《钢桶制造技术》
杨文亮 辛巧娟 编著
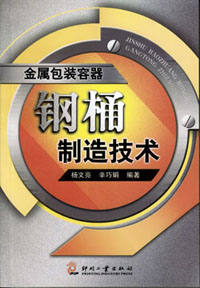
第十一章 桶底顶成形工艺
第三节 桶底顶成形模具设计要点
一、冲裁件凸凹模刃口尺寸的确定
冲裁件的尺寸和冲模间隙都决定于凸模和凹模刃口的尺寸。因此,正确地确定冲裁模刃口尺寸及其公差是冲模设计中很重要的一项工作。
冲裁时,落料件外形尺寸取决于光亮带的尺寸,即落料件的尺寸接近于凹模刃口的尺寸,所以,落料时取凹模作为设计的基准件,设计冲模时,首先确定基准件刃口的尺寸,然后再确定另一件刃口的尺寸。
冲模在使用过程中有磨损,落料件的尺寸会随凹模刃口的磨损而增大,为了保证零件的尺寸要求,并提高模具使用寿命,落料时所取凹模刃口尺寸应靠近落料件公差范围的最小尺寸,冲模间隙应采用合理间隙范围内的最小值。落料时冲模刃口与零件尺寸及其公差的关系如图11-12所示。图中的符号为:Dd——落料凹模刃口的名义尺寸;Dp——落料凸模刃口的名义尺寸;Dmax——落料件的最大极限尺寸;△——冲裁件公差;Z——最小双边合理间隙;χ——系数,为了避免多数冲裁件尺寸都偏向极限尺寸(落料时偏向最小尺寸),可取系数值χ=0.75~0.5;δd、δp——分别为凹模凸模的制造公差,一般取零件公差△的1/3~1/4;对圆形件,由于制造简单,精度容易保证,制造公差可按2~3级精度选取。
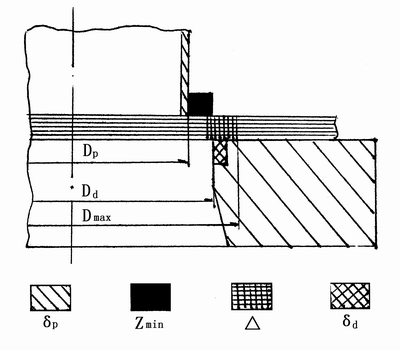
图11-12 冲模刃口尺寸的确定
冲模刃口各尺寸的关系为:
(11-17)
(11-18)
对于一般圆形及矩形等规则形状刃口的凸模和凹模,可以采用按图纸分别加工的方法。此时应保证下述关系:
(11-19)
二、冲裁模设计要点
1.模具总体结构型式的确定
模具总体结构型式的确定是设计时必须首先解决的问题,也是冲模设计的关键,它直接影响冲压件的质量、成本和冲压生产的水平,所以必须予以十分的重视。模具型式的选定,应以合理的冲压工艺过程为基础,根据冲压件的形状、尺寸、精度要求、材料性能、生产批量、冲压设备、模具加工条件等多方面的因素,做综合的分析研究和比较其综合的经济效果,以期在满足冲压件质量要求的前提下,达到最大限度地降低冲压件的生产成本的基本要求。确定模具的结构型式时,必须解决以下几方面的问题。
(1)模具类型的确定:简单模、连续模、复合模等;
(2)操作方式的确定:手工操作、自动化操作、半自动化操作;
(3)进出料方式的确定:根据原材料的型式确定进料方法,取出和整理零件的方法,原材料的定位方法;
(4)压料与卸料方式的确定:压料或不压料,弹性或刚性卸料等;
(5)模具精度的确定:根据冲压件的特点确定合理的模具加工精度,选取合理的导向方式或模具固定方法等。
除生产批量、生产成本、冲压件的质量等要与模具类型相适应外,在设计冲模时还必须对其维修性能、操作方便、安全性等方面予以充分注意,以下举例说明。
(1)模具结构应保证磨损后修磨方便;尽量做到不拆卸即可修磨工作零件;影响修磨而必须去掉的零件(如模柄等),可做成易拆卸的结构。
(2)冲模的工作零件较多,而且使用寿命相差较大时,应将易损坏及易磨损的工作零件做成快换结构的型式,而且应尽量做到可以分别调整和补偿易磨损件的高度尺寸。
(3)需要经常修磨和调整的部分尽量放在模具的下部。
(4)重量较大的模具应有方便的起运孔或吊钩环等。
(5)模具的结构应保证操作者的手不必进入危险区,而且各活动零件(如卸料板等)的结构尺寸,在其运动范围内不致压伤操作者的手指等。
2.冲模的压力中心
冲裁力合力的作用点称为模具的压力中心。如果压力中心不在模柄轴线上,滑块就会承受偏心载荷,导致滑块导轨和模具不正常的磨损,降低模具寿命甚至损坏模具。通常利用求平行力系合力作用点的方法——解析法或图解法,确定模具的压力中心。
在实际生产中,可能出现冲模压力中心在加工过程中发生变化的情况,或者由于零件的形状特殊,从模具结构考虑不宜于使压力中心与模柄中心线相重合的情况,这时应注意使压力中心的偏离不致超出所选用压力机所允许的范围。
3.冲模的封闭高度
冲模总体结构尺寸必须与所用设备相适应,即模具总体结构平面尺寸应该适应于设备工作台面尺寸,而模具总体封闭高度必须与设备的封闭高度相适应,否则就不能保证正常的安装与工作。
冲裁模的封闭高度是指模具在最低工作位置时,上下模板底面间的距离。
模具封闭高度H应该界于压力机的最大封闭高度Hmax及最小封闭高度Hmin之间,一般取:
(11-20)
如果模具封闭高度小于设备的最小封闭高度时,可以采用附加垫板。
三、圆形桶底顶拉深模工作部分尺寸的确定
拉深模工作部分(凸模、凹模和压边圈)的结构形状和尺寸,不仅对拉深时毛坯的变形过程具有重要的影响,而且也是影响拉深件质量的重要因素。当拉深的方法、变形程度、零件的形状、尺寸与精度的要求不同时,也要拉深工作部分具有不同的结构形状和尺寸。
一般桶底顶零件拉深较浅,且有凸缘,故拉深模必须采用防皱压边圈。
凹模的圆角半径rd对拉深过程有非常大的影响。在拉深过程中,板材在凹模圆角部位滑动时产生较大的弯曲变形。当由凹模圆角半径区进入直壁部分时,又被重新拉直,或者在通过凹模与凸模之间的间隙时受到校直作用。假如凹模的圆角半径过小,则板料在经过凹模圆角部位时的变形阻力与摩擦阻力以及在模具间隙里通过的阻力都要增大,结果势必引起总拉深力的增大和模具寿命的降低。在生产中一般尽量避免采用过小的凹模圆角半径。
凸模的圆角半径rp过小时,毛坯在这个部位上受到过大的弯曲变形,结果降低了毛坯危险断面——底与直壁交接部分的强度,使极限拉深系数增大。另外,即使毛坯在危险断面不被拉破,过小的凸模圆角半径也会引起危险断面附近毛坯厚度的局部严重变薄。所以过小的凹模与凸模的圆角半径都是不适宜的。
假如凸模与凹模的圆角半径过大,虽然可以降低拉深所需的力和增加毛坯危险断面的强度,为拉深变形提供更为有利的条件,但是,由于在拉深初始阶段处于压边圈作用之外,而且不与模具表面接触的毛坯宽度(rd+rp)加大,因而这部分毛坯很容易起皱。在拉深后期,过大的凹模圆角半径也会使毛坯外边缘过早地脱离压边圈的作用而起皱,尤其当毛坯的相对厚度小时,这个现象十分突出。因此,在设计模具时,应该根据具体条件选取适当的圆角半径。
凹模的圆角半径决定于拉深毛坯的厚度、成品零件的形状与尺寸、拉深方法等,在一般情况下,桶底顶拉深模凹模圆角半径可如下选取:
当毛坯相对厚度(
)在1~0.3之间时
rd=(15~20)t (11-21)
当毛坯相对厚度在0.3~0.1之间时
rd=(20~30)t (11-22)
一般情况下,可以取凸模的圆角半径的一半叫做间隙,即C=(dd-dp)/2。当间隙过大时,对毛坯的校直作用小,冲成的零件侧壁不直,容易形成弯曲的形状,或都形成口大底小的锥形。当间隙过小时,虽然可能得到侧壁平直而光滑的高质量零件,但是,由于毛坯在通过间隙时产生的校直与变薄变形都需要较大的拉力;另一方面,间隙较小时,毛坯与模具表面之间的接触压力加大,也会增加模具的磨损。
拉深模的间隙数值,主要决定于拉深零件的形状、尺寸精度的要求、拉深方法等。由于拉深过程中板材不可避免的有增厚现象(图11-10),所以间隙的数值常必须取得大于毛坯的原始厚度。在一般情况下的圆形桶底顶拉深时,间隙值可如下选取:
c=1.1t (11-23)
四、矩形桶底顶拉深模工作部分形状和尺寸的确定
由于桶底顶拉深高度较小,毛坯侧壁内拉力的数值不大,毛坯不易紧密地贴靠在凸模表面,在底部圆角和侧壁部位都容易形成不与凸模表面吻合的不规则表面,这时应取尽可能小而又不致啃伤毛坯表面的凹模角半径(尤其是在直边部分)。在一般情况下,可以根据毛坯的厚度,取凹模的圆角半径Rd为
Rd=(4~10)t (11-24)
一般在冲模设计时取较小数值Rd,然后在冲模试冲调整时根据实际情况适当的修磨加大。
矩形拉深模的间隙,应该根据拉深过程中毛坯各部分壁厚变化的情况而定。圆角部分的间隙,可以根据对零件尺寸精度的要求选取:
当零件的尺寸精度要求较高时,取间隙为
c=(0.9~1.05)t (11-25)
当零件的尺寸精度要求不高时,取间隙为
c=(1.1~1.3)t (11-26)
直边部分壁厚增大量较圆角部分小。在整个周边上壁厚的变化是均匀的,所以一次拉深成功的模具间隙也最好做成均匀过渡,在圆角部分最大,在直边部分最小。当矩形件的相对圆角半径r/B较小(r/B<0.15,B为直边宽,r为圆角半径)时,直边部分的中点附近的间隙可按弯曲模选取。
【返回目录】