钢桶生产线气压检漏系统的创新设计
文/刘洪军、郭华
摘要:针对钢桶的微漏气检测问题的基本原理、检测方法进行了研究,并设计了以单片机控制为核心,具有PLC接口的表压式气压检漏系统。实践证明:该气压检漏系统具有较高的检漏精度,可检漏0.1mm漏孔,在生产线的运行过程中具有良好的检漏性能。
关键词:钢桶;单片机;表压式;检漏精度
1 引言
大量的薄壁包装钢桶在生产过程中往往是采用充气压的方法检测漏气性的。
当钢桶存在较大漏缝时,桶内充气后保持不住压力,容易判断是废品;但是当被检测桶只有微小的泄漏时,压力下降很慢,短时间内靠观察压力表难以判断是否漏气。为此,目前许多工厂仍采用较原始的泡水检查法,即将被测桶充气后放入水中观察气泡的情况以判断桶的泄漏与否,这种方法尽管判断较为准确,但效率低下,不能在线检测,被测桶浸水后还要干燥防潮防锈。为了对钢桶产品进行快速的在线逐一检漏,保证产品的质量,需要根据生产工艺在生产线上增加自动漏检环节,该漏检环节主要由钢桶气压检漏系统组成,利用微处理技术、现代传感技术及机电一体化技术,实现高精度的钢桶微漏自动化检测。
2 检漏仪的组成
如图1,由传感器采集的信号传给放大器,经过放大之后传给A/D转换器,把它送给显示块,压力可以适时地显示出来,同时把这个数据送给单片机进行处理判断,得到的结果送给外围设备,用以控制薄壁桶生产线的动作。
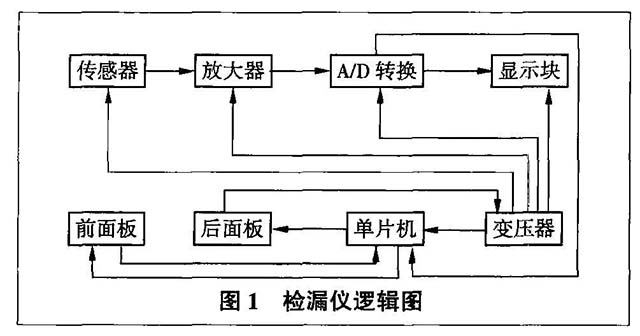
3 气压检漏测量原理
用充气检测法可能会出现三种不同的情况:一是桶的漏洞很大,压力根本升不上去;二是微漏,充气后压力缓慢下降;三是不漏气,充气后压力保持不变。三种情况分别对应图2中的(a)、(b)、(c)。
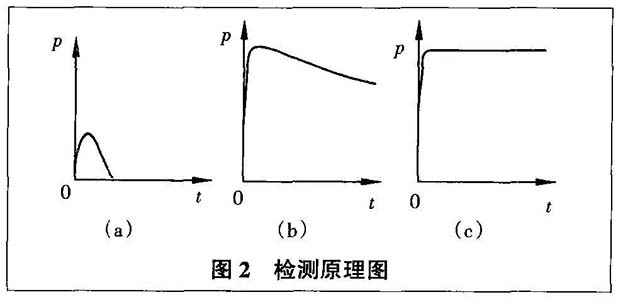
图2(a)情况在充气后系统对桶内压力采集的第一次压力值已经判断桶是不合格的,因为采集的压力值小于设定的最低压力值;图2(b) 为微漏的情况,充气后系统采集第一个压力值p0,与设定最低压力值p0比较,p1≻p0,延时(时间可由拨码开关设定),采集第二个压力值p2,然后判断p1=p2, 的结果与设定泄漏值px比较,如果p1-p2≺px,桶就合格,反之不合格;图2(c)为不漏气,判断过程与图2(b)情况相同。
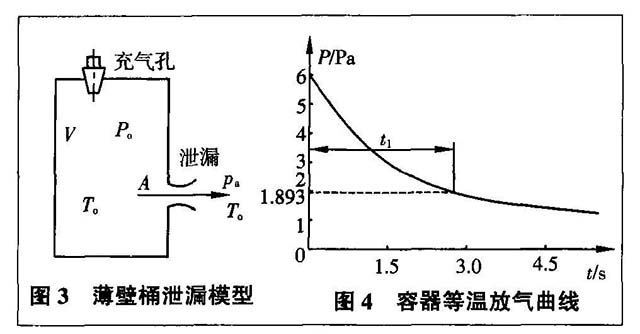
桶如有某处泄漏,充气后,其模型如图3所示的容器自由放气情况。如钢桶微漏,即泄漏面积A很小,钢桶壁导热很好,此时可近似看作等温过程。在被测钢桶中的压力p≻1.893p0时,泄漏孔A处将出现音速,在p下降达到1.893pa之前,由pa等温放气到p所需时间为
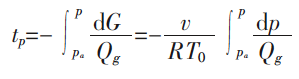
式中 ,为气体的质量流量;p为容器中的压力,初始值为p0;T0为容器中的温度;A为泄漏面积(看成喷嘴);V为容器的容积;R为空气的气体常数。
经推导计算,有:
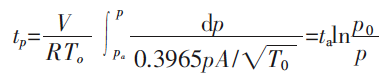
其中 等温充气时的时间常数。
当容器中气体压力降到小于1.893pa以后,问题较为复杂,表达式不易推导,一般借助于近似计算。图4所示为某泄漏孔面积为A的桶内的压力与时间的关系曲线。
由式(2)和图A 可知,延时时间设定在0.1~9.9s(由两位拨码开关设定)能够满足检测要求。
3.1 检漏仪硬件组成
根据生产线要求和检测精度要求,设计的钢桶气压检漏系统硬件本体主要由98C51为控制核心的单片机、型号为BQ10的简易硅压阻式压力传感器及其驱动电路、以AD524为主的滤波放大电路、以ICL7135为核心的AD转换电路、数码管驱动电路、PLC驱动接口电路和以8155为主构成的扩展接口组成。
3.2 压力传感器二次仪表电路
压力传感器的二次仪表电路由恒流供桥电源电路、差动放大电路和RC滤波电路三部分组成,见图5所示。
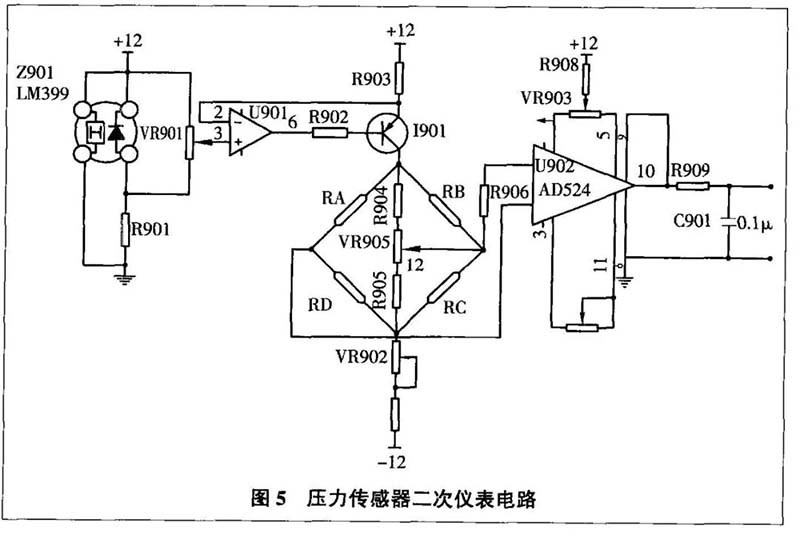
A/D转换电路的设计主要考虑转换速度和转换精度。气动测量中气压的稳定速度较慢,也不存在需要实时控制的问题,因此本系统选择了双积分型A/D转换芯片,考虑到测量分辨率的要求,此处选择的型号是ICL7135,该芯片是美国Intel公司生产的高准确度、通用型单片CMOS4位半A/D转换器。
用8155接口芯片直接同7135联接,节省了硬件资源的开销。
3.3 检漏仪与PLC的接口
该检漏仪所应用的生产线是由PLC控制的,所以该检漏仪与生产线存在连接的问题,因为PLC输出的是24V直流电压,而单片机需要的是弱电流,或者说是脉冲,所以PLC传过来的信号不能直接送给单片机,否则会烧坏芯片,为此选用固态继电器把两者连接起来。
4 检漏仪软件设计
根据前述的检漏原理和检漏动作步骤分析,所设计的单片机检测主程序流程如图6所示。

5 结论
根据生产线的要求所设计的钢桶微漏气压自动检测仪,经过一段时间的实际运行考验,证明完全适合此类密封容器的微漏检测实际情况,经过多次测量试验,带有直径为0.1mm小孔的桶能准确无误地检测出来,出厂的桶在泄漏指标内100%合格,检漏仪达到了设计指标,比传统的手动泡水法检测效率提高了20倍以上,成功地实现了产品的在线检测。
|