关于冲压模具掉铁屑问题的应对措施
文/魏本华,叶立渊

前期用于手工线生产的冲压模具转到自动化线生产后,由于模具修边掉铁屑问题,导致冲压件返工和报废率一直居高不下,严重制约着我们的质量、成本和效率。为此我们成立修边掉铁屑问题技术攻关小组,对影响掉铁屑的问题开展技术攻关,取得了较好的效果。
工厂的目标是追求高质量、低成本,老生产基地冲压手工生产线的生产节拍为3 ~5spm,通过改造升级为自动化生产线后生产节拍可达到6 ~10spm,生产效率提高1 倍,同时生产运营成本也大幅地降低。但是随之而来的问题是,手工线的模具不足以支撑自动化线的生产,必须对用于手工线生产的模具进行必要的改造升级,以适应自动化封闭线的生产要求。
冲压模具掉铁屑问题
冲压手工线模具改自动化模具的重点是解决修边掉铁屑问题。因为冲压生产中出现的铁屑极易粘附在模具和零件表面(图1),进而会在制件表面压出凹痕(图2),线尾质量检测人员识别出压痕缺陷时,至少已造成7 个以上的返工或报废。不仅严重影响冲压件产品外观质量,而且增加后期运营成本。如何消除修边模具产生的铁屑,是困扰冲压生产的重大难题。我们通过对手工线模具结构的优化和改造,可以有效减少生产中产生的铁屑,冲压件表面无明显的废铁屑压伤问题。
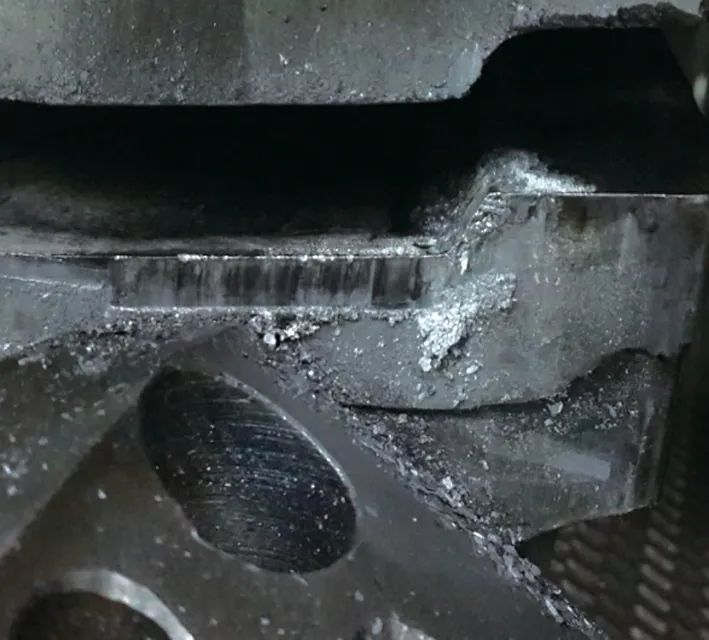
图1 下模刀块铁屑堆积
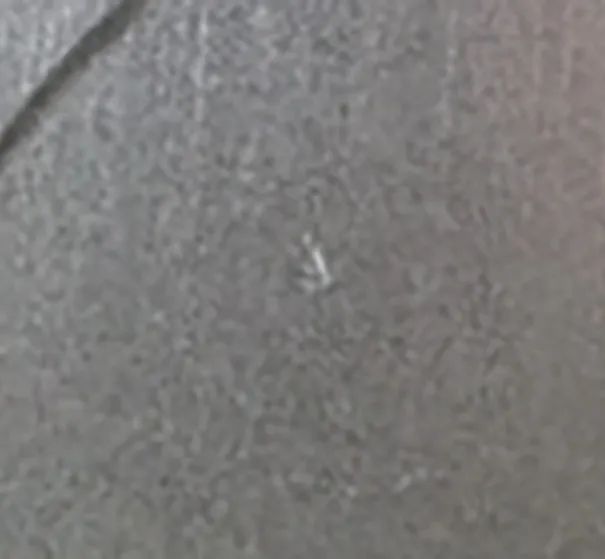
图2 冲压件外表面压伤
刃口结构的优化整改
通过对修边刀块及冲头的优化整改,使其符合标准,确保稳定生产的同时,减少铁屑产生,从根本上解决铁屑问题。⑴对直修刀块的优化改进内容包括(图3、图4):①基准面“波浪” 部位进行修顺;②刀面正锥改为90°垂直面;③刃口啃伤修复锋利;④基准面控制在10mm。
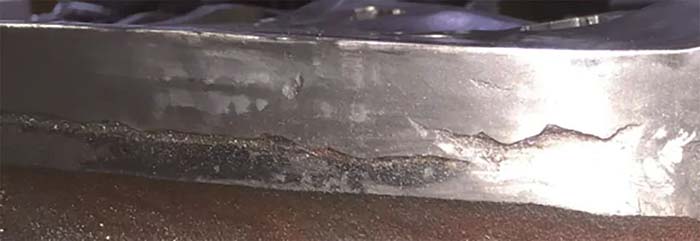
图3 直修刀块整改前
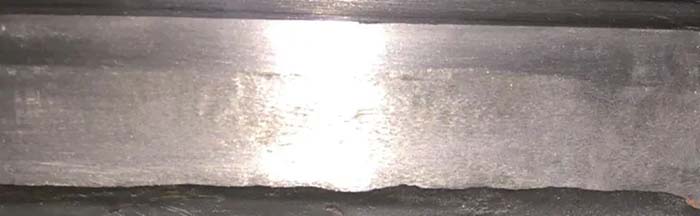
图4 直修刀块整改后
⑵对冲头的优化改进内容包括(图5、图6):①将原吃入量由10mm 改至5mm 内;②冲头上部周边刃口低、中间凸起修整至平整;③将冲头刃口和周圈推顺抛光处理。
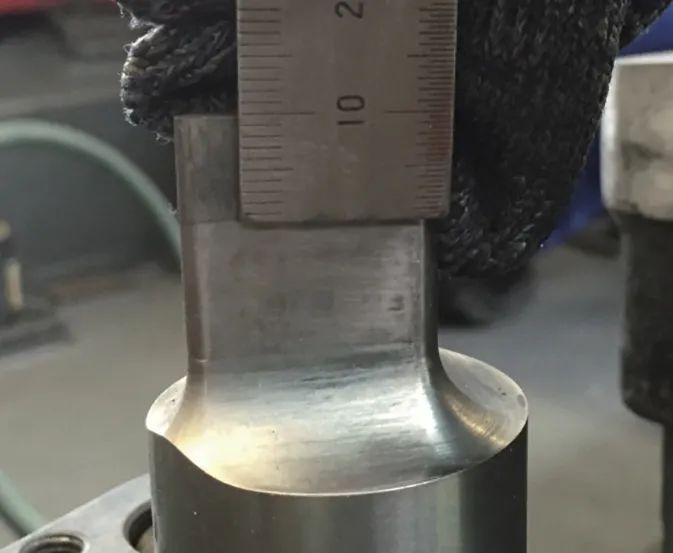
图5 冲头吃入量过大
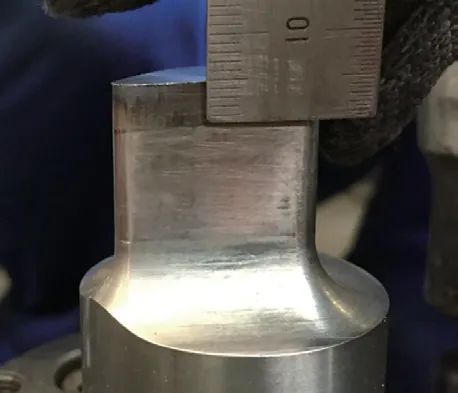
图6 冲头吃入量合理
⑶对刃口间隙及其与压料板间隙优化改进内容包括:
①用红丹研配刃口间隙,使其间隙均匀合理(图7、图8);
②调整刃口与压料板之间的间隙,由原来的0 ~0.1mm,调整为0.5mm ~0.7mm(图9、图10)。
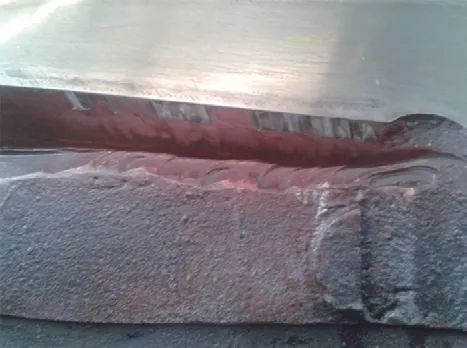
图7 刃口间隙过小
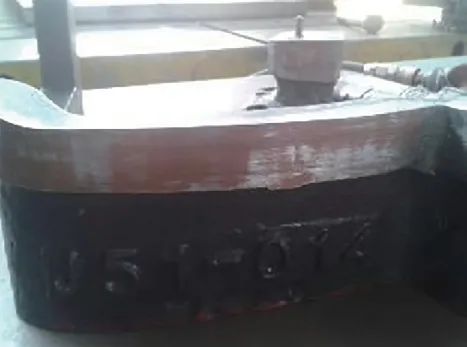
图8 刃口间隙均匀
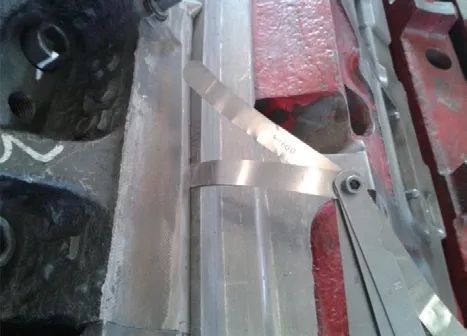
图9 刃口与压料板轮廓间隙小
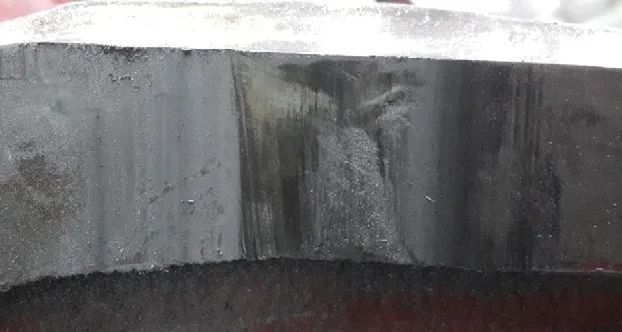
图10 刃口与压料板轮廓间隙均匀
⑷对废料刀的优化改进内容包括(图11、图12):
①废料刀与刀块的间隙由原来的7mm 调至1mm;
②吃入量由12mm 调至4mm;
③无空刀调整至有空刀。
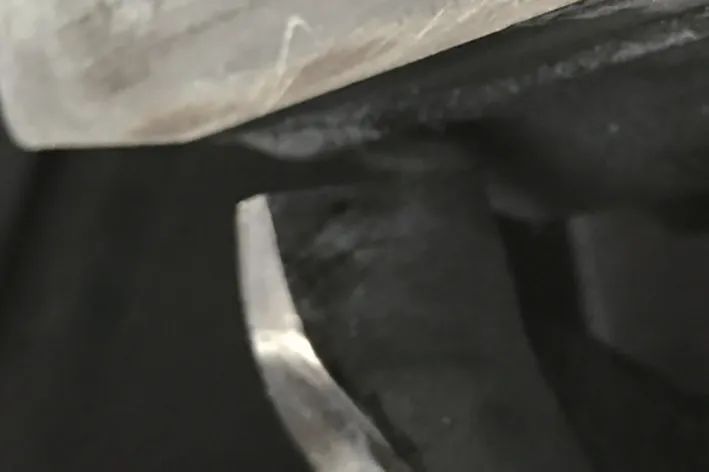
图11 废料刀整改前
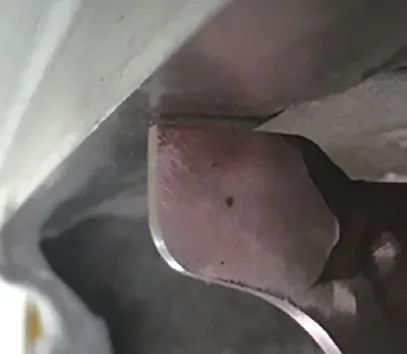
图12 废料刀整改后
压料芯结构整改
对压料芯的压料面的优化改进内容包括(图13、图14):
①压料芯压料控制面由最大40cm 调至20cm 以内,减少压料面积有助于压痕的减少,因为即使有少量铁屑产生,也不至于带入模具;
②压料芯研合率由75%研合到95%以上;
③所有压料型面推顺抛光处理。
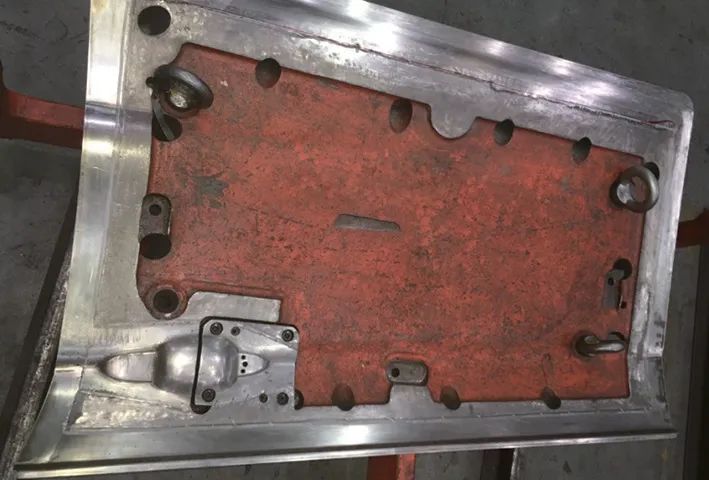
图13 压料芯型面整改前
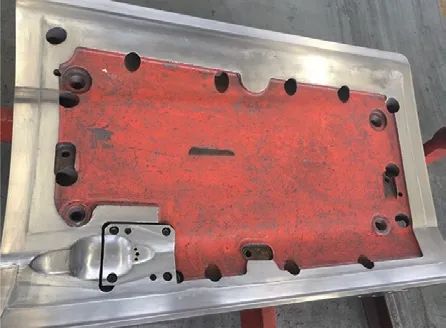
图14 压料芯型面整改后
压料芯内部的局部封闭区域增加直径30mm的通气孔,使之维持与外界气压一致,避免出现生产时由于模具内部的负压而导致的吸铁屑问题的出现,如图15、图16 所示。
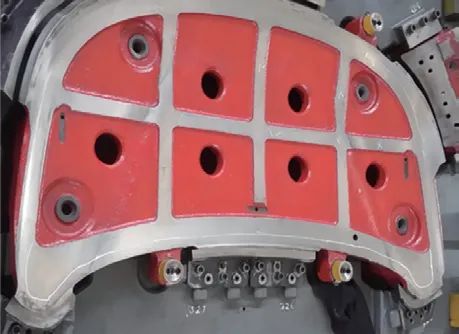
图15 压料芯增加通气孔前
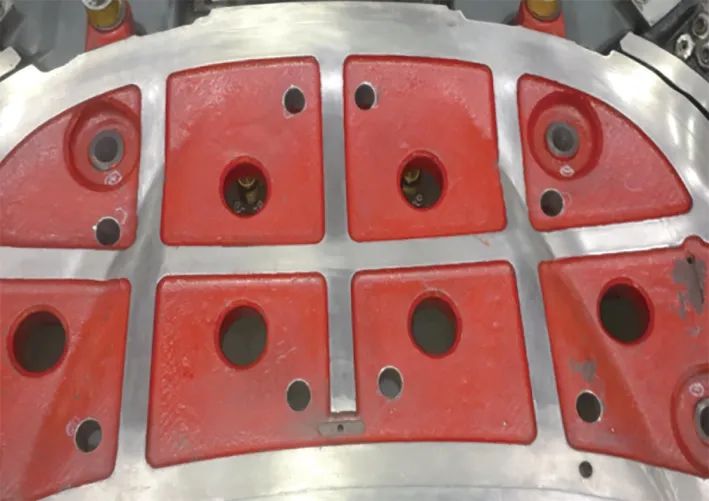
图16 压料芯增加通气孔后
凸模增设通气孔
凸模增设通气孔的优化改进内容包括:①凸模表面的通气孔数量由原来的230 个增加至290 个,增加比例为26%,通气孔选择在面积大、弧面过渡不大的部位,通气孔的尺寸为φ6mm,与原尺寸保持一致(图17、图18);②凸模型面推顺抛光处理。
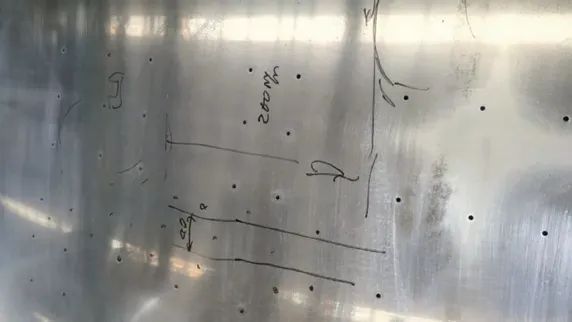
图17 凸模增加通气孔前
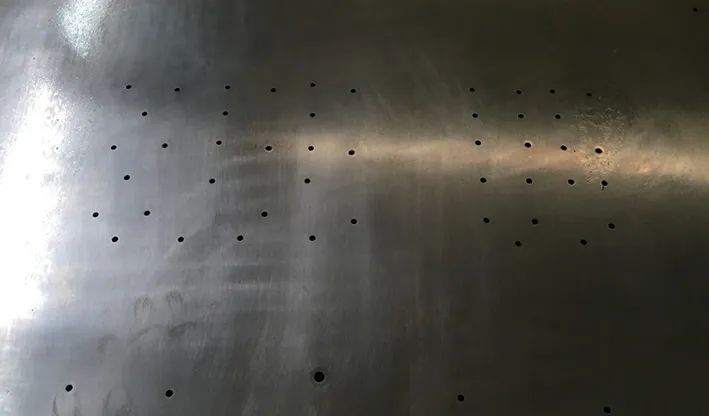
图18 凸模增加通气孔后
结束语
通过对刃口、压料芯、凸模结构的优化和改善,使其工艺参数符合修边工艺要求,减少修边铁屑的产生,进而避免铁屑压伤制件和模具,在最近8 个月的生产中,压痕率由8.5%降低至3.1%,且连续三个月保持稳定,效果明显。在巩固成果持续改善方面:我们一方面将改进明显成功的典型案例应用到新品模具的结构设计阶段,在最大程度上杜绝修边掉铁屑问题的产生。另一方面,我们制定了冲压模具修边掉铁屑模具检修规范,从制度和流程上进行管控,确保生产运营期冲压模具的生产稳定性,减少因修边铁屑导致的产品不合格问题。
|