《金属包装设计与制造》(14)
钢桶制造工序
文/吴若梅、刘跃军
1、下料工艺
剪板机是钢桶毛蚽下料的主要设备。剪切工艺的基本原理是利用上、下剪刀的剪力把材料剪断,应具有压料装置。压料力一般可用如下经验公式:

对于机械压料装置K=0.5~0.6;对于液压压料装置K=0.8~1.1,单位kN/mm2。小容量钢桶用的薄钢板(0.5mm以下)下料中,常用圆盘剪。裁剪下料工艺对板料尺寸、形状及裁剪口有具体的要求,200L闭口钢桶板材的对角线偏差不大于6mm,邻边垂直公差在士0.5°以内,毛剌不大于0.5mm,长宽误差不超过±0.5mm,料片四角应为90°,下料的方向要使材料的轧制方向与钢桶轴线平行。
也可采用错位冲压工艺,可降低材料成本,其工艺流程为:
卷板→开卷→校平→定尺送料→桶底盖冲压→桶顶盖冲压、底盖输出→剪废料、顶盖输出。
2、磨边工艺
磨边工艺一般采用砂轮磨边机,由4~12个独立的砂轮架组成,其工作示意图如8-25所示,砂轮圆周速度在20~30m/s范围内。厚度小于0.8mm的钢板可采用柔性(布)砂轮,镀锌钢板采用类砂轮刀具磨边。没经过磨边的桶身,在焊缝处厚度是正常厚度的2倍,为保证焊接质量并使接头部分与桶身的厚度比较一致,需将待焊钢板的边磨出一定斜度。桶身焊接完成后要进行折边、压波纹、胀筋、卷边封口等工序,磨边能减小焊缝的厚度,使卷边封口更加牢固。采用全自动缝焊机生产,因焊缝搭边很窄,不会引起焊缝过厚的问题,对表面比较干净的冷轧板,常可免去磨边工序。磨边处的厚度要根据钢板的厚度来确定,磨边宽度应等于或稍大于焊接的搭接宽度,磨边厚度一般是桶身还料厚度的66%,并且受磨面均匀。磨边宽度一般比缝焊搭边宽度多1~2mm,磨边尺寸的一般规范如表8-5所示。
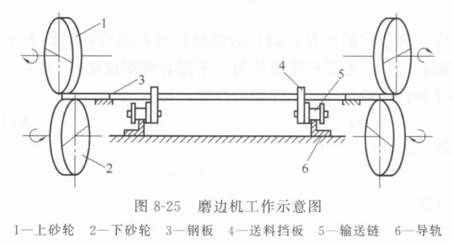
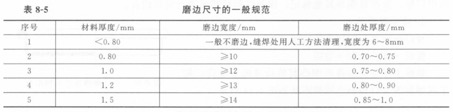
影响磨边工艺质匾的因素,主要有磨边机的精度和砂轮的选用、修整以及进给量的调整等。
3、卷圆工艺
卷板机可分为三辊卷板机和四棍卷板机两类。三辊卷板机又可分为对称式与不对称式两种,通常在三辊式卷圆机上将钢板卷成圆筒。
根据卷圆变形的特点,卷圆过程可分为弹性变形、弹-塑性变形、纯塑性变形阶段,如图8-26所示。
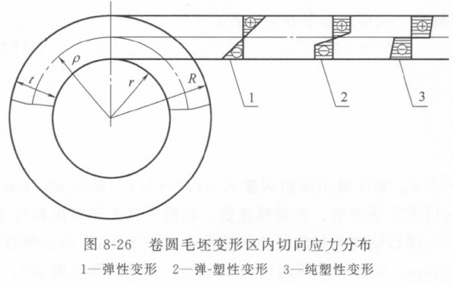
三辊卷圆机的工作原理如图8-27所示,桶身板被送入上辊2和下辊1之间时,转动的辊子通过摩擦力的作用带动板料向后运动,接触位置高于下辊l的后辊5时,使板料不断弯曲卷圆,已卷圆的桶身柱在挡架3、斜板4的作用下进入下道工序的输送带。
调节上、下辊的间隙,可适应不同厚度的板材,调整后辊的位置可改变桶径的大小。为保证点焊、缝焊等后续工序的顺利进行,卷圆曲度应均匀,不能有皱褶或锥度。
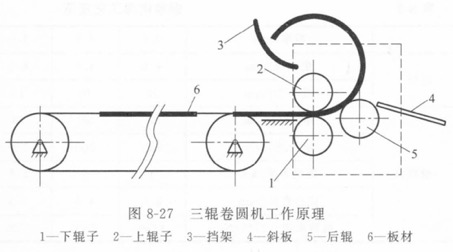
在钢桶生产中,可采用下面经验公式确定应变中性层的位置,即:

4、焊接工艺
钢桶焊接设备一般包括专用或通用的点焊机、缝焊机、凸焊机。钢桶全自动缝焊机是配以桶身卷圆机的全程自动焊接的专用缝焊机,由机架、装卸台、升降台、双张控制的分张装置、卷圆机构、成圆后的桶身定位、桶身传送器、中间传送链、桶身导向轨、焊缝校准器、焊接滚轮及焊缝修正器、出桶输送机和卸料台、控制器显示屏、控制柜组成。
激光钢桶缝焊机、激光钢桶环焊机,是将桶身、桶底、桶盖用激光焊接成一个整体。焊接部位材料因熔融而形成具有韧性的牢固焊缝,抗拉强度等于或大于母材,其强度高出二倍以上。可适应金属、非金属各种材质,内装高温液体、危险品液体也不会产生泄漏,可达到“零渗漏”,实现薄型化。能耗仅为传统焊机的15%左右,节能效果显著。焊缝宽不足1mm,可实现包装减簸化,降低生产成本和运输费用。
采用电阻焊缝焊法,沿桶身纵向将搭接接缝焊合,形成一条气密型焊缝。桶的外径用三个大辊轮引导,接头处板料边沿用Z形杆引导,以控制搭接量,其焊接方法及其结构类似于三片罐的电阻焊机。
焊接时,首先要进行点焊,焊点的形状与尺寸决定接头的强度和质量。不同的材料,厚度及厚度比,对焊点直径d要求不同,如表8-6所示。
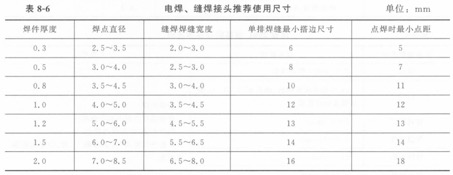
(勘误:此处的“电焊”应为“点焊”)
焊接参数的选择与桶件材料的性能,如导电性、导热性、导温系数、高温强度、熔点、塑性温度范围、变形抗力、硬度、热敏性等有关。表8-7为低碳钢电焊工艺的一般规范。
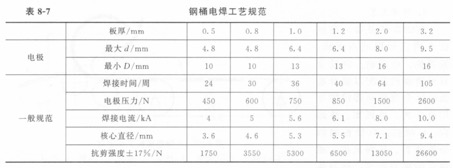
(勘误:此处的“电焊”应为“点焊”)
对于200L钢桶来说,在两端及中间最少应进行三点点焊,焊点直径6.5mm,搭边均匀一致,尺寸12mm±1mm,焊点牢固,无烧焦及烧穿等现象。
接下来要进行缝焊,钢桶桶身的缝焊属于气密缝焊,缝焊规范参数的选择按工艺图纸、依据桶身材料性能、厚度、质量要求及设备条件来进行。表8-8所示为低碳钢桶身缝焊中速缝焊的工艺规范,可根据板厚不同而选择高速或低速缝焊及相关参数,可查阅有关资料,如表8-9所示为焊接200L钢桶桶身的一般技术规范。
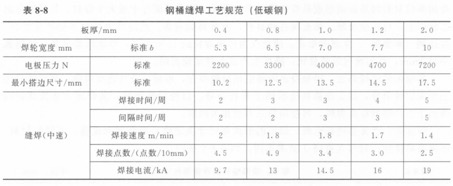
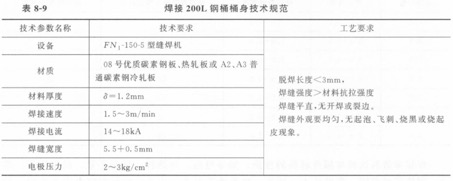
钢桶的材料多为低碳钢,也常采用镀锌钢板、马口铁等,其焊接规范因材料不同而不同。
影响焊接质量的因素很多,一般可归纳为设计、工艺和使用三类,如图8-28所示。
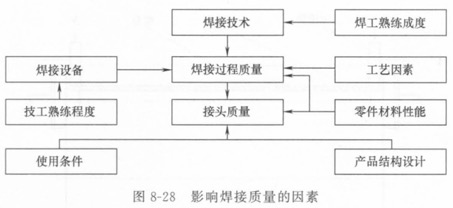
5、翻边工艺
在专用翻边机上用翻边压轮将桶身的两端各向外翻出一个角度,以便与桶底、桶盖封口组合,翻边应均匀平齐,不应出现裂口或皱褶。
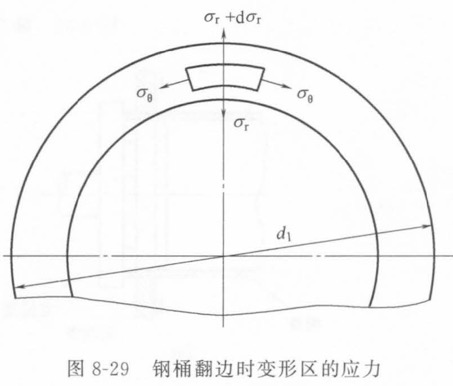
桶身翻边是伸长类曲面翻边的一种形式,在翻边时毛还变形区的受力情况如图8-29所示。毛坯变形区受两向拉应力切向拉应力σθ和径向拉应力σr,的作用。允许的翻边宽度b,可用下式计算
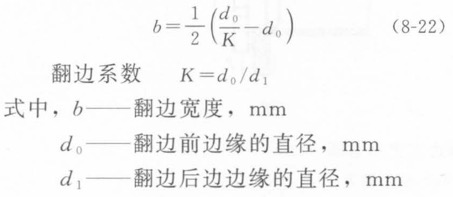
翻边工艺主要分为以下几种:
①模具翻边工艺,如图8-30所示,效率高,质量好,设备结构简单,体积小,但翻边过渡圆弧不能太小。翻边角度在90°~120°。
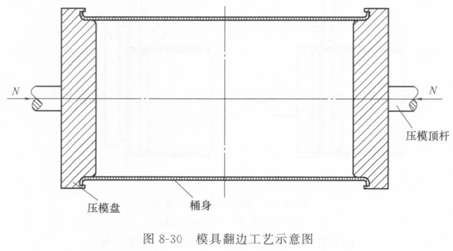
②滚压翻边工艺,如图8-31所示。一般凸轮转速为5~8(r/min),工作滚轮转速为200~500(r/min)。工作滚轮直径约为桶径的1/4。
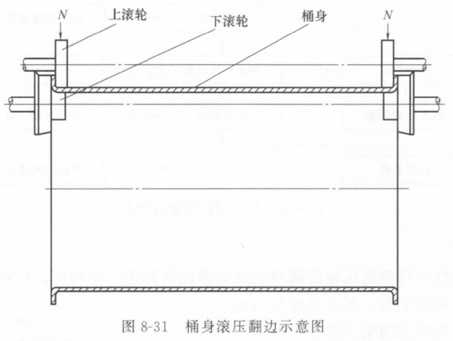
③胀形翻边工艺,如图8-32所示,翻边机主要由定位盘、夹桶芯、胀形块等组成工作部分。其效率高,质量好,但设备较为复杂,体积也较大,多用在小桶或异形桶的翻边工序中。
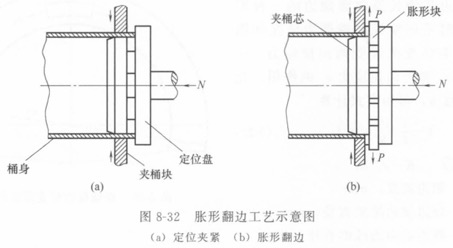
④偏心轮滚压翻边工艺,如图8-33所示。
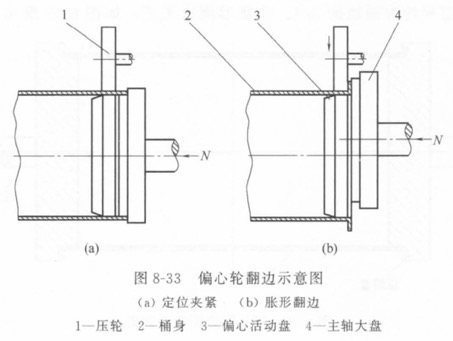
翻边工艺尺寸需与桶底顶盖的尺寸密切配合,卷边搭接量和配合角度,可用桶身钩接百分率ρ来计算:

对于有二重卷边,翻边角度取90°±2°。对于三重圆边,翻边角度为108°±2°。对于200L闭口钢桶,一般采用二重平卷边时,其翻边宽度尺寸为12mm±1mm;采用三重圆卷边时,其翻边宽度尺寸为17.5mm±0.5mm。为保证翻边质量,翻边应光滑圆整,不得有破裂以及皱折;焊缝两端翻边处不许有突嘴、破边等现象;翻边处圆角不宜过大,一般情况下,圆角半径不应大千板料厚度的5倍。
6、滚波纹、环筋工艺
在波纹机上通过滚压,在桶身上同时滚出若干条圆周波纹,变形区材料受双向拉伸作用,如图8-34所示为其成型示意图。滚压成型中,滚轮设计是最重要的技术,滚出的波纹要达到均匀光滑、深浅一致、不得歪斜、无机械损伤,则生产时需考虑滚轮节圆直径、滚轮的间隙、板料防回弹、表面防划、滚轮材料等问题。
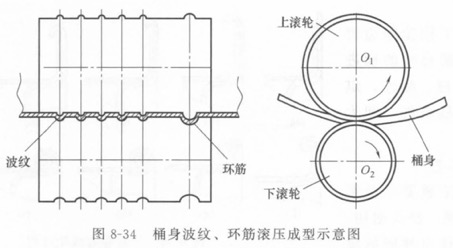
在桶身中段扩胀两条加强筋,胀筋头用凸轮或液压传动,滑块沿径向将筋胀出,加工完毕胀筋头缩回原位,胀出的环筋应无机械损伤和裂纹。
7、前试漏
加左右压紧盘,打入一定压力的亚硝酸钠溶液,以测试桶身纵缝有无泄漏现象。检验合格的桶进行清洗、喷涂、然后干燥。为提高表面涂料与金属桶表面的结合牢度,有些生产厂还增加了磷化处理工艺。
8、卷边封口
把桶底和桶盖装到桶身两端,旋转并轴向顶紧,用辊轮进行卷封,图8-35所示为卧式卷封装配机的工作原理图,卷边的部位应注入封缝胶。钢桶的卷封类似于金属罐,其成型过程及原理可参见第三章相关内容。由于桶承受的冲击力大,通常采用三重卷边来提高封严强度,防止桶底(顶)变形及渗漏。
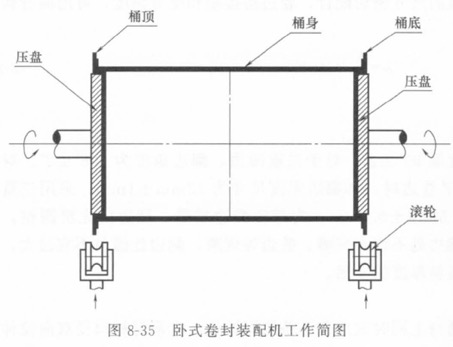
在三重卷边成型过程中桶身和桶顶、桶底材料要经过更多的弯曲变形,这就要求压辊的进给距离比二重卷边的要大,一般需三个压辊分三次加工完成卷边成型。桶身与桶底(顶)卷封加工前的状态如图8-36(a)所示,首先第一道压辊沿径向移动对桶底(顶)进行预卷,如图8-36(b)、图8- 36(c)所示,然后第二道压棍沿金属桶径向逐步进给卷边,如图8-36(d)~图8-36(f)所示,最后第三道压辊完成三重卷边的成型图,如图8-36(g)~图8-36(i)所示。
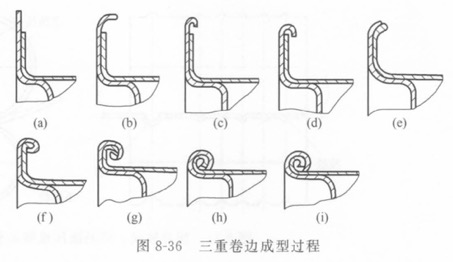
上述成型工艺过程,一般都是在预卷机和封口机两台设备上进行的,在预卷机上先通过第一道压棍完成三重卷边的预卷变形,再通过封口机上安装的第二道压棍和第三道压棍实现三重卷边的组合封口。
9、后试漏
目的是为了检验卷边封口的质量,检验合格的桶进行表面除油处理、喷漆、烘干,最后装上桶口件,即为成品。
10、涂装工艺
钢桶表面漆膜要求色彩鲜艳,光亮丰满,经久耐用。为此除了选用优良性能的涂料外,必须合理地选择施工方法和使用设备。当钢桶用来盛装食品时,如盛装蜂蜜、果酱、番茄酱等,由于食品卫生要求比较严格,必须在内部涂上无毒无味的防腐蚀涂料。另一类化工包装桶,内盛物容易与钢桶的金属反应产生腐蚀,使内容物变质或使钢桶损坏,所以也要内涂防腐蚀的化工涂料。对于闭口钢桶的内涂,必须在桶身与桶底、顶卷封装配前分开进行,内涂并烘干后才能进行卷封装配,然后再进行外部涂装。由于季节温度的变化,会给钢桶的喷涂工艺带来不良影响。也可通过加热的方法来调节温度降低涂料的黏度、保证黏度的稳定性,一般涂料的加热温度到50℃即可,最多不超过70℃。
(1) 涂装前处理
钢桶在涂装前需进行表面处理,其关系着涂层的附着力和使用寿命,直接影响涂装质量。表面准备工序,主要是清除钢桶表面的油污、锈蚀、有机污物和尘土等,以改善钢桶表面状态。表面处理的目的,主要有以下三个方面:增强涂膜对钢桶表面的附着力,涂膜的美观平整准备条件,增加表面抗腐蚀能力。涂装前表面处理的程序是:先除油,其次去锈。除油主要是利用溶解、皂化、乳化作用将钢桶表面油污去掉。除锈可以进行机械处理和化学处理。机械处理法较为简单,即利用钢刷、砂布、砂纸、布等工具手工除锈,工作效率极低,质量也不好。化学除锈是用酸溶液与这些金属氧化物发生化学反应,使其溶解在酸溶液中。金属表面在完成除油、除锈等表面处理后,往往容易重新生锈。为了防止发生返锈,通常要进行化学处理,使金属表面形成一层保护膜。钝化处理就是其中一种方法,形成的钝化膜不活泼,如磷化就是将钢桶表面经含有锌、锰、铬、铁等磷酸二氢盐的酸性溶液处理后发生化学反应,在金属表面形成一层主要成分为不溶于水的稳定的磷酸盐保护膜的过程。
(2) 涂装工艺
钢桶的涂装一般采用空气喷涂、高压无气喷涂、静电喷涂、粉末喷涂等。空气喷涂是利用一种专用的喷漆枪,以压缩空气把漆液从贮罐里吸上来,压缩空气的气流再把漆液带到喷枪的喷嘴,吹散成细雾,均匀地喷涂千钢桶表面。高压无气喷涂,如图8-37所示为卧式钢桶高压无气喷涂室,高压无气喷涂是将涂料施加高压(通常为11~25MPa),使其从涂料喷嘴喷出,以高达100m/s的速度与空气发生激烈的高速冲撞,使涂料破碎成微粒,在涂料粒子的速度未衰减前,涂料粒子继续向前与空气不断地多次冲撞,涂料粒子不断地被粉碎,使涂料雾化,并黏附在被涂钢桶表面。
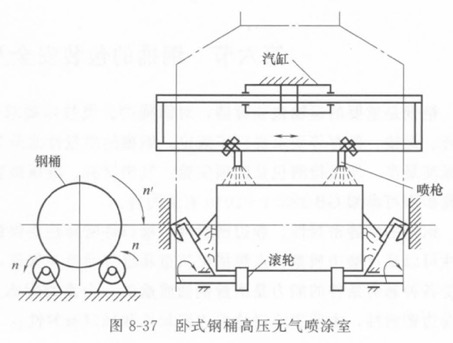
静电涂装是在喷枪(或喷盘)与被涂钢桶之间形成一高压静电场,一般钢桶接地为阳极,喷枪为负高压,当电场强度足够高时,枪口附近的空气即产生电晕放电,使空气发生电离,当涂料粒子通过枪口带上电荷,成为带电粒子,在通过电晕放电区时,进一步与离子化的空气结合而再次带电,并在高压静电场的作用下,向极性相反的被涂钢桶运动,沉积于钢桶表面,形成均匀的涂层,图8-38所示为静电涂装示意图。
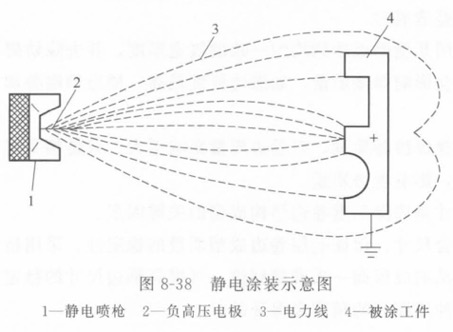
粉末喷涂,是在喷枪和钢桶之间形成较强的静电场。当运载气体(压缩空气)将粉末涂料从供粉桶经输粉管送到喷枪的导流杯时,导流杯接上高压负极产生电晕放电,其周围产生密集的电荷,粉末带上负电荷,在静电和压缩空气的作用下,粉末均匀地吸附在钢桶上,经加热、粉末熔融固化(或塑化)成均匀、连续、平整、光滑的涂膜,图8-39所示为粉末静电喷涂工艺流程。
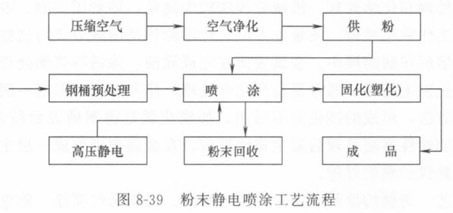
|