《厂长经理的设备管理课》
主讲/辛巧娟
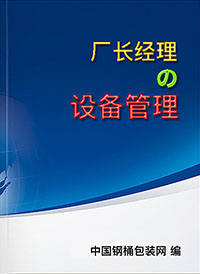
第二十五讲
精益生产和精益维修
最早的精益生产来源于日本丰田大野耐一等研究和实践的成果。其中有两大要点, 一是准时化;二是人性化的自动化(并非纯粹设备的自动化),称为TPS,即丰田生产体系。其简单描述是:根据订单,通过看板传递信息,后拉式组织生产,力争将中间库存不断降低,追求零库存管理。也就是说企业没有中间库,没有最终库,接到订单后逆推到每一道工序,直到第一道工序。美国人称之为JIT(Just In Time)即准时化生产。JIT又称为适时生产,就是在适当的时候生产出适当的中间或最终产品。后来麻省理工学院的学者将这种生产方式总结提炼为Lean Production,一般翻译成精益生产,也有翻译成精实生产的。
显然,这种后拉式生产组织模式可以减少流动资金占有、减少库存、降低市场变化风险,但却对管理提出更高要求和挑战。精益生产要求设备随时待命,有更高的可用性,更低的故障率、设备管理组织需要有更快的应变能力,可以更迅速地解决现场问题。在这样的前提下,国际一些企业提出精益维修管理问题。所谓的精益维修,就是让维修适应精益生产的要求,是对传统维修管理的挑战,是更高水平、更精准的维修管理体制。
在当今世界,很多企业为了能够应付激烈竞争的局面,要不断增加利润。降低成本成为实现这一目标的重要而且简洁的手段。然而,连续降低成本也出现了一些负面的效果。于是不少企业开始探索精益生产的方式,与此对应的精益维修就应运而生。
在精益领域的维修就是关注价值的维修管理。
1)从成本的思维转换成价值思维——传统维修预算的关注点主要是降低成本,但要看到它能够给组织或者客户创造多少价值这一积极的一面。
2)强化维修组织——精益维修组织要为客户创造附加值,是客户的重要合作伙伴。
3)为产能提升做出贡献——精益维修通过精益文化和工具的导入提升设备可靠性,减少停机损失,为产能和效益提升做出贡献。
4)以少得多——通过良好精益思想和工具应用,可以利用较少设备生产更多产品,以优秀备件管理,降低库存。
5)简化工作——通过知识共有化,包括维修任务的描述、管理流程计划、工具的运用来简化工作。
关键的精益要素可以使组织效率改善,并保持持续的进步。它不仅是为了堵住漏洞、解决问题,达到某种数量的下降,而且让我们的工作得到增值。其要素包含:
1)在客户眼里,增加价值与无价值的比例不断改善。
2)要了解精益的相关原则。
3)选择正确的工具。
4)持续改善的理念。
5)营造改善的文化基础。
没有做过精益生产的人往往很难发现改善点,因为这些都是生产系统的固有内容,大家一直都是这么做的。另外的原四是改善项目更关注于以往正在进行的流程,看如何改善并使之创造增值,而非从大系统的角度看正在做的事情是否有价值。
精益生产要从文化上引导企业,其关键点是:
1)价值流——业务流程。
2)减少浪费——增加有附加值的任务。
3)流程——按照客户要求方向进步。
4)后拉式——满足客户实际而非预想的需求。
5)完善——创造持续改善文化。
另外一个关键要素是选择正确的工具。虽然没有确定的工具清单,其实很多工具都可以应用,如企业的有氧活动(CPS+OPL)等。
精益生产是没有终点的旅程,一旦停下来就可能被其他企业超越,所以要不断培训员工,不断学习新的东西。
精益生产也是以文化为基础的,因为以前的很多改善是专注于设备和流程控制,但其中60%~80%的原因却是来自人的因素——文化。也不限于管理上的或是现场操作层面上的,而是所有层面上的制度和行为。这往往是很难改变的,需要不断地从基础、领导、制度、参与和评价等方面坚持下去。
如何成为一个精益维修组织呢?首先要选择正确的工作项目;还要选择和培训恰当的人;要应用准确的路线图和工具,并提供有效的管理支持,旨在实现预期的结果。
选择正确的工作项:项目要与组织目标相关联,要确保项目可以获益,要将项目按照价值、资源需求和时间排出优先序,而且选择项目的关键管理要素,项目要关注“浪费”问题。
选择和培训恰当的人:要保证正确的领导和参与者,选择可以改善的合适人选,建立精益的支持团队,保证足够的培训和改善时间,而且要保证恰当的资源支持到位。
应用准确的路线图和工具:这些内容包括价值流图、标准化、纠错防错设计、快速改善流程以及精益矩阵等。
提供有效的管理支持:要经常性地进步评价,不断清除障碍,持续地沟通,评价要与绩效管理——个人KPI(Key Performance Indicator——关健绩效指标法)挂钩。
实现预期的结果:要推进有效的控制计划,专注过程的常规培训,每季度评价系统效率,持续识别和开发新项目等。
经常出现的主要障碍表现为人们的短期观念,以技术改造为借口,过于关注设备硬件,忽视软环境、缺乏激情以及没有愿景等。
成为精益维修组织的关键因素是人的行为和态度——文化。首先要详细、准确地描述什么是正确的行为,要能够度量这些行为,要让大家看到正反两方面的结果差异,得到大家的晌应。为此,需要投入一定时间来纠正人的态度,人们是否主动?是否一起进步?怎么做更好?
精益维修组织的另外特征是具有精湛的诊断和维修技术。维修组织不是总在忙忙乱乱。要能够不断找出问题的源头,解决未来的问题。企业要不断培训顷工掌握诊断知识,不断告诉团队如何积累经验。
激情是行动的词汇而非仅仅代表情感。精益团队的领导应该是具有激情的领导,是工作的典范,每天都创造价值,每天都有勇气,每天都乐观,每天都是优秀的沟通者。
广义的精益维修是个三维的概念,它体现在以下方面。
1、从设备整个生命周期上寻求精益
在设备整个生命周期管理的各个环节,包括设备规划、选型、招标投标决策、安装、使用、维护、修理、改造、淘汰都存在降低浪费和创造增值的空间,都可以寻求精益。
2、从维修管理流程上寻求精益
维修管理流程实际上就是从维修策略制定、信息采集、故障诊断、维修组织设计、维修资源配置、维修流程、维修技术和验收标准,还包括设备管理KPI评价以及激励等全过程,这也是PDCA循环在设备管理逻辑轴上的延伸。每个环节都存在精益的内容。例如,不向的策略,其投入产出比不同,不同的维修组织结构和维修资源配置会产生不同的维修成本;不同的KPI评价引导不同的结果。
3、从资源要素上寻求精益
资源是维修效果的保证。维修资源包括维修设备、备件、材料、能源、技术服务、信息、人工、知识、关系等。合理地配置不同的维修资源,充分发挥企业内部维修资源的效率,挖掘维修资源的价值,也是精益维修的重要任务。例如,备件库存的优化可以在保证检修的前提下使维修备件库存和流动资金占有最小化;有效地将企业内部员工自主维护、外部合同化维修与企业内部专业维修队伍合理搭配,可以使维修成本最小化,维修效率最大化;做好维修知识资产的发掘、储存、分享、标准化和培训,可以大大提升管理效率,减少重复性差错,提升维修组织的整体水平, 其整体架构如图25-1所示。
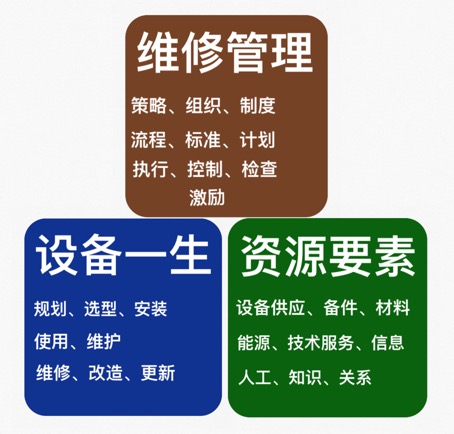
图25-1 精益维修架构
返回目录