆的原理与前面介绍的桶身卷圆原理相同,这里不再琐述。
封闭箍滚压成形的原理,就像图12-17所示的那样是由各组成形辊轮顺次弯曲并向前送进的滚压成形,如果就第二组辊轮成形为例来看,就是图12-18那样。板料从辊轮的入口处1进入,一面受到弯曲,一面向前运动,在辊轮的中心面4处,即成形定毕,并从上下辊轮中穿出来。
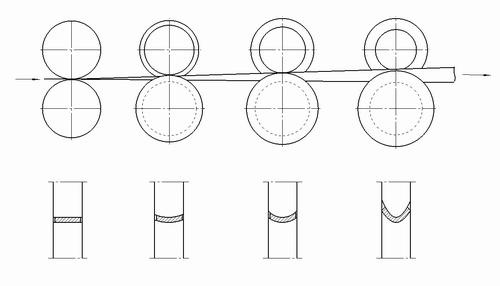
图12-17 封闭箍的滚压成形原理
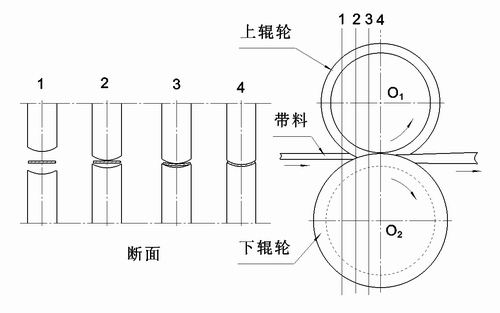
图12-18 封闭箍滚压成形过程
三、封闭箍滚成形工艺
1.滚压成形机
封闭箍的滚压成形工序,是在封闭箍成形机上进行的。滚压成形机有两类:一类为悬臂式(开式),辊轮主轴为单边支承,是薄壁小断面封闭箍成形的设备;另一类为闭式,主轴为双边支承,是厚壁大断面封闭箍成形的设备。钢桶封闭箍成形多采用开式成形机。
作为成形设备设计和使用的基本出发点,与变形力呈函数关系的辊轮主轴直径被认为是强度和尺寸的基本因素,主轴与板厚之间具有正比关系。主轴的驱动方式有上下等速驱动、变速驱动和下轴驱动等,在辊轮的槽型设计中要注意摩擦损失。为减少辊轮和板材之间的摩擦,可利用水溶性油辊合液(2~10%)作为冷却润滑剂。
作为滚压成形的辅助加工装置,常把导向、滑槽、托辊、矫正、剪切等机构结合起来,使其联动,实现自动化生产。
如图12-19所示为常用封闭箍成形机示意图。它的工作过程是:
带料从滑槽1中送进,能使带料位置不致偏斜和歪移;然后通过A、B、C三道辊轮的滚压,已形成所需零件的断面形状。当带料从C辊出来后遇着卷圆辊D,使带料转向上弯,由导向轨5导向卷圆成形。滑槽1是可以调节宽度的长槽,可适用于不同宽度带料的定位需要;手轮2、3、4可调节对辊A、B、C上下辊之间的间隙,使之适用于不同厚度的带料;手轮6可调节卷圆辊D与对辊C的距离,以实现不同直径的封闭箍。在封闭箍直径变化的同时,导向轨5也可改变。
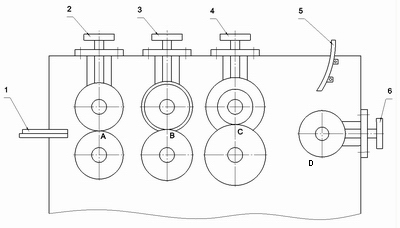
1—定位滑槽;2—A辊调节手轮;3—B辊调节手轮; 4—C辊调节手轮;5—导向装置;6—D辊调节手轮
图12-19 封闭箍滚压成形机示意图
2.封闭箍成形工艺及辊轮设计
(1)封闭箍形状:考虑所需形状的时候,首先要避免封闭箍形状出现太深的沟槽,对于弯曲半径,要考虑材质的弯曲性能,避免急剧过渡的尖角,死尖角成形是难以达到精度要求的。这些都是首要的基本条件。
(2)封闭箍断面形状的展开:进行工艺设计时,要考虑所需断面的形状,接着,绘制把封闭箍逐渐展开直至回复到平板料的展开草图进行研究分析。这种方法,不论是对于形状简单的断面还是复杂的断面都是有效的研究方法,进而就可以从整体上去考查从一个辊轮槽型移至下一个辊轮槽型的时候,高度方向和宽度方向的弯曲加工有无不合理的地方。
(3)封闭箍成形直边角度:成形材料的最大高度是基于以直线关系向上增加为出发点,其设计方法为控制成形直边角度使之合理化。对于一般低碳钢材料采用3°左右即可,但边缘部分的延伸过大恐怕就有发生边缘波纹的危险。
(4)滚压成形导向线:为使板料从平板状态向前移动直至成形出所需断面形状,就需要有水平导向线和垂直导向线。水平导向线从第一组辊轮开始到最后一组辊轮为止,始终保持在同一水平面上,为确定成形辊轮的节圆直径的基准。垂直导向线垂直于辊轮轴线,是从第一组辊轮至最后一组辊轮使得在此导向线两侧的成形加工量都是均等的一条基准线,在对称断面中,此导向线与断面中心线一致。
(5)辊轮的节圆直径:上下辊轮一致的直径是辊轮的节圆直径,也称槽型线,在节圆上可以无滑移地送进成形材料,在此点以外的辊径上,辊轮和材料之间就要发生滑移。将辊轮节圆直径选在成形辊轮槽型的哪一点上是一个重要的问题。从理想的角度出发,最好是选在辊轮受力最大的点上,但是这些点在每一组成形辊轮上是变化的。在这里,如考虑设计使通过第一组辊轮直至最后一组辊轮的水平导向线和辊轮节圆直径相一致,那么,在各辊轮中,使节圆直径与断面形状的底面或者与断面高度的中心相重合就方便了。节圆直径的长度要在每一槽型中增加0.5~1.0%左右,朝着最后一组辊轮方向对材料给以拉伸作用以防止弯曲和扭转。
(6)辊轮的组数:辊轮组数的确定是一个困难的问题,但是对于简单断面形状的成形,一般辊轮组数可由下式确定:
(12-1)
式中:n——辊轮的组数;α——成形直边的上升角度;d——辊轮工位间距;L——成形机全长;h——封闭箍成形截面深度。
(7)带料宽度的计算:与模具弯曲的情况一样,滚压成形的带料宽度按等于弯曲中性线的长度来计算。在急剧弯曲的部位,必须注意到中性线向受到压缩的侧面,亦即是弯曲的内侧转移这一现象。如果取中性线的长度为L1,弯曲角度为α,内侧弯曲半径为R,板料厚度为t,从弯曲内侧到中性线的距离为kt,则
(12-2)
中性线在板厚的1/2处时(弯曲半径大的情况),k=0.5,但是随着出现急剧弯曲,k即变为0.4~0.3。
(8)辊轮槽型的间隙:在滚压成形中,板厚不会出现变厚的现象,对于弯曲部分,由于材料变薄,因此就可以取间隙等于材料厚度。由于除去辊轮节圆直径之外,原则都要发生位移,所以对于节圆直径以外的点,倒是取得较板厚大一些更为安全。此外,对于最后一组辊轮槽型以后的各中间槽型最好是把间隙取得大一些。
(9)防止回弹:为了克服回弹而采用的过弯法,以及对正在精整辊轮槽型中的封闭箍制件,从四周向槽型作强制加压的方法,对于限制滚压成形件的回弹都是行之有效的。
(10)防止表面伤痕:滚压成形中,如果板坯放置在辊轮肩部半径处,那么,由于辊轮回转的滑移作用,就要在纵向表面上产生连续的表面伤痕。为了防止这种缺陷,要把槽型做成宽阔的,这时将板料放进槽型的倾斜面成形,或者由侧辊轮从横向挤压都是有效的。
(11)辊轮的材料:将碳素工具钢,特殊工具钢等材料淬火至洛氏硬度60左右即可作为辊轮使用。大尺寸的滚轮用特殊铸钢,对于软材料的滚压成形也有用铸铁作辊轮的。镀铬辊轮和硬度青钢辊轮可以防止产生表面伤痕。
【返回目录】