《钢桶制造技术》
杨文亮 辛巧娟 编著
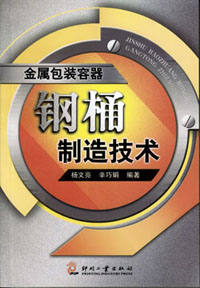
第十一章 桶底顶成形工艺
第二节 桶底顶成形工艺设计
一、冲裁力与冲裁间隙
冲裁力是选择冲压设备吨位和检验模具强度的一个重要依据。
平刃冲模的冲裁力可按下式计算:
P=kLtτ (11-1)
式中:P——冲裁力,N;L——冲裁件周边长度,mm;t——材料厚度,mm;τ——材料抗剪强度,N/mm2;k——系数。
系数k是考虑到实际生产中的各种因素而给出的一个修正系数。生产中的各种实际因素很多,如模具间隙的波动和不均匀,刃口的钝化,板料机械性能和厚度的波动等。根据经验一般可取k=1.3。
抗剪强度τ的数值,取决于材料的种类和状态。为了便于估算,可取抗剪强度τ等于该材料强度极限σb的80%,即取τ=0.8σb。
为了简便也可按下式估算冲裁力:
P=Ltσb (11-2)
用平刃模具冲裁时所需的冲裁力大,在钢桶底顶零件冲裁时,往往会超出现有设备的吨位。为了减小冲裁力,减小冲击、振动和噪声,可以采用斜刃冲模。
斜刃冲模冲裁时其情况如斜刃剪板机一样,材料是沿长度逐渐分离的。为了制取平整的零件,落料时凸模应做成平刃,凹模做成斜刃。斜刃一般做成波浪形,应力求对称以避免水平方向的侧向力。
斜刃冲模的减力程度由斜刃波峰高度H和角度φ而定。斜刃冲裁力Ps可按下式计算:
Ps=kP (11-4)
式中:P——用平刃冲模冲裁时所需的力;k——斜刃冲裁的减力系数(表11-2)。
在一般桶底顶落料情况下,可取H=2t,φ<5°,如图11-8所示。
表11-2 斜刃减力k值
H |
H=t |
H=2t |
H=3t |
k |
0.4~0.6 |
0.2~0.4 |
0.1~0.25 |
从上一节的冲裁过程分析中可知,冲裁凸模和凹模间的间隙,对冲裁件断面质量有极重要的影响。此外,冲裁间隙还影响模具寿命、卸料力、推件力、冲裁力和冲裁件的尺寸精度。因此,冲裁间隙是一个非常重要的工艺参数。
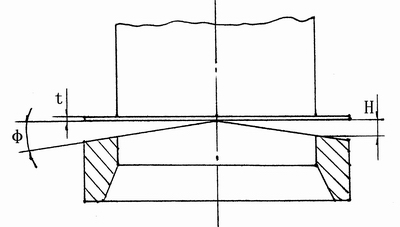
图11-8 斜刃冲模示意图
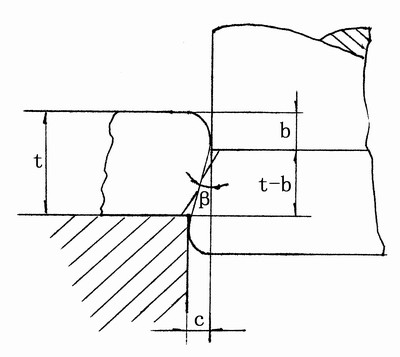
图11-9 冲裁模间隙
冲裁模的合理间隙数值应使冲裁时材料中的上、下两剪裂纹重合,正好相交于一条连线上(图11-9)。根据图上的几何关系可得:
(11-4)
式中:c——单边间隙,mm;t——材料厚度,mm;b——光亮带宽度,或产生裂纹时凸模挤入的深度,mm;b/t——产生裂纹时凸模挤入材料的相对深度,mm;β——剪裂纹与垂直线间的夹角。
材料厚度增大,间隙数值应成正比地增大,反之亦然。
比值b/t是产生剪裂纹时的相对挤入深度,它与材料有关。材料塑性好,光亮带b大,间隙数值就小。塑性低的硬脆材料,间隙数值就大一些。另外,b/t还与材料的厚度有关,对同一种材料来说,b/t不是一个常数。因此,薄料冲裁的合理间隙要小一些,而厚料的b/t数值小,合理间隙应取得大一些。
在实际工作中,可采用下述经验公式计算合理间隙c的数值。
c=mt0 (11-5)
式中:t——材料厚度, mm;m0——系数,与材料性能及厚度有关。
在实用上,对于桶底顶一般情况来说,可以选用下列数值:m0=0.06~0.09。
间隙是影响模具寿命诸因素中最主要的一个因素。冲裁过程中,凹模与落料之间均有摩擦,而且间隙越小,摩擦越严重,在正常情况下,间隙对冲裁力的影响不甚严重。
间隙对卸料力、推料力的影响比较显著。间隙增大后,从凸模上卸料或从凹模洞口推料都将省力。一般当单边间隙增大到材料厚度的15~25%时,卸料力几乎减到零。
表11-3为正常情况下合理间隙数值。其中“双边”是指模具在直径方向上两边的间隙总和。
表11-3 冲裁模合理间隙值(双边)
材料种类 |
材料厚度(mm) |
0.1~0.4 |
0.4~1.2 |
1.2~2.5 |
硬度较小的钢板 |
0.01~0.02mm |
7~10%t |
9~12%t |
硬度较大的钢板 |
0.01~0.05mm |
10~17%t |
18~25%t |
在使用表11-3时,当对冲裁件断面质量要求高时,可将表中的间隙数值减小1/3;当凹模洞口型式为圆柱形时,取表中偏大的数值;当凹模洞口型式为锥形时,取表中偏小的数值。
二、拉深力与拉深间隙
拉深件的拉深程度一般用拉深系数表示,拉深系数(m)是指拉深后制件直径d与毛坯直径D的比值:
m=d/D (11-6)
m是小于1的系数。当m越小时,说明拉深时变形程度越大,传统习惯把K=1/m表示拉深程度或拉深比。
在确定m值时,在保证产品质量的前提下,要做到充分利用材料的塑性,使其达到最大可能的变形程度,以降低成本。
为了正确选择设备,工艺设计时应进行拉深力的计算,在生产中常用近似公式计算。
对圆形桶底顶制件:
P=Kπdtσb (11-7)
对于矩形桶或复杂形状的桶底顶制件:
P=KLtσb (11-8)
式中:t——材料厚度,mm;d——拉深凹直径,mm;L——拉深凹模口周长,mm;σb——材料强度极限,N/mm2;K——系数,取0.6~1.0(m小时取大值)。
为了防止拉深过程中起皱,模具应有压料装置,压料力一般由下式计算:
对于圆形桶底顶制件:
(11-9)
对于矩形及复杂形状的桶底顶制件:
Q=K1Fq (11-10)
式中:D——毛坯直径,mm;d——拉深凹模直径,mm;r凹——凹模圆角半径,mm;q——单位压料力,N/mm2,对于一般桶底顶制件,q=0.25N/mm2。F——有效压边面积,mm2;K1——系数,取1.1~1.4(m小时取大值)。
因为压料力和拉深力是同时进行的,所以计算总的拉深力时包括压料力在内,即
P总=P+Q (11-11)
拉深模具凸凹模之间应有一定的间隙,拉深模的间隙数值,主要决定于拉深零件的形状、尺寸精度的要求,拉深方法等,由于拉深过程中板材不可避免地有增厚现象(图11-10),所以间隙的数值通常必须取得大于毛坯的原始厚度,以利于拉深过程的进行。
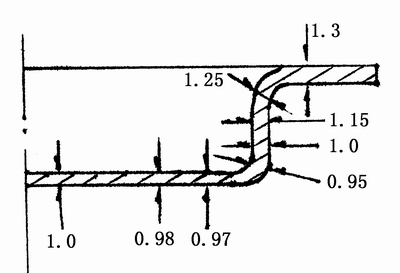
图11-10 有压料圈拉紧时制件厚度的变化
(制件名义尺寸为1.0)
拉深间隙就是凸模与凹模直径之差的一半,通常用Z来表示。拉深间隙的大小,对拉深力、制件质量和模具寿命均有影响。间隙过大,制件容易起皱;过小则直壁容易变薄,表面挤伤甚至拉裂,也降低模具寿命。拉深间隙的计算公式为:
(11-12)
式中:K——系数,取1.1~1.5;t——料厚,mm;△——料厚上偏差,mm。
对于一般桶底顶拉深情况来说,可取K=1.1,即用下式来计算拉深间隙:
Z=1.1t+△ (11-13)
三、矩形桶底顶件毛坯形状和尺寸的确定
正确地决定矩形制件毛坯的形状和尺寸,对节约钢材和提高拉深件质量都是很重要的。因为过大的毛坯尺寸,能够引起危险断面的拉应力的增大。当毛坯局部尺寸过大时,在拉深过程中,这部分会从变形区突出去,不但突出部分本身的变形减小,而且也使邻近部分的板料变形比较困难。毛坯尺寸大的部分变形阻力增大,使其变形过程减小,必然导致拉深变形较多集中到其他部分去,于是增加了沿毛坯周边变形分布不均匀的程度。引起制件壁厚不均匀和变形过分集中部位的局部起皱,降低了拉深件的质量。
矩形件拉深时,计算毛坯尺寸的依据是等面积法,即根据毛坯的面积和制件的面积相等的原则进行计算。但是,毛坯的形状必须保证材料在整个周边的分布,能满足制件周边每点上都形成等高的侧壁的需要。
矩形件直边部分的应变可略而不计,即认为是简单的弯曲,按弯曲变形展开计算。
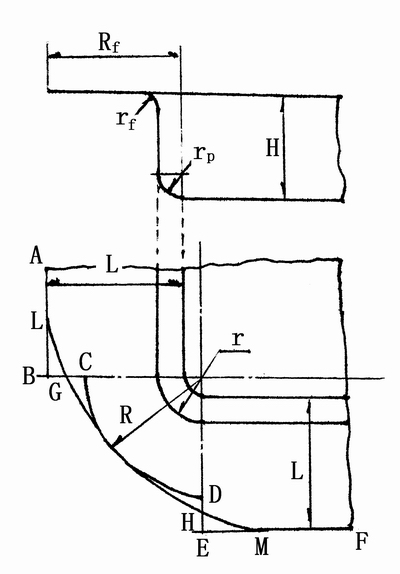
图11-11 矩形拉深毛坯的概略计算
圆角部分按四分之一圆形件拉深变形在矩形件底部的平面展开,见图11-11的ABCDEF。
上述毛坯不具有圆滑过渡的轮廓,而且也没有考虑到圆角部分向直边部分转移,所以要作如下修正:由BC和DE的中点G和H做圆弧R的切线,并用圆弧R将切线和直边展开线连接起来,则得到修正后的毛坯外形ALGHMF。
按弯曲变形展开的直边部分长度L为:
(11-14)
式中:H——矩形件的冲压高度(应包括修边余量△h,其值为0.03h~0.05h),其值应等于矩形件高度h和△h之和,mm;rp——矩形件底部的圆角半径,mm;Rf——底部圆角中心和凸缘边之间的距离,mm;rf——矩形件边缘与侧壁圆角半径,mm。
圆角部分按四分之一圆形件展开得半径R,其值按下式计算:
(11-15)
式中:a——桶底顶的边宽,mm。
矩形件可以一次拉深成功,拉深力P可近似地按下式计算:
(11-16)
式中:r——矩形件圆角部分的圆角半径;L——矩形件直边部分长度的总和;σb——材料的强度极限;t——材料的厚度;K1——系数,一般可取K1=0.5;K2——系数,间隙足够大,压边力较大,Q≥0.3P时取K2=0.3,强力压边时取K2=1。
【返回目录】