冲压操作易发生伤人事故的原因分析
文/三哥
冲床之所以多发生伤人事故, 主要是由于冲床生产的特点是工序简单、速度快,滑块往返运动一次就能完成一个工序或一个零件,一个工作班一台机床可以完成数千到数万个工序或零件。
直到现在,绝大多数企业仍为手工进行送料、排样落料、取件、清除废料等工作。 操作者要快速单调地重复 “上料(或排样定位 )→启动滑块冲压→卸件→清除废料→上料 (或排样定位 )→⋯⋯”动作,这些动作的配合顺序需要准确无误,稍有不慎,就会造成设备或人身事故。
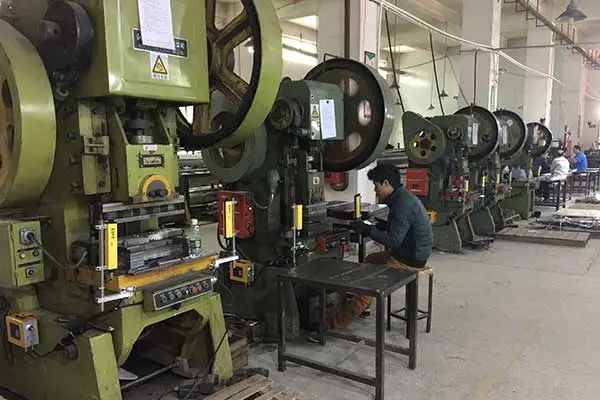
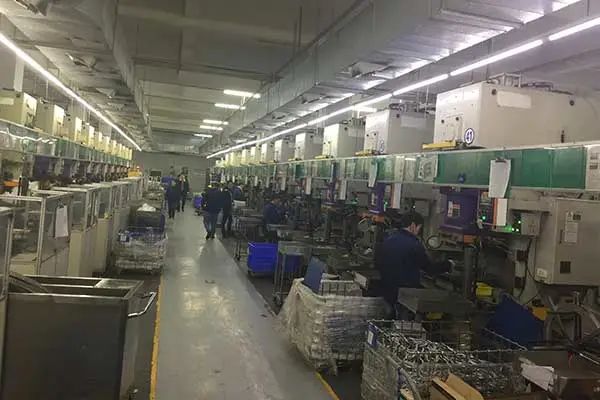
根据人机工程学和行为科学、心理学所揭示的规律,人在长时间从事这种在极为嘈杂的环境中进行快速而又简单重复的作业动作时, 极易产生机体疲劳、神情恍惚、反应迟缓现象,导致注意力不能集中,动作失调。万一出错,惨剧便在瞬间发生。据统计资料显示,在冲压过程中发生的伤害事故, 多数发生在长时间加班或周一及周末思想较分散的时候。
另外,对于 16 吨以下的小型冲床来说,其运动速度远远大于人的反应速度,是造成事故的又一个原因。 即便在注意力高度集中的状态下,要想将手作出移动几厘米的动作,也需要 0.3~0.4秒,而这段时间已超过滑块从上死点到下死点的时间。 也就是说,即便在头脑清醒的情况下,若手在模内时意识到误启动了滑块,也来不及将手撤出危险区。
也就是说,冲床,尤其是小型冲床的工作性质,超出了人的生理极限。这种在冲压过程中发生的伤害事故, 约占冲压伤害事故的 55%~60%。
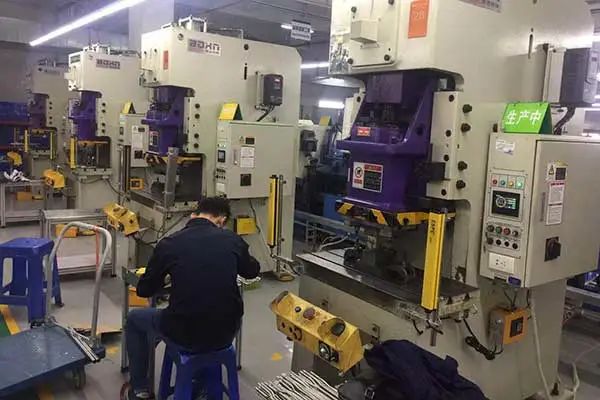
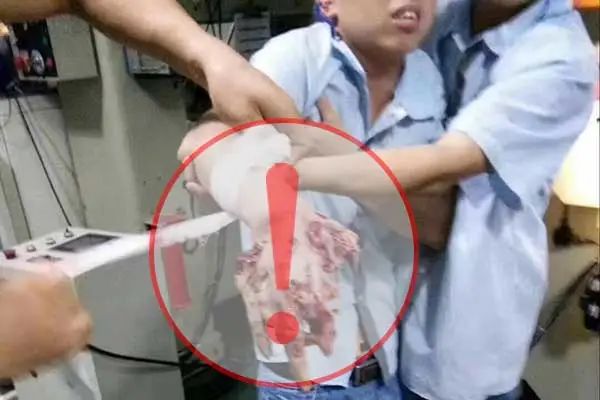
曾有人根据冲床的运行规律和人机工程学原理,计算得出,在正常管理的情况下,冲压过程中发生人身事故的几率,约为千万分之 2.73,也就是说,假如每小时冲压 500次,每天实际冲压 6 小时,每年工作 250天,大约三年左右发生一次人身事故。
对比媒体上所报道的情况, 现在多数厂家的事故率远远高于这个几率,说明这些单位的安全管理较差,而且冲压操作的负荷率较高;而前面提到的那个军工企业在 20 年前的事故率,远远低于上面计算得出的数据,则是除了当时管理严格之外,其冲床的实际冲压负荷率也远远低于我们上面所假定的数据。
随着近年来国家对民营企业安全问题的关注。相关安检部门对冲床设备没有安装红外保护装置,安全光栅(安全光幕)的企业采取相应的强制措施,直到安装了安全光栅才能恢复正常生产。安全光栅(安全光幕)是通过一种看不见红外线来保护作业员的操作安全,是在一种不没影响作业员生产或作业的前提下保护作业员的人身安全。
|