《安全生产及事故案例分析》
杨文亮 辛巧娟 编著
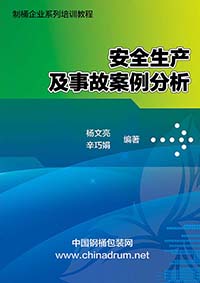
下篇 典型安全事故案例分析
第一章 生产过程安全事故案例
案例15:吊运钢板滑落造成重伤事故
2002年1月12日,华中某制桶厂制桶车间在生产过程中,一名卷板机操作工在吊运一摞桶身钢板到卷板机上料架过程中,由于钢板突然倾倒滑落,造成一名工人被钢板铲脚骨折(后截肢)事故。
1、事故经过
1月12日10时45分许,某制桶厂制桶车间在生产过程中,卷板机操作工张某吊运一摞钢板料(200张1mm厚的桶身料为一摞,重2.5T),为桶身卷圆加工做准备工作。张某在吊运过程中,因钢丝绳被挤住,就叫旁边的点焊工高某(男,29岁)帮忙,高某手持撬杠将钢板撬开,张某抽出钢丝绳,此时上部钢板突然倾斜,致使上层10多张钢板滑落砍在高某的右脚上,造成高某右脚踝关节开放性骨折、脱位(后截肢)。
2、事故分析
造成这起事故的直接原因,是操作工张某安全意识淡薄,在钢丝绳固定钢板不平衡不稳的情况下吊运,致使钢板倾斜滑落伤人。造成事故的间接原因,一是公司技术部门对钢板加工的准备阶段未设计采用专用吊装器具,造成操作工随意吊装待加工件。二是车间及班组的岗位安全教育针对性不强,生产作业现场的安全管理及预防事故发生的具体防范措施不到位。
3、事故教训
这起事故的发生有两个方面的原因,一是操作者的原因,二是本质安全方面的原因。就操作者方面的原因来讲,事故的发生具有偶然性(钢板倾斜滑落伤人);就本质安全方面的原因来讲,事故的发生具有一定的必然性,也就是说,只要钢板倾斜的危险存在,事故伤人的情况就会发生。因此,在安全生产管理上,应注意检查工艺规程是否存在问题,工艺规程是否存在不完善之处,这对于提高安全生产的可靠程度具有积极的意义。
4、防范措施
(1)公司安全管理部门要针对全厂操作人员起吊物料的情况,认真组织开展起重工专业培训,并登记建档。
(2)认真吸取事故教训,在全厂进行一次工艺规程大检查,对查出的隐患立即采取措施,制定计划全面完善生产加工工艺规程并落实整改。
(3)加强生产现场安全管理,开展有针对性的安全教育,提高职工安全意识和自我保护能力。
案例16:压力机故障造成伤害事故
2003年1月4日,华中某制桶厂冲压车间在生产过程中,一名冲压工在操作120T压力机时,压力机突然发生故障连车,造成该冲压工左手开放性骨折事故。
1、事故经过
1月4日19时10分许,某制桶厂冲压车间在生产过程中,冲压工翟某在操作120T压力机,加工钢桶桶顶底时,左手伸入上下模危险区取工件时,压力机突然发生故障连车,翟某左手回抽不及,被下行模具压伤,造成左手第2、3、4掌骨开放性骨折。
2、事故分析
造成这起事故的直接原因有两个:一是桶底顶生产加工工艺设计采取的安全辅助工具(夹钳),未在实际生产作业过程中加以落实执行,致使操作工人长期用手进入上下模危险区卸装工件。二是冲压设备因电磁阀压簧断裂造成气阀未能复位,离合器不能脱离而发生连车故障。造成事故的间接原因,则是该厂对120T压力机存在的连车故障未采取针对性的计划维修措施,未强化日常的动态检查与隐患整改,致使设备带病运转。
3、事故教训
这起事故有几个教训:其一,技术部门在工艺、设备管理方面还存在漏洞,未设计提供安全可靠的作业条件,对特种危险设备存在隐患没有采取科学、有效的超前预测、预防,控制防范措施还落实不够、不到位。其二,设备管理部门的安全责任落实不够,采取安全防范措施不力,特别是对危险点(此压力机为A级控制点)管理控制针对性不强、措施不力,日常的动态监控和隐患整改未认真落实到位。其三,冲压车间贯彻落实“五同时”不够,对生产作业过程中出现的不安全因素未采取积极措施予以处理。
4、防范措施
(1)通过事故教训,强化各车间各部门安全生产责任制的落实,认真贯彻落实安全生产“五同时”,根据本单位生产加工特点和设备状况,举一反三,组织开展一次工艺安全大检查,重点排查工艺安全技术条件、规程、措施的制定及贯彻落实到位情况,对查出的问题要认真分析、研究,落实责任采取强有力的整改措施予以解决。
(2)设备、安全等职能部门要严格贯彻危险点管理规定,会同有关生产车间对特种危险设备必须定期进行故障类型分析,对存在的不安全因素要采取针对性的安全防范措施,落实责任,予以解决。设备部门要强化设备的计划维修及隐患整改工作,进行科学、有效的管理。安全部门要加大监督检查力度,严格考核,确保设备设施的本质安全和操作人员的生命安全。
(3)应结合安全检查工作,加大力度,把必要可行的事故预防控制措施落实到生产过程的每一个环节中去,特别要突出抓好特殊危险作业的管理,对从事特殊危险作业的职工要进行认真细致的安全技术教育,提高全员的安全意识、素质和自我保护能力,坚决杜绝类似重伤事故的再次发生。
案例17:冲床电气故障导致人身伤害事故
2001年8月8日,西北某制桶厂二车间一名冲压工,在操作压力机加工200升开口钢桶桶盖过程中,由于压力机电气控制故障导致误动作,上滑块突然下落,造成右手手掌离断事故。
1、事故经过
8月8日9时45分许,某制桶厂二车间冲压工陈某(女,36岁),在与同组冲压工丁某操作160T压力机,加工200升开口钢桶桶盖过程中,由于压力机电气控制故障导致误动作,上滑块突然下落,将正在操作中取工件的陈某右手挤压在上、下模之间,造成右手手掌离断。
2、事故分析
造成这起事故的直接原因,是该厂设备管理部门疏于日常检查和管理,特别是对生产车间重点危险设备的计划维修、使用情况及存在的问题缺乏检查,监控不力,致使维修管理出现漏洞,造成压力机在生产过程中由于电气控制故障导致误动作。造成事故的间接原因,一是技术科工艺制度管理方面存在较大漏洞,未严格执行工艺文件及工艺纪律,缺乏对作业现场的工艺检查,未给操作人员提供安全可靠的作业条件。二是生产车间对设备在工作中存在的故障未认真进行分析和采取有效的维修措施予以处理,致使设备带病运转。
3、事故教训
事故的发生,通常是由几个因素共同作用的结果,这起事故也不例外。值得注意的是,造成事故的其中一个原因是“设备带病运行”,这对于冲压设备来讲是一个大问题。按照原国家机械工业委员会颁布的《冲压安全管理规程》规定,发生下列情况时,要停机检查修理:
(1)听到设备有不正常的敲击声。
(2)在单次行程操作时,发现有连冲现象。
(3)坯料卡死在冲模上,或发现废品。
(4)照明熄灭。
(5)安全防护装置不正常。
造成事故的冲压设备究竟如何带病运行,未交代清楚,我们不得而知,但是对于冲压设备这样危险性高的设备,只要发现运行不正常,就应该停机检查修理,绝不能带病运行,否则会造成事故的发生。这应该作为企业的一条硬性规定坚决执行,绝不能有任何的马虎。
4、防范措施
(1)应吸取这起事故教训,针对生产工艺认真组织有关人员全面排查整改,完善工艺安全技术条件并落实到操作岗位,强化工艺纪律检查和管理。对所查出的问题要认真分析研究、落实责任,采取强有力的措施予以解决。
(1)应进一步加强对设备、设施的管理,认真履行设备管理部门职责,完善安全管理制度及检查制度,强化对设备、设施的日常监督检查与考核,并针对这起事故反映出电气控制系统短路及设计缺陷进行整改。
(2)生产车间应认真落实安全管理责任,进一步加强设备的维修管理工作,认真贯彻“五同时”,落实安全生产责任制,加强职工的自我防护意识,强化作业现场的安全管理。
案例18:设计缺陷导致天车撞人事故
2007年5月25日,华东某制桶厂冲压车间下料班两名天车职工违章在天车上交接班,由于天车存在设计缺陷警铃不响,新接班的天车司机启动天车后,将换班的司机挤在厂房立柱上造成死亡事故。
1、事故经过
5月25日上午,天车司机裴某、计某二人按正常班次上班。先由计某上新的10T天车作业。9时30分,按规定由裴某换计某下车休息,两人在天车上配电柜旁碰面进行交接。交接后裴某进入驾驶室,他误以为计某已下到地面便贸然启动天车。天车刚一启动,裴某即感觉到天车运行有阻力,立即停车走出驾驶室查看,发现计某被天车端部挤贴在厂房立柱上,重又返回驾驶室倒回天车,并喊人一道将计某架到地面;同时向车间、厂部汇报。工厂领导闻讯立即赶往出事地点,将计某送往医院抢救,但因伤势过重抢救无效,于10时左右死亡。
2、事故分析
造成这起事故的直接原因,是裴某、计某在操作中违反安全操作规程规定,在天车上交接班,是习惯性违章造成的事故。造成事故的间接原因,一是天车登梯设计存在缺陷,警铃不响,又没有其他提醒装置,导致接班司机贸然开动天车。二是安全管理工作存在漏洞,执行管理规章制度不严格,监督检查流于形式,对类似于操作工长期违章在空中交接班问题熟视无睹,制止不力,处理不严,导致少数职工安全意识淡薄。
3、事故教训
这起事故的发生有直接与间接两个方面的原因,在这两个原因中,虽然造成事故的直接原因是违反操作规程,在天车上交接班,但是应引起注意的是天车登梯设计上存在的缺陷。这种设备和技术上存在的缺陷,对于导致事故的发生可能更为重要,它属于非本质安全因素。只要这种设备和技术上的缺陷存在,这种非本质安全因素就存在,就有导致事故发生的可能。因此,消除设备和技术上的缺陷,消除非本质安全因素,才能更加有效地防范事故的再次发生。
4、防范措施
事故发生后,该厂根据生产特点和实际情况,采取积极的防范措施:一是以健全安全生产责任制为重点,重新制定和完善了各项安全生产规章制度,并组织职工学习;二是根据厂房的实际情况,重新设计安装登梯和警铃;三是加强对特殊工种和重点岗位人员的安全培训,做到持证上岗,并重申安全操作规程,以增强职工的安全意识和遵章守纪的自觉性。
案例19:输送机防护不周造成断指事故
2005年3月24日,华南某制桶厂小桶车间,发生一起由于违章操作和皮带输送机防护不周密,导致操作工左手三指轧伤的事故。
1、事故经过
3月24日17时许,该厂小桶车间(生产18升方便桶)准备开工。按照车间要求,设备在下班前必须清理皮带输送机及设备周围的杂物,班长高某带领另一人在清理皮带机时,为求方便快捷,由高某启动了皮带机,2人分别进行清理。高某在清理时发现原固定皮带机支架的铁丝脱落在皮带上,觉得有碍皮带机传输,探身准备用右手检拾时,左手手套不慎被传动的齿轮挂住并连同食指、中指、无名指卷入齿轮,将这三指第一节轧伤。
2、事故分析
造成这起事故的直接原因,是操作工在清理封口机旁皮带输送机杂物时,启动皮带机进行清理,这是典型的违章操作。造成事故的间接原因,一是安全护罩配备不齐,该车间针对制桶生产线皮带输送机多的特点,在各传动装置上99%的地方增设了防护罩,唯独这个设备多、环境差的地方没配置,恰恰就在这里出了事故。二是安全教育不到位,操作工安全意识差,而且对习惯性违章纠正不力。
3、事故教训
事故发生后,经调查了解,事故当事人高某自2001年底到公司做工以来,没有接受过正规安全培训、教育,仅仅到有关部门办理了证件后,便安排到操作岗位,而且车间也没有进行安全教育,车间领导只是在作业现场强调了安全注意事项,指定应完成的任务即上了岗。由于安全意识的欠缺和安全技术的不足,加之管理上的脱节,操作人员具有习惯性违章行为,并因习惯性违章而没有发生事故形成侥幸心理。正是在这种侥幸心理的作用下麻痹大意、忽视安全、不遵守操作规程而导致事故。
4、防范措施
(1)加强安全教育,消除安全“死角”。首先针对目前在岗的所有工人进行安全意识、安全技能培训教育;其次责令各新进的工人,必须先到安全部门进行安全培训,然后到车间、班组接受安全教育。
(2)重新完善防护罩。对于锈蚀严重、不规范的全部整改。
(3)加强安全监管。车间、安全部门经常抽查工作场所,督促工人自觉遵章守纪,做到“三不伤害”。
【返回目录】