涂装锆化前处理生产线的设计,质量缺陷及产生原因
文/郑福斌,苏和,龙庆,陀家晖,李业红
摘要:锆化前处理作为一种新型的环保前处理材料,引领了涂装行业的前处理变革。本文结合锆化前处理的应用实绩,对涂装锆化工艺设计过程中工艺设备的选择提供了参考。关键词:锆化;磷化;前处理
0 引言
涂装前处理工艺通常包括了预水洗、预脱脂、脱脂、水洗、化成(磷化、锆化或硅烷等),水纯水洗等,其中最重要的工艺为化成工艺,化成膜可以提高产品的漆面附着力和耐腐蚀性能。
在前处理化成工艺中,磷化处理已经广泛使用近百年,经过了几代产品的改进,具有结晶致密,与涂装匹配抗腐蚀性好的特点,但也存在一些缺点:
1)环保性差。磷化主剂中成膜物质磷酸根和促进晶核生成的镍离子均为废水排放中第一类限制浓度排放污染物;同时大多数磷化工艺使用亚硝酸钠促进剂,它被列为有毒物质,具有剧烈刺激性,且对水生物有害。
2)磷化渣难处理。磷化成膜过程中,产生较多的渣,通常需要投入大量的设备,如PS过滤器、FK过滤机等进行处理,如果未及时处理挂附在产品表面,影响涂装品质。为适应环保和行业的发展,无磷前处理(硅烷或锆化等)的应用是发展趋势。2000年左右硅烷或锆化材料开始在欧美企业使用,国内企业2010年左右开始试用,2015年开始生产使用,目前已经是涂装前处理工艺的首选。本文结合锆化前处理生产线的建设及生产应用实绩,为涂装前处理生产线设计提供一定的参考。
1 锆化生产线工艺设计
锆化工艺与传统磷化工艺具有明显的区别,因此在生产线的设计时不能直接使用磷化工艺的前处理设计,需要根据锆化工艺本身的特点进行合理布局,常见的生产线工艺流程见表1。
表1 锆化前处理生产线工艺流程
序号
|
工序
|
处理方法/时间
|
处理介质
|
备注
|
1
|
预清洗
|
洪流半浸泡60s
|
工水
|
排放废水
|
2
|
预脱脂 |
喷淋60s |
脱脂剂 |
|
3
|
脱脂
|
全浸泡120-180s
|
脱脂剂
|
|
4
|
第1水洗
|
喷淋30s
|
工水
|
溢流至预水洗
|
5
|
第2水洗
|
喷淋30s
|
工水
|
溢流至水洗1
|
6
|
第3水洗
|
全浸泡入/出 |
纯水
|
溢流至水洗2
|
7
|
锆化
|
全浸包90-120s
|
锆化液
|
|
8
|
第4水洗
|
喷淋30s
|
纯水
|
排放废水 |
9
|
第5水洗
|
全浸泡入/出
|
纯水
|
溢流至水洗4
|
10
|
第6水洗
|
喷淋30s |
纯水
|
|
11
|
沥干
|
雾化喷淋 |
纯水 |
|
1.1 脱脂工艺设计
脱脂的主要目的是消除产品内外表面上各种油污(如拉伸油、防锈油等)和尘埃,达到产品表面水膜完整的状态。锆化前处理工艺与磷化前处理工艺不同在于:三元系磷化膜厚度在2-3微米,锆盐转化膜膜厚在20-50微米,如果脱脂不干净,锆化将无法成膜且产品更容易生锈,即使后续有砘化膜,未上锆化膜处也无附着力,存在品质风险。为了使产品有更好的脱脂效果,前处理生产设计时,应从以下几个方面考虑:
1)选择脱脂效果更好的脱脂材料;
2)通过对预水洗加热至35-40度,增加产品表面的温度,使得产品进入涂装工序后提升脱脂效果;3)预脱脂增加大流量喷淋、冲洗产品内外油污;
4)脱脂槽增加循环次数,通常设计2-3次/h;
5)脱脂处理时间延长,通常脱脂和处理时间为120s,锆化处理线设计时可以延长至150-180s;
6)槽体内增加微发泡脱脂装置或超声波处理装置,增加脱脂槽的除油效果,具体工艺对比见表2。
表2 传统磷化与锆化前脱脂工艺比较
工序
|
处理参数 |
磷化前的脂脂工艺
|
锆化前的脂脂工艺
|
预水洗
|
处理时间
|
半浸泡
|
半浸泡
|
处理温度
|
常温
|
35-45度
|
预脱脂
|
处理时间
|
30s
|
30s
|
脱脂
|
处理时间
|
120s
|
150-180s
|
处理温度
|
40-50度
|
40-50度
|
辅助装置
|
无
|
微发泡或超声波
|
1.2 锆化工艺设计
锆化工艺与磷化工艺不同,锆化处理反应速度较磷化快,沉渣量少,因此在生产线设计时设备选型与磷化不同。
1.2.1 处理时间设计
通常锆化生产线设计时,考虑锆化的耐腐蚀性能要求,通常要求冷轧板锆化膜重大于20mg/m2,经过试验数据,满足锆化膜重要求,锆化处理时间仅需60s以上,考虑产品内腔液体流动性差,通常为保证锆化膜品质,锆化槽设计时全浸泡时间取90-120s比较合理。
1.2.2 锆化处理温度设计
不同厂家的产品,锆化工艺对温度要求不同,常见的产品有加热(约38-42度)与常温(15-35度)两种产品。通过试验数据对比,常温产品在相同的浓度和不同的处理时间下对比,120s的处理时间,温度在10度以上,满足锆化膜生的品质要求。从生产线的设计及后期运行成本考虑,为节约热交换设备、锅炉加热设备投入、后期燃气的使用,锆化槽的设计时考虑处理条件为常温,选用不加热材料。
1.2.3 锆化后的处理设计
锆化反应与磷化反应不同,磷化膜在成膜晒太阳随时间的延长,磷化膜成膜后增长的速率很慢,锆化则增长的速率很快。同样的板材90s处理时间后,磷化的成膜每分钟增长速率为0.19g/m2,锆化的成膜每分钟增长速率为16.15mg/m2,锆化槽反应增长速率快于磷化,因此在锆化槽设计时出槽后不能留有过长的沥水时间,防止沥水时间过长,产品表面继续成膜,导致表面成膜不均匀形成锆化条纹。锆化出槽设计时应该按照以下设计:
1)出槽端设置锆锆化液雾化喷淋,保证产品表面锆化膜均匀,同时又能够使产品腔体里面的液体沥干;
2)产品腔体的液体沥干后,增加大流量水洗喷淋,快速冲洗产品表面,使产品表面残留锆化液清洗干净,不再继续成膜。
1.2.4 锆化除渣设备的选型
传统三元磷化反应,冷轧板产渣量约为2.7g/m2;锆化反应,冷轧板产生渣量为0.2g/m2,为磷化沉渣的1/10。
磷化槽槽液渣含量一般控制在3.0×10*-8以下,通常会通过FK过滤机、PS过滤器、斜板沉降等来处理磷化渣。锆化槽如果渣含量较多,沉渣悬浮在槽液呈泥黄色,影响锆化的品质,因此锆化槽通常控制在5.0×10*-6~1.0×10*-6以下,考虑至锆化渣含量及存在状态,在锆化除渣设备设计时,应注意:
1)锆化槽底部去除漏沉降,采用平板0.1%~0.2%斜波设计;
2)锆化槽采用全流量过滤罐过滤及板框除渣机辅助设计,过滤精度控制在5微米以下,常见设计见图7。
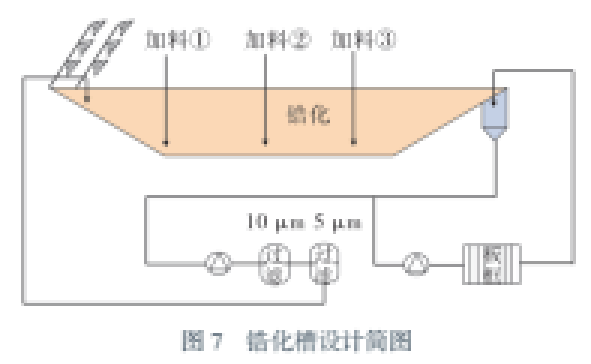
1.2.5 锆化加药管路的布局
锆化反应与磷化反应有所不同,锆化反应速率较快,且槽液浓度对锆化反应有较大的影响,因此,为避免锆化加药后产品表面反应不均匀,造成条纹及药剂的浪费,在锆化槽设计时,需要考虑加药管路的布置,通常在图7示意中:
1)3个加药管路均匀布置在槽的前、中、后位置;
2)加药管路需深入槽体底部,充分保证槽液循环,同时要防止加药管路虹吸槽液。
1.2.6 锆化后水洗槽防锈设计
锆化成膜较薄,在冷轧板的产品上,锆化部位易生锈,为保证锆化后水洗不生锈,通常设计时的锆化后的第4水洗、第5水洗设计独立的防锈剂滴回管路。
1.2.7 涂装前U段的设计
为保证涂装前产品沥水干净,通常生产线会有U段沥水或转载设计。通常U段一般2~3个产品位,产品通过时表面会有部分表干,出现干湿不均情况。磷化膜干湿不均后,涂装无明显的缺陷,但锆化膜干湿不均,涂装后会出现条纹等缺陷。锆化工艺在设计时,通常会在U段增加高压雾化喷淋设计。
1.2.8 锆化渣定期清洗设备设计
锆化渣长期会残留在管路、槽壁、输送等设备上,因此锆化槽每隔1~2天需对槽体进行清洗一次。由于锆化渣硬且不易清除,通常需要采用特殊的酸(常用硝酸混合物)进行清洗,因此在锆化槽设计时,需配置耐酸清洗泵及管路。
1.2.9 锆化槽体材质选择
锆化液作为一种酸洗表面处理药剂,pH一般在4.0~4.8左右,且槽液中含有F离子,对设备腐蚀性能较传统三元磷化高,因此,在锆化槽壁设计时,一般选择规格较高的216不锈钢板材,输送件至少也应该选择304或更高规格的不锈钢材质。
2 结语
锆化处理工艺无磷、无镍排放,同时在常温下反应,作为一种低碳、环保的前处理材料,目前在涂装行业内迅速推广应用,但前处理设计仍保留在传统磷化的理念上,本文通过对比磷化处理工艺,为新建锆化前处理生产线脱脂设备、锆化处理时间、温度、加药设备、防锈处理、除渣设备、槽体板材选择提供了依据。通过实践,新建的涂装锆化生产线,运行3年产品品质稳定,无锆化导致的品质不良,为涂装锆化前处理工艺设备选型设计提供了一定参考。
|