钢桶桶盖成型方法的研究与实践
刘国斌
【摘要】大开口钢桶是化工、食品等行业大量使用的包装容器,大开口钢桶桶盖的成型质量对包装桶的密封性、使用性至关重要,是国内制桶行业生产企业十分关注的问题。采用合理的工艺方法,即能够保证质量,又能够降低成本。介绍了目前制桶行业生产大开口桶钢桶盖的三种方法及所使用的模具、设备,比较了三种方法的特点,为解决生产实际问题提供了参考。
【关键词】钢桶桶盖;成型;模具;研究
1 概述
钢桶是重要的包装容器,随着我国进入国际市场的步伐,许多化工企业和食品生产企业加大了出口的数量,钢桶的需求量越来越多。目前,我国现有制桶企业近800家,所生产的钢桶分为闭口钢桶和大开口钢桶,以往我国企业大多使用闭口钢桶,主要用于液体包装。但随着产品的变化、种类的增加,更多地需要用大开口钢桶作为包装,这为大开口钢桶产品提供了更加广阔的市场,而一些精明的国外制桶厂家纷纷在国内投资建厂,将他们的先进设备及技术带到国内,以他的产品质量优良且成本低等优势,扩大其在国内大开口钢桶市场占有率。这就对国内的制桶企业形成很大冲击。随着产品出口量的不断增大,大开口钢桶的市场潜力也逐步增大,尤其是在我国西部,潜在市场巨大。因此,许多大开口钢桶生产企业也看好这一市场前景,纷纷在研制开发全大开口钢桶这一新产品。桶盖的成型质量对包装桶的密封性、使用性至关重要,采用合理的工艺方法,即能够保证质量,又能够降低成本,这是生产企业十分关注的问题。我公司近年来自行改造设备,研制模具等工装,完成了大开口钢桶的研发和批量生产。
2 大开口钢桶桶盖的成型方法
在项目的具体实施过程中,围绕着大开口钢桶桶盖的成型工艺方法进行了深入研究。大开口钢桶桶盖产品如图1所示,其技术要求规定冲压毛刺不能大于0.2mm,大开口钢桶桶盖的料厚为0.9mm、1.0mm、1.2mm共三种。
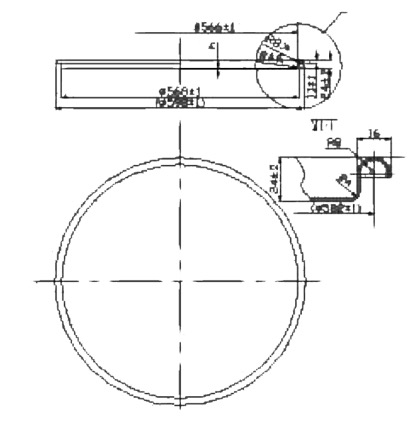
图1 大开口钢桶桶盖产品图
2.1 模具一次成型法
采用复合模一次成型钢桶和桶盖是制桶厂常用的方法,为此,我们设计了专用的复合模具。模具一次成型法所用的模具结构如图2所示。
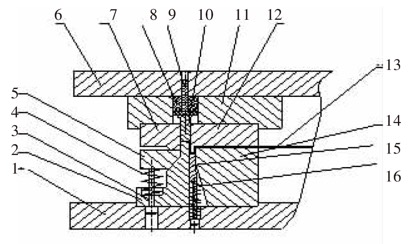
1-下模座;2-下刀口;3-螺栓;4-弹簧;5-托料圈;
6-上模座;7-上刀口;8-聚氨酯橡胶棒;9-橡胶棒导向柱;
10-上压边圈;11-上垫板;12-上模芯;13-工件;
14-下模芯;15-内托料圈;16-弹簧
图2 模具结构图
该模具采用聚氨酯橡胶压缩变形产生压边力,利用普通单动C型机身冲床一次冲压成型。其工作过程如下:首先模具利用自动送料机将钢板送入模具中,先由上刀口7与下刀口2进行落料,由托料圈5将废料托出;然后,由上压边圈10与下刀口2将落料下的钢板夹住;经过聚氨酯橡胶棒8的压迫逐渐变形形成边缘。为防止工件起皱,上模芯12与下模芯14对工件进行拉深,再由内托料圈15将工件脱出。整个成型过程一次完成,模具结构采用反拉深形式,拉延筋形成桶盖的凹边,顶出时工件在模具平面以上,便于在废料走料时将工件带出,形成自动化连续工作。
模具参数计算如下:
(1)工件毛坯下料尺寸计算
根据冲压手册公式:D=√F (1)
F=9.87dar+d2+4dH+πdhb
根据图纸得出:da=582;r=8;d=568;H=16;hb=4;db=598
式中:da——翻边外缘中心直径,mm;
r——翻边外缘圆角半径,mm;
d——拉深筒形外径,mm;
H——拉深筒形高度,mm;
hb——翻边外缘的直边高度,mm;
db——翻边外缘的外径,mm。
代入公式(1)得: F=412;442;D=642mm
(2) 落料力的计算
根据公式:P=tLσb/1000 (2)
式中:σb——材料的抗拉强度(MPa);
t——工件的厚度(mm);
L——工件的周长(mm);
P——冲裁时所需要的力(N)
根据图纸得出:
σb=450;t=1.2;L=642π=2015.86;P=1089(kN)
(3) 拉深力的计算
根据公式P=K1tLσb/1000 (3)
式中:σb——材料的抗拉强度(MPa);
t——工件的厚度(mm);
L——工件的周长(mm);
P——拉深时所需要的力(N)
K1——修正系数
根据产品图得出:
σb=450;t=1.2;L=598π=1877.72;K1选最大为1时, P=1044(kN)。一般压边力为拉深力的1/3即为P拉=348(kN)。
从以上计算得出选用原有200T冲床是可行的。
2.2 利用原闭口钢桶桶盖二次整型法
闭口钢桶桶盖成型后产品如图3所示。利用原闭口钢桶桶盖二次整型法模具结构如图4所示。
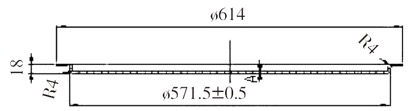
图3 闭口钢桶桶盖成型产品图

1-下模座;2-螺栓;3-下凹模;4-弹簧;5-下模芯;6-工件;
7-上凸模;8-上模座;9-打料盘;10-打料钉;11-模柄;12-螺母
图4 二次整型模
二次整型模的工作过程如下:首先将工件放在下模芯5上,上凸模7与下凹模3将工件整形,若成型后的工件卡在上凸模7中,则由打料盘9打落;如果成型后工件卡在下凹模3里,可由下模芯5托出。
此二次整型模的模具结构简单,利用原来的闭口桶盖产品制成的产品再成型,其模具比一次成型法的模具造价低,投资少,但由于需要两次成型,工时利用率较低。
2.3 利用闭口钢桶盖旋压成型法
旋压工艺是一种高效成型方法,大开口钢桶桶盖旋压机的结构如图5所示。
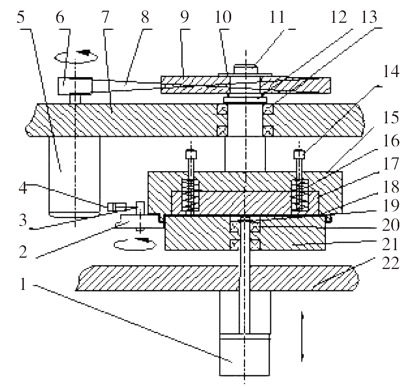
1-气缸;2-旋压轮;3-旋压轮轴;4-汽缸;5-电机;6-小皮带轮;
7-上床身;8-皮带;9-大皮带轮;10-弹簧挡圈;11-主轴;
12-锁母;13-轴承;14-螺栓;15-上大盘;16-弹簧;17-上托料圈;
18-工件;19-弹簧挡圈;20-轴承;21-下定位盘;22-下床身
图5 大开口钢桶桶盖旋压机结构示意图
此旋压设备的工作过程如下:将工件滑入下定位盘21,气缸1将下定位盘21 顶起,由于上大盘15一直在旋转,这时上大盘15和下定位盘21将工件18夹紧并旋转。气缸4推动旋压轮2将工件18旋压到上大盘15的曲面上,获得所需要的形状。成型后,气缸1落下,上托料圈17将工件脱出。如果工件落在下定位盘21上,则气缸4落下时两侧刚性挡块将工件托起。此工艺简单易行,成本低,但工件尺寸的一致性不如模具成型。
3 三种成形方法的比较
三种成形方法各有特点,其比较见表1。
表1 三种成形方法的比较
项目 |
模具一次成型法 |
二次整型法 |
旋压成型法 |
产品尺寸精度 |
高 |
高 |
低 |
产品尺寸一致性 |
高 |
高 |
低 |
模具费用 |
高 |
中 |
低 |
生产效率 |
高 |
中 |
低 |
工人劳动条件 |
好 |
中 |
差 |
工厂改造投资 |
高 |
低 |
中 |
比较三种成形方法的优缺点,其中:“模具一次成型法”是一种高质量、高效率的成形方法,特别适合于新投资建厂的规模化、大批量生产模式,其产品质量高,质量稳定性好;“二次整型法”比“模具一次成型法”增加了一道整型工序,中间毛坯需要一次周转,加大了操作工人的劳动强度。但分开两次成型可以降低每一次的塑性变形量,可以有效地防止由于一次塑性变形量过大而使桶盖边缘产生裂纹的现象,提高了成品率,即使生产时板料的塑性产生波动,也不会对产品质量产生明显的影响。而且“二次整型法”可以在原有的闭式钢桶桶盖生产线上增加整型工序,即可以生产出大开口钢桶桶盖。这样特别适合于原有生产线的改造。“旋压成型法”的模具费用低,但生产效率低,仅适合于小批量的生产。而且产品质量不稳定。
4 总结
通过对大开口钢桶桶盖三种成型工艺方法的比较,我们采用了第二种方法,即“利用原闭口钢桶桶盖二次整型法”,这样可以利用企业原有生产线设备及条件,投入一套整型模具,增加整型工序,就可以生产出合格的产品,而且产品质量较高。同时保留了原有的生产线,可以在需要的时候恢复闭口钢桶的生产。
参考文献
[1] 杨文亮.我国制桶企业的现状和发展[J].上海包装:2001,(3):46.
[2] 林陈彪.复合模具在钢桶生产中的应用[J].机电技术,2007,(3):52~54.
[3] 赵琳瑜,韩冬,张立武,等.旋压成形技术和设备的典型应用与发展[J].锻压技术,2007,(6):18~26.
[4] 陈适先.强力旋压及其应用[M].北京:国防工业出版社,1996.
|