《钢桶制造技术》
杨文亮 辛巧娟 编著
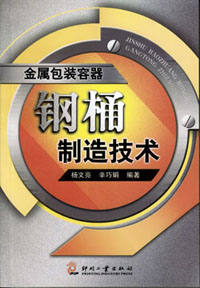
第十一章 桶底顶成形工艺
钢桶一般由桶身、桶顶、桶底、封闭器及相关辅件组成。在钢桶生产中,钢桶的桶顶、底盖和封闭器等常用冷冲压方法加工。钢桶顶底盖的冲裁、拉深、翻边;封闭器的落料、冲孔、拉深;钢桶顶盖与螺圈的锁装均由冲压加工完成。因而冲压加工在钢桶生产中有着很重要的地位,它是钢桶生产中应用广泛的一种加工工艺。
冲压是金属压力加工方法的一种,它是在常温下借助模具在冲床上进行的加工方法。
由于桶底顶盖和封闭器成批大量的生产,采用冲压加工,不论在技术方面还是在经济方面,都有着显著的优点,它不但能获得重量轻、强度高、刚性好、外表光滑美观的桶件,而且操作简便、劳动强度低。很容易实现机械化自动化生产,提高生产率。
第一节 桶底顶成形的特点
桶底顶的成形是由冲裁(落料)和拉深成形两个过程完成的。桶底顶的类型如图11-1所示可分为圆形、矩形、椭圆形,多边形等,还有些桶底顶设有加强筋。
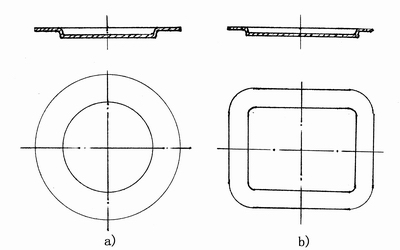
a—圆形桶底顶;b—矩形桶底顶
图11-1 桶底顶的类型
图11-2 桶底顶冲裁过程
一、桶底顶冲裁(落料)成形特点
如图11-2是钢桶材料的冲裁过程。当模具间隙正常时,这个过程大致可以分成三个阶段。
1.弹性变形阶段
当冲头接触板料后,开始压缩材料,并使材料产生弹性压缩,拉伸与弯曲等变形。这时凸模冲头略挤入材料,材料的另一侧也略挤入凹模洞口。随着冲头继续压入,材料内的应力达到弹性极限。此时,凸模下的材料略有弯曲,凹模上的材料则向上翘,间隙越大,弯曲和上翘越严重。
2.塑性变形阶段
当凸模冲头继续压入,压力增加,材料内的应力达到屈服阶段。这时冲头挤入材料的深度逐渐增大,即塑性变形程度逐渐增大,材料内部的拉应力和弯矩都增大,变形区材料硬化加剧,冲裁变形力不断增大,直到刃口附近的材料由于拉应力的作用出现微裂纹时,冲裁变形力达到最大值。材料出现微裂纹,说明材料开始破坏,因而塑性变形阶段告终。由于存在冲模间隙,这个阶段中除了剪切变形外,冲裁区还产生弯曲和拉深,显然,间隙越大,弯曲和拉深也越大。
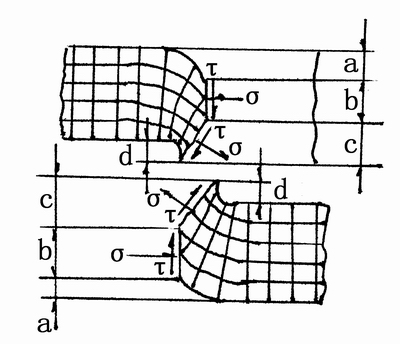
a—塌角;b—光亮带;c—剪裂带; d—毛刺;σ—正应力;τ—切应力
图11-3 冲裁区应力与应变情况
3.断裂分离阶段
凸模冲头仍然不断地继续压入,已形成上下微裂纹逐渐扩大并向材料内延伸,像楔形那样地发展,当上下两裂纹相遇重合时,材料便被剪断分离。
材料在冲裁时的应力应变如图11-3所示,在塑性变形过程中,由冲头挤压切入所形成的表面是很光滑的,一般称为光亮带。材料在剪断分离时所形成的断裂带,表面粗糙,称为剪裂带。
桶底顶冲裁(落料)件的断面具有明显的区域性特征。断面上可以明显地区分为光亮带、剪裂带、塌角和毛刺四个部分。图11-3,a为塌角,形成塌角的原因是当冲头压入材料时,刃口附近的材料被牵连拉入变形的结果;b为光亮带,表面光滑,断面质量最佳;c为剪裂带,表面粗糙并略带斜度,不与板平面垂直;d为毛刺。
塑性差的材料,断裂倾向严重,经由塑性变形形成的光亮带及塌角两部分所占的比例较小,毛刺也较小,而断面大部分是剪裂带。塑性较好的材料,与此相反,其光亮带所占的比例较大,塌角和毛刺也较大,而剪裂带则小一些。
模具间隙较大时,材料中的拉应力将增大,容易产生剪裂纹,塑性变形阶段较早结束,因此光亮带要小一些,而剪裂带、塌角和毛刺都比较大,制件的翘曲现象也较显著。反之,间隙较小时,材料中拉应力成分减小,静水压效果增强,裂纹的产生受到抑制,所以光亮带变大,而塌角、斜度、翘曲等现象均减小。
间隙过大或过小均将导致上、下两方的剪裂线不能相交重合于一线,毛刺、塌角、斜度都将增大,使冲裁件尺寸与冲模刃口尺寸的偏差增大。间隙合适,即在合理间隙范围内时,上、下剪裂纹基本重合于一线,这时光亮带约占板厚的三分之一左右,塌角、毛刺和斜度也均不大。
从上面分析中可以看出,冲裁件质量主要是通过断面光亮带大小、塌角、毛刺以及冲裁件的翘曲等来判断的。增大光亮带的关键在于推迟剪裂纹的产生,所以要尽量减小材料内的拉应力和弯曲力矩,其主要途径是减小间隙。压紧凹模上的材料,对凸模下的材料施加反压力。减小塌角、毛刺和翘曲的措施,除了尽可能采用合理间隙的下限值外,还要注意保持刃口的锋利,采用压板和在凸模下面加反压力等。
表11-1为一般桶底顶冲裁(落料)件允许的毛刺高度。对于一般钢桶用材料,冲裁断面粗糙度在12.5~6.3之间。
表11-1 桶底顶冲裁毛刺的允许高度
材料厚度,mm |
生产时毛刺高度,mm |
试模时毛刺高度,mm |
~0.5 |
≤0.05 |
≤0.015 |
0.6~1.0 |
≤0.10 |
≤0.03 |
1.1~2.0 |
≤0.15 |
≤0.05 |
二、桶底顶拉深成形特点
拉深成形过程,是利用模具使冲裁后得到的平面桶底顶毛坯变成为如图11-1所示的零件的冲压工艺方法。在多数企业的桶底顶实际生产中,冲裁落料与拉深是在同一个复合模中一次冲压成形的。也有一些生产条件较差的(或缺少大吨位冲床的)企业生产中,会单独进行拉深加工。现就拉深成形的特点进行简单的分析。
桶底顶拉深过程如图11-4所示,其凸模与凹模和冲裁时不同,它们的工作部分都没有锋利的刃口,而是做成为一定的圆角半径,并且其间隙也稍大于板料的厚度。在凸模的作用下,原始直径为D0的毛坯,在凹模端面和压边圈之间的缝隙中变形,并被拉进凸模与凹模之间的间隙里形成空间零件的直壁。零件上高度为H的直壁部分是由毛坯的外部环形部分转化而成的,所以拉深时毛坯的外部环形部分是变形区,而底部通常是不参加变形的不变形区。
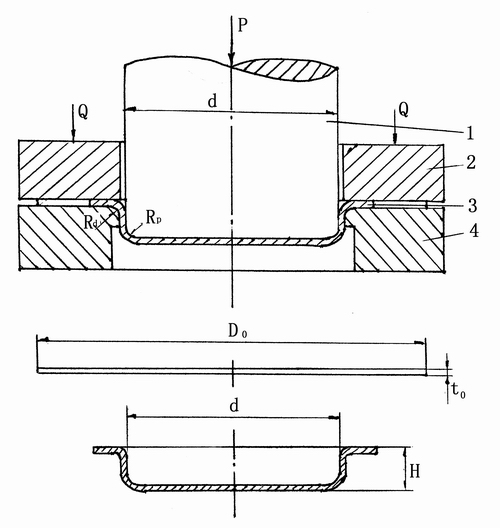
1—凸模;2—压边圈;3—毛坯;4—凹模
图11-4 桶底顶拉深过程
1.圆形桶底顶的拉深特点
圆形桶底顶制件在拉深过程中,毛坯各部分的受力情况都是不同的,其毛坯的变形特点,见图11-5所示。
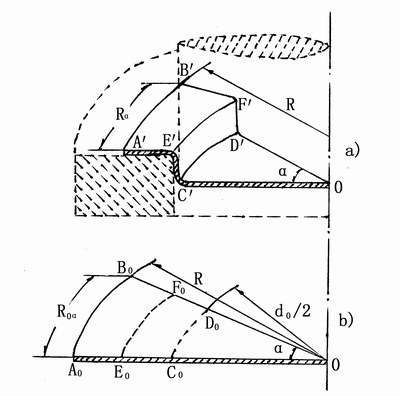
图11-5 圆形桶底顶拉深的变形特点
制件的OC0D0部分,在全部拉深过程中始终保持其平面形状,是不变形区。这部分毛坯起力的传递作用,它把接收到的凸模作用力传给毛坯的圆柱形的侧壁,使侧壁产生轴向拉应力,而本身是双向受拉的应力状态,如图11-6所示。
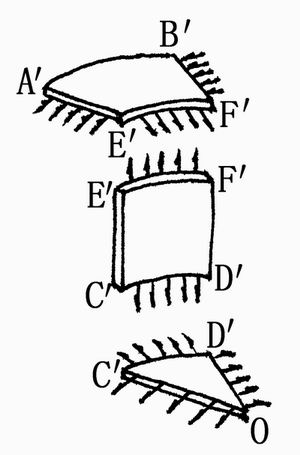
图11-6 拉深时毛坯内各部分的内应力
拉深时形成的圆柱形侧壁部分C'D'E'F'是由平板毛坯C0D0E0F0部分转化而成的。这部分是已经结束了自己的塑性变形阶段的已变形区,它也起着力的传递作用,即把凸模的作用力传到平面环形部分A'B'E'F',并使其内部产生足以引起拉深变形的径向拉应力σ1(图11-6)。平面环形部分A'B'E'F'是拉深时变形区,在径向应力的作用下,产生塑性变形,并向中心移动,而且逐渐地进入凸模与凹模的间隙里,最终形成制件所需要的形状。
拉深毛坯在凸模圆角处一直承受着圆柱形直壁传来的拉应力,并且受到凸模的压力,使这部分材料变薄最为严重,因此危险断面就在凸模圆角附近处。当拉深程度较小时,侧壁内的拉应力也小,毛坯与凸模圆角部分不能紧密接触,制件的底部也容易产生畸变。
2.矩形桶底顶的拉深特点
矩形桶底顶制件的拉深,是一种复杂的变形过程,是拉深与弯曲的组合。矩形制件与圆形制件的最大差别是在拉深件周边上变形是不均匀的,见图11-7。
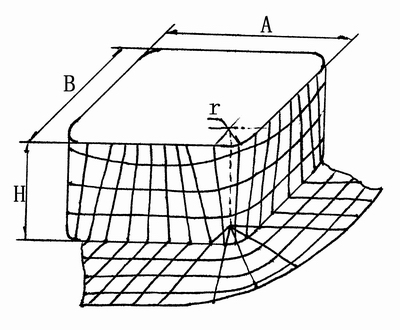
图11-7 矩形件拉深变形特点试验
为了分析矩形桶底顶制件在拉深时的变形特点,拉深前在毛坯表面上,在圆角部分成径向放射线与同心圆弧所组成的网格。而在直边部分划成由相互垂直的等距离平行线组成的网格,然后拉深。观察拉深后制件表面网格的变化,可以了解矩形桶底顶制件在拉深时变形的情况。
(1)直边部位侧壁上的网格尺寸发生了横向压缩和纵向伸长的变化,同时其分布也是不均匀的:在直边部分的中间部位拉深变形最小,在靠近圆角部分的拉深变形最大。变形在高度方向上也是不均匀的:在靠近底部位置变形最小,在靠近上口部位变形最大。
(2)圆角部位平板上的径向放射线,在拉深变形后不是成为与底面垂直的等距离平行线,而是成为上部距离大,下部距离小的斜线。其变形特点与圆形桶底顶制件拉深相似,但其变形程度小于半径与高度相同的圆形制件。
【返回目录】