《金属包装设计与制造》(24)
金属包装制造常见模具结构
文/吴若梅、刘跃军
在金属包装容器的成型、制造过程中,大都需要模具的辅助。随着工业的发展和科技的进步,社会对金属包装容器的要求也越来越高,因此模具在设计、材料、生产、使用等各方面都发生了很大变化。本节对现在应用最广泛的冲裁模、弯曲模和拉深模及其典型结构做了详细分析;对在金属包装容器制造过程中起到重要作用的翻边、缩口、胀形、整形等模具也做了简单介绍。
一、冲栽模
1、单工序冲裁模
单工序冲裁模是指即在一副模具中只完成一种工序,如落料、冲孔。由于落料和冲孔在冲裁工艺中仅仅是取舍部分不同,而模具工作原理大致相同。下面以无导向落料模为例,介绍落料模的工作流程、原理及特点。
如图11-2所示为无导向落料模。冲裁(落料)工序开始时,首先利用导料板4及定位板7将坯料定位,之后在冲压力作用下进行冲裁,在凸模推力的作用下,从坏料上分离下来的冲裁件直接从凹模洞口落下,环绕在凸模上的废料由固定卸料板3脱下,完成落料工作。这种落料模的特点是上、下模均无导向装置,冲裁位置由机床滑块的导向精度决定,结构简单,制造难度较低。此类模具的缺点是安装调试比较困难,条料排样形式局限较大,操作也不够安全,仅适用于冲裁精度要求不高、形状简单和生产批最小的冲裁件。
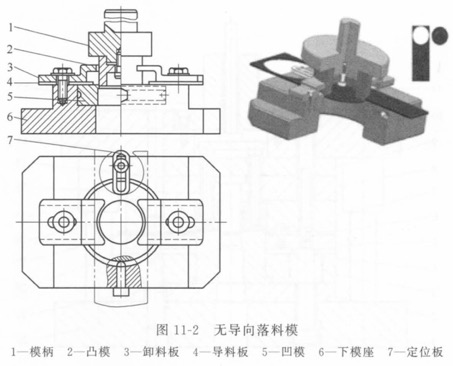
与无导向落料模相比,固定导板导向落料模和导柱导向落料模均对压还位置及上下模的运动做了精确导向,冲裁精度高,安装方便,但制造成本较高,适用于生产批址较大、精度要求较高的制件。
2、复合冲裁模
复合冲裁模在结构上最主要的特征是:存在一个零件具备凸模和凹模两个零件的功能,称之为凸凹模。如在落料冲孔复合模中既作为落料凸模又作为冲孔凹模的零件就是凸凹模。如图11-3所示为冲孔落料复合模的基本结构。落料凹模与冲孔凸模均安装在下模,凸凹模安装在上模。冲裁开始时,随着上模的下降,凸凹模的外侧刃口与落料凹模配合工作,完成落料工序;同时,凸凹模的内侧刃口与冲孔凸模配合工作,完成冲孔工序。
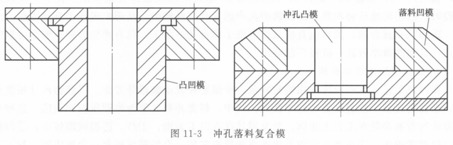
根据凸凹模在模具中的装配位置不同,通常将复合模分为正装式复合模和倒装式复合模两种。凸凹模装在上模的称为正装式复合模,凸凹模装在下模的称为倒装式复合模。
如图11-4所示为落料冲孔倒装复合模。凸凹模21安装在下模上,冲孔凸模16和落料凹模7安装在上模上。还料由定位销6(两个导料销和一个挡料销)定位,冲裁时,上模向下运动,因弹性卸料板5和安装在凹模型孔内的推件板20分别高出凸凹模和落料凹模的工作面约0.5mm, 且落料凹模7上与定位销对应的部位加工出了凹窝,坯料首先被压紧。随着上模的继续下降,冲孔、落料两个工序同时完成。此时,冲下的工件卡在凹模孔内、冲孔废料在凸凹模的型孔内积聚,坯料箍紧在凸凹模上,而弹簧4被压缩,弹性卸料板5相对凸凹模的上表面向下移动了一个工作距离。上模回程时,被压缩的弹簧回弹,推动卸料板向上移动复位,同时将雏紧在凸凹模上的还料脱卸。卡在凹模孔内的工件,借助打料横杆(随滑块一起上下运动)与挡头螺钉(固定在压力机的机身上)之间的撞击力,被打杆12、推板13、推杆15和推件板20组成的刚性推件装置推出。在下一次冲裁行程时,凸模的推压将积聚在凸凹模型孔中的冲孔废料推出,从而实现逐个自然漏料。
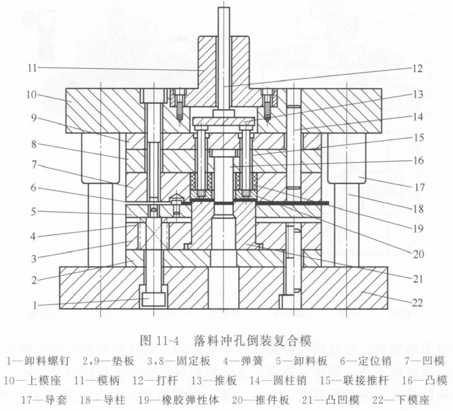
采用倒装复合模,废料能直接从压力机工作台孔中落下,具有操作方便、安全可靠等优点,且生产效率较高,故被广泛应用。
3、带齿圈压板的冲裁模
在冲裁工艺中,还经常采用精密冲裁、半精密冲裁或整修等方法,以获得尺寸精度更高、断面更光洁、垂直度更高的冲裁件。其中,精密冲裁又称为齿圈压板冲裁法。这种冲栽方法与普通冲裁在工艺上相同,但是模具存在以下差别:
①凸、凹模间隙极小;
②凹模刃口位置带圆角;
③在模具结构上比普通冲裁模多装一个齿圈压板和一个顶出器。
其工艺流程如图11-5所示。
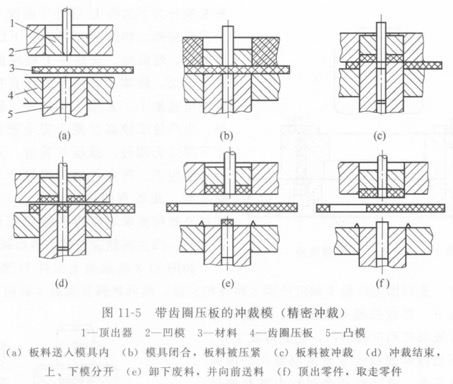
精密冲裁在提高冲栽周界塑性的同时,还大幅度降低了还料剪切区的拉应力。同时,由于凹模刃口为圆角,消除了应力集中,从而大大降低了因拉应力产生撕裂断面的概率。此外,顶出器的存在能防止弓弯现象的产生,故能得到冲栽面光亮、锥度小、平整而精度高的工件。
二、弯曲模
金属材料的弯曲主要通过模具及其装备来完成,弯曲件的形状及弯曲工序的安排决定了弯曲模的结构。金属包装材料几乎涵盖了所有类型的弯曲件,如钢桶桶身的滚弯件、提手的折弯件等。由于弯曲件的种类很多,形状不一,因此弯曲模的结构类型也是多种多样的。
1、V形件弯曲模
如图11-6所示为V形件弯曲模的基本结构。
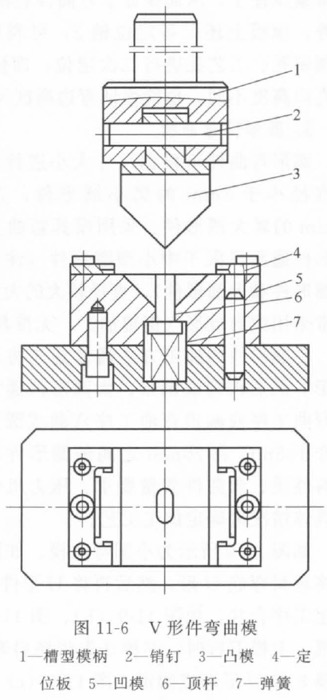
零件3为凸模,由销钉2固定在标准槽形模柄1上。凹模5通过螺钉和销钉直接固定在下模座上。弯曲工序开始时,还料由定位板4定位。顶件装置由顶杆6和弹簧7组成,其主要作用有:
①在弯曲过程中压住蚽料防止还料位置偏移;
②回程时将弯曲件从凹模内顶出。
该模具的特点是结构简单,便于安装及调试,对坯料厚度的公差要求不高。适用于加工两直边相等的V形件,在弯曲终了时可利用顶件装置对弯曲件进行一定程度的校正,回弹较小。
2、U形件弯曲模
根据弯曲后弯曲件的推出位置,可将U形件弯曲模分为下出件U形件弯曲模与上出件U形件弯曲模。如图11-7所示为下出件U形件弯曲模,弯曲后,安装在上模座的凸模继续往下运动,将加工后的弯曲件直接从下模座的凹模孔推下,无须手工取件,模具结构简单,生产效率较高且便于安全操作。但是由于下模座无顶杆、顶板等装置,因而无法进行弯曲校正,弯曲件的回弹较大,底部也不够平整。此类弯曲模可用千加工高度较小、底部平整度要求不高的小型U 形件。弯曲半径和凸、凹模间隙应取较小值以减小回弹。
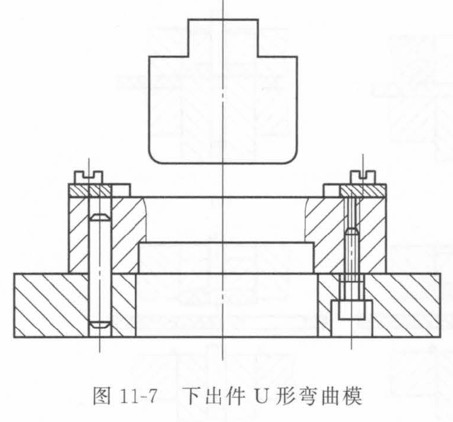
如图11-8所示为上出件U形件弯曲模,弯曲开始时,先利用定位板4和定位销2将还料定位,然后蚽料及顶板3被向下运动的凸模1同时压下,并在凹模5内成形。回程时弯曲后弯曲件被顶杆和顶板顶出,完成弯曲工作。该模具与下出件弯曲模的主要区别是在凹模内设置了顶件装置,再冷的弯曲过程中坯料被顶板紧紧压住了,从而保证了弯曲件底部的平整。此外,顶板上还配备定位销2,可利用坯料上的预留孔、工艺孔进行二次定位,即使U形件两直边高度不同,也能保证弯边高度尺寸。
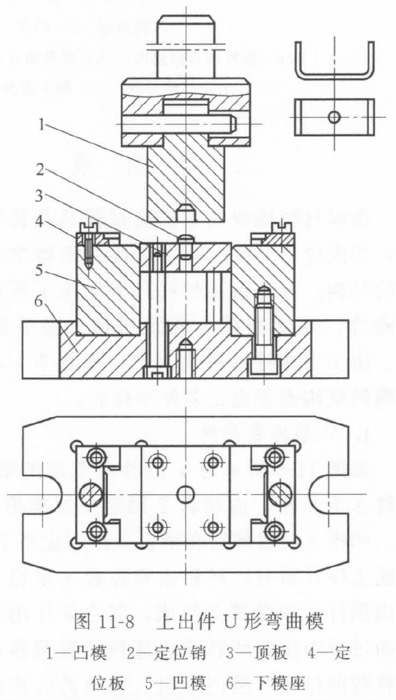
3、圆形件弯曲模
圆形弯曲件可根据尺寸大小进行分类,通常直径小于5mm的属小圆形件,直径大于20mm的属大圆形件。采用模具弯曲方法加工圆形件通常只限于中小型圆形件(注意:包括小圆形件和大圆形件),直径较大的大型圆形件通常采用滚弯成形(钢棍加工、无模具)。
小圆形件的加工方法通常是先将还料弯成U形,然后再弯成圆形;大圆形件通常采用三道弯曲工序或两道弯曲工序弯曲成圆。加工直径介于5mm和20mm之间的圆形件,可根据材料性质、弯曲件质量要求、压力机性能参数等具体情况来确定加工工艺。
如图11-9所示为小圆弯曲模。如图11-9(a)所示为使用两套简单模具弯圆的方法,先将还料弯成U形,然后再将U形件弯成圆形。这种两次弯曲操作方法效率较低,可将两道工序合并,如图11-9(b)、图11-9(c)所示。其中图11-9(b)为有侧楔的一次弯曲模,上模下行时,芯棒3先将还料弯成U形,随着上模继续下行,侧楔7便推动活动凹模8将U形弯成圆形;图11-9(c)所示是另一种一次弯圆模,上模下行时,压板2将滑块6往下压,滑块带动芯棒3先将坯料弯成U形,然后凸模1再将U形弯成圆形。如果工件圆形度或精度要求较高,可旋转工件连冲几次。弯曲后工件环套在芯棒3上,取下即可。
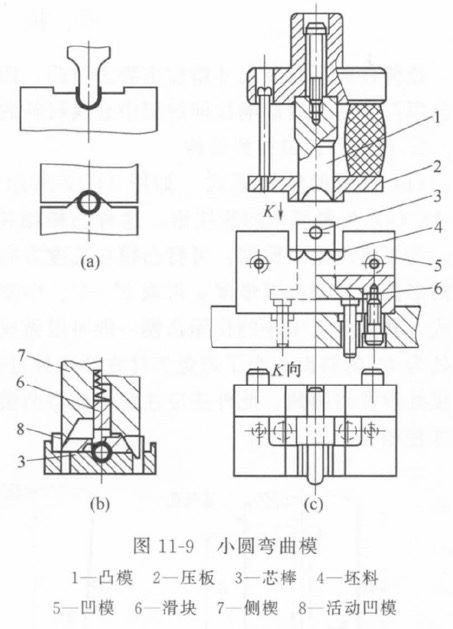
如图11-10和图11-11所示分别为三道工序弯曲大圆的方法及两道工序弯曲大圆的方法。前者生产效率较低,但适用于加工还料厚度较大的工件;后者先将坯料预弯成三个120°的波浪形,然后再利用第二套模具弯成圆形,此方法操作简单,但对各工序加工精度及模具要求较高。
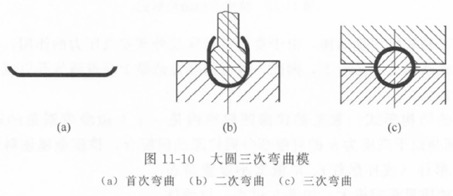
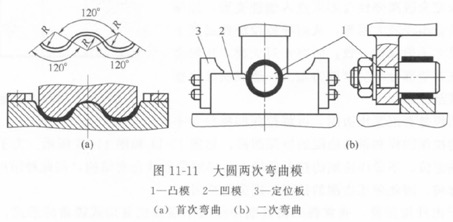
4、其他形状零件的弯曲模
除以上三种在金属包装容器中常用的弯曲模具之外,还有很多其他形状件的弯曲模,如L形件弯曲模、Z形件弯曲模、较链件弯曲模及其他异形件弯曲模。由于这些弯曲件形状、尺寸、精度要求及材料各不相同,难以有一个统一的弯曲方法,只能在实际生产中根据各自的工艺特点采取不同的弯曲方法。
三、拉深模
拉伸件的形状及尺寸精度主要通过凸、凹模来控制的,因此,凸、凹模断面形式的设计合理与否将直接影响拉伸过程中金属材料的流动状态,进而影响拉伸件质量。
1、拉深凸、凹模的结构
(1) 凸模的结构形式
如图11-12所示为几种常见的拉伸凸模结构形式,其中图11-12(a)为最简单的圆柱形,这种凸模结构简单,制造成本较低,但是不利于工件脱模。为了解决这一弊端,可将凸模在高度方向上加工一定的锥度a[图11-12(b)],一般圆筒形件的拉深凸模锥度a 可取2°~5°。中型和大型拉深件的加工通常需要多次拉深才能完成,其前几道工序的拉深凸模一般可以做成带有锥形侧角的结构[图11-12(c)],其转角处为45°的斜面。为了避免工件在圆角处过分变薄甚至断裂,通常需要在斜面和圆柱形连接处设置倒圆角。此外还应注意,此类凸模底部直径小的大小应与下一次拉深时凸模的外径相等。
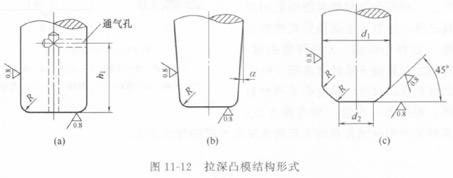
即使采用了易脱模凹模结构,由于受模具挤压及外部空气压力的作用,拉伸后的工件仍常常紧紧套在凸模上不易脱下,因此,通常需要在凸模上开设通气孔以减小空气压力的影响[图11-12(a)]。
(2) 凹模的结构形式
常见的拉深凹模结构是一个上边缘带圆角的圆柱孔,如图11-13所示。圆角以下高度为h的直壁部分同拉深凸模配合,挤压金属还料产生滑动使之变形成为圆筒形件(或杯形件)。h值大小设置是否合理对拉伸件的质量影响极大,如果h过小,拉伸件金属材料未完全脱离弹性变形区进入塑性变形,拉深过程结束后会出现较大回弹,从而导致拉深件高度上各部分的尺寸不能保持一致;而当h过大时,还料金属在凹模内直壁部分滑动摩擦力增大,造成制件侧壁过分变薄甚至拉断。
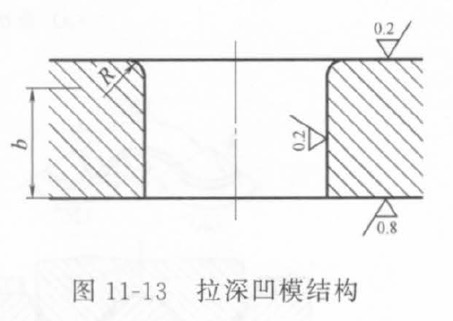
根据凹模是否配置压边圈,可将拉深凹模分为不带压边圈的拉深凹模和带压边圈的拉深凹模,如图11-14和图11-15所示。为了保证拉深坯料的正确定位,不带压边圈的拉深凹模在口部通常做成台肩结构,但此种结构形式的凹模不便于修模,因此带压边圈的拉深凹模更为常用。
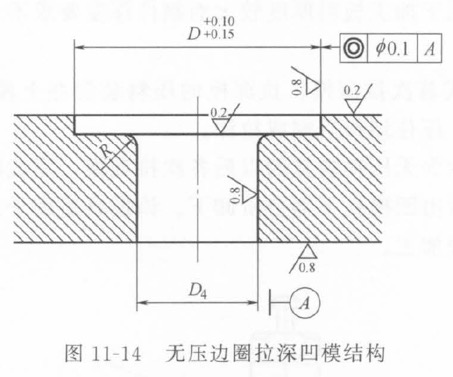
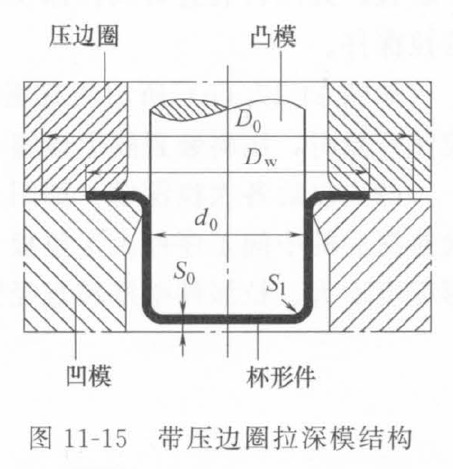
对于下出件拉深模,通常将凹模直壁部分的下端做成直角或锐角的形式,这样在拉深过程终了时,拉伸件随凸模上行时其口部会被凹模下端勾住,完成脱模,如图11-16所示。如果此处设置为圆角或钝角,拉伸件可能会随凸模一起上行,无法顺利完成脱模。
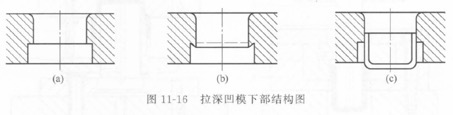
2、拉深模的典型结构
(1) 首次拉深模
如图11-17(a)所示为无压料装置(如压边圈)的首次拉深模。此类拉深模可根据拉伸件性质决定是否设置卸件装置:
①如果拉深结束后拉伸件回弹较小,拉深件紧套凸模,此时需要装配卸件装置,在凸模回程时,卸件装置的底部会作用于拉伸件口部,完成卸件;
②如果制件拉深变形较小,拉深后有一定回弹量并因此引起拉深件口部张大,当凸模回程时,凹模下平面挡住拉深件口部而自然卸下拉深件,此时无需配备卸件装置。无压料装置首次拉深模结构简单,适用于加工板料厚度较大而制件深度要求不大的拉深件。
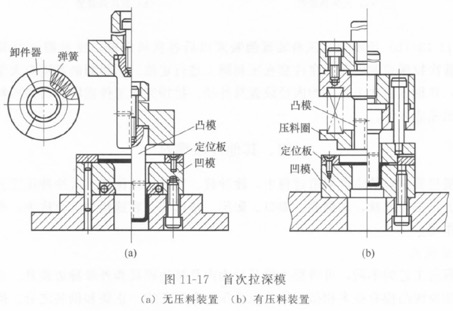
如图11-17(b)所示为有压料装置的正装式首次拉深模。拉深模的压料装置在上模,拉深开始时,压料装置随上模座一起往下运动,压住蚽料后完成拉深。
(2) 以后各次拉深模
如图11-18(a)所示为无压料装置的以后各次拉深模,完成前次拉深后的中间工序件由定位板6定位,拉深后由凹模孔下部台阶卸下。该模具适用于变形程度不大、拉深件壁厚和直径要求均匀的拉深加工。
如图11-l8(b)所示为有压料装置倒装式以后各次拉深模,压料圈6兼具压料、定位作用,前次拉深后的中间工序件套在压料圈上进行定位。压料圈的高度应大于前次工序件的高度,并根据前次工序件的内径设置其外径。拉深完的工件在回程时由压料圈和推件块分别顶出完成卸件。
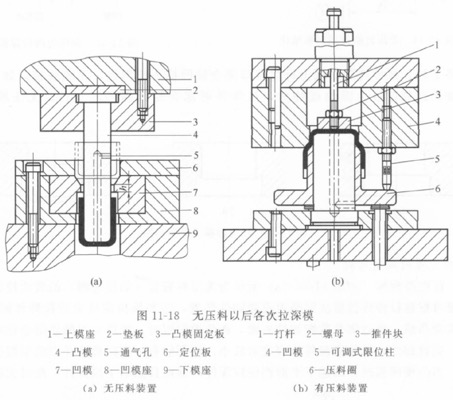
四、其他冲压模具
在金属包装材料的生产制造过程中,除冲裁、弯曲、拉深这三大冷冲压工艺外,其他冷加工方法也不可或缺,如翻边、缩口、胀形、整形等。在这些加工方法中,模具也起到了重要的作用。
1、翻边模具
根据翻边工艺的不同,可将翻边模具分为内孔翻边模具和外缘翻边模具。总体来看内孔翻边模和拉深凸模有很多相似之处,也有压边和不压边、正装和倒装之分。同时,内孔翻边模一般不需要设置模架。如图11-19所示为几种常见的圆孔翻边凸模形状及尺寸,其中图11-19(a)~图11-19(c)为较大孔的翻边凸模,在这三种凸模中,抛物线形凸模最利于翻边工艺的进行,球头凸模次之,平底凸模最差。图11-19(d)~图11-19(f)所示的翻边凸模端部带有较长的引导部分,如图11-19(d)所示凸模用于圆孔直径大于10mm的翻边,如图11-19(e)所示凸模用于圆孔直径小于10mm的翻边,如图11-19(f)所示凸模用于无预孔的不精确翻边。
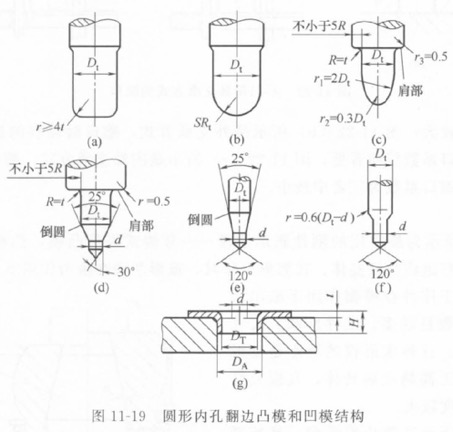
如图11-20所示为内孔、外缘翻边复合模结构,其中凸凹模安装在下模座,既起到内孔翻边凹模的作用,也起外缘翻边凸模的作用。

2、缩口模具
如图11-21所示为缩口凹模结构图,其基本结构通常为一个根据缩口件形状要求设置的锥形孔。根据缩口时模具对蚽料壁部是否有支撑作用可将缩口方式分为三类,如图11-22所示。图11-22(a)所示为无支承方式,缩口过程中还料的刚性差,易失稳,因而许可的缩口系数较大;图11-22(b)所示是外支承方式,缩口时还料的抗失稳能力较前者高,许可的缩口系数较前者低;图11-22(c)所示是内外支承方式,缩口时还料的稳定性最好,许可的缩口系数为三者中最小。
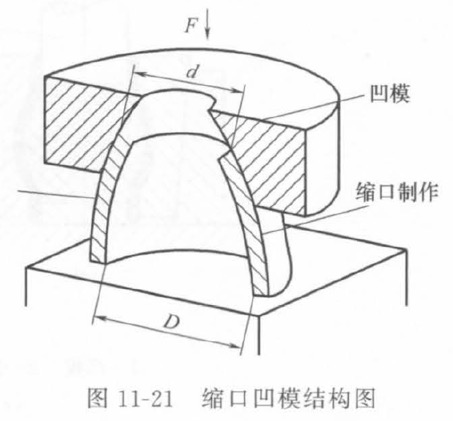
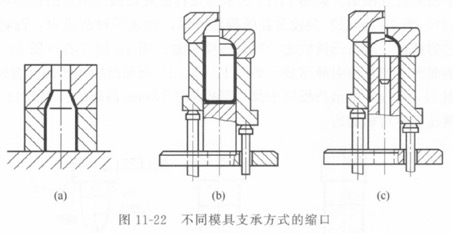
3、胀形模具
如图11-23所示为最常用的刚性胀形凸模分瓣式胀形凸模,凸模被分成多个模瓣,所有模瓣一起组成凸模整体。在胀形工作时,锥形芯块在推力作用下上行,将分瓣凸模顶开,从而使工序件在模瓣作用下胀出所需形状。模瓣的数目越多,工件形状、尺寸和精度控制越好。这种胀形模的缺点是变形不均匀,难以加工高精度旋转体,且模具结构复杂,制造难度较大。
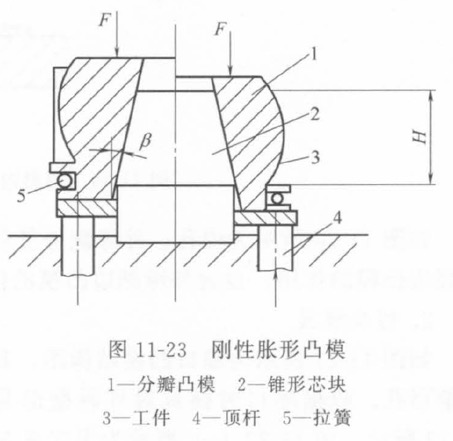
如图11-24所示是软凸模胀形,其原理是利用橡胶、液体、气体和钢丸等代替刚性凸模,与工件直接接触完成胀形。这种胀形方法所加工的还料变形均匀,且不受零件形状的复杂程度限制,因此在生产中被广泛使用。
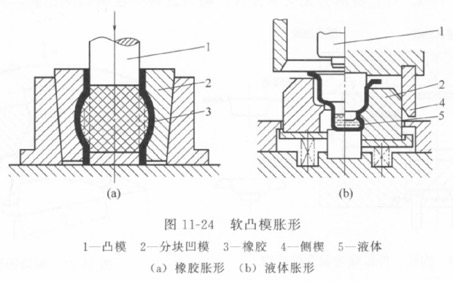
4、整形模具
由于工艺方法、模具精度、金属加工后回弹现象等众多因素的影响,冷冲压制件在尺寸精度或形状细节上离要求标准仍存在细微差距,这时就需要对这些制件进行整形。由于整型后制件的精度要求比较高,因而对模具的精度要求也是较高。
①校平模具。根据校平件的表面形状,可将校平模具分为平板校平模具和齿面校平模具,如图11-25所示。进行校平整形时,将工件置于上模板和下模板制件,然后在两模板之间施加一定压力,并根据要求保待一定时间,使工件完成定型。
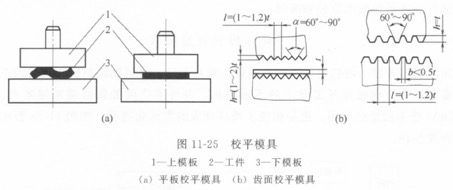
②弯曲件整形模具。弯曲件的整形分为压校和墩校,如图11-26所示。
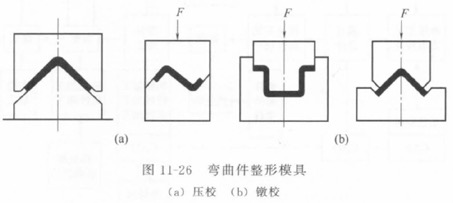
③拉深件整形模具。根据拉伸件是否有凸缘,相应的将拉伸件整形模具分为无凸缘拉伸件整形模具和带凸缘拉伸件整形模具,它们的基本结构和拉深模具基本一样,都由凸模凹模组成,区别是前者未配置压件装置,而后者在整形过程中需要固定凸缘,因此配备了压件装置,如图11-27所示。
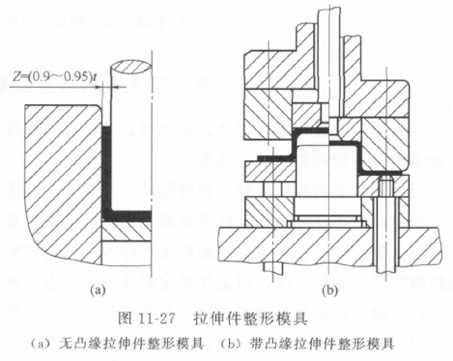
需要注意的是,带凸缘的拉延件在整形过程中需要拉伸件多部位的参与,包括需凸缘平面、侧壁、底平面和圆角等,有些区域在整形时需要从邻近区域得到补充材料。
|