《安全生产及事故案例分析》
杨文亮 辛巧娟 编著
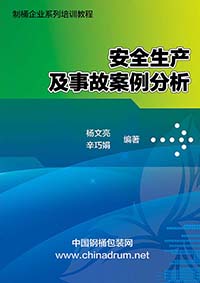
下篇 典型安全事故案例分析
第一章 生产过程安全事故案例
案例4:违章操作卷板机断臂事故
2004年10月10日,西北某制桶厂一名女工在生产过程中,严重违反安全规定,戴手套进行操作,不幸被旋转的钢辊卷入,造成右手手臂被夹断事故。
1、事故经过
10月10日13日15分许,某制桶厂女工李某,操作钢桶卷板机,将剪好的桶身平板料送入卷板机压辊中,卷成圆筒形,交下道工序进行缝焊。工作时,要求她在每张钢板送入前,必须用抹布先将钢板上的磨边铁屑擦掉,然后才由机器自动送料机自动送入卷板机。当一张刚擦完的钢板头部送入卷板机上下辊之间时,她突然发现钢板上的铁屑还没擦拭干净,于是又伸出手迅速擦掉。但由于太过慌忙,手中的抹布头被夹在钢板和钢辊之间,她急拽抹布时,手套也随抹布卷入到钢辊中,右手腕部被旋转的钢辊夹住、卷入,右手腕当即被夹断,右臂尺骨、桡骨外露2/3,皮肤肌肉脱套,无法再植,后将右小臂截去2/3。
2、事故分析
造成这起事故的直接原因,是操作者严重违反安全规定戴手套操作。此外,在未停机的情况下擦拭已进入机器卷圆的钢板,能省时省力,但不值得提倡,尤其对于行动不够敏捷、缺乏经验的新工人来讲,更不应该提倡这种操作方式。造成事故的间接原因:一是安全生产管理不严格,制度不健全,只顾生产经营,放松了安全管理工作,检查督促不够。二是作业环境较差,或者钢板边缘过于锋利,不戴手套害怕伤手。但由于卷板机的上料是自动的,完全用不着用手去接触钢板边缘。
3、事故教训
在卷板机安全操作规程中,特别重要的一条就是要求操作者必须穿紧身工作服,袖口不能敞开,长发要戴防护帽,操作时不能戴手套。为什么不能戴手套操作?其原因是戴上手套后容易被旋转的机械卷入,造成伤害。这种规定属于常识性和硬性规定,不能有丝毫的通融,没有任何回旋余地,而是必须遵守的规定。在这个事故案例中,操作者为什么要戴手套操作呢?一是怕伤手,二是有侥幸心理。应该注意的是,这种违章行为可能是习惯性违章,以往车间领导和安全管理人员发现后未及时纠正,并且安全教育也不够。
4、防范措施
(1)各级领导和全体职工,要吸取此次事故教训,增强安全意识,牢固树立“安全第一”的思想,加强对安全生产的领导,查找管理漏洞,严格考核,落实安全生产规章制度。
(2)组织好安全日活动,坚持进行三级安全教育,补课、建卡,对职工进行《安全操作规程》的学习和考试。
(3)开展“我要安全”活动,学习岗位安全操作规程,严格管理,制止违章。合理使用劳保用品,为安全生产创造良好的环境和条件。
案例5:故障不停机造成断指事故
1、事故经过
2008年10月21日15时25分左右,华中某制桶厂小桶车间检验工王某进行渗漏检验作业时,输送线上的链条突然停止了运行,他看到输送线对面的检查口处链条下卡了一块抹布,阻碍了链条的运行,于是准备到检查口检查。此时上道工序的操作工发现传动皮带不轮,以为皮带打滑,就用手使劲搬动了一下皮带轮,于是皮带轮立即转动。此时王某正走到设备对面,左手伸入链条处抓住被卡住的抹布往外拉,由于皮带突然转动,使链条卡着抹布向前移动,结果王某左手被挤在链条与护板之间,造成左手中指、无名指骨折,小指粉碎性骨折,左手小指从掌部截去。
2、事故分析
在这起事故中,事故发生的主要原因是两名作业人员之间配合不够,一人前去检查,另一人却对此不知,由此而造成事故。所以,当两人同时操作时,有必要采取安全互保制度,相互之间进行配合,防止错误操作造成伤害。有些企业在几名职工共同作业时,实施安全互保制度,相互帮助相互关照,防止有人错误操作造成意外伤害。这种安全互保制度在电工作业中实行比较普遍,也取得了明显的效果,值得推广和提倡。
3、防范措施
应采取的防范措施,一是在共同作业中推行安全互保制度,防止相互之间配合不够而发生意外伤害。二是要加强对职工的安全教育和安全管理,严格执行规章制度和岗位操作规程,今后凡是设备出现故障,必须先停机后处理,任何人检查设备时,必须全面停机,并采取手电照明,严禁用手深入设备内检查。
案例6:地面油污引起断指事故
1、事故经过
2001年8月5日,华东某制桶厂在夜班生产中,负责操作剪板机的女工赵某跟随师傅张某操作时,要检查剪板机的下料尺寸定位情况,当时剪板机是空运行。张某正查看校验设备定位时,赵某站在剪板机旁的脚踏板上测量下料尺寸,脚下突然打滑,站立不稳,右手没能抓住送料架,却将手伸到了正在上下运行的剪板机刃口中,右手食指被剪掉两节。
2、事故分析
造成这起事故的直接原因,一是该工作区域地面上有油污,容易造成打滑。二是赵某视力不佳,在夜间工作时视力为0.6和0.7,又未戴近视镜。这两个原因相互关联,互为因果,对事故的发生都是重要因素。造成事故的间接原因,是该厂和车间对现场文明生产检查要求不细,对作业环境要求不严,未能及时消除生产岗位上存在的不安全因素,即上下岗时未按规定检查工作场地,清理油污。
3、事故教训
在设备的操作和使用上,通常在设备前设置脚踏板,其目的是为了便于操作和为了防止地上油污使人滑倒。脚踏板使用时间长了,上面会积累很厚的油污,不仅起不到原有的作用,反而会产生相反的效果,这起事故就是例证。脚踏板问题是一个小问题,往往被人们所忽略,在车间安全检查中,通常不列入安全检查的内容,但许多安全生产事故的发生就是由这样的小问题引起的。此外,对设备操作工的视力、身高都有一定的要求,视力不好,本身就不适宜进行设备操作,这起事故的发生也与操作工的视力不佳有关,企业对此应引起注意。
4、防范措施
需要采取的防范措施,一是对现场使用的脚踏板进行全面的检查,清除脚踏板上的油污,对损坏的进行修复和更换,配齐安全、可靠、适用的脚踏板。二是加强对操作工人的选择、培训工作,对那些不适合设备操作的人员,应调换其他工作。三是加强安全文明生产的管理,班前班后搞好作业现场的清理工作,车间领导、班组长以及安全管理人员要认真检查,严格考核。
案例7:违章不停机调整辊轮造成挤压事故
1、事故经过
2012年7月23日9时20分许,华中某制桶厂大桶车间封口机操作工冯某,在操作卷边封口机时,因为卷边辊轮位置不合适,想稍微调整一下,就在未停机的情况下,右手伸到辊轮下调整辊轮,被下降的辊轮挤压,造成右手中指、食指末节挤压伤,食指末节开放性骨折,中指、食指末节屈伸指肌腱断裂。
2、事故分析
造成这起事故的直接原因,是冯某违反操作规程,在设备未停机状态下,右手伸到辊轮下危险区内操作。造成事故的间接原因,一是该厂技术科对现有的安全技术操作规程制定得不细,未明确调整辊轮工装时应注意的事项,造成作业人员操作时的随意性。二是思想麻痹,疏忽大意。
3、事故教训
就这起事故而言主要是人员操作上的问题。按照通常的操作规程规定,调整辊轮等操作需要停机后进行,但是在操作中停机、开机比较麻烦,操作人员有时嫌麻烦而不停机操作,即违规操作。如何克服操作人员“嫌麻烦”的心理,保证操作人员按照安全规程操作,是安全管理、安全教育的一个重要内容。
4、防范措施
(1)加强职工的安全意识教育,教育职工遵守操作规程,切实将安全生产放在首位。在安排组织生产时,要安排车间领导负责现场安全管理工作,及时发现问题、解决问题,对现场查出的违章行为,要按规定严肃处理。
(2)技术和设备管理部门应根据目前状况,完善安全技术操作规程,包括每种设备正常工作及准备工作的动作方式,并加强现场工艺纪律的检查力度和技术资料档案的规范管理,对查出的隐患限期进行整改。
(3)强化安全生产责任制的落实,组织开展有针对性的安全检查,有计划地提高职工的操作技能。
案例8:违章操作电动葫芦造成死亡事故
1、事故经过
2015年5月4日晚8时50分许,华中某制桶厂外协汽车拉来一车制桶用钢卷板,司机要求马上卸车,要连夜出车接其它生意。当时厂里已下班,车间里没有一个工人,工人住的地方离厂里也很远。于是车间主任丰某让一个值夜班保卫科员工蔡某协助他一起卸车。当时保卫科员工蔡某在旁边观察位置,充当临时指挥。由于丰某并不是电动葫芦的操作工,操作经验不足,在操作时,由于操作失误,竟把蔡某挤在两个钢卷之间,造成颅骨骨折和严重脑挫裂伤,经抢求无效死亡。
2、事故分析
造成这起事故的直接原因,是丰某操作时,搞错了电动葫芦的运动方向,本该向右走,但他却操作了向左走的按钮,而且也没有提醒蔡某注意安全,不要站在危险的位置,结果造成伤害。造成事故的间接原因,一是车间主任在操作电动葫芦时,没有认真观察周围的状况。二是工厂和车间领导没有牢固树立“安全第一”的思想,在车间承包的环境下,安全管理上要求不严,措施不力,对职工安全教育不够。
3、事故教训
在这起事故中,涉及到对员工的安全管理与职工自身安全意识。一般来讲,操作电动葫芦看似简单,但责任却非常大,这类设备的操作,安全要求比较高,必须是定员、定岗、定设备,非本设备操作工不许操作,而且操作工必须要进行必要的培训并发操作证,才能上岗。作为车间主任,其本人安全意识差,不注意安全,发生事故的概率就会更高。
在各类事故统计中,吊装作业的事故占有相当大的比例。为了预防吊装作业发生事故,许多企业制定有吊装作业制度,并且要求吊装作业时必须有两名以上的人操作,或者临时指定一名操作工做帮手,以防止意外的发生。在这起事故中,事故的发生与车间主任单独操作,而帮手也是没有任何吊装工作经验的人,事故就难免发生。
4、防范措施
(1)加强对安全生产工作的领导,认真落实各项安全生产规章制度,抓好安全文明生产,搞好危险作业的安全监护,及时排除隐患,严格制止违章操作,杜绝重大事故发生。
(2)加强车间、班组的安全基础工作,狠抓班组建设,认真落实安全活动,树立“安全生产,人人有责”的思想,遵章守纪,切实执行班组安全生产互保公约,做到安全文明生产。
(3)要认真吸取教训,有针对性地制定吊装安全管理制度,推行吊装监护制,预防类似事故的再次发生。
案例9:违章操作冲床造成挤伤事故
1999年3月5日,华中某制桶厂冲压车间在生产过程中,一各冲压操作工在操作时,由于违章操作和疏忽大意,导致右臂粉碎性骨折和肌肉挤压伤事故。
1、事故经过
3月5日14时30分许,某制桶厂冲压车间二班职工席某等四人,按照生产任务,操作160T冲床加工200升钢桶底盖,席某负责上、下料等辅助工作。由于冲床东侧台面上桶盖垛推放过高,席某在另一位冲压工右侧捅模具底板废料时,不慎将右臂搭在冲床旁桶盖料垛边缘处,此时滑块下行,使其右臂挤在滑块与料垛之间,导致右臂粉碎生骨折和肌肉挤压伤事故。
2、事故分析
造成这起事故的直接原因,是操作工安全意识不强,违反冲压工安全操作规程有关“滑块未停前,头、手严禁伸入危险部位和上、下模之间”的规定,在滑块未停止运行的情况下,右壁进入危险区清理废料。造成事故的间接原因,一是多人共同操作分工不明确,相互配合不当。二是生产现场物料堆放混乱,不利于操作工观察周围环境,操作不便。
3、事故教训
要实现冲压作业的安全,需要做好两个方面的工作:一是必须在危险区域装有安全防护装置,如安全启动装置、机械防护装置、自动保护装置等。二是严格操作规程,操作人员必须按操作规程操作。在这起事故中,事故的性质属于操作事故,事故发生的主要原因是违反操作规程和疏忽大意,同时多人共同操作相互配合不当。如果从另外一个方面来认识这起事故,即从事故发生时间和事故发生原因分析,堆积大量物料之后不进行清除还要连续作业,这与安全意识有关,与习惯性操作方法有关。实际上在堆积大量物料之后,操作人员应该意识到应停机清理,既方便操作又清除隐患,之所以不停机清理,根本上还是安全管理、安全教育不到位,企业应加强这方面的工作。
4、防范措施
(1)认真吸取事故教训,加强安全管理和安全教育,加大作业现场安全检查和考核力度,进一步结合实际强化职工安全意识,切实提高整体安全素质和自我保护能力。
(2)多人操作时应明确分工、协调配合,统一指挥并有一人负责安全。
(3)冲床工作台面只允许单侧垛料,高度不允许超过工作台240mm,清理废料时严禁将头、手伸入危险部位;冲压废料堆积时应及时清理。
【返回目录】