复合模具在钢桶生产中的应用
林陈彪
【摘要】100L和200L钢桶是化工产品的主要包装物,电石产品的钢包装桶属危险品包装物,生产工艺流程长,占用压力机多。通过改造生产流程、合并工序及应用复合模具等方法,可实现减少压力机台数,提高生产效率及经济效益。
【关键词】包装钢桶;复合模具;提高效率;节省投资。
1.引言
化工产品多属危险产品。其使用的包装钢桶则为危险品包装物,原生产工艺流程长,占用压力机多。还需要多台专用钢桶加工机械。
为满足用户的需求,三化机械厂包装钢桶系列及品种不断增加,所需的钢桶加工设备也越来越多。其中用于桶盖、小盖和桶底制作压力机需求也不断增加。如果依靠更换模具来减少压力机的投入。将无法提高生产效率,而且模具多次安装将可能出现上下模配合精度误差而影响产品质量。组织生产的灵活性也必然下降。本文采用复合模具等方法,对生产流程进行改造,达到减少压力机用量.提高生产效率的目的。
2.桶盖和桶底的生产工艺流程的改进
包装桶的桶盖、小盖和桶底的生产过程,零件结构的主要工艺,基本上都由压力机上安装各式模具来完成。钢桶生产线改造之前。使用常规模具、以单个结构的冲裁、弯曲或拉深工序来完成零件制作。以100L电石桶为例,桶盖和桶底材料均为10#钢,薄板厚为1mm。桶盖、桶底零件图见图1。
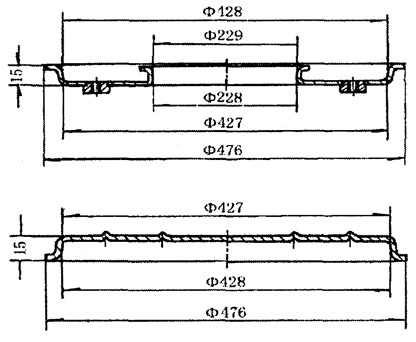
图1 100L电石桶桶盖、桶底示意图
桶盖改造前生产工艺流程:落料冲裁→拉深→成形→冲小孔→冲大孔→一次翻边→二次翻边→冲字成形。
桶底改造前生产工艺流程:落料冲裁→拉深成形→加强筋成形。
冲裁是完成桶盖的落料工序。其基本尺寸为Φ490;拉深是完成Φ428(Φ427)尺寸的成形工序:冲小孔完成2个透气小孔的制作工序。用于点焊M10螺帽并安装专用螺丝;冲大孔完成Φ190基本尺寸的冲裁,为一次翻过做准备,大孔用于装料及封小盖;一次翻边完成Φ229(Φ228)尺寸的翻边工序;二次翻边完成尺寸Φ245的翻边工序:冲字则完成内销或出口标志和产品批号等字体的成形工序。
钢桶生产线改造的设计重点是应用复合模具来合并工序。经过对工艺流程的分析研究,多种复合方案的比较确定,将桶盖工艺流程中落料冲裁与拉深成形合并、冲大孔与一次翻边合并、冲小孔、冲字成形合并;将桶底工艺流程中落料冲裁与拉深成形合并。并将此方案作为改造的优选方案。
改造后桶盖生产工艺流程:落料、拉深复合冲裁成形→小孔、字复合冲裁成形→大孔、一次翻边复合冲裁成形→二次翻边。
桶底改造后生产工艺流程:落料、冲压复合冲裁成形→加强筋成形。
3.复合模具设计的运用
由于复合模具生产效率高。冲裁零件的尺寸与外缘。相对位置精度较高,在需要依靠多道冷冲压生产工序完成的零件制作过程中,逐步得到广泛的应用,是冷冲压生产线性改造的主要方向之一。改造方案确定后,结合三化机械厂模具制造能力进行模具结构方案设计及加工图设计。
3.1 落料、拉深冲裁成形复合模
落料、拉深冲栽复合模的结构设计,上模采用上模刀口与上模座焊接方法制作,下模采用凹模刀口与下模座销子定位、螺丝紧固方法制作。
复合模的材料,上模刀口与凹模刀口均选用45#钢。要求热处理至HRC50~55,上模座和下模座则采用Q235A。以节约材料费用;卸料橡胶选用弹性好的天然橡胶或顺丁橡胶。落料、拉深冲裁成形复合模结构见图2。
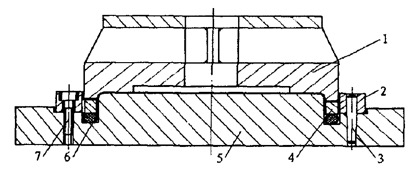
1-上模座及上模刀;2-凹模刀;3-圆锥销;
4-卸料板;5-下成形模;6-卸料橡胶;7-螺钉
图2 落料、拉深冲裁成形复合模
3.2 小孔、字冲裁成形复合模
小孔、字冲复合模的结构设计。上模采用上模座与气孔上刀口螺纹联接的方法制作,上模座本体采用中板焊接方法制作;下模座采用厚板整体制作。气孔下刀口采用过盈配合及螺栓固定的方法,准确安装在下模座上;上、下字模采用销子定位、螺丝紧固的方法,分别安装在上、下模上。
复合模的材料,上下气孔刀口、上下字模均选用45#钢。热处理至HRC50~55。而上模座和下模座则选用Q235A。小孔、字冲裁成形复合模结构见图3。
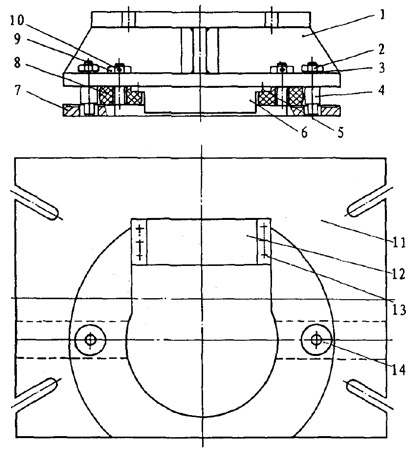
1-上模座;2-螺母;3-弹簧垫;4-气孔上刀口;
5-螺栓、销钉;6-上字模;7-卸料板;8;卸料橡胶;
9-螺栓、螺母;10-销子;ll-下模座;12-下字模;
13-螺栓、销钉;l4-气孔下刀口
图3 小孔、字冲裁成形复合模
3.3 大孔、一次翻边冲裁成形复合模
大孔、一次翻边复合模结构设计,采用拉深(一次翻边)正装、冲裁倒装式复合。拉伸凸模与上模刀口合二而一,并与上模座螺纹联接的方法制作。下模中拉深凹模及下模刀口与下模座以销子定位、螺丝紧固方法联接。结构设计时要注意,上道工序完成字体的凸起后,对应下模设计。应铣出足够容纳凸起字体的凹槽。
复合模材料,上模刀口与下模刀口均选用45#钢,热处理至HRC50~55。上模座和下模座则选用Q235A。大孔、一次翻边冲裁成形复合模结构图见图4。
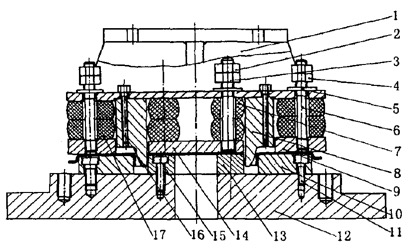
1-上模座;2-螺母;3-螺杆;4-螺母;5-垫片;6-螺杆;
7-卸料橡胶;8-拉深模及内刀口组合;9-卸料板;
1O-拉深下模;ll-螺钉;12-下模座;l3-下刀口;
14-小卸料板;15-螺钉;16-螺栓;17-卸料橡胶
图4 大孔、一次翻边冲裁成形复合模
模具结构设计是复合模具设计过程中的重点,设计过程参考了常规模具的设计思想及现场使用特点。模具间隙、工件变形量的计算和冷冲模模具设计手册。一般零件的选材及热处理要求参考相应的设计资料及现场使用经验。
4.复合模具的制作及试运行
复合模具制作关键是模具各部分的尺寸必须准确,能完整实现设计意图。根据三化机械厂多年制作钢桶模具的经验。模具制作完成后必须进行合模检测调试,调试采用安装试运行的方法。除落料、拉深冲裁成形复合模外,小孔、字冲裁成形复合模及大孔、一次翻边冲裁成形复合模均需制作专门试件,首先进行小孔、字体、大孔、一次翻边的单个要素冲压调试。成功后再进行复合模的完整调试。对搭边、模具的间隙、卸料能力等再做出适当调整后进行试生产。试生产过程,专业技术人员应跟踪测量、记录。对复合模具提出改进的建议,再根据建议对模具进行优化完善,最后正式投入生产。
5.复合模具的投用效果
通过生产流程改造,设计复合模具来合并工序,并成功地应用于100L电石桶等钢桶生产,实现了减少压力机,缩短工艺流程的效果。桶盖、桶底生产线经改造后,正式投入三化机械厂生产,节省了四台63t压力机的投入,减少了设备占地面积。同时,借鉴100L电石桶复合模具的设计理念及调试方式,应用于多种钢桶复合模具的设计,达到了同样的效果。生产效率及经济效益获得同步提高,产量逐年上升,目前钢桶年生产能力已达到10多万个。
6.结束语
100L和200L钢桶生产线改造实践表明,通过改造生产流程、合并工序及应用复合模具等方法,可实现减少压力机台数,提高生产效率并取良好经济效益。
参考文献:
【1】赵伟阁.膜具设计[M].西安:西安电子科技大学出版社,2006
|