《厂长经理的设备管理课》
主讲/辛巧娟
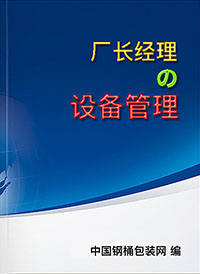
第五十九讲
59-什么是以可靠性为中心的维修(RCM)?
以可靠性为中心的维修管理(Reliability Centered Maintenance——RCM,属于第三代维修管理的最具有代表性的模式。这一设备管理模式强调以设备的可靠性、设备故障后果,作为制定维修策略的主要依据。按照以可靠性为中心的维修管理模式,首先应对设备的故障后果进行结构性评价、分析并综合出一个有关安全、运行经济性和维修费用节省的维修策略。另外,在制定维修策略时,自觉地以故障模式的最新探索成果作为依据。也就是说,以可靠性为中心的维修管理,是综合了故障后果和故障模式的有关信息,以运行经济性为出发点的维修管理模式。下面介绍一下这一维修体系的基本要点。
(1)关于故障后果的评价
以可靠性为中心的维修管理,对设备故障后果进行结构性评价。这种评价是以下面的颇序来排列其重要程度的。
1)潜在故障问题。目前对设备无直接影响,而故障一旦发生则后果严重。
2)安全故障问题。故障一旦发生,会损害人身健康或威胁生命安全。
3)运行故障问题。故障一旦发生,影响生产运行和修理的直接费用。
4)非运行故障问题。此故障一般不影响生产运行,但影响修理费用。
按照以可靠性为中心的维修管理策略,如果设备故障后果严重,则应采用预防维修。否则除日常维护和润滑外,不必进行预防维修。在评价故障后果以便制定维修策略时,每个设备的所有功能和故障模式都应加以考虑,并进行分析,制定出每一设备的维修方针。其故障后果与维修策略关系如表59-1所示。
表59-1 故障后果与维修策赂的选择
故障类型 |
维修策略 |
潜在故障 |
强制预防维修 |
预测维修(状态监测、点检) |
周期性预防维修 |
有碍安全故障 |
强制性预防维修 |
经济性故障
(运行故障) |
根据经济性可选预防、预测或事后维修 |
经济性故障
(非运行故障) |
事后维修 |
(2)对于故障特性的研究
预防维修是根据设备故障特征曲线或浴盆曲线,在设备进入耗损故障期之前安排进行的维修活动。当今的设备比以往要复杂得多,而且故障模式也有了新的变化。美国民航在过去30年间,作了大量关于设备可靠性的研究,发现在设备从使用到淘汰(包括无形磨损造成的设备报废)其故障特征曲线呈6种不同形状,如图59-1所示。

图59-1 不同的故障特征曲线
研究表明,原来认为设备使用时间越长磨损越严重,而且会使故障率迅速上升,这样一种观点不一定正确。对于某种故障模式起主导作用的设备,故障率可能与使用时间长短有关。而对于大多数设备而言,使用时间长短对于设备可靠性的影响不大。也就是说,经常修理设备或定期大修,不一定会防止故障发生,反之可能将初期的高故障率引入稳定的系统之中,增加设备总故障率。
根据上面的认识,设备的定期大修只有在故障后果严重且无法准确预测的情况下才必要。有条件则尽可能采取预测维修,一般情况下则可采用日常维护保养及润滑等措施。
(3)对子潜在性故障和功能性故障的研究
所谓的潜在性故障,指故障发生前的一些预兆,是可以识别的物理状态,它表明一种可能的故障即将发生。功能性故障是指设备巳丧失了某种规定功能。预防维修是在设备进入潜在故障期,但尚未发展成功能故障时进行的维修活动。我们称设备从潜在故障到功能故障的间隔期为P-F间隔,如图59-2所示。
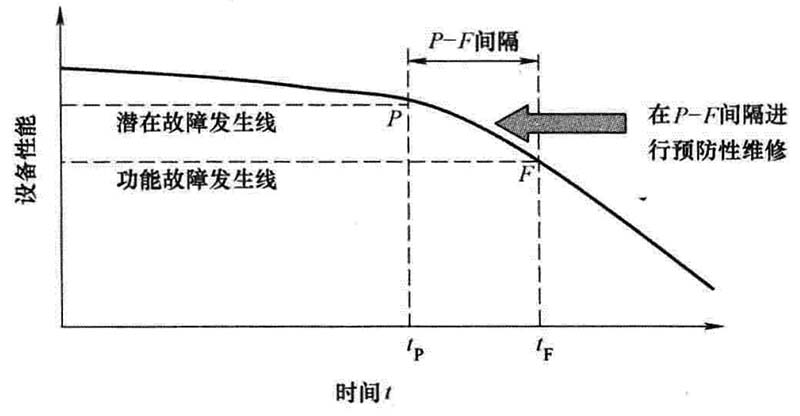
图59-2 故障的P-F间隔
图中P点表示设备性能己开始劣化并进入潜在故障期。这一时期在设备上具体表现为裂纹、振动、噪声、炉体表面的过热点、轮胎的磨损等。F点表面设备己丧失规定功能,即己发展为功能故障。各种设备和不向的P-F间隔期差别很大,有的仅是几微秒,有的长达几十年。较长的P-F间隔期,使我们有更多的时间作预防维修。在作维修计划时,就应把这种关于潜在故障起始时间的测量,作为选择预防维修时间的依据。
(4)维修策略
以可靠性为中心的维修管理的最大特点,是以后果评价作为维修方法选择的依据。其要点是:
1)对潜在故障使用强制性的预防维修。通过在线或周期性的故障检查来寻找故障。
2)对危害安全的故障使用强制性的预防维修方法。如果没有可以使故障灾害降低的维修方法,则应考虑设备或部件的重新设计。
3)运行和非运行的经济性故障,则根据经济合理性来决策到底使用何种维修方式。
4)对于那些预防维修方法不能解决的问题,可以采用技术改造、重新设计和改装的方式解决。
(5)故障诊断和维修策略的应用
以可靠性为中心的维修管理所使用的故障检测方法主要为:
1)状态监测技术。现在大约有包括振动监测和油液分析在内的150~200种监测技术。
2)根据产品质量变化来诊断设备故障的技术。
3)设备性能监测技术。
4)人的感觉检查,即凭视、昕、触、嗅来检查设备状态变化。
以可靠性为中心的维修管理的维修策略包括:
1)视情维修。通过以上检查诊断技术的运用,决定对设备的预防维修,再结合定期维修和定期报废更换维修方法。
2)预防维修。定期维修或检查后安排的维修方法,作为视情维修方法的补充。
3)事后维修。在不重要的设备上仍可采用。
以可靠性为中心的维修管理还注重评估各种维修方法的可用性和有效性。所谓可用性,就是此方法在技术上是否行得通;有效性则是评估每种方法使用后的结果。结果有效,还应对使用和不使用这种方法的总费用进行对比。
(6)维修资源的合理调配
以可靠性为中心的维修管理,主张尽可能有效地利用人力、材料等维修资源。综观当代工业发展趋势,企业维修费用不断增长,作为“机器看管者”的操作工人不能得到充分地重视。当前,企业设备维修的承担者可以有三种选择:
1)外部承包者。外部承包者在集中高水平维修力量、维修工具等方面有一定优势。他们可以承担的工作有:分散的设备,如交通、起重工具;超出正常工作量的停产大修;费用便直的工作,如管道、油漆工作等;专门设备,如空调、计算机等;复杂设备的长期疑难问题,可由生产厂或其代理人协助解快。
2)多技能操作者。设备自动化程度的提高,使操作工人成为机器的看管者。为了充分发挥这些工人的作用,不少企业开始注意把操作与维修结合起来,并交给一个人来完成。这些人也就是我们说的多技能操作者。他们也就是掌握了维修技能的生产操作工。也是“全员生产维修”的主力军。
3)企业内部的维修部门。在相当一段时间内,企业内部的维修部门还应保留。他们承担着企业内相当一部分的维修任务。
(7)强调工人和管理人员的培训
因为以可靠性为中心的维修管理,要求操作者具备维修技能,如电气、电子知识,机械知识,气动、液压及传感技术等。管理人员应具备根据故障厉果评价和选择维修策略的水平。同时还要求管理者对于维修计划、派工单、工时估计、工作分配计划、预算和费用控制及领导和启发艺术均达到一定水平。因此,企业要经常性地对工人和管理人员进行培训,使他们适应现代企业的发展。
(8)以可靠性为申心的维修管理的实施
以可靠性为中心的维修管理,可以在一年之内完成对人员的培训和实践练习。可以分三个阶段进行:
1)第一阶段利用以可靠性为中心的维修管理的思想和技术,评价故障后果和选择预防性措施。这个阶段结束后,将形成一个全厂设备维修需求的全面总结或计划系统, 这一计划应该使总维修工作量显著减少。
2)第二阶段利用第一阶段的结果,制定劳动力和备件管理政策,视实际情况对现有管理状况加以调整。
3)第三阶段设计各种系统和执行程序,以保证第一阶段和第二阶段计划顺利进行。
(9)逻辑决断分析
以可靠性为中心维修的核心是根据RCM原理所进行的关于维修策略的逻辑决断分析。
首先需要判断故障后果是否严重,对于不严重的后果,非预防形式的事后处理可以最大限度延长设备的有效使用时间。
如果故障后果严重,即故障对于安全、环境、职业健康和生产损失的影响严重,则再看定期预防维修、非定期的状态维修以及隐患检测是否技术可行,如果技术不可行,则只能通过改进设计加以解决;如果技术可行,再进一步看预防维修从经济上分析是否合理,如果经济上不如做改善或者事后处理,则不必采取所推荐的策略。
如果经济上是合算的,则采取预防维修策略。RCM的逻辑决断图多而复杂,但综观各类RCM逻辑决断图,其本质不外乎我们总结出的如下简单形式的RCM逻辑决断图,如图59-3所示。
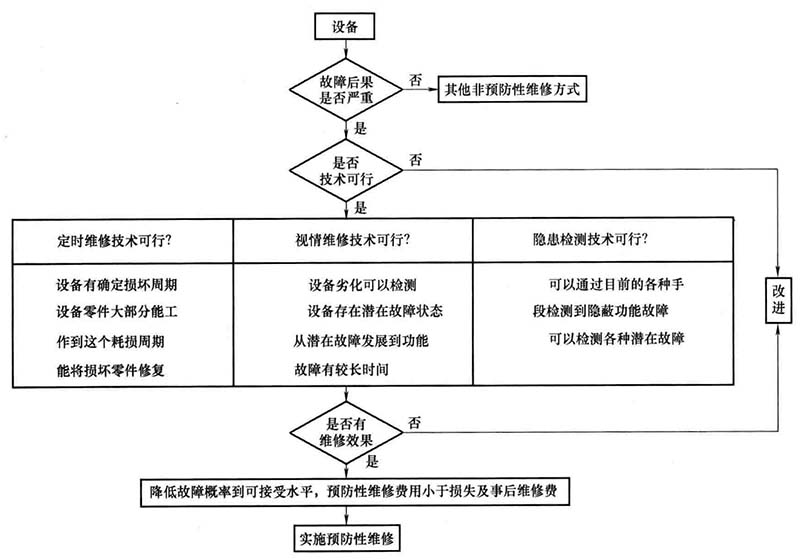
图59-3 简单形式的RCM逻辑决断图
图中隐患检测包括两种情况,一种是设备某种功能平时是工作的,但我们很难知道设备是否工作,例如烟火传感报警装置,平时是工作的,但我们并不知道是否正常,需要通过某些方法检测出其是否工作;另外一种是平时不工作,但需要其工作时却不能保证其是否工作,例如灭火的自动喷淋装置或者设备的备用泵,平时不工作,但真正需要其工作又不知能否发挥作用。这也需要有检测手段和方法将其隐蔽故障检测出来。
返回目录