模具表面处理对冲压生产的影响
文/于海军
【编者按】冲压生产过程中,生产稳定性是影响生产效率和生产成本的主要问题。本文详细介绍了导致生产不稳定的主要原因中拉毛、开裂、起皱的形成原理,并对四种解决措施进行阐述。最后通过实际应用证明措施有效,为后续类似项目的整改提供有效借鉴方案。
随着钢桶工业近十年的高速发展,钢桶的质量越来越高,但价格却越来越低,因此降低钢桶生产成本是每个制桶企业迫切需要解决的问题。对于冲压专业来讲,降低成本的重要举措之一是确保生产稳定。影响生产稳定的主要原因包括冲压件的起皱、开裂、拉毛。解决这些缺陷的措施主要为进行模具的表面处理,模具的表面处理能够降低模具的表面粗糙度、提高研度,增加耐磨性。从而提高生产稳定性,降低生产成本。
一、生产不稳定因素产生原因
1、拉毛
在成形过程中板料与模具相对滑动时由于板料与模具的强制接触而发生粘着磨损导致在板料上留下条状痕迹,如图1 所示。量产—段时间后出现拉毛—般由3 点原因导致
(1) 拉延凹模圆角硬度降低与板料硬度接近导致模具与板料发生粘连。
(2) 模具或板料脏在模具与板科之间有硬质异物在相对滑动过程中划伤模具及板料。
(3) 凹模圆角破损或补焊后遗存裂纹或气孔板料流过凹模圆角时被划伤。
2、开裂
一般而言开裂可分为强度开裂、塑性开裂两种见图2 。强度开裂又称𝛂开裂是指在冲压过程中板料传力区的强度不能满足变形区所需要的变形力要求时在变形区开裂。如圆筒零件拉深成形时在凸模圆角处产生的开裂就属于强度开裂。塑性开裂又称𝛃开裂指在冲压成形过程中板料变形区的变形能力小于成形所需要的变形程度时在变形区产生的开裂。如零件拉延筋为锁死筋材料基本不流动零件通过胀形成形此种状态下的开裂属于塑性开裂)。按受力状态来分开裂有两种类型—种是受到X 和Y 两个方向拉应力导致的开裂通常为横向开裂另一种是X 和Y 两个方向上—个是拉应力另一个是压应力相邻金属晶格间相对移动过大产生的开裂,—般为纵向开裂。
3、起皱
零件在拉延或成形过程中受力状态非常复杂没有规律可循由千板料厚度与长宽两个方向相比小很多因此在受拉压应力的状态下在厚度方向上非常容易失稳导致起皱,如图3 所示。起皱可分为压应力起皱、不均匀拉应力起皱和切应力起皱。压应力起皱的特点是呈现与凹模口方向垂直—般出现在凹模口的拐角处由于收缩变形板料里的晶格在平行凹模圆角的方向受压应力压应力超过板料所能承受的极限时引发失稳起皱。不均匀拉应力起皱一般多发生在外板的平缓区域因受到的都是拉应力不会出现较大的褶皱主要表现形式是缓坑或波纹。切应力起皱的特点是起皱区域所受拉力不均相邻金属晶格流动速度不一致导致错位失稳在其作用下产生剪切应力而导致的起皱。
二、生产不稳定解决措施
为了保证生产稳定模具试生产合格及生产过程中模具表面磨损原有的工艺平衡条件被打破出现生产不稳定情况时都要对模具进行表面处理使模具达到新的稳定状态。表面处理有以下几项措施。
1、凹模圆角剖光处理
冲压生产过程中,应定期对模具进行清洁和保养去除模具表面的锌皮和油污同时检查凹模圆角的粗糙度。如发现粗糙度变差需要对凹模圆角进行剖光处理,剖光最低需选用600 - 800 目的砂纸里面垫上矩形研磨块在圆角上涂研磨膏,沿走料方向进行研磨直到粗糙度达到要求为止。
2、凹模圆角补焊处理
生产中出现较为严重的局部拉毛或起皱、开裂现象排除设备与工艺间题一般为拉延圆角磨损而导致的硬度降低到40HRC 以下,或者为拉延圆角出现裂纹、破损。解决措施是对有问题部位进行补焊处理:
(1) 补焊前先对破损部位进行清除用角磨机打掉深20mm 宽10mm 的坡口同时满足坡口的边缘要超过圆角切线点5mm 以上。
(2) 焊条材质的选择补焊—般为两层里面为填充层外面为工作层填充层的焊条选用与模具本体机枙性能基本—致尤其是硬度及冲击韧性材质可与本体不同。工作层焊条要与模具本体的互熔性好结合处必须牢固结合处避免出现裂纹及咬口现象焊接完成后,硬度应达到模具本体淬火后的硬度水平50HRC 以上。我司拉延凹模本体材料是球墨铸铁牌号为GGG70L 填充层焊条选用东海的TC-3F 工作层选用的是日亚的NH-100R 使用结果良好。
(3) 焊接过程中速度要均匀断续焊接同时焊接过程中要用锤子敲击去除焊接气孔和内应力避免因焊材温差大或内应力产生的裂纹。
(4) 焊接完成后数控加工留0.1mm 余量剩余由人工进行精研需保证维修部位与原型面衔接顺滑无起伏修完后进行精剖光保证模具的平顺度及粗糙度并最大限度的与原状态保持—致。
3、镀铬处理
电锁是在某些金属表面上镀上—薄层金属或合金的过程达到防止金属氧化提高表面硬度及粗糙度的目的—般以被锁基体金属为阴极以锁层金属为阳极通过电解使溶液中金属的阳离子在基体表面沉积形成锁层的一种表面加工方法。冲压专业的电镀,—般指的是锻硬铬主要是为了提高模具表面的硬度、耐磨度和降低表面粗糙度。电解液为铬酸溶液基体表面锁—层较厚的络锁层它的厚度—般在10 ~ 2Oμm 。
4、PPD处理
PPD 是指脉冲等离子渗氮是针对汽车覆盖件冲压模具取代电锁的一种终身抗磨损处理技术在低真空(小于2000Pa) 环境中以炉体为阳极,以被处理的金属产品为阴极通电后在两者之间产生高达几百伏电压使氮气和其他气体分子分离成氮离子氢离子和电子。氮离子开始与模具表面基体离子反应形成硬化渗氮区域。经过渗氮后模具表面形成—层极硬的合金氮化物(Fe4N, Fe2N) 渗氮层的硬度—般可达到50 - 60HRC 具有很高的表面硬度和耐磨层并且适用于大部分汽车模具所使用的铸铁、铸钢材料。
PPD 处理有很多优点:
(1) 表面可以用800# 及以上油石处理。
(2) 损伤表面可以焊接。
(3) 补焊后的表面可以接受高温热处理。热处理后的表面形状不会改变。
(4)PPD 处理后的模具—般可保证50 万冲次。
(5) PPD 处理后进行再次处理无需其他工艺处理。
(6)不污染环境。
对模具本体进行PPD 处理要满足以下几点要求:
(1) 先要将需要处理零件清理干净拆除镶块螺钉导滑板等附件。
(2)保证焊接质量不存在虚焊、焊接气孔、焊接裂纹。
(3) 在PPD 前做过其他涂层处理的需要将其退掉。
(4) 模具圆角部位表面粗糙度Ra0 2 ~ 0 4 μ m 平面区域RaO. 4 - 0. 6 μ m 。
三、表面处理应用
2018 年9 月开始生产正常的3 个项目的2 套前门内板1 套后门内板拉延模具频繁出现拉毛现象偶尔夹杂开裂、起皱。严重影响生产效率和产品—次合格率对生产的组织造成很大困扰。因此工厂立项解决此问题。经过一段时间的排查统计每批次都有不同程度停机,见表1 。
运用鱼骨图分析法将可能产生拉毛的各因素按照生产要素人、机、料、法、环的原则进行分类分别进行排查最终确定引起拉毛主要原因为模具凹模圆角经过多年生产已经磨损出现拉毛部位硬度多处低于50HRC 且有些部位出现气孔鱼骨图如图4所示。
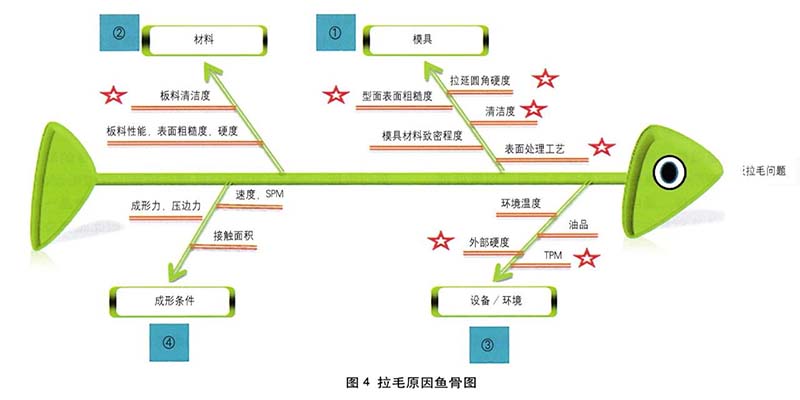
对三套模具的上模口圆角打坡口、补焊数控加工人工精修表面剖光经过3 个批次验证确认模具变更后的制件符合要求后模具补焊如图5 所示。
将项目1 前项目3 模具镀硬铬处理项目2 的前门内板模具进行PPD 处理,圆角表面硬度达到55HRC 以上粗糙度达到Ra0 2 ~ 0 4μm ,完全符合要求。表面处理完成后对此3 个项目的结果进行跟踪。整改要求符合预期解决生产稳定性问题跟踪结果见表2 。
四、结束语
通过五要素分析法找出生产不稳定的根本原因及整改方案对拉延凹模圆角进行补焊研磨用剖光模具表面进行锁硬铬或PPD 处理,使模具圆角的硬度、粗糙度都达到技术要求。在随后的生产中拉毛基本消除也未出现开裂和起皱现象。表现稳定。此次3 个项目的表面处理工艺及流程对后续类似项目有—定的借鉴意义。
|