辛巧娟:钢桶原材料钢板的选择和常见问题解析(3)
文/辛巧娟
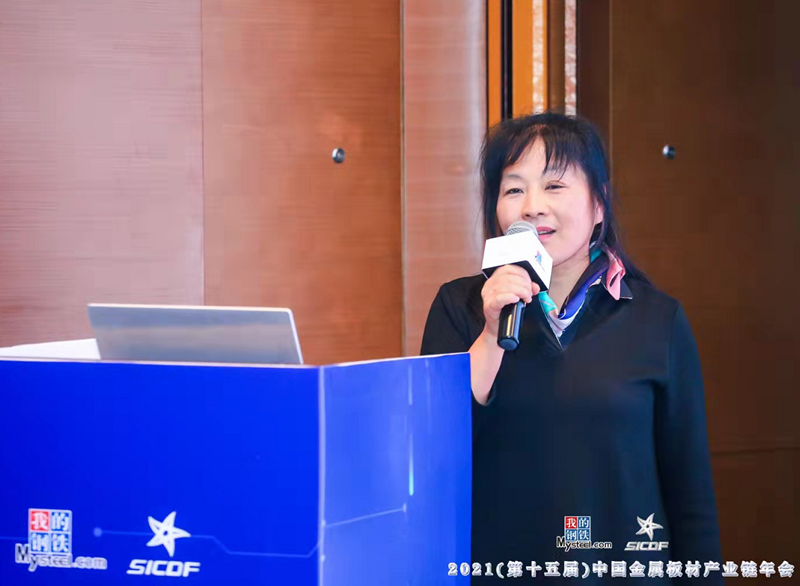
四、钢桶生产中常见问题分析
(一)裂纹
裂纹大部分出现在桶底部,当然桶身上也有,我曾多次在钢桶行业中讲,是材料厚度问题,我们在座的同仁也非常赞同这个说法。因为这样就把问题甩锅给桶厂,与钢厂没关系,其实任何事物发展都有根源,进一步追踪,会发现还是钢材质量问题,出现问题,桶厂可以通过一些方法杜绝或避免此类问题的再发生,但最终还是要从钢板质量上解决。
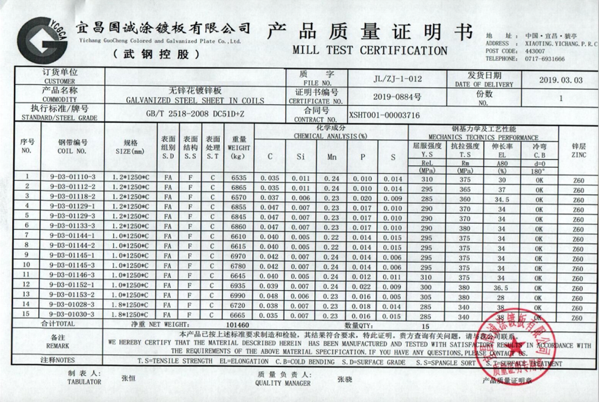
产品质量证明书中有钢卷号、表面质量、尺寸、数量、重量、化学成分及性能指标等参数,对于钢卷号、表面质量、尺寸、数量、重量这些参数,钢材在进厂检验时都应该得到确认,我们主要看其化学成分和性能指标。
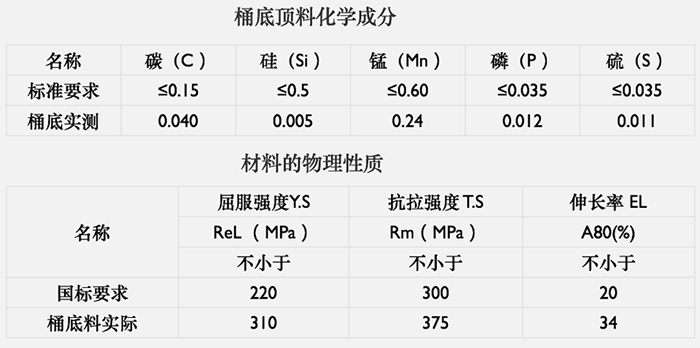
1、从力学性能分析
对于材料的屈服强度和抗拉强度,这里先做一下介绍。
前面曾经提到过,抗拉强度和屈服强度是金属材料重要的两个力学性能指标。抗拉强度是断后最大强度,而屈服强度是明显产生塑性变形时的最小强度。
屈服强度和屈服点相对应,屈服点是指金属发生塑性变形的那一点所对应的强度成为屈服强度。
抗拉强度指材料抵抗外力的能力,是拉伸实验时拉断时的强度。也就是钢材受拉断裂前的最大应力值(b点对应值)称为强度极限或抗拉强度。
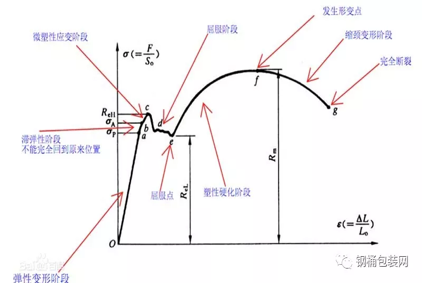
应力(kg/mm3)-应变(%)曲线图
屈服强度是金属材料发生屈服(塑性变形)现象时的屈服极限,也就是抵抗微量塑性变形的应力。大于屈服强度的外力作用,将会使零件永久失效,无法恢复。
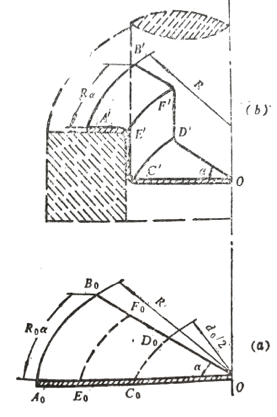
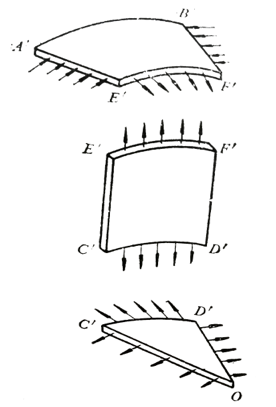
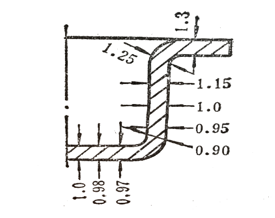
一般桶厂购的材料都有产品质量证明书,从材料的力学性能来看,是合格的。
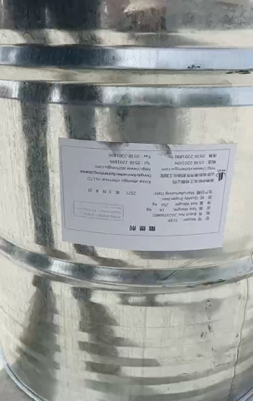
2、从微观上进行分析
我们将有裂纹的钢桶剖切开,观察桶底、顶及桶底顶卷边处均有从内壁向外突起变形现象存在,桶顶上的突起有7~8处,桶底上的突起有2~3处,其中1处发生开裂,裂纹基本沿径向分布。切割取样后发现桶底开裂发生在卷边附近桶底拉伸处,与桶顶上的突起变形部位相比开裂处的变形幅度较大。
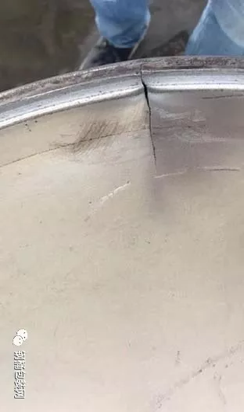
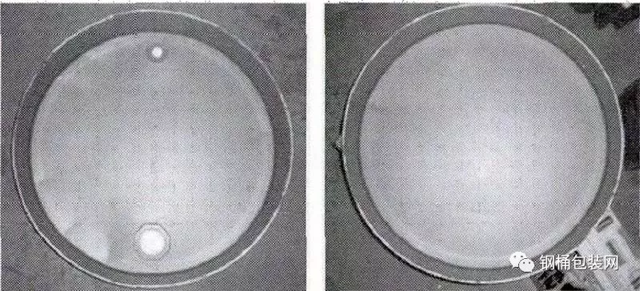
钢桶桶底开裂处的外表面形状
(1)金相组织
在桶底上对开裂处及未开裂部位进行取样,分别制备金相样品,进行显微组织分析。从下图可以看出金相组织均为:铁素体+球粒状渗碳体。晶粒度为7~8级。组织均匀,只是两个部位晶粒大小不同。
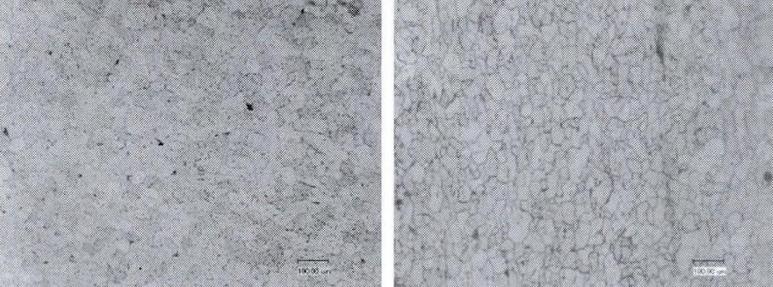
a)未开裂部位金相组织;(b)开裂部位金相组织
(2)扫描电镜微观分析
将裂纹打开后在扫描电镜下观察裂纹断口的形貌,结果发现钢桶开裂始于钢桶桶底的拉伸面上,裂源的断口上存在呈八字形分布的裂纹扩展台阶,从图中可以看出,裂纹扩展区的断口形貌呈现疲劳辉纹特征,在远离桶底拉伸弧面即底平面的断口上也存在疲劳辉纹特征。
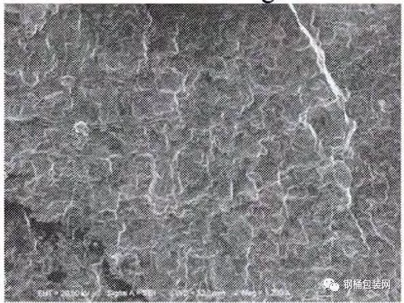
裂源附近裂纹扩展区断口形状
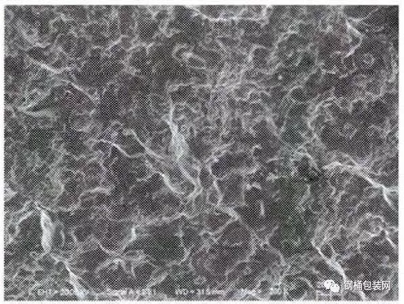
远离破裂处断口形状
所以钢桶桶底上的开裂性质为疲劳断裂,疲劳裂纹源位桶底拉伸直边附近突起变形幅度最大位置的内壁。
钢板在经过落料拉伸变形后,折弯部位内壁的形变相对较大,钢桶承载时如果在内壁形变量较大的区域发生幅度较大的突起变形,形成应力集中点。容易造成该处的内壁表面发生破裂,形成裂纹源。钢桶在运输过程中存在颠簸,随着路途距离的增大,颠簸振动的次数增加,并形成周期性作用力面产生共振现象,应力开始释放,造成疲劳裂纹从钢桶桶底内壁的裂纹源向外壁扩展,最终导致钢桶桶底疲劳开裂。
(二)穿孔和夹杂
我们对缺陷部位进行宏观分析、金相检验、扫描电镜及能谱分析
1、宏观分析
下图a)为钢桶穿孔处宏观形貌,可见裂纹呈中间宽、两头窄形貌,缺陷部位附近无明显的机械擦伤,属于张力作用下拉裂形成的孔洞。对穿孔部位折弯后发现孔洞内有大块异物,如图b)所示。
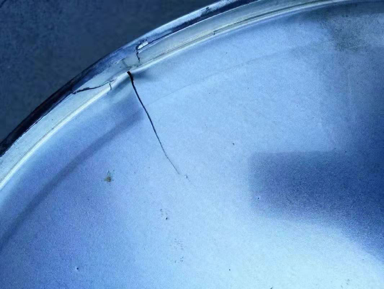
a)裂纹形貌
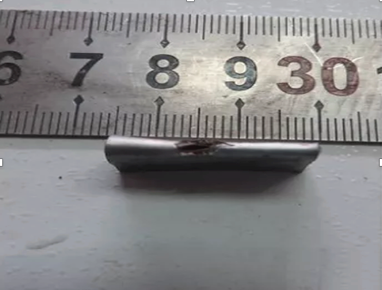
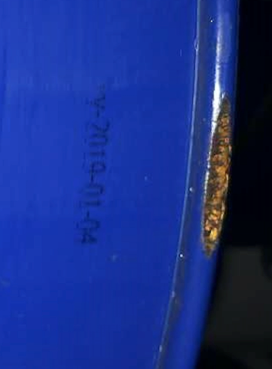
b) 大块异物形貌
2、金相检验
对缺陷部位取样进行金相检验,可以发现穿孔内有大块疑似夹渣的黑色异物,同时附近基体还内嵌有多个小块异物
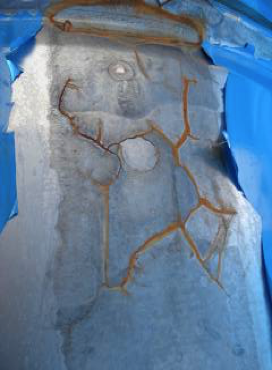
穿孔处压弯后断口SEM形貌
3、扫描电镜分析
为了进一步确定异物的组成,将穿孔部位折弯撕开后对暴露的断面进行扫描电镜( SEM) 观察,并对异物使用能谱仪( EDS) 进行分析,确定其组成成分。
扫描电镜下可以看到穿孔部位断面上内嵌许多大小不一的颗粒物,颗粒物带角,多为不易变形的脆性夹杂物; 夹杂类孔洞的微观特征是,在孔洞的断口上有大型脆性夹杂物,或聚集状夹杂物和分层等缺陷。对颗粒物进行能谱分析,结果显示其主要含有氧、钙、铝、碳、锌、磷、硫等元素。
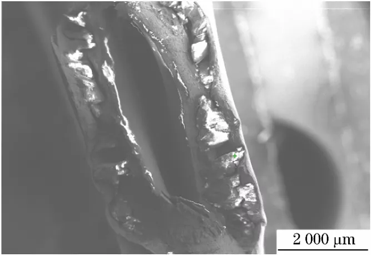
4、能谱分析
分别对扫描电镜观察到的断口表面聚集状夹杂物进行能谱分析。
可以看出夹杂物经能谱测定含有Ca、Al、Na、S、O等元素的夹杂物。夹杂物为颗粒状夹杂物的聚集,从能谱分析看夹杂物应为Ca、Al、Na、S、O等元素组成的氧化物。
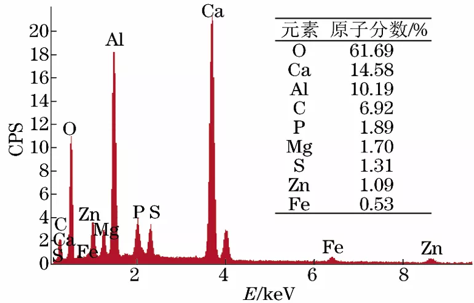
断口表面异物能谱分析结果
扫描电镜能谱分析结果显示钢桶穿孔部位的异物主要为钙、铝复合氧化物夹杂,由于这些非金属夹杂物的存在,钢在变形时其基体的连续性被破坏,其工艺性能就会降低。
一方面在进行加工变形时夹杂物容易从基体上断裂脱落,形成孔洞; 另一方面在凝固时夹杂物与基体的线膨胀系数不同而形成内应力,在夹杂物周围产生应力,使夹杂物与基体的界面极易产生微裂纹,微裂纹在后续加工过程中受到拉应力或切应力的作用发生扩展导致开裂。
在钢桶加工过程中,由于复合型夹杂物与基体变形量不同,导致夹杂物与基体之间产生微裂纹,在外力的作用下,裂纹扩展,最终导致形成砂眼,造成穿孔渗漏。薄板厚度仅为1.0mm,冷轧产品的规格越薄则夹杂物的危害性越大,基板产生孔洞的概率就越大,在轧制力的作用下严重的会形成穿孔。
(三)材料厚度不均匀问题
钢板各部分厚度不一致称厚薄不均,凡厚度不均匀的钢板,一般都是偏差过大,局部钢板厚度超过规定的允许偏差。厚度不均匀,不仅导致桶重不一,更主要是生产过程控制困难,焊接是因为厚度不同,焊接规范很难控制,焊缝会出现击穿或焊不牢固等现象,桶底料拉伸时
因间隙不同,从而影响拉伸质量出现翘曲不平、法兰边大小不一致、拉破等,钢桶卷封时也会出现铁舌等。
这样大钢厂精度高的轧机控制的较好,一般我们钢桶要求取下差,厚度公差控制在10微米内,如:我们用1.0的钢板做的200L钢桶,重量应为18kg,我们出厂桶一般写17.8±0.5 kg。由于灌装产品不同,大部分客户要求桶重控制在±0.2 kg范围内:
1.2/1.2/1.2的桶重21.5kg
1.2/1.0/1.2的桶重18.8kg,可许多厂家做的桶都是19.1-19.5kg,
1.0/1.0/1.0的桶重17.8kg,
1.0/0.9/1.0的桶重16.8kg
0.9/0.9/0.9的桶重16.2kg
1.0/0.8/1.0的桶重15.3kg