《包装企业质量检验员培训教程》
杨文亮 辛巧娟 著
第四章 质量统计检验
第三节 计数抽样检验
二、百分比抽样检验及其不合理性
1.百分比抽样检验的概念
所谓百分比抽样检验,就是不论产品批量的大小如何,一律按同样的百分比从产品批中抽取样本,而在样本中允许出现的不合格品个数是相同的。比如,按10%抽取样本,当批量为1000时,样本大小为100,当批量为100时,样本大小为10,并且规定的这两个样本中都不允许有不合格品,即规定Ac=0。有的还规定,当第一次抽检未被接收时,还可允许第二次加倍抽取样本进行检验,同样规定Ac=0,即不允许有不合格品。可见,这种抽样方案,对大批量严,对小批量松,而且当批量很大时,抽取的样本数也随之增大,不经济。
2.百分比抽样检验的不合理性
(1)抽样比例的确定缺乏理论根据:采用百分比抽检时,应确定多大的比例,并无科学根据,大多是靠“拍脑袋”确定的,即使是参照类似的产品标准或行业规定,但实际上那些规定也是没有什么依据的。一般是认为重要的,抽样比例就高些,不太重要的就低些。并且常常因人而异。
(2)百分比抽检没有明确的质量保证值:现假定批量为N,按20%从批中取样本n进行检验,未发现有不合格品就接收,即Ac=0,若发现有不合格品就拒收。
设有两批批量不同的产品要作检验:
第一批产品的批量N1=10,其中有1件不合格品(即d1=1),则批不合品率p1=d1/N1=1/10=10%,按20%抽取样本n=20%×N1=2,抽取的样本n1为合格品的可能性为80%,抽到不合格的可能性为20%,也就是产品批N1被接收的可能性为80%。
第二批产品的批量N2为50,其中也只有1件不合格品(即d2=1),则批不合格品率p2=d2/N2=1/50=2%,按20%抽取样本n2=20%×N2=10,当把产品批按10件为一组分成五组时,显然其中有一组样本含有那一个不合格品,其余四组则均为合格品,此时该批被接收的可能性同样为80%。
由此可以看到,两批不同批量的产品,虽然批不合格率有好有坏,相差很大,但用同一百分比抽样时,产品批被接收的可能性都是相同的。因此说明,被接收的产品批没有明确的质量保证值,不能反映其实际质量水平到底是多少。
(3)百分比抽样具有“大批严、小批松”的缺点:今有批量不同的五批产品,规定均按5%抽样,并规定合格判定数Ac=0,则抽样方案分别是:
N1=100 |
n1=5 |
Ac=0 |
N2=200 |
n1=10 |
Ac=0 |
N3=400 |
n3=20 |
Ac=0 |
N4=600 |
n4=30 |
Ac=0 |
N5=2000 |
n5=100 |
Ac=0 |
将这五个方案画出如图4-4所示抽样特性曲线,可以看出方案(100/0)比方案(5/10)严得多。当批的不合格品率均为20%时,这两个方案的接收概率相应为0.13和0.90。
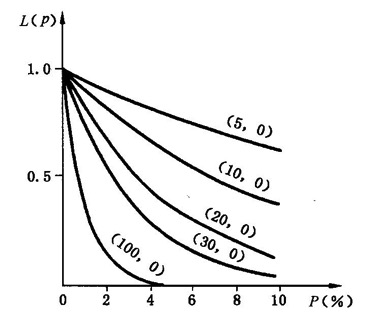
图4-4 抽样特性曲线
三、计数调整型抽样检验
1.计数调整型抽样方法的形成
计数调整型抽样检验是当今国内外应用最广的一种检验方案。具有代表性的计数调整型抽样方案是美国军用标准MIL-105D(简称105D)。日本在105D的基础上,制定了日本工业标准,称为JIS9015。1974年国际标准化组织(ISO)也在105D的基础上制定并颁布了ISO2859国际标准。我国标准GB/T2828-1987,就是参照国际标准ISO2859:1974制定的。它适用于连续批的检验。
国际标准化组织(ISO)后又对ISO2859标准作了重大修订,将该标准作为一个通称为《计数抽样检验程序》的系列标准的第一部分,即ISO2589-1:1999《按接收质量限(AQL)检索的逐批检验抽样计划》,我国于2003年根据该标准发布了与此等同的GB/T2828.1-2003国家标准。
2.计数调整型抽样方案的基本特点
所谓调整型抽样方案,就是在验收过程中,不是采用固定的一种抽样方案,而是根据产品质量的变化,轮番地采用正常检验、加严检验和放宽检验这三个不同的抽样方案,通过转换规则连续组成一个完整的抽样体系。该方案一个显著特点,就是检验员(或使用方)可以根据已有的历史资料调整抽样方案的宽严程度。即在一般情况下,采用正常检验;经过初次或几批检验结果表明制造者提供的批质量变好时,转换到放宽检验;反之,当批质量变坏时,转换到加严检验;如果质量下降到某种规定程度时,就要停止检验,直至采取措施,确认质量有明显好转后,才能重新开始实行抽样检验。在调整型抽样方案中,正常检验体现了对生产方式的保护,加严检验体现了对使用方的保护。而放宽检验则是对提供优质产品在生产力的一种鼓励。三种方案转换如图4-5所示。
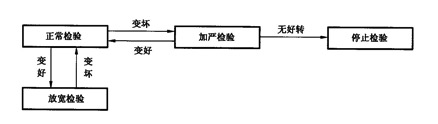
图4-5 调整型抽样方案相互转换示意图
调整型抽样方案的主要优点在于对产品质量具有较好的辨别能力。通过调整检验的宽严程度,能鼓励和促进生产方更好地关心提高产品质量,也为使用方择优选择产品提供了科学的依据。此外,还具有抽样数量少、检验费用低等优点。因此被广泛应用于原材料、工序检验、产品成品检验。原则上适用于连续批检验。
3.计数调整型抽样检验的使用方法
参阅GB/T2828.1-2003(ISO2859-1:1999,IDT)《计数抽样检验程序 第1部分:按接收质量限(AQL)检验的逐批检验抽样计划》。
四、孤立批抽样检验
1.抽样方法及标准的形成
我国参照国际标准以极限质量LQ检索的孤立批抽样检验方案ISO2859-2:1985设计,发布GB/T15239-1994《孤立批计数抽样检验程序及抽样表》国家标准,专门用于孤立批的抽样检验。在生产实际中,孤立批的情况主要有:从连续稳定生产的供应商处采购的一批或少数几批产品的验收;质量波动大、忽好忽坏的产品批的检验;单位生产或新产品小批试制过程中加工的产品的验收。
2.孤立批抽样方法的特点
(1)GB/T15239中规定以极限质量LQ为质量指标。对一个产品来说,是否被接收,取决于生产方式或使用方对检验批的质量要求,而极限质量LQ是与较低的接收概率相对应的一种质量水平,是使用方所不希望的质量水平。
孤立批抽样方案确保当产品批的质量水平接近极限质量时,批被接收的概率很小。因此可以说孤立批的抽样方案是通过控制使用方风险来实现对批的质量保证的。
(2)根据产品来源的不同而区分检验模式。GB/T15239根据产品批的来源不同,提供两种抽样模式。
模式A是在生产主和使用方均为孤立批的情形下使用,如单件小批生产、质量不稳定产品批、新产品试制的产品批的检验。
模式B针对来自于稳定的生产过程的少数几批产品的验收,即对生产方是连续的,而使用方由于对这种产品采购的产品批数较小,对它而言应视为孤立批。
3.孤立批抽样检验GB/T15239的使用
孤立批抽样检验方案GB/T15239-1994的抽样检验程序如下:
(1)规定单位产品需检验的质量特性,并规定不合格的分类;
(2)根据产品批的来源选择合适的抽样模式;
(3)规定检索方案所需的要素,检索抽样方案。
不同的抽检模式所需规定的检索要素是不同的,对于模式A必须规定极限质量LQ、批量N和抽样类型。极限质量的规定方法与AQL相似,因为它们均是对质量水平提出的要求,只不过极限质量LQ是批不可容许的质量水平,因此对于同一种产品LQ值的大小应与以往规定的AQL值拉开一定距离,如果两个值太接近,会使检索出抽样方案样本量过大;如果两个质量水平相差太远,又会使抽样方案过于宽松。批量N的大小根据生产实际组批,组批的要求与前面的内容相同。在孤立抽样检验两种模式均给出了一次和二次抽样方案,抽样类型的选取与GB/T2828.1相同。
孤立批的抽样方案的B模式除规定以上要素外,还要给出检验水平,因为B模式的设计是根据限质量LQ、批量N、检验水平的抽样类型设计的。在B模式中检验水平的规定与GB/T2828.1相同,仍为4个特殊水平和3个一般检验水平。但是在孤立批检验标准中检验水平的作用和GB/T2828.1有所不同,B模式中规定在极限质量处的接收概率应很低,因此只要给出了极限质量,无论是选择哪个检验水平,在极限质量处的接收概率相差不大,不同的检验水平在对检验批规定极限质量相同的情况下对使用方的影响较小,而对生产方的影响较大。如当N=10000,LQ=2.0(%)时,检验水平为Ⅱ的抽样方案为(200,1),当检验水平为Ⅲ时,抽样方案为(315,3)。两个方案在极限质量处的接收概率相差不大,而在生产方风险为5%处的质量水平相差很大。当极限质量与过程平均相差较大时,可以选择较低检验水平。
返回目录页
|