《钢桶制造技术》
杨文亮 辛巧娟 编著
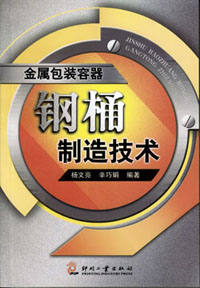
第十二章 钢桶封闭器制造工艺
封闭器是指加在容器上的一套封闭装置,其目的是使内装物保持在容器里和防止内装物受污染。钢桶封闭器按结构型式分为四类,见表4-1所示。
钢桶封闭器的类型虽然很多,但无论哪种封闭器,其使用目的就是密封桶口,制造方法也大多为压力加工方式,还有一些用到金属切削加工方法。这里,我们介绍最常用的几种钢桶封闭器的制造工艺。
第一节 螺旋式旋塞型封闭器
如图4-3所示为螺旋式旋塞型封闭器装配结构图。螺旋式旋塞型封闭器的装配型式为内平式,由桶塞、螺圈、垫圈、衬圈、封盖组成,其中封盖也可不设置。
一、旋塞型封闭器的结构及尺寸要求
1.典型的挤压桶塞结构见图12-1,尺寸要求见表12-1。
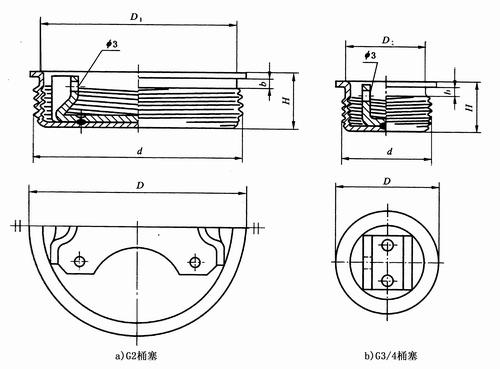
图12-1 挤压桶塞结构图
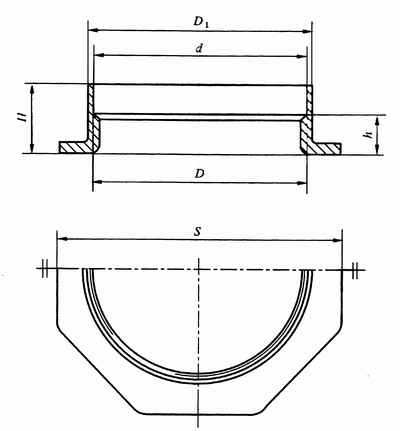
图12-2 螺圈结构图
表12-1 挤压桶塞尺寸(mm)
名称代号 |
D |
D1 |
H |
b |
d |
G2桶塞 |
61.2±0.3 |
56.0±0.3 |
15.4±0.3 |
3.0±0.3 |
G2 |
G3/4桶塞 |
28.2±0.3 |
22.9±0.3 |
13.6±0.3 |
3.0±0.3 |
G3/4 |
G4-1/2桶塞 |
127.0±0.3 |
- |
18.0±0.3 |
4.0±0.3 |
G4-1/2 |
注:螺纹尺寸G2、H3/4和G4-1/2见表13-5。 |
2.螺圈结构见图12-2,尺寸要求见表12-2。
表12-2 螺圈尺寸(mm)
名称代号 |
D1 |
d |
H |
h |
S |
D |
G2螺圈 |
62.3±0.2 |
60.4±0.2 |
18.8±0.3 |
10.5±0.4 |
77.8±0.2 |
G2 |
G3/4螺圈 |
29.0±0.2 |
27.2±0.2 |
15.8±0.3 |
8.6±0.4 |
43.7±0.2 |
G3/4 |
G4-1/2螺圈 |
123.6±0.2 |
121.4±0.2 |
20±0.3 |
10±0.4 |
141±0.2 |
G4-1/2 |
注:螺纹尺寸G2、H3/4和G4-1/2见表13-5。 |
3.垫圈、衬圈分为橡胶材料的矩形圈和O形圈,其结构如图12-3,尺寸要求如图12-3。
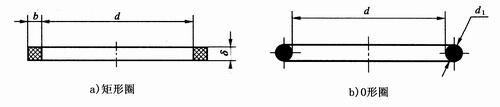
图12-3 垫圈、衬圈结构图
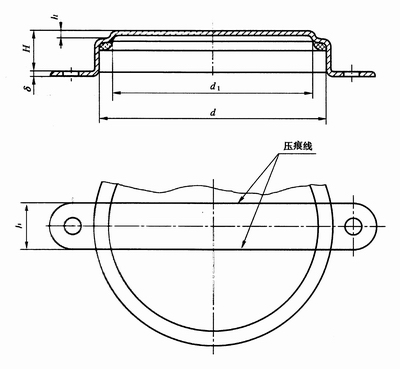
图12-4 封盖结构图
表12-3 垫圈、衬圈尺寸(mm)
名称代号 |
内径
d |
矩形圈 |
O形圈 |
δ |
b |
d1 |
G2垫圈 |
50.0±0.5 |
2.6±0.2 |
2.7±0.2 |
3.0±0.2 |
G3/4垫圈 |
20.0±0.5 |
2.6±0.2 |
2.7±0.2 |
3.0±0.2 |
G2衬圈 |
60.5±0.5 |
2.7±0.2 |
3.2±0.2 |
3.3±0.2 |
G3/4衬圈 |
27.5±0.5 |
2.7±0.2 |
2.4±0.2 |
3.3±0.2 |
4.封盖结构见图12-4,尺寸要求见表12-4。
表12-4 封盖尺寸(mm)
名称代号 |
d |
d1 |
H |
h |
δ |
G2封盖 |
69.4 |
63.0 |
11.0 |
2.5 |
0.28 |
G3/4封盖 |
34.7 |
30.0 |
9.0 |
1.5 |
0.28 |
5.旋塞型封闭器螺纹为G桶用管螺纹要尺寸要求,见表12-5。
表12-5 G桶用管螺纹尺寸(mm)
名称 |
代
号 |
25.4mm牙数 |
螺距 |
牙型角 |
大径 |
中径 |
小径 |
基本尺寸 |
上偏差 |
下偏差 |
基本尺寸 |
上偏差 |
下偏差 |
基本尺寸 |
上偏差 |
下偏差 |
桶塞 |
G2 |
11 |
2.309 |
55° |
59.62 |
-0.62 |
-1.12 |
58.14 |
-0.40 |
-0.76 |
56.66 |
-0.40 |
- |
螺圈 |
59.62 |
- |
0 |
58.14 |
+0.37 |
0 |
56.66 |
+0.94 |
+0.44 |
桶塞 |
G3/4 |
14 |
1.814 |
55° |
26.44 |
-0.44 |
-0.94 |
25.28 |
-0.38 |
-0.65 |
24.12 |
-0.38 |
- |
螺圈 |
26.44 |
- |
0 |
25.28 |
+0.26 |
0 |
24.12 |
+0.58 |
+0.08 |
桶塞 |
G4-1/2 |
11 |
2.309 |
55° |
121.26 |
-0.80 |
-1.65 |
119.78 |
-0.70 |
-1.55 |
118.3 |
-0.52 |
- |
螺圈 |
121.26 |
- |
0 |
119.78 |
+0.35 |
0 |
118.3 |
+0.94 |
+0.44 |
二、旋塞型封闭器制造工艺
1.螺圈制造工艺
螺圈生产工艺过程如下:
(1)下料:一般采用带钢,也可将大块料剪成条料,要求下料后的钢带平整光滑,无缺陷。材料选用2.5~3mm厚冷轧带钢,材料凹凸不平、压痕等缺陷的深度或高度不大于0.15mm,要求平整光滑无锈迹。
(2)落料拉深:可在压力机上进行。图12-5为落料拉深工序图。工序要求保证工艺尺寸:拉深深度H、直径D1及外缘直径D2。拉深要均匀、无毛刺、无缺口、无裂缝。
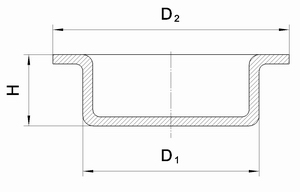
图12-5 螺圈落料拉深工序图
(3)整形冲孔:如图12-6为螺圈整形冲孔工序图,该工序可在压力机上进行,要求保证尺寸:高度H、直径D1,形状要求 D1圆柱与M平面的垂直度,其误差不超过0.15mm,并要求整形后无拉伤等现象。
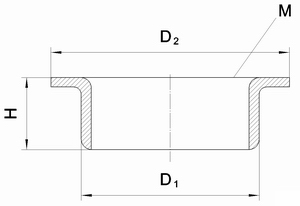
图12-6 螺圈整形冲孔工序图
(4)八方切边:如图12-7为八方切边工序图。该工序可在压力机上进行,工序要求保证八方对边尺寸S,以及直径D1的圆柱与直径D2圆(八方外接圆)的同轴度小于0.1mm。要求八方各边均匀、无毛刺。
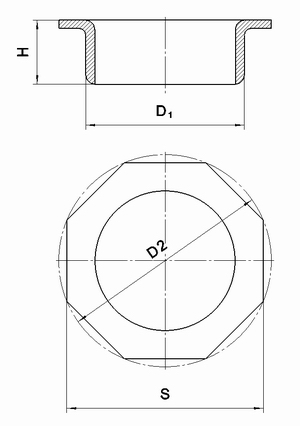
图12-7 螺圈八方切边工序图
(5)螺圈扩孔:如图12-8为螺圈扩孔工序简图,该工序应在扩孔机上进行,也可以在车床上加工。工序要求扩孔直径d1、深度h1、高度H,直径d1圆柱与直径D1圆柱的不同轴度不大于0.10mm,壁厚均匀,d1内孔粗糙度要不低于6.3,无毛刺。
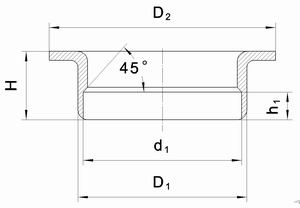
图12-8 螺圈扩孔工序简图
(6)螺圈攻丝:如图12-2所示,为螺圈攻丝工序完成后的产品简图。该工序应在攻丝机上进行。工序要求螺纹中径、螺纹内径、螺距、螺纹角尺寸符合工艺要求(表13-5所示),螺纹光滑完整,不能有破牙、歪斜等缺陷,螺纹整牙数不应少于三个。
2.挤压桶塞制造工艺
挤压桶塞生产工艺过程如下:
(1)下料:材料采用1.0~1.5mm厚带钢,要求凹凸不平、压痕等缺陷的深度或高度不大于带钢厚度,带钢厚度偏差-0.09mm,无锈迹。也可以采用板料裁剪,下料应在剪板机上进行,先将板料裁成条料备用,要求剪成的钢带平整,无缺陷。
(2)落料拉深:如图12-9所示为桶塞落料拉深工序简图。该工序可在压力机上进行,工艺要求保证各尺寸满足工艺要求,严格控制拉深直径D1和拉深高度H;无毛刺、无拉伤、无裂纹,圆周边宽均匀,其不圆度为0.1。
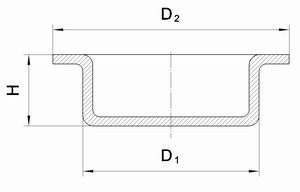
图12-9 螺塞落料拉深工序简图
(3)压周边圆弧:如图12-10所示,在螺塞上压周边圆弧,能够使封闭器装配时,螺圈与螺塞在垫圈处结合更为紧密,螺塞与螺圈拧紧时,不会将垫圈挤出,有利于桶口的密封。
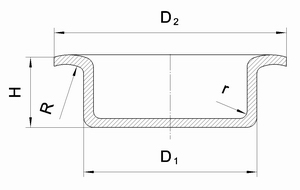
图12-10 螺塞压周边圆弧工序简图
该工序可在压力机上进行,工艺要求高度H和直径D1,以及圆角r满足工艺要求。制件无毛刺、无裂纹。保证周边圆弧R,圆弧周边无明显压痕和扭曲现象。
(4)螺塞滚丝:如图12-1为螺塞滚丝工序完成后的产品图。该工序在滚丝机上进行。工艺要求滚丝后螺纹外径尺寸、螺距螺纹角、螺纹中径、小径尺寸均应满足表12-5的规定。螺纹光滑完整,不得有破牙或歪斜等缺陷,螺纹不少于三个整牙。
(5)板扣凸焊:将制造好的螺塞板扣与螺塞进行凸焊装配。该工序可在凸焊机或点焊机上进行。焊接工艺参照第八章介绍。
3.螺塞板扣制造工艺
为了螺塞的装卸方便,要求在在螺塞上点焊一个板扣,如图12-1所示,螺塞中间部分的零件即为板扣。板扣的形状比较复杂,需要多道冲压工序来完成,在前面我们已专门介绍过冲压工艺方法,这里我们只做简单介绍。
(1)G2螺塞板扣制造工艺流程简介:
落料→压形→折弯压点→钻孔。
图12-11为G2螺塞板扣结构简图。
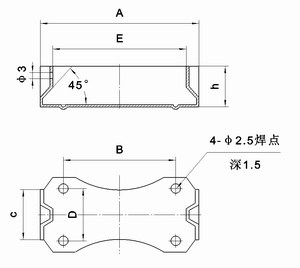
图12-11 G2螺塞板扣结构简图
(2)G3/4螺塞板扣制造工艺流程简介:
落料→冲孔——压点→折弯。
图12-12为G3/4螺塞板扣结构简图。
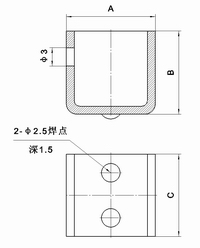
图12-12 G3/4螺塞板扣结构简图
就一般情况来说,以上工艺方法是成功的,由于不同的材料,冲压性能是不一样的,由于冲压工序较多,有的使用在冲压件的边角废料制造封闭器。所以,金属材料在冲压加工变形过程中,可能产生冷作硬化,其特征是σs、σb提高、塑性下降。为保证后续变形工序得以继续进行而不致破裂,可采用中间退火(再结晶退火)、高温退火等办法。
对于08#、10#、15#、20#钢,低温退火温度为600~650℃,在空气中冷却。
对于08#、10#、15#钢,高温退火温度为700~780℃,保温20~40分钟,在箱内空气中冷却;对于A1、A2钢,高温退火温度为900~920℃,保温20~40分钟,在箱内空气中冷却;对于20#、25#、30#、A3钢,高温退火温度为700~720℃,保温60分钟,在炉内冷却。
如果低温退火不能收到良好的效果,可采用高温退火。
为了不使零件产生很深的氧化皮,可以采用光亮退火,即在有中性的或还原媒质的电炉内退火。
三、封闭器常见缺陷与改善措施
在封闭器生产中,如果出现了废品或产品出现了缺陷,应及时找出产生废品或产品缺陷原因并采取相应措施加以消除或改善。现将生产中常见缺陷分析如下(冲压工艺的缺陷在前几章中有介绍,这里重点分析其它加工工艺):
1.封闭器车削加工常见缺陷与改善措施
封闭器车削件的常见缺陷、产生原因以及改善措施如表12-6所示。
表12-6 封闭器车削件常见缺陷与改善措施
常见缺陷 |
产生原因 |
改善措施 |
高度尺寸超差 |
刀具磨损 |
修磨车刀或更换车刀 |
内孔不圆 |
1、主轴承间隙过大 |
1、修理机床主轴承 |
2、零件夹紧变形 |
2、调整夹紧力 |
内孔有锥度 |
1、刀具磨损或崩刃 |
1、修磨车刀或更换车刀 |
2、主轴歪斜 |
2、校正导轨与主轴线平行 |
3、刀尖轨迹与主轴轴线不平行 |
3、大修机床导轨 |
内孔不光 |
1、刀具磨损工作中心 |
1、修磨刀具或更换刀具 |
2、刀尖低于工件中心 |
2、刀尖略高于工件中心安装 |
内孔尺寸超差 |
刀具磨损 |
修磨刀具或更换刀具 |
偏心 |
弹簧夹头不好 |
调整弹簧夹头或更换弹簧夹头 |
2.封闭器攻丝工序常见缺陷与改善措施
攻丝工序的常见缺陷、产生原因以及改善措施如表12-7所示。
表12-7封闭器攻丝工序常见缺陷与改善措施
常见缺陷 |
产生原因 |
改善措施 |
烂牙 |
1、丝锥磨钝或刀刃有粘屑 |
修磨丝锥或去掉刀刃粘屑攻丝时,一定要使丝锥与工件端面垂直 |
2、攻歪很多还强行借正 |
滑牙 |
1、复位弹簧位置不正 |
1、调整或更换复位弹簧 |
2、分配轴凸轮松动 |
2、调整紧固凸轮 |
螺孔攻歪 |
1、丝锥位置不正 |
1、调整丝锥位置 |
2、丝锥与螺孔不同 |
2、调整丝锥与孔使之同心 |
螺纹中径偏小 |
丝锥磨损 |
修磨丝锥或更换丝锥 |
螺纹中径太大 |
1、攻丝时丝锥晃动 |
1、检查同轴度,要求主轴与丝锥的同轴度在0.05mm以内 |
2、丝锥切削刃修磨不对称 |
2、正确修磨丝锥 |
螺纹表面粗糙度大 |
丝锥的刀刃有崩裂等损坏 |
更换丝锥 |
3.封闭器滚丝常见缺陷与改善措施
滚丝工序的常见缺陷、产生原因以及改善措施如表12-8所示。
表12-8 滚丝常见缺陷分析
常见缺陷 |
产生原因 |
改善措施 |
桶塞 |
1、大小滚轮对刀不准 |
1、调整大小滚轮的螺距 |
2、大小滚轮径向间隙太小 |
2、调整大小滚轮的间隙 |
3、小滚轮倒角太小 |
3、修磨小滚轮使其适当的倒角 |
螺纹中径偏小 |
1、大小滚轮径向间隙太大 |
1、调整大小滚轮的间隙其适当的间隙 |
2、大滚轮磨损 |
2、修磨大滚轮或更换大滚轮 |
螺纹表面粗糙度大 |
大滚轮磨损 |
修磨大滚轮或更换大齿轮 |
【返回目录】